
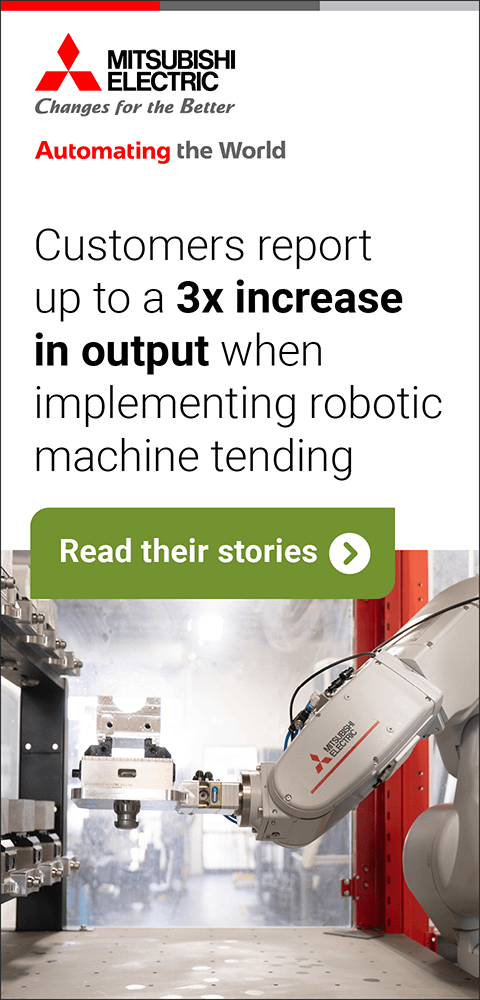
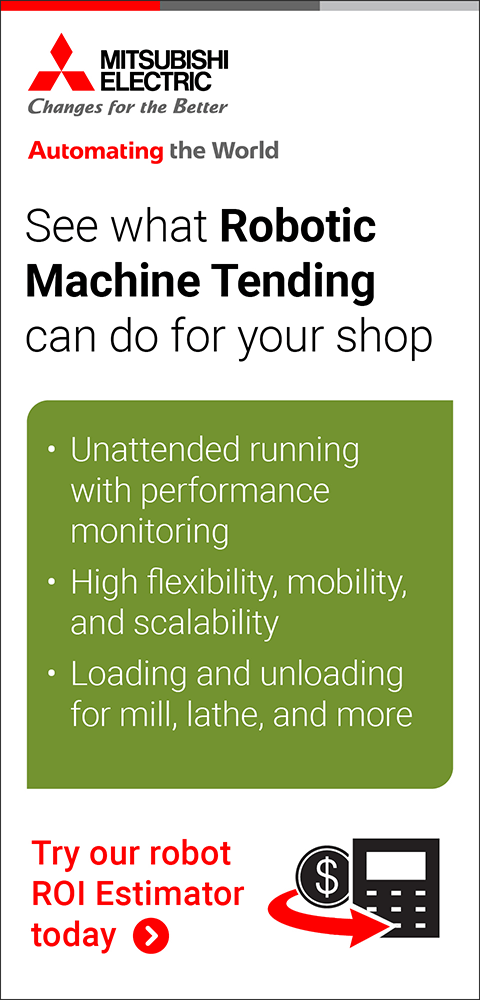
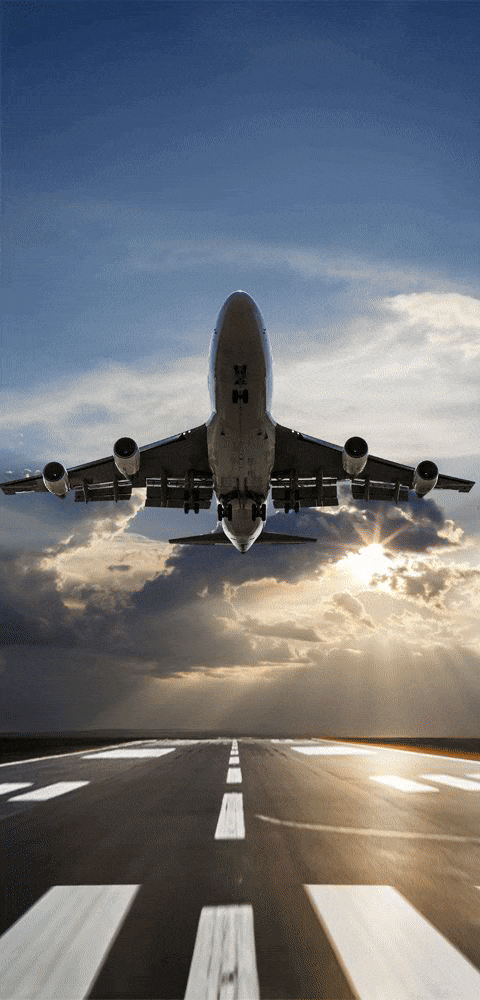
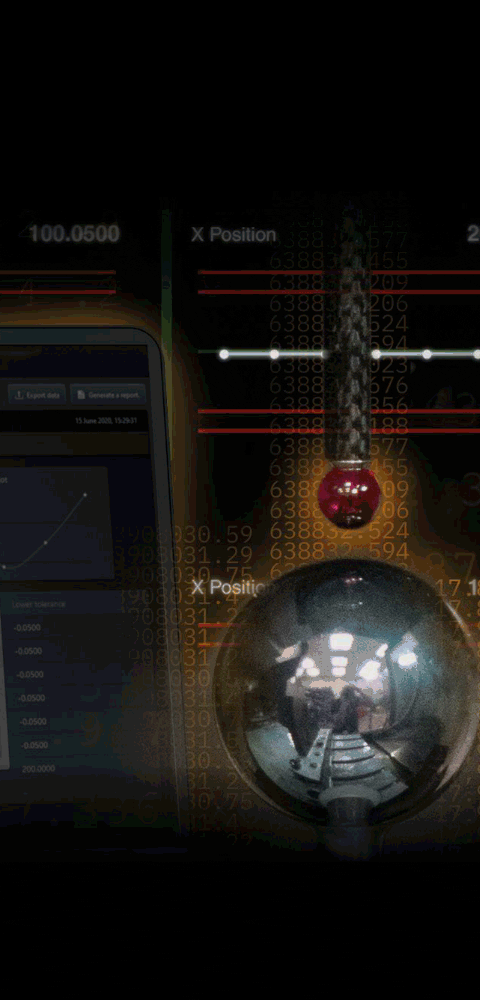
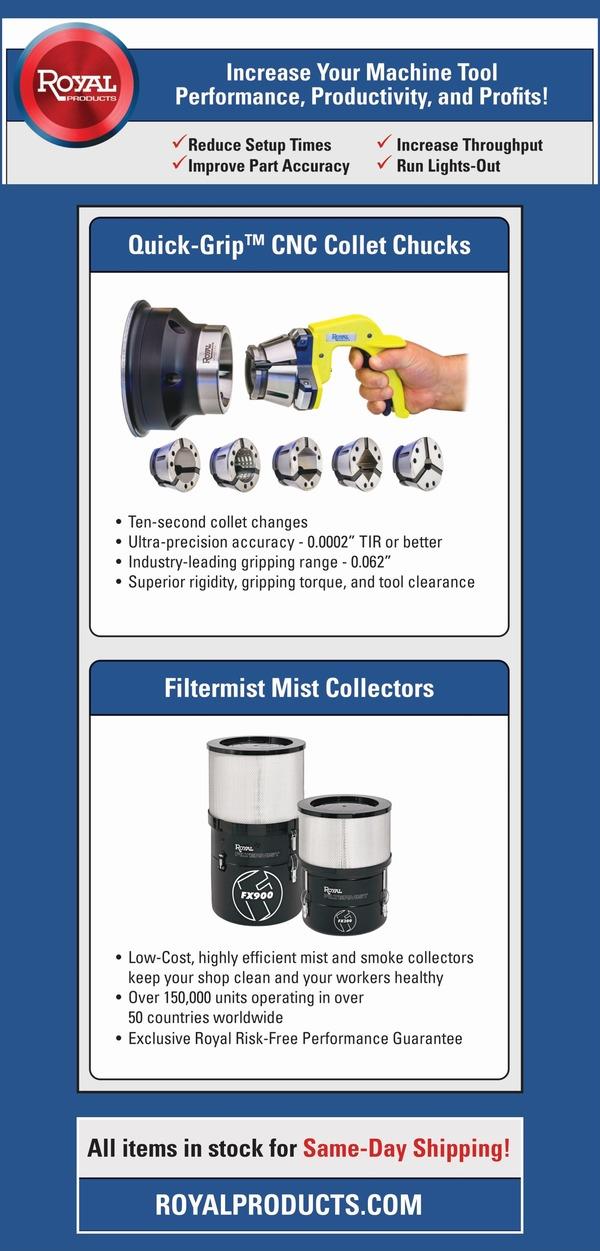
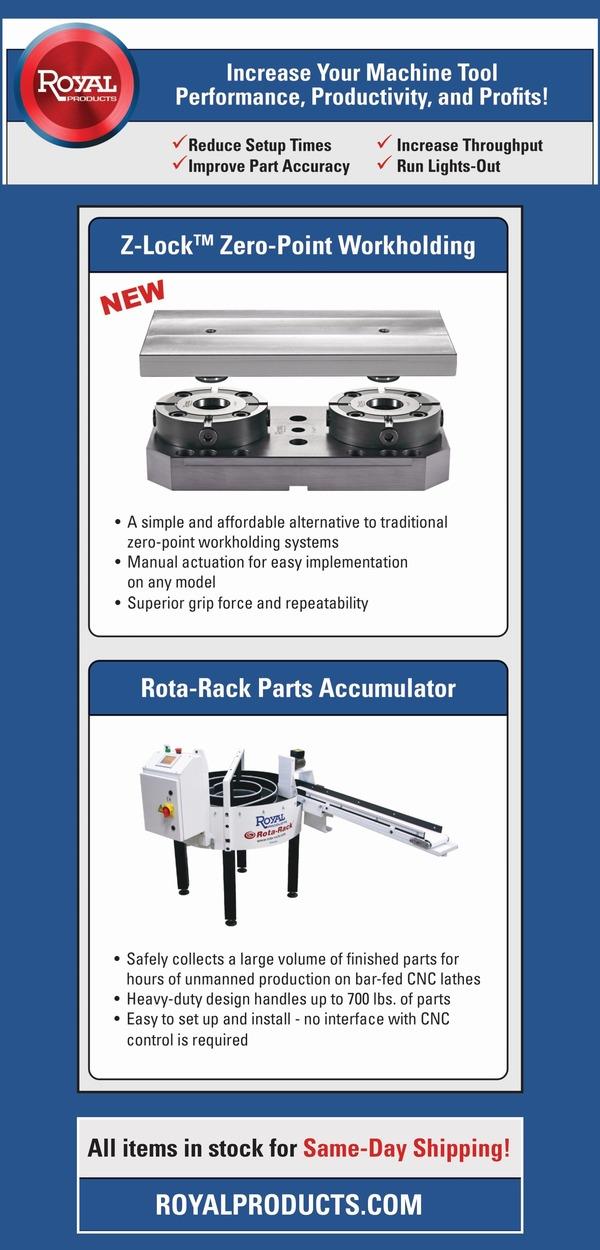

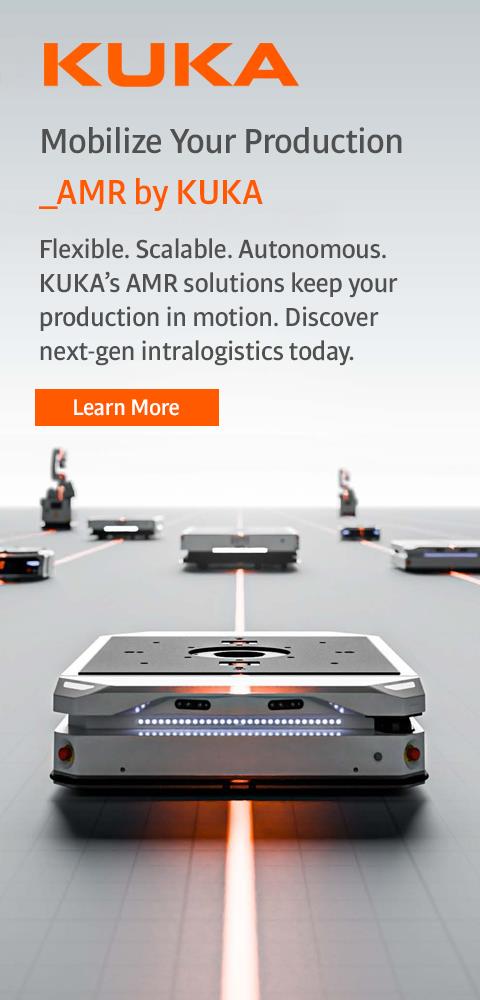
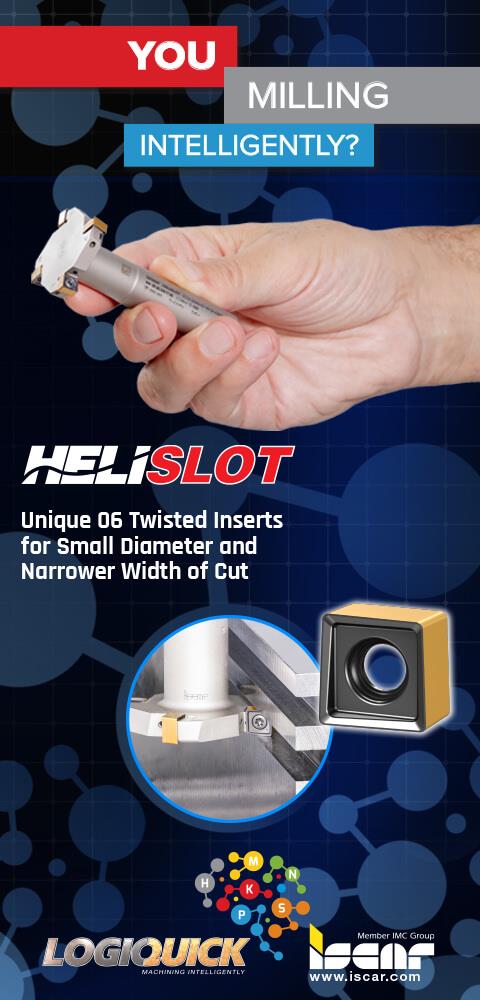
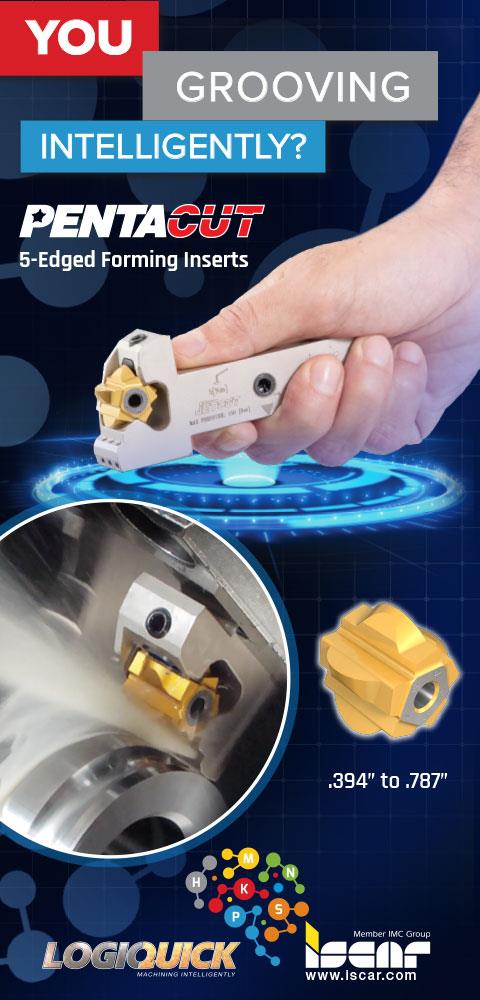
Stainless Steels: Roughing, Finishing with One Milling Tool
November 1, 2016
Mikron Tool has launched the CrazyMill Cool product family designed for fast and reliable milling of stainless steel, titanium, heat resistant alloys or even CrCo alloys. Its application field is roughing and finishing when copy milling, contour milling or face milling. Suitable industries include medical (instruments and implants), which is dependent on reliable cutting tools with a high quality, and in segments where the working material has to be heat resistant (e.g., energy industry with turbine blades, automotive or aerospace with compressors).
The carbide end mill is offered in the diameter range from 0.3 to 8 mm (.012" to .315") and for cutting depths of 2 x d / 3 x d or 5 x d.
"A straight collaboration with competent partners like carbide producers and coating specialists and the integration of different factors such as tool geometry, grinding technology and coolant supply results in high cutting speeds and surface quality in roughing and finishing," said a company spokesperson. "CrazyMill Cool end mills feature integrated coolant channels with the outlet located on the shank taper. They feed the cutting edges continuously with a consistent coolant jet and flush the chips away from the cutting zone."
The form of the channels is designed to permit a maximum quantity of coolant, even at lower pressure, without reducing the stability of the tool. The smallest diameters (from 0.3 mm / .012") with a 3 mm (.12") shank diameter need a coolant pressure of 15 bar to provide a good cooling effect.
The grinding secondary angle is designed to provide vibration free machining and, combined with a high cutting speed, a high surface quality. Changing the infeed ap and ae this tool can be used for roughing or for finishing. When roughing it is possible to go with a vertical infeed ap up to 1 x d and a horizontal infeed ae up to 0.3 x d, when finishing infeed has to be reduced to ap max. 0.5 x d and to ae 0.05 to 0.15 x d (depending on the required surface quality). Roughing means working in a vertical position; for finishing it is recommended working in an inclined angle of 10° - 15°.
For more information contact:
Mikron Corp. Monroe
200 Main Street
Monroe, CT 06468
203-261-3100
mmo@mikron.com
www.mikron.com
< back