
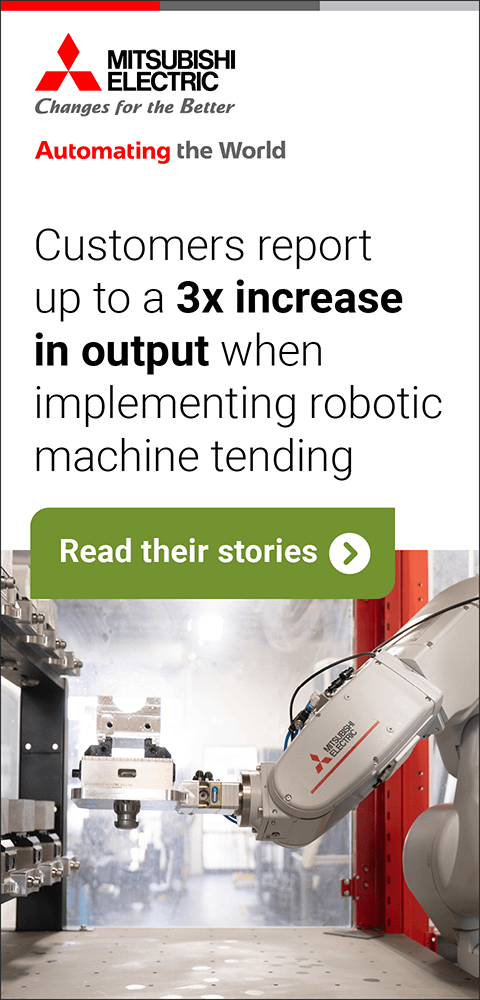
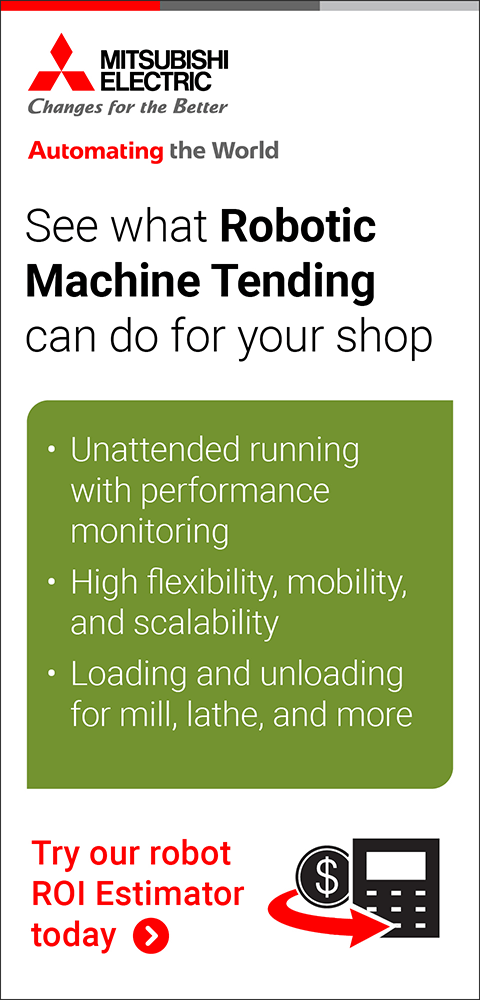
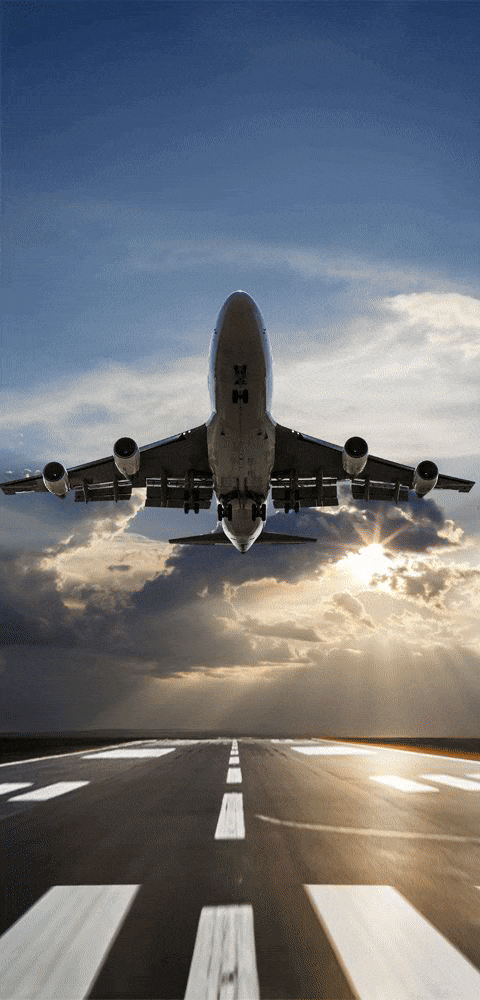
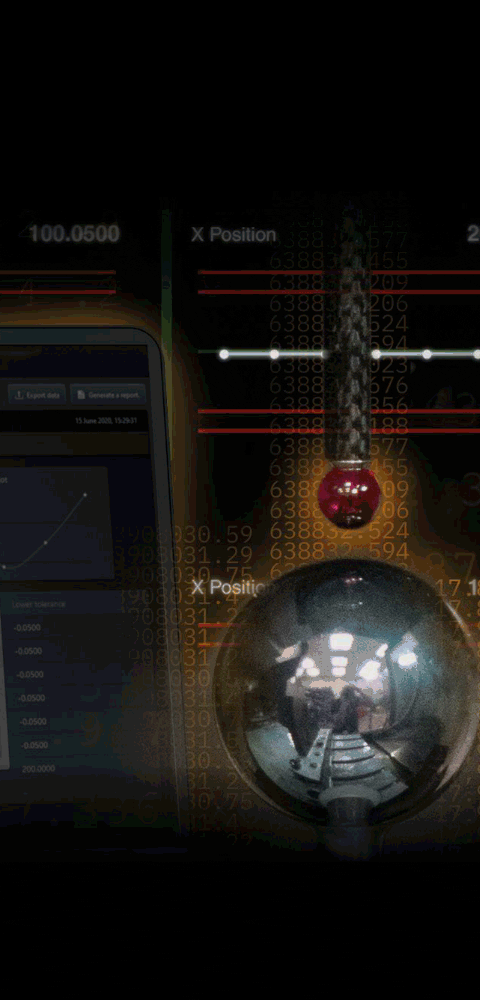
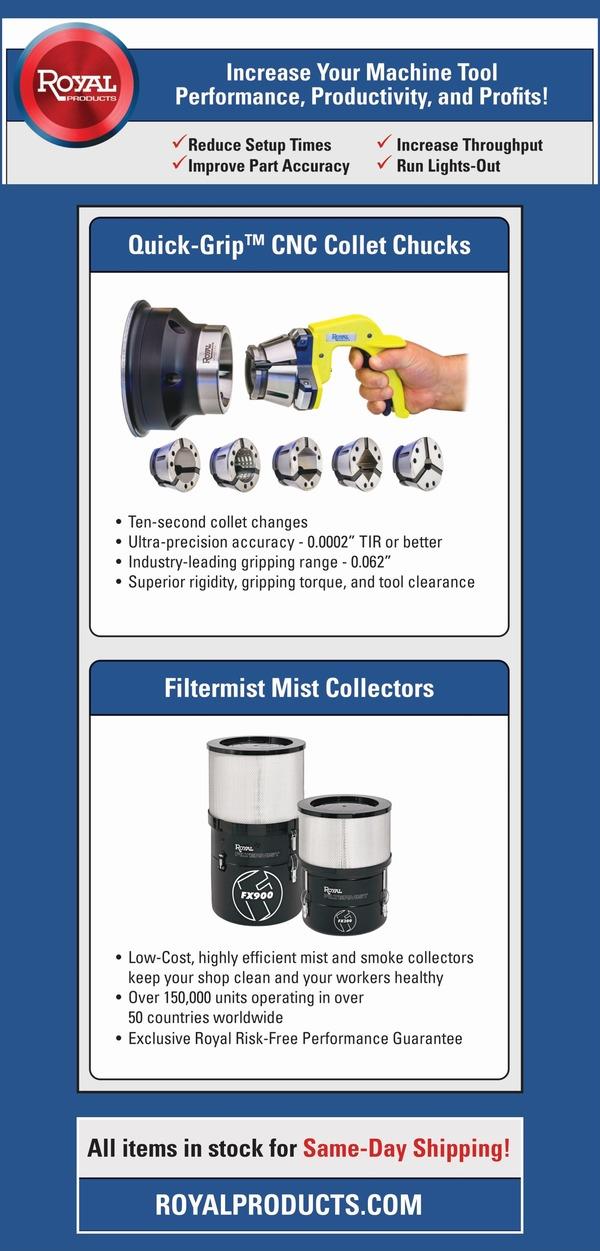
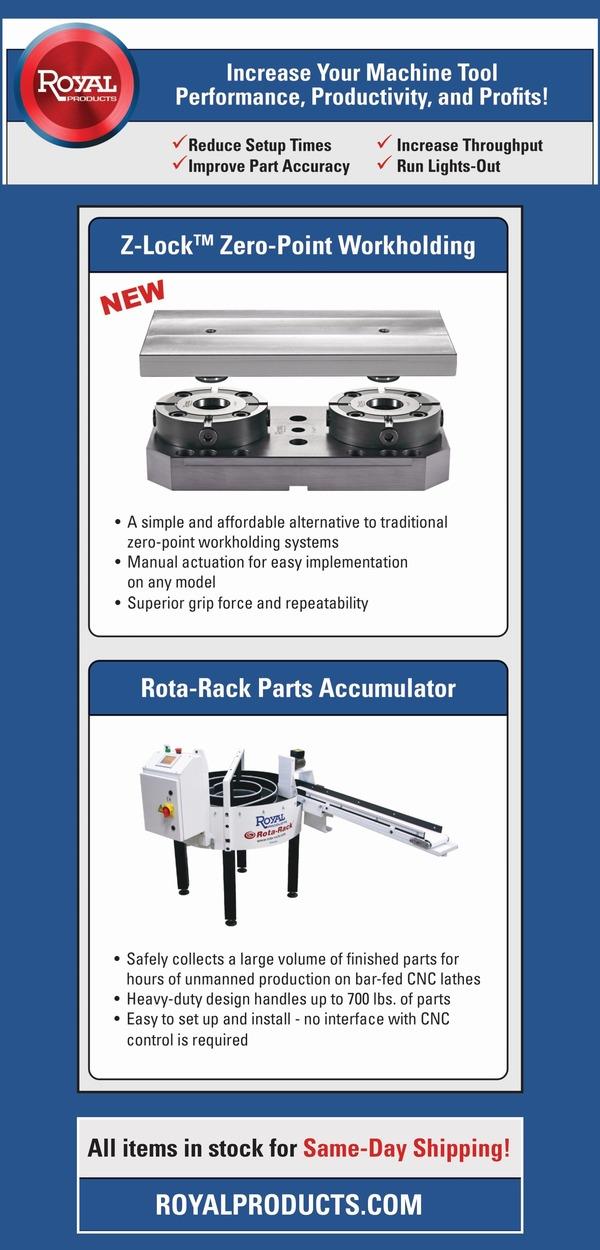

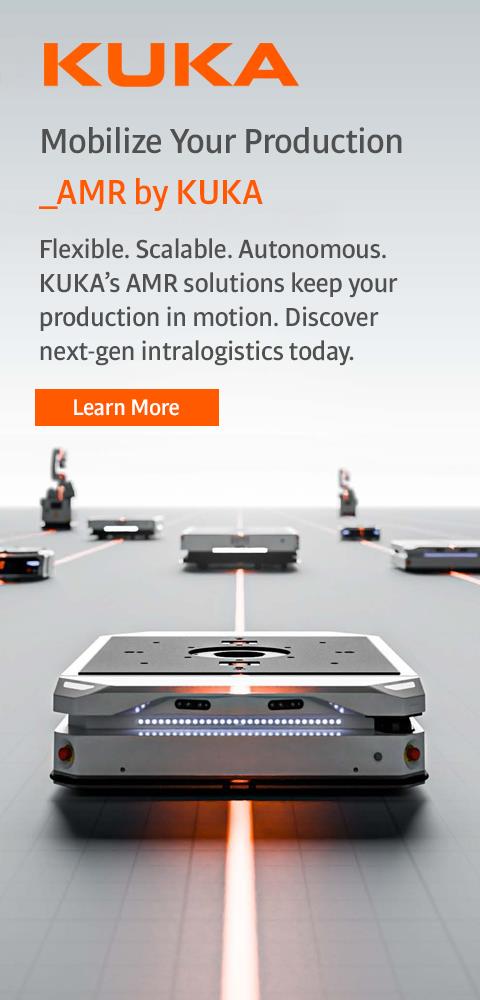
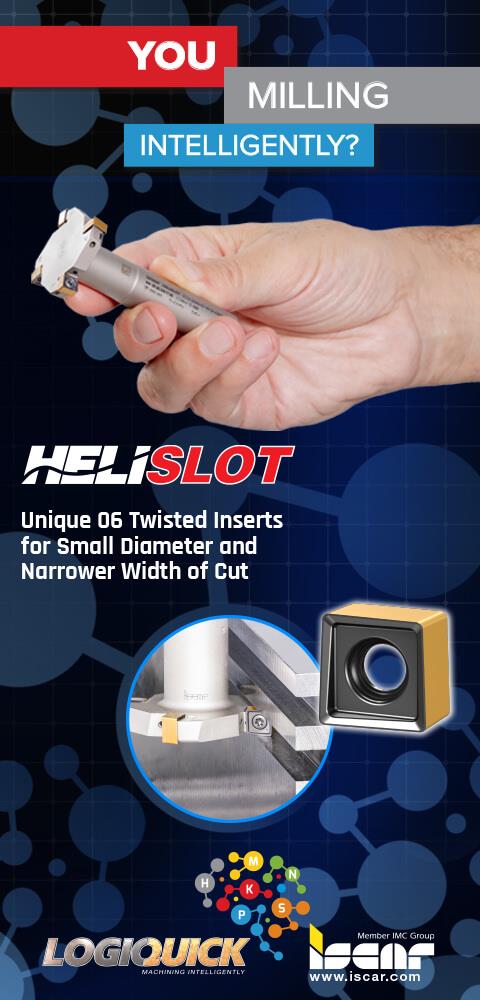
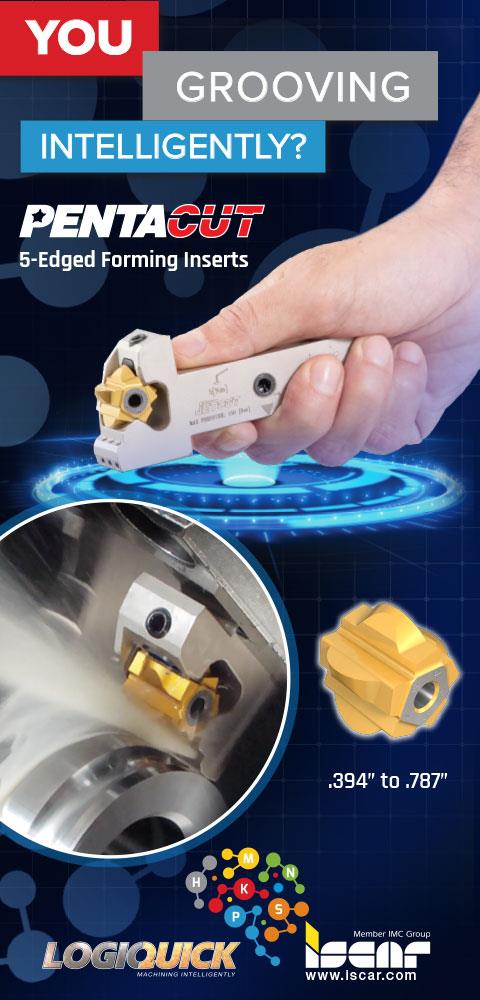
Advanced Deburring and Surface Technologies
November 1, 2016
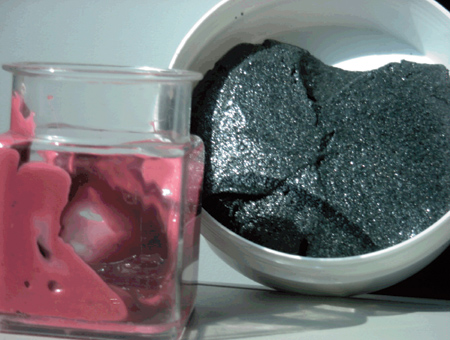
STREAMER
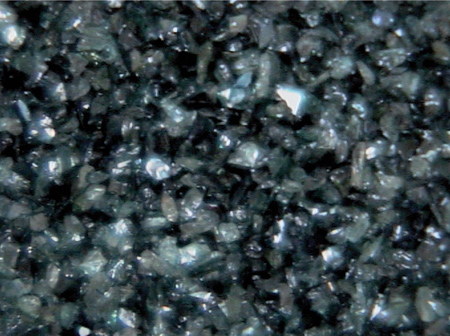
Grains
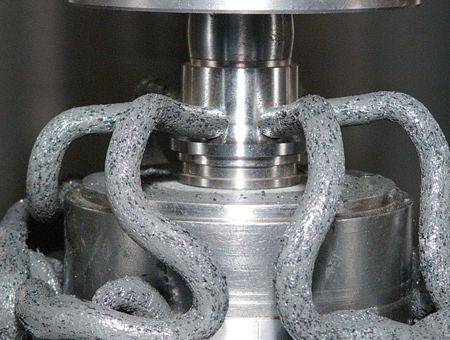
STREAMER at work
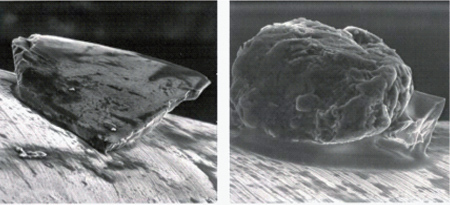
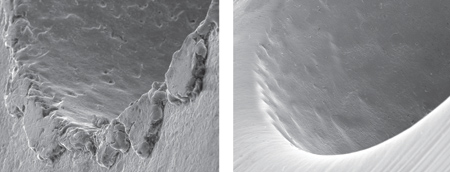
Pütz Group Micro Surfaces GmbH offers its STREAMER technology. The MicroStream flow machining is a mechanical removal process. The STREAMER is the tool for the MicroStream abrasive flow machining. The STREAMER is chemically inert, non-corrosive and non-aggressive.
All STREAMERS are a mixture of a basic medium and abrasive grains:
- Oil + stearate = gel
- Gel + polymere = base
- Base + grain = STREAMER.
Customized mixtures are produced for different applications, characterized by a certain viscosity of basic medium and a size, type and quantity of abrasive grains.
The abrasive grains that achieve removal at the workpiece are carried by the basic medium. The basic medium is a plastic mixture that has rheological properties that allow the flow machining to happen.
In principle, all types of abrasive grains can be mixed with the medium. The abrasive materials that are most frequently used in the STREAMER are:
- Silicon carbide (S)
- Corundum (K)
- Boron carbide (B)
- Diamond (D).
Applications include:
- Machining the inner surfaces of drill holes
- Machining of hard to reach drill holes, deburring gaps, grooves and edges, whereby several drill holes and edges can be processed at the same time
- Rounding edges consistently and regularly, for example tooth flanks and the edges of gear wheels.
- Removal of martensite layers following erosion.
As with any abrasive tool, the STREAMER also becomes blunt and worn with time. "After long-term tests carried out by our R&D department, we can guarantee a lifetime of 375 hours with a maximum temperature of 75 °C when used appropriately," said a company spokesperson.
For more information contact:
Pütz Group
Micro Surfaces GmbH
info@microsurfaces.de
www.microsurfaces.de
< back