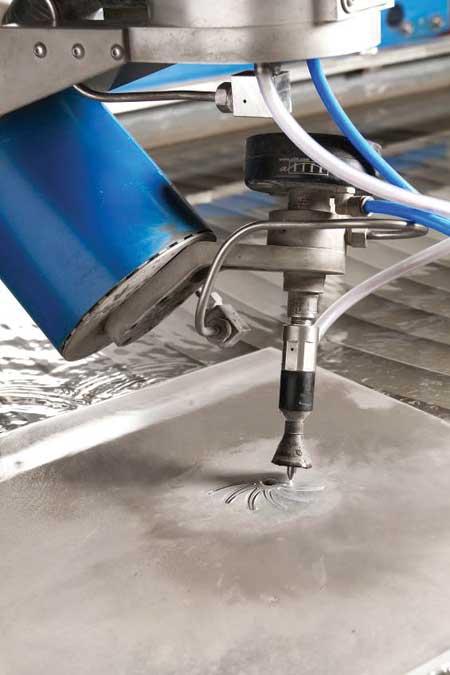
Spatial movement of the newly developed 5-axis cutting head - waterjet cutting of an impeller
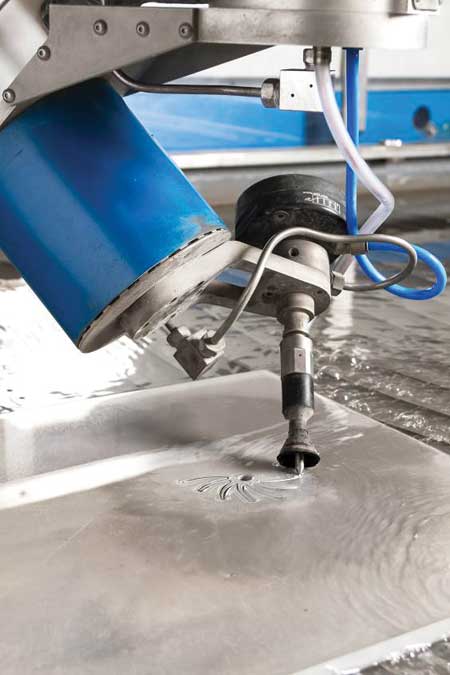
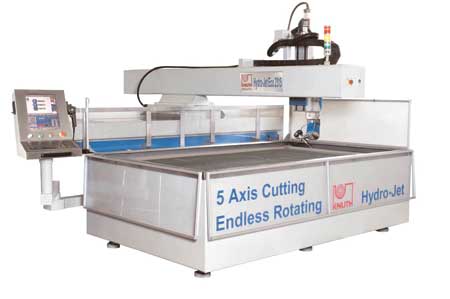
Waterjet cutting system Hydro-Jet Eco 1525 equipped with the newly developed 5-axis cutting head
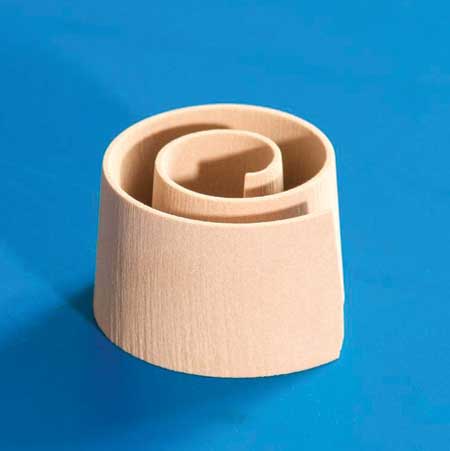
3D waterjet cutting produced spiral of a mineral hard-material, in which the spiral walls have a trapezoidal cross section (element height 25 mm, base diameter 42 mm, wall thickness above 1.5 mm and below 4.0 mm)
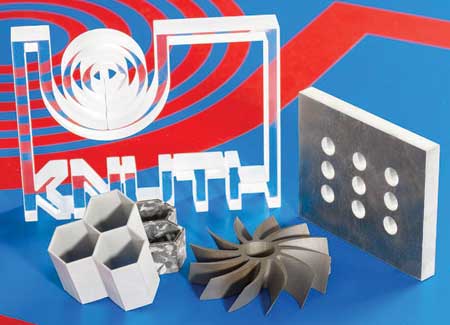
The use of the 5-axis cutting head produced specimens of various materials satisfying the following requirements (clockwise from back left): acrylic glass (20 mm thick) with the cut surfaces being perpendicular; aluminum sheet (10 mm thick) with perpendicular cut surfaces and precisely formed holes; steel impeller with smooth blade surfaces which have a defined curvature; honeycomb-shaped structures with a constant wall thickness, cut from a 40 mm thick aluminum plate (remaining wall thickness of 1 mm) as well as from 20 mm thick artificial stone (remaining wall thickness 2.5 mm)
KNUTH's Hydro-Jet, 2D waterjet cutting systems designed for various industrial sectors, can now be optionally equipped with a 5-axis cutting head. "The feature of endless rotation offers advantages for the processing of cutting jobs," said Dr. Ingo Decker, Technology Consultant at KNUTH Machine Tools. "This cutting head also allows higher component accuracies for 2D cutting with increased cutting speeds due to the compensation of the downwardly tapered cutting kerf by an adapted angular setting."
According to the company, compared to both plasma cutting and laser cutting, waterjet cutting has gained importance in recent years. Today, waterjet cutting is an industrially accepted cutting technology. Since waterjet cutting does not require electrical conductivity of the material and is not dependent on a sufficient absorption of the laser beam, it can be used for a variety of materials. By adding an abrasive to the high-pressure waterjet, material can be effectively removed within a narrow cutting kerf.
"In contrast to the thermal cutting methods, there is no critical overheating of the cut material by the 'cold' waterjet cutting, even at very slow feed," said Decker. According to the company, waterjet cutting can also be used for large workpiece thicknesses up to more than 4". "An interesting circumstance that sets waterjet cutting apart is that the flatbed-waterjet cutting systems not only cut surfaces which are perpendicular to the sheet surface, but they also beveled cut surfaces which are inclined by any angle required," explained Decker. For this process, according to the company, the cutting head requires axes X, Y and Z and two additional axes of rotation. This makes it possible for the waterjet to be set under any required angle to the surface at any location in the working area of the cutting machine.
According to the company, the 5-axis cutting head developed by KNUTH is based on the design principle of the nutator. In this design, the two axes of rotation are at a 45° angle to each other: on one hand, a rotation around the Z-axis and, on the other hand, a rotation around an axis orientated under 45° to the Z-axis, which forms a 45 nutation cone when the cutting head rotates around the Z-axis. According to the company, the tip of this nutation cone is chosen as the "Tool Center Point." During waterjet cutting, this is the point of contact for the stream on the workpiece surface. Rotational movements of the cutting head lead to no change of position. "This has the advantage that for a change of the waterjet direction no compensatory movements of the X, Y or Z axes must be made," explained Decker. "The modern 5-axis cutting heads from different manufacturers are designed predominantly according to this principle."
The rotation around the Z-axis, according to the company, creates the limitation that it cannot run endlessly without further measures. This occurs because the supplies for electrical energy, electronic signals, compressed air, high-pressure water and the abrasive must be transferred into the cutting head and these cannot be wound up multiple times. "In particular, the feeding hose for the abrasive must be vacuum-compatible and free of setting edges in order to guarantee a uniform dosage of the abrasive," said Decker. "Because of this limitation, the machine control has to be implemented with a numerical tool ensuring look ahead that during the operation on the cutting contour, all the necessary rotational movements can be performed without having to re-rotate the cutting head in between."
According to the company, there are cutting head assemblies in which rotation around the Z-axis is not necessary due to a special lever mechanism which generates the inclinations of the cutting head. "However, this principle frequently used in plasma cutting systems has the disadvantage that it cannot hold the counterforces of the emitted waterjet as well as the nutator arrangement with its high rigidity," explained Decker. For waterjet cutting, this mechanical stability is most important in order to achieve a high accuracy of the cut parts.
"To overcome the limitations of the rotation around the Z-axis, at the 5-axis cutting head developed by KNUTH, suitable rotary feedthrough were selected for all supplies. For electricity, compressed air and high-pressure water existing feedthrough solutions have been chosen. However, a special rotary element had to be designed for the abrasive that allows a continuous transport of the abrasive sand under the various conditions of processing and for the different sand properties. This has been solved successfully, so the waterjet cutting systems from KNUTH can now be equipped with an endlessly rotating cutting head for 3D cutting as an option," continued Decker.
According to the company, the following are advantages of this 5-axis cutting system:
- Restoring movements of the cutting head are avoided and thus the non-productive times of the machine operation are reduced
- Rapid changes in angle can be performed by the cutting head which otherwise would not be permitted due to the compensating movements of the other axes and their available acceleration capacity
- Contours can be created without interruption of the cutting process, which require rotations around the Z-axis with a multiple of 360° (e.g., cutting of spiral contours).
"The maximum angle of inclination is +/-51°," continued Decker. "The cutting head has been designed so that components subject to wear are used only in a minimal number. Only one rotary element is installed in the high-pressure water supply. The overall structure is designed so that the necessary service work can be executed comfortably and needs to be done only at long intervals."
According to the company, the erosion process in the cutting kerf is characterized by the fact that the kerf width becomes smaller downwards. This effect is more pronounced the higher the cutting speed selected. In the most extreme case, this is half the kerf width at the waterjet entrance. Therefore, the requirement for high accuracy of the cut part requires the setting of reduced cutting speeds in the case of a pure 2D cutting machine. According to the company, this also significantly improves the cut surface quality. "With the help of the 5-axis cutting head, however, the inclination of the resulting cut surface can be directly compensated by a corresponding angular setting of the cutting head," explained Decker. "The angle to be adjusted is dependent on the momentary cutting speed, on the type of material and on the plate thickness. It is automatically calculated by a special software (taper compensation). The efficiency of a waterjet cutting system can be significantly increased especially in the case of high accuracy requirements."
According to the company, the deviations of the cut surface from the target level can be observed well below 0.1 mm. This occurs not only at the upper plate surface (entry side of the high-pressure waterjet) but also throughout the cut surface. "With good alignment of the motion axes and with a new cutting nozzle and focusing tube, high-quality holes with smooth inner surfaces can be produced having diameters at the top and bottom side, which differ only by 0.01 mm for up to 40 mm thick material," said Decker.
For more information contact:
Knuth Machine Tools USA
590 Bond St.
Lincolnshire, IL 60069
847-415-3333
info@knuth-usa.com
www.knuth-usa.com