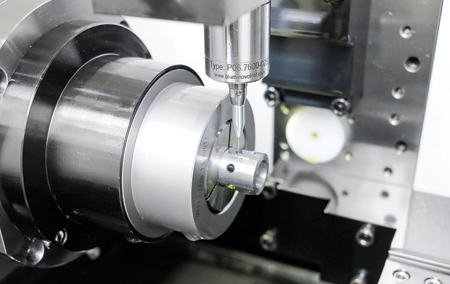
The TC76-DIGILOG touch probe from Blum-Novotest scans the complete contour of the slot.
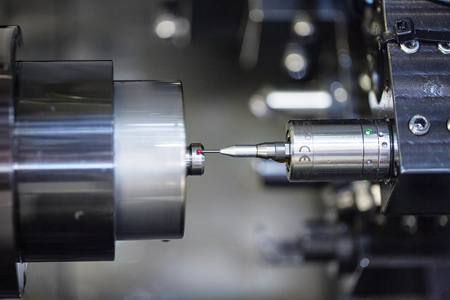
The TC76-DIGILOG touch probe can be positioned horizontally or vertically in the lathe, depending on the measurement task.
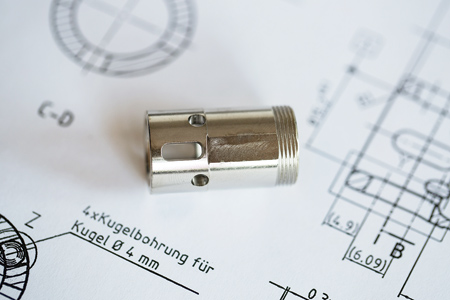
The quick-coupler prevents the loud snapping noise when detaching. Its manufacture is highly complex. Measurement of the four lightly tapered slots was only possible with the aid of the BLUM TC76-DIGILOG touch probe.
A complex component, incorporating four long slots among other features, was posing problems for Timo Lehmann, CEO of Karlheinz Lehmann GmbH in Oberwolfach, Germany.
"Highly complex components are part and parcel of our business. But implementing a quick-coupler for compressed air input was a tough nut to crack," said Lehmann of the challenges posed by a project for Parker Hannifin GmbH, a provider of drive and control technology and pneumatics. "The key components are hardened and coating-free cutting steel, threads, bores and four lightly tapered slots. The slots were the crucial point of the whole design."
The parallelism of the slots was only allowed to vary by 2 µm from the reference values. Otherwise, the fully automated machine assembling the component unit at Parker-Hannifin would abruptly stop. Moreover, the quick-coupling would not work if the tolerance was exceeded. When assembled, the lightly tapered slots contain balls, which must not protrude too far, yet must also never be allowed to fall through the slot. Through this design, the Parker quick-couplers prevent the otherwise common snapping noise when detaching, and also allow single-hand operation. Just as challenging as the production process is the task of measuring the slots. The solution was ultimately provided by a Cincom M32 lathe in conjunction with a TC76-DIGILOG touch probe from Blum-Novotest. "The BLUM TC76-DIGILOG touch probe proved the only cost-effective means of verifying the design's dimensional accuracy," said Lehmann.
"Analogue measurement is always advantageous for assessing areas or lines," said a Blum-Novotest spokesperson. "If a switching digital probe were to be used in the Lehmann application, for example, a very large number of points on the slots would have to be measured in order to attain an adequate resolution. By contrast, the TC76-DIGILOG scans across the surface at a measuring speed of 2 m/min. As this is happening, the system generates an extremely large number of values (50,000 per second) in a fraction of the time based on analogue data acquisition."
The Cincom M32 and TC76-DIGILOG combination has been running smoothly and efficiently in Lehmann's production operations. The sequence is as follows: at the start of a production run, a reference part is clamped onto the machine and the complete contour of the corresponding slot is scanned and recorded. The master profile is recorded and saved in the evaluation software. The subsequent production workpieces are measured and compared against the recorded profile, and any that exceed the tolerance are discarded. As a result, the tight tolerances of the slot are reliably checked immediately after the cutting process in the lathe. "In-machine measurement itself delivers enormous benefits," said the spokesperson. "If it is run without problem in the idle times, as in Parker Hannifin's quick-coupler production, it is hard to beat. It allows Lehmann to implement 100% checking, with error trends being detected at an early stage by evaluation software."
"It does not matter whether the TC76-DIGILOG is fitted in a grinding machine or a milling machine, and due to its increased scanning forces, it is even well suited to the tough demands of applications in lathes," continued the spokesperson. "The TC76-DIGILOG scans the part accurately and non-directionally, measuring with precision due to the patented shark360 measuring mechanism. Neither coolant nor viscous oils impair the reliability of the measurement data. With its higher scanning force, the touch probe simply pushes through the coolant."
The Blum-Novotest/Citizen combination is also used for other large production lots from 10,000 to 30,000 pieces. The processed materials are wide ranging, from stainless steels, heat-treatable steels and free cutting steel to aluminum. "Given that we were close to having to refuse the quick-coupler order from Parker Hannifin, we are delighted to have found such a powerful solution in the combination of a BLUM touch probe and Citizen machine," said Lehmann.
Machining contractor Karlheinz Lehmann GmbH is based in Oberwolfach in Germany's Black Forest. At its 1,000 square meter site, the family business employs 17 people operating 20 state-of-the-art CNC lathes and milling machines, mostly in the manufacture of high precision rotationally symmetrical parts. The company has been in business for over 40 years, and is now managed in the second generation by the founder's son and daughter.
For more information contact:
Karlheinz Lehmann GmbH
www.lk-zerspanung.de
Blum-Novotest, Inc.
4144 Olympic Blvd.
Erlanger, KY 41018
859-344-6789
solutions@blum-novotest.us
solutions@blum-novotest.us
www.blum-novotest.com/us
Marubeni Citizen-Cincom, Inc
40 Boroline Road
Allendale, NJ 07401
201-818-0100
www.marucit.com