
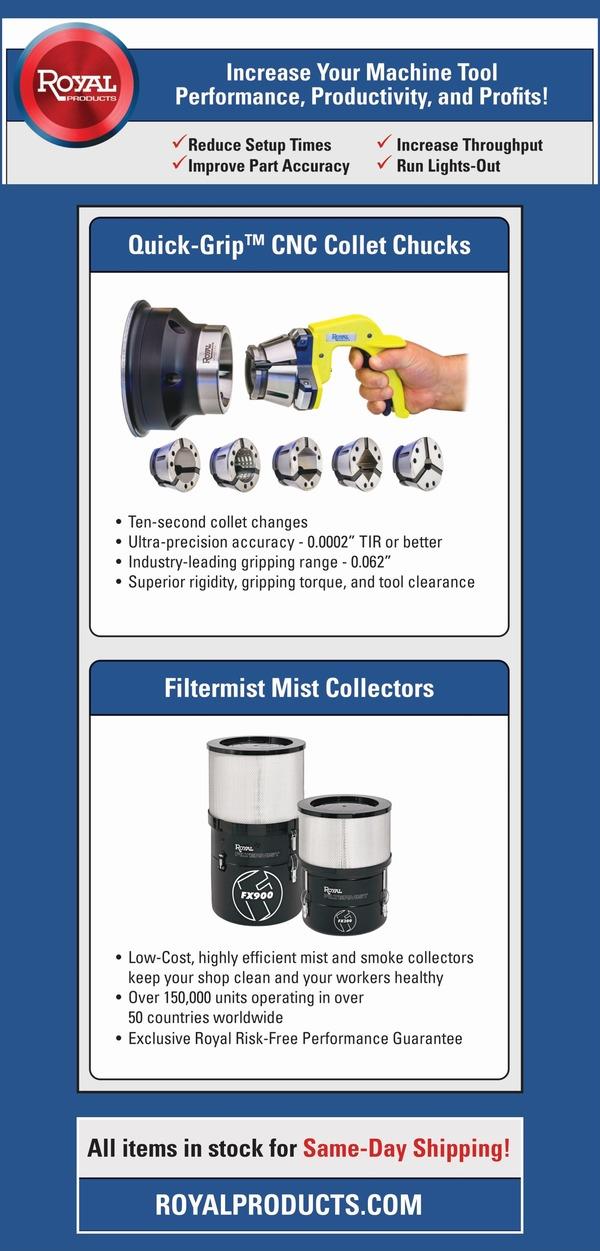
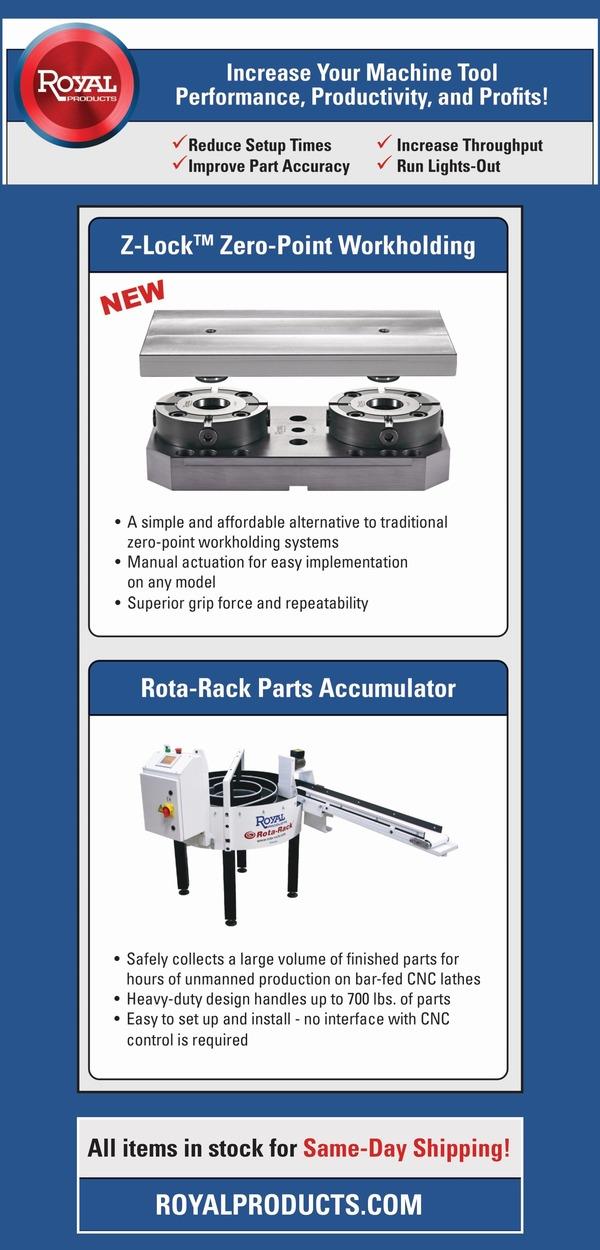

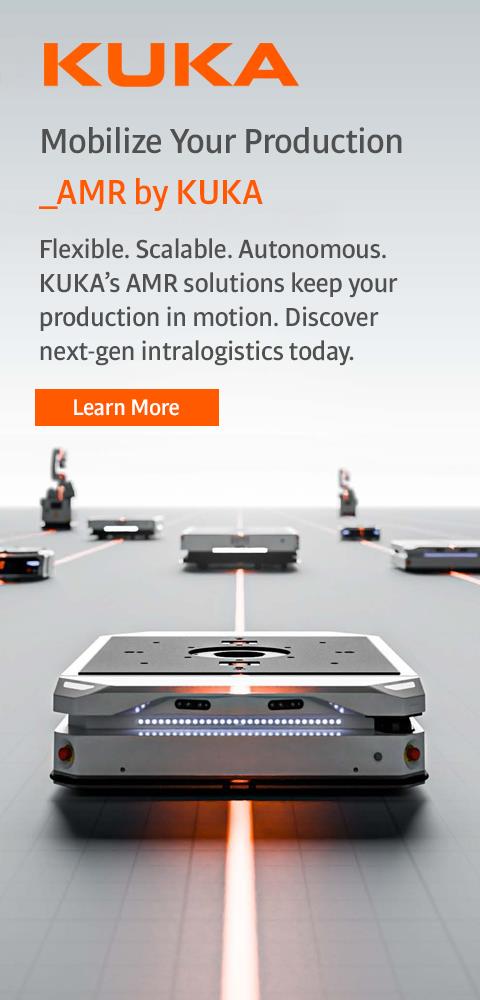
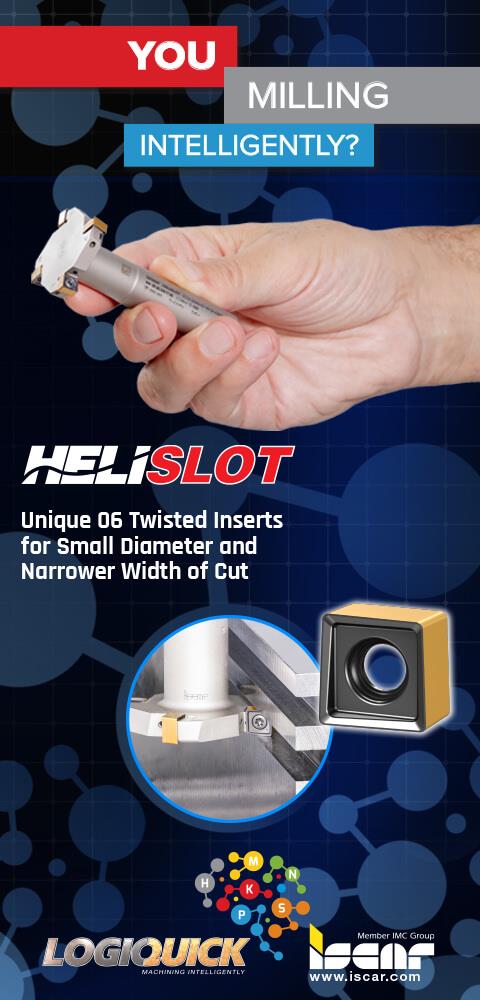
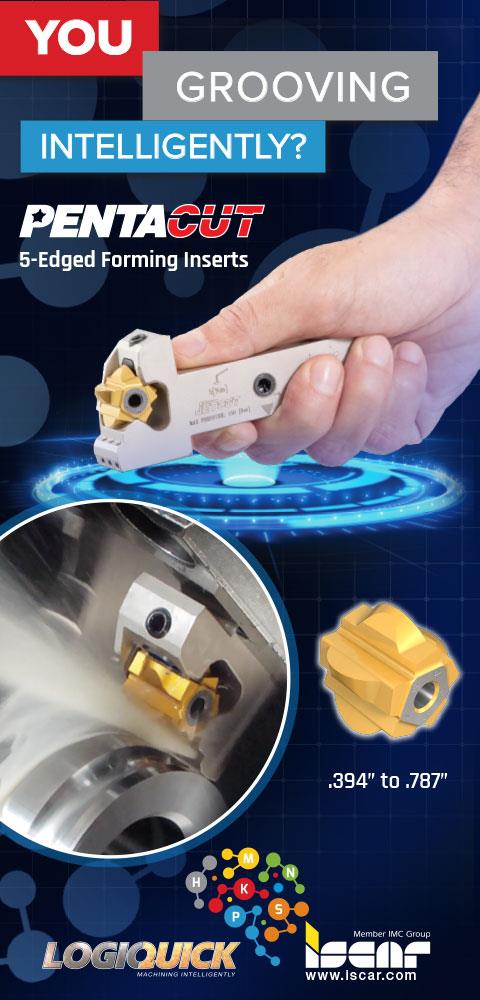
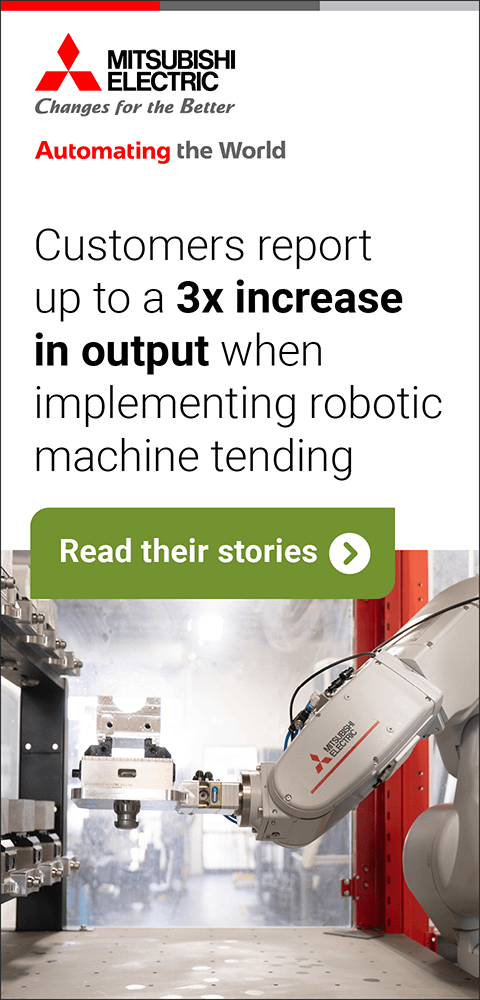
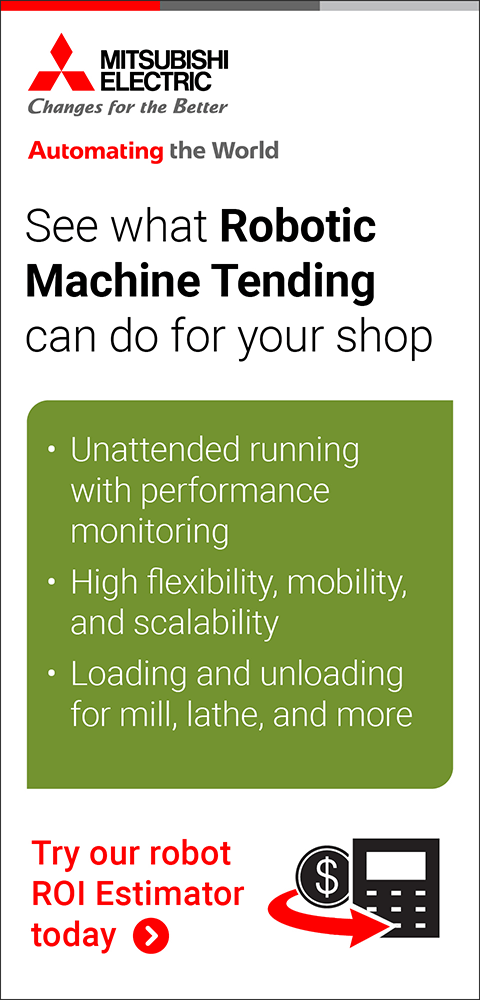
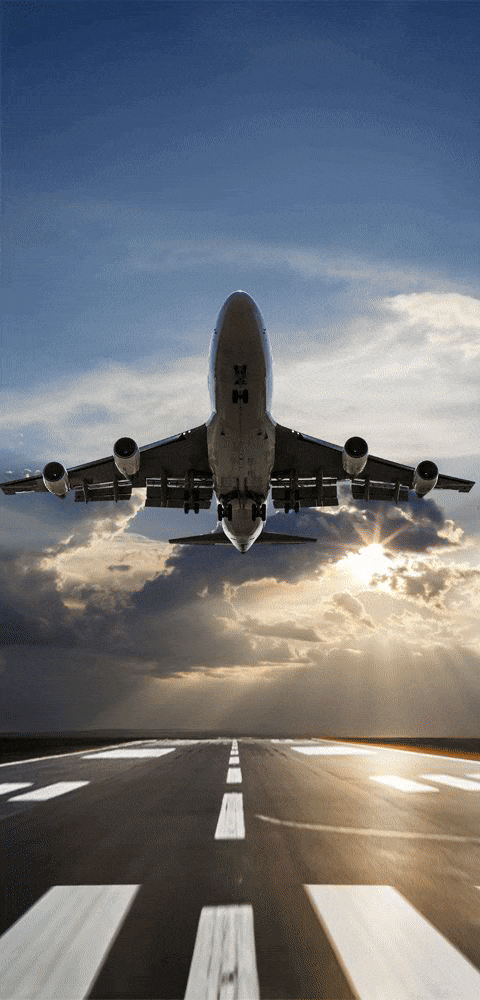
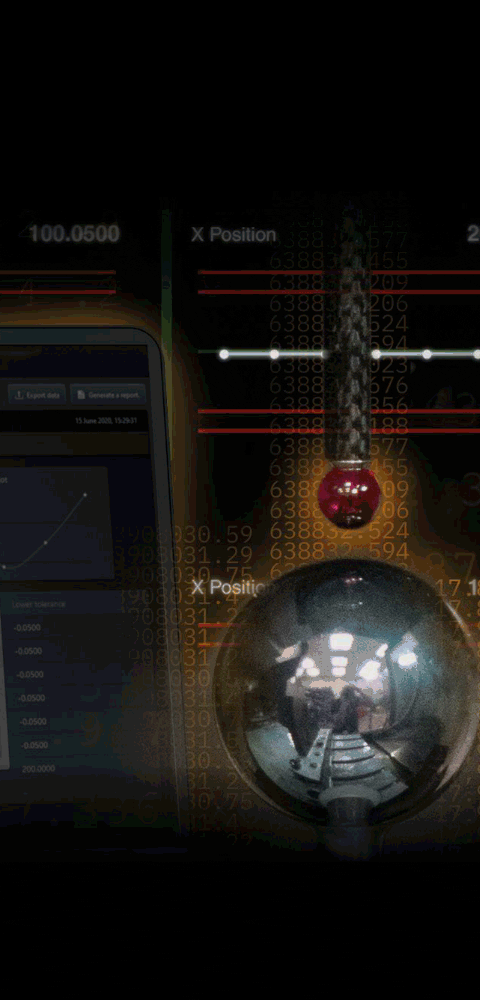
3-D Printing Technology Uses Traditional Manufacturing Materials
March 1, 2017
Collider has launched Programmable Tooling, a new rapid production and manufacturing technology designed for low volume production with a drop-in replacement for plastic casting.
Programmable Tooling is a hybrid process that first prints a hollow shell in photopolymer using continuous DLP lithography. Then, inside the same Collider machine, the shell is injected with traditional plastic casting materials. These two-part materials cure via a chemical process, and then the hollow shell dissolves in hot water. The end result is a production quality part.
"Collider's founder, Graham Bredemeyer, has an extensive history in 3-D printing and manufacturing," said a company spokesperson. "He spent several years consulting for manufacturers and 3-D printing providers and kept hearing the same complaints: customers wanted a dozen or a hundred products, but they did not want to spend thousands of dollars to cut a mold. He imagined a world without tooling costs, and recognized that 3-D printing would be the perfect complement. Thus, Programmable Tooling was born. This technology combines the best parts of plastic casting with the best parts of 3-D printing."
Customers can request material samples and submit parts for printing.
For more information contact:
Collider
100 Cherokee Blvd.
Chattanooga, TN 37450
contact@collidertech.com
www.collidertech.com
< back