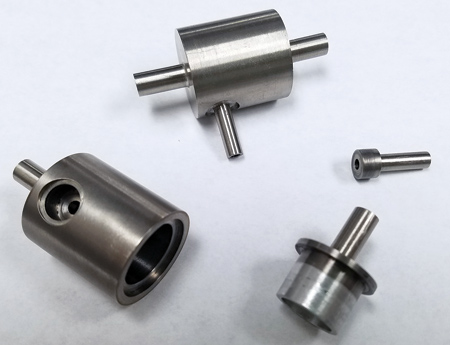
This part, made up of six different components (not all components shown), is used for a satellite application. The aluminum/titanium assembly in the lower right corner consists of four parts with one electron beam weld. The aluminum was explosively bonded to the titanium. There are a total of three electron beam welds on this part.
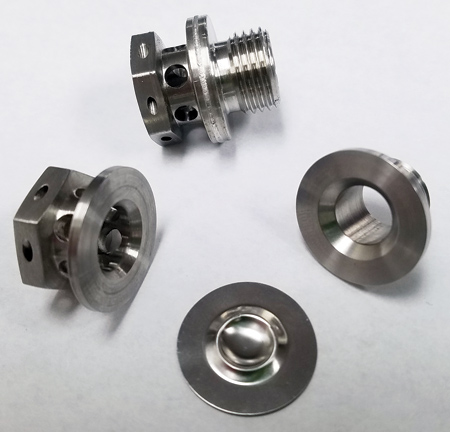
This part is used on commercial airplanes. It is all stainless steel but requires a very deep weld penetration.
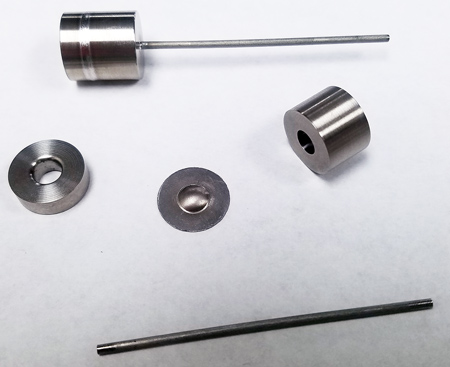
This is an all titanium assembly that is used in a medical equipment application. The small tube is only 0.062" diameter. There are two electron beam welds. The welds have to hold more than 12,000 PSI.
"Electron Beam Engineering, Inc. (EBE), a precision electron beam and laser beam welding company, has supported BS&B Safety Systems with significant improvements in the welding of its rupture disks," said an EBE spokesperson.
Rupture disks, also known as pressure safety disks, are sensitive relief devices designed to instantaneously rupture at a predetermined pressure and temperature as a means of providing protection for personnel, electronics and equipment. Rupture disks can respond within milliseconds to an increase or decrease in pressure and temperature. Once the disk is ruptured, it will not reseal. They can be used as a single protection device or as a backup device for a conventional safety valve. If the system pressure reaches an unsafe level and the safety valve fails, the rupture disk will burst. Rupture disks are commonly used in petrochemical, aerospace, medical, pharmaceutical, food processing and oil field applications.
The rupture disks made by BS&B Safety Systems must burst with a tolerance of +/- 5% to meet most standards and its customer's expectations. Quite often, especially for low pressure applications, the rupture disk membrane is made from very thin material. It is not uncommon for the rupture disk to be as thin as 0.002". This thin membrane is often mated to much thicker machined components to form a welded assembly. The weld must be a hermetic seal as well as have the structural strength to hold the parts together under load from installation torque and/or operating pressures. Welding very thin material to one or two much thicker pieces is always a challenge. When excessive heat input can have a negative effect on the burst pressure of the rupture disk, the challenge is even greater.
BS&B has in-house TIG welding capabilities, so that is always the company's first option when considering a solution. In cases where the material does not lend itself to TIG welding (aluminum, titanium, tantalum), then electron beam welding is the next option. In some cases where the material is easy to weld, such as 300 series stainless steel, the heat input from the TIG welding still poses a problem.
Electron beam welding was selected as the solution for applications and materials that BS&B could not TIG weld in-house. "The heat input from the electron beam weld is much less than that of the TIG weld, so we are able to achieve deeper penetration with much less effect on the rupture disk," said Arnold Mundt, CEP Engineering Manager at BS&B. "For example, one application required a minimum of 0.060 inch weld penetration with the disk material only being about 0.005 inch thick. We could not achieve penetration greater than 0.025 inch without affecting the rupture disk burst pressure so dramatically that we could no longer hold the burst tolerance. EBE was able to successfully weld the part with penetrations of 0.080 inch to 0.090 inch with no negative effect on the burst pressure."
"Because of our precision electron beam welding and the low amount of heat generated, our process produces less distortion and minimal effect on the burst disk material," said Grant Trillwood, General Manager of EBE. "The result is a much better product that is ideal for special materials and designs. Additionally, our process requires no post weld machining or cleanup. The outcome is a manufacturing procedure that is more predictable, resulting in a higher yield of disks all having the same burst pressure."
While BS&B would prefer to weld everything in-house, it is not always economical to have all types of welding equipment along with the necessary knowledge to operate it on hand. "For these cases, EBE has been a welding partner with BS&B since the mid-1980s," said Mundt. "The very first project we worked on together involved welding columbium material (now called niobium) for a rupture disk used on the Trident II missile. That project ran successfully for more than 20 years."
EBE provides precision electron beam welding and laser beam welding services throughout the United States, Europe and Australia. EBE specializes in working with complex components for a variety of applications, including medical, sensor, aerospace and automotive. Richard Trillwood founded EBE in 1991 and was the designer of the compact production electron beam welding machine, from which he developed a wide range of precision laser and electron beam welders.
Founded in 1931, BS&B Safety Systems is a designer and manufacturer of bursting disks and other pressure relief devices. BS&B products are designed for the industrial process industries, including chemical, oil and gas, pharmaceutical, biotechnology, food and beverage and the OEM industry, ranging from fire protection to automotive. Products include rupture disks, safety equipment, explosion vents and a number of custom engineered products.
For more information contact:
Electron Beam Engineering, Inc.
1425 South Allec Street
Anaheim, CA 92805
800-EB-WELDS / 714-491-5990
sales@ebeinc.com
www.ebeinc.com
BS&B Safety Systems, L.L.C.
7455 East 46th Street
Tulsa, OK 74145-6379
800-BSB-DISK / 918-622-5950
sales@bsbsystems.com
www.bsbsystems.com