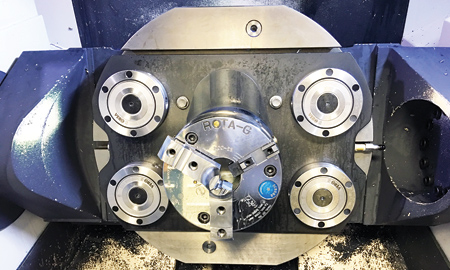
The Vero-S system features a modular design, giving Joe Gibbs Racing the versatility to quickly use any fixture on any machining center in the facility with a minimal amount of changeover time.
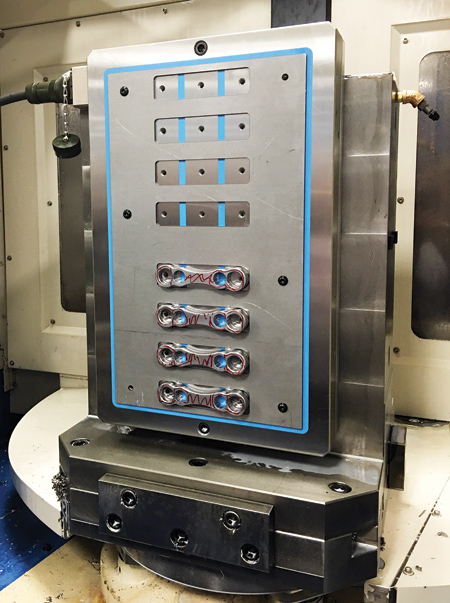
Magnet vise mounted by a Vero-S system
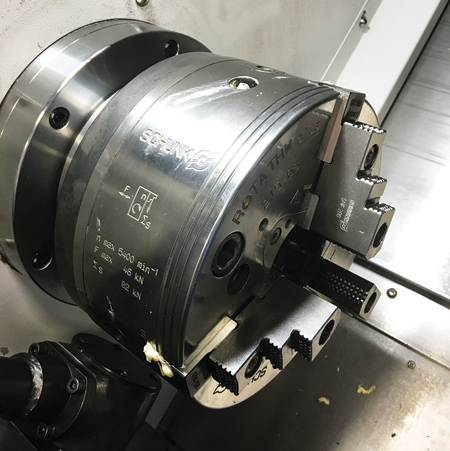
All lathes are equipped with SCHUNK chucks
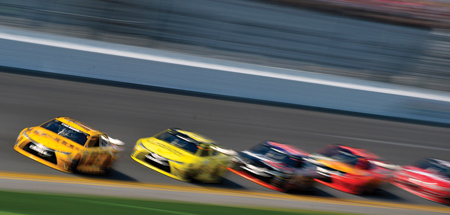
Joe Gibbs Racing produces up to 90% of the parts and components found in the cars in its 12+ racing teams.
Joe Gibbs Racing manufactures high performance race cars, motors and components. In fact, it produces up to 90% of the parts and components found in the cars in its 12+ racing teams. This adds up to more than 2,000 different parts and pieces - including engine and chassis components, suspension systems and much more - made from a wide range of materials, including steels, aerospace steels, titanium and aluminum.
"We have a high volume of jobs and super short lead times," said Dan Schnars, Manufacturing Engineer, Joe Gibbs Racing. "We can break something on Sunday, and on Monday morning we will have new drawings and models and have to turn the parts around by midweek to get them back in the race cars. Other times we have the same families of parts coming through every four to six weeks. It is a mix between chaos and families of parts that we commonly make."
"Time is crucial because we have a large concentration of engineering personnel," said Mark Bringle, Technical Sponsorship and Marketing Director of Joe Gibbs Racing. "Our 70+ engineers are constantly pushing the envelope on design and speed and making parts lighter, stronger and faster. Whenever these parts are proven out, obviously we cannot wait three or four weeks to manufacture them - they want them on the cars that weekend." To keep up with this high demand, the machine shop has 30 CNC machines operating 22 hours a day.
In the past, the machinists were inundated with scheduling, and were constantly trying to figure out how to get parts in and out of that department more quickly and reliably. In addition, rigid fixturing was needed to help achieve surface finish quality and to maintain tight engineering tolerances.
"We looked at purchasing or making sub plates for our machining centers with common bolt patterns to accommodate all of our vises and fixtures," said Schnars. "This would have required reworking several dozen legacy fixtures to make them conform to the new fixture / bolt pattern. Not only was this impractical in most situations, but it was also going to be labor intensive. It would also consume several hours of our already sparse shop capacity and machine time to design, machine and install all of the sub plates. There was going to be considerable expense in materials, tooling and special components. This was a good solution for some machines, but not for others. On some machines, the added thickness of the sub plate, coupled with a vise or fixture on top of it, would have reduced our available working envelope and would have limited maximum tool lengths and part sizes. No solution we came up with provided us with the speed, required accuracy, repeatability or rigidity. We needed a solution that would work across the board, on as many of our machines as possible, and with a minimal amount of downtime per machine to get the new system installed and operational."
The team selected the Vero-S system from SCHUNK, firstly because it was cost effective and made the most sense from a return on investment standpoint. The Vero-S system was quick and easy to mount into the machining centers with minimal negative impact on the work envelope. "On some machines, we simply bolted the clamping pallets to the tables using the existing tee slots, and on our horizontal machining centers (HMCs), we actually machined the faces of the tombstones to accept the Vero-S mounting bases so we could maximize our work envelope," said Schnars. "The Vero-S system is extremely rigid, gives us the accuracy and repeatability we need, and due to its modular design, gives us the versatility to quickly use any fixture on any machining center in our facility with a minimal amount of changeover time. It solved the challenge of not having an across the board solution."
"Installation and implementation was done in a fraction of the time it would have taken to fit and install sub plates," continued Schnars. "Accuracy and repeatability is `load and go' with well-designed fixturing. An operator can remove a pallet of parts, install a new one and not have to re-check or reset work coordinates. Our operators can also change parts outside of the machining center while another pallet of parts is running in the machine - reducing spindle off time. The rigidity of the Vero-S allows us to aggressively remove material when necessary, and allows us to hold tight engineering tolerances and surface finish requirements. The Vero-S system has been trouble-free mechanically, as well."
"With the old way, the operator put a fixture in the machine, and then had to find the zero of the fixture and program the zero - taking approximately three hours of machine set-up," said Bringle. "Meanwhile, operators could not do anything outside of the machine - the machine was down while they were switching parts over and changing parts out."
With the Vero-S system, this process now takes only 15 minutes. This includes taking the old fixture out and putting the new fixture in. "It is a quick change system, so it cut hours out of the set-up. With the Vero-S system, operators can service the pallets outside of the machine, pull the pallet out of the machine and put a new pallet in while the machine is running parts," said Schnars.
In particular, the SCHUNK Vero-S system has had a positive impact on the machining of front wheel spindles. Spindles are machined from hardened billet steel and require operations in multiple machining centers. All of the final machining is performed on 5-axis machining centers. "The Vero-S system has drastically reduced set-up and changeover time, allowing us to quickly and effortlessly switch between different part configurations," said Schnars.
"We had one specific application we were looking for and SCHUNK had the answer," said Bringle. "When we researched further, we found the whole product line to be a perfect fit for the way we do business."
To hold four stations on the HMCs, the team uses SCHUNK KSD vises on the tombstones. "They provide a universal fit in applications where we do not have the Vero-S systems," said Schnar. "In some of the systems we actually have the KSD vises under the Vero systems so we can pop the vises on and off of the tombstones as needed."
All of the lathes have SCHUNK chucks. Rail vise systems allow operators to machine multiple blanks in one set-up versus one blank at a time.
Tendo hydraulic holders are used for many roughing applications. "We are using them for applications requiring zero runout, good surface finish, long reach or accurate tooling situations, such boring or even drilling with carbide drills," said Schnars.
"The systems are set up to be used on all of our machines so we can move jobs from machine to machine throughout the shop quickly and easily," continued Schnars. "We now have the flexibility to move things around and utilize whatever resources are available. This is huge. Having quicker set-ups has freed up many hours of machining time in the shop."
Joe Gibbs Racing's manufacturing facility relies on 24 Doosan Infracore machining centers. There are 14 vertical machining centers (VMCs) with 3-, 4- and 5-axis capability, four HMCs with 4- and 5-axis capability with spindles ranging from 6,000 to 12,000 RPM and six turning centers ranging from 2- to 9-axis in capability. All machining centers are equipped with Blum probes, lasers and tactile measuring systems for tool and workpiece measurement. The facility also has Mitsubishi wire EDMs as well as a Mitsubishi sinker EDM, Hole Popper, laser, waterjet and press brake.
Joe Gibbs Racing manufactures parts and components for its NASCAR Sprint Cup and NASCAR Xfinity Series race teams, as well as parts and components for its Monster Energy and Lucas Oil AMA Supercross Teams. Parts are machined and fabricated from many different alloys of steel, aluminum, titanium, tungsten, various composites, plastics,and carbon fiber.
Joe Gibbs Racing, which started in 1992, is celebrating its 25th year of racing and has 570 employees.
For more information contact:
Joe Gibbs Racing
13415 Reese Blvd. West
Huntersville, NC 28078
www.joegibbsracing.com
SCHUNK Inc.
211 Kitty Hawk Drive
Morrisville, NC 27560
919-572-2818 / 800-772-4865
info@us.schunk.com
www.schunk.com