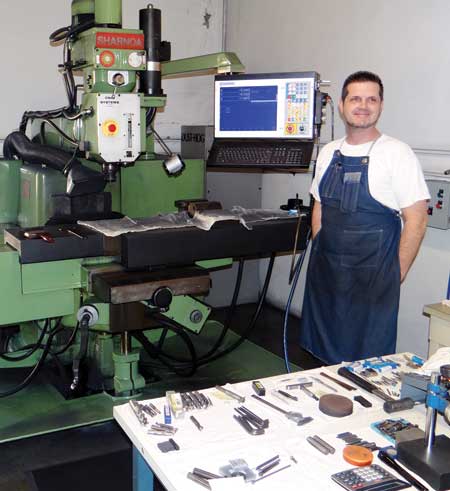
Atticus Overbay, Head of Research and Development, RPM RC Products, with the Sharnoa CNC knee mill with new Centroid M400 CNC control upgrade.
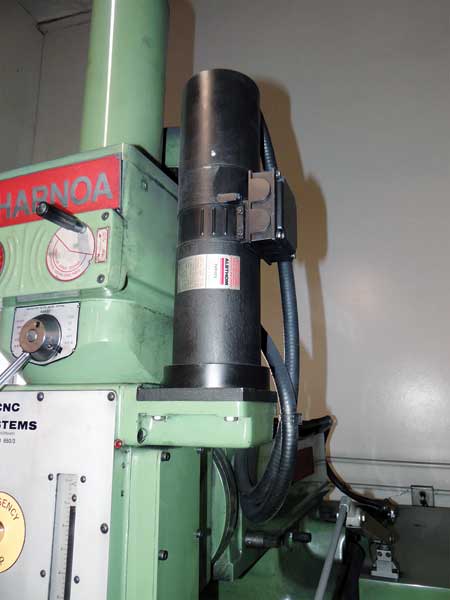
The original servo motors were retained during the Sharnoa's upgrade (Z-axis shown).
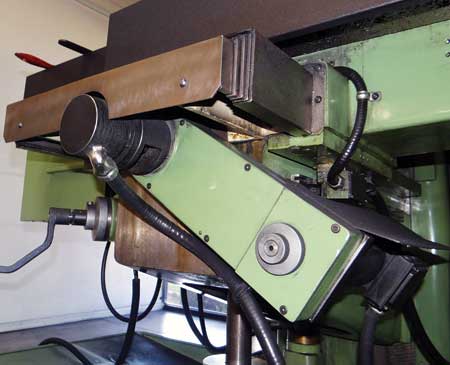
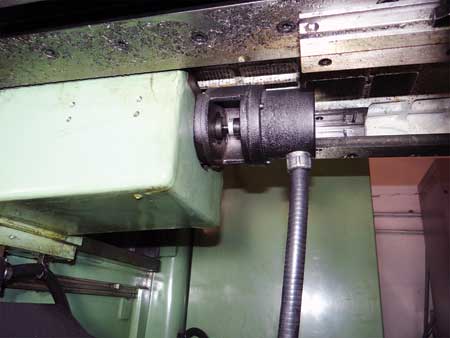
The X- and Y-axis encoders are mounted to the ends of the ballscrew and were upgraded to a high resolution unit during the upgrade.
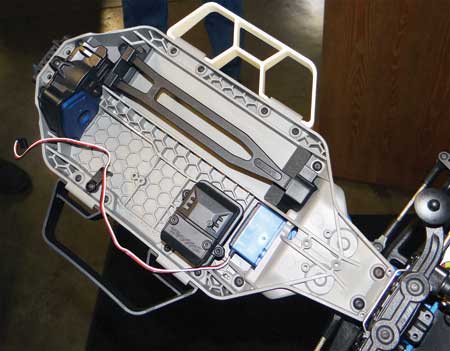
A prototype high performance side bumper (or nerf bar) can be seen in beige colored plastic. The prototype is used to check fit before production run begins on the Sharnoa.
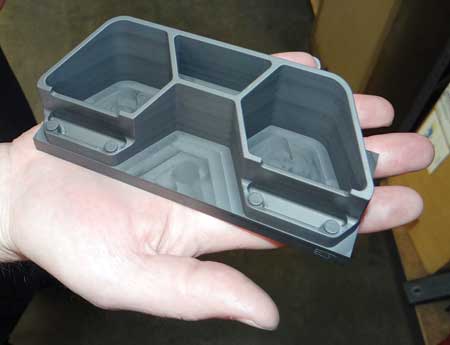
The high performance side bumper, a graphite electrode, after machining on the Sharnoa.
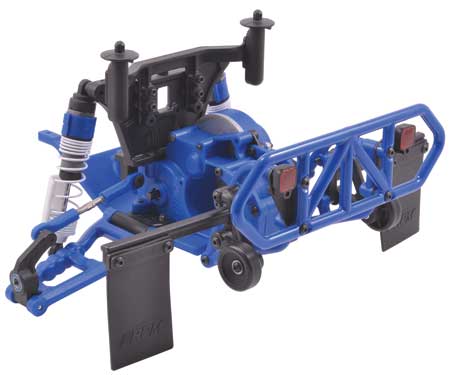
This image shows a whole series of radio controlled car parts manufactured by RPM RC Products for one particular vehicle. The only molded items not produced by the company are the shocks and the internal components of the gear box.
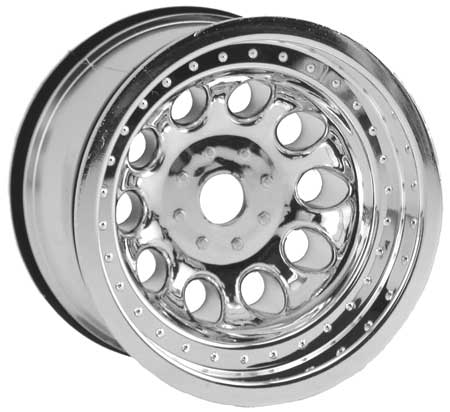
One of many styles of scale wheels produced by RPM RC Products.
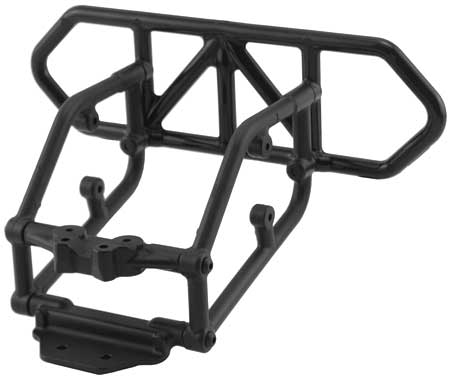
A complete rear bumper system manufactured by RPM RC Products.
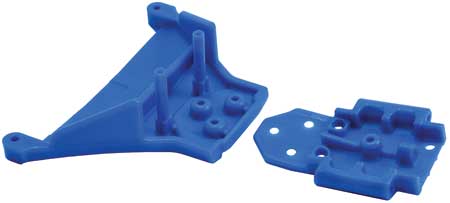
This bulkhead assembly has a curved bottom, while the front piece has multiple parting line angles in both directions.
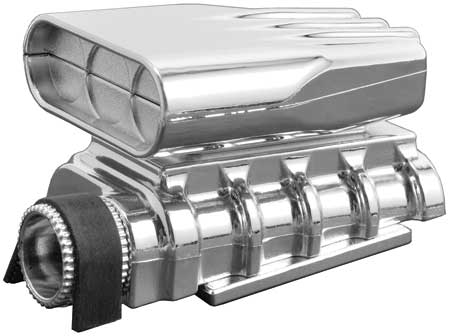
A faux blower system in 1/10th scale. It is used for dressing up the appearance of a radio controlled car.
RPM RC Products specializes in making high performance parts for the radio controlled vehicle industry. RPM maintains control of the design and quality of its R/C parts by producing every component of the injection mold process in-house. RPM purchased a Sharnoa CNC knee mill new in 1987 for this purpose, and it has provided reliable machining. Over the years, as RPM grew into 3D machining of precision carbon electrodes for moldmaking, the Sharnoa mill control could not keep up. The control was slow (point to point), and it started having electrical problems.
While the basic machine was still functioning perfectly, the memory was rated in kilobytes. "A simple 3D program could not run without using DNC, and its DNC capabilities were severely limited as well," said Atticus Overbay, Head of Research and Development, RPM RC Products. "For example, running in anything other than G17 (X/Y circular interpolation) was out of the question. That means everything done in X/Z or Y/Z planes had to be done in small, straight line segments - and our programs were huge."
The old DNC program could not communicate fast enough with the machine, so toolpaths could rarely be run at full feedrate speeds. "The machine would bog, waiting for the next line of instruction, especially when our line segments for small radii would be about .001 inch - .003 inch in length," said Overbay. "If we were running 40 IPM, it could bog to as slow as 10 - 15 IPM during those times.
"When we began considering an upgrade to our machining center, we were looking at updating the control and computer systems. While we would have loved to bring in a new machining center to replace our outdated system, it simply was not necessary. Our Sharnoa machining center could still hold tight tolerances on all three axes, so we just needed an updated computer and control system."
A new Centroid M400 CNC control was installed in the Sharnoa by Doug Laursen of Machines in Motion. The original servo motors were reused, making the upgrade simple. There was no mechanical work required to fit new motors. The M400 CNC control uses Centroid's own digital DC servo drive, which, according to Centroid, is a very robust unit and can drive almost any DC servo motor up to 15 amp per axis. "If servos are in good shape and can be reused during an upgrade there is a cost savings," said a Centroid spokesperson. "In this case, reusing existing servos saved over $3,000 in the cost of the upgrade."
These particular Sharnoa machines have the X and Y axes encoders mounted directly to the end of the ballscrew. While not typical for a knee mill, this set-up does produce good results as long as the servo motor to ballscrew mechanical system is in good shape with low lash (play). Laursen upgraded the old encoders with new modern high resolution units during the installation of the Centroid M400 CNC system.
"With a new controller, we were now back in business with software that can cope with our increasing 3D programming requirements," said Overbay. "We now have more than enough memory for our needs and we can finally work in G18 / G19 modes, reducing our overall file sizes dramatically since we can now interpolate curves in alternates axes."
Overbay uses Mastercam version 6 to program the 3D G-code to create the carbon electrodes. He said the Centroid handles the large programs with no problems and he likes the ability to stop, check his work and restart at any point. He solid models his parts to get all the angles and drafts just right before committing to machining carbon or steel.
"Our programs are smaller, our finishes are significantly better and our cycles times are reduced by at least 50% since we are not working with slow DNC communications," said Overbay. "That means feedrates are at full speed. I can now cross-hatch 3D parts in less time than what it would have taken to run the same part in only one direction using our old controller.
"Before, we would try and use small step-overs but would never cross-hatch our parts due to the ridiculously long cycles it would have created. For example, traversing in only one direction would have easily taken three hours to run a single electrode in one direction. Now, it may take two hours to run that same part, but this is with a cross-hatch program. So, we are technically running the 3D surfacing part of the program twice - once in X/Z and once in Y/Z - in less time and with better detail. Additionally, we are not locking up or dedicating a computer system to run DNC any longer since the new system can accommodate longer programs with full functionality."
RPM RC Products produces around 95% of its own parts and products. Most are fairly small, molded components for high-end R/C cars. RPM makes the electrodes and molds and does the injection all under one roof.
Rohart Precision Molds, Inc. was founded by Richard Royall as a partnership that was soon dissolved into a corporation with Royall as President. Early on, RPM built molds for large corporations such as Rain Bird, Toro and Mattel, among others. The company also provided parts for kites and spray guns, as well as products for the medical industry, to name a few. In the early 90s, Royall bought a hobby-grade R/C car for his son but soon found flaws in the vehicle. With his naturally mechanical way of thinking, he fixed those issues and soon found a niche in the industry, spawning the creation RPM R/C Products. Now, 90% of what the company produces is for its own product line, but the company still has a few outside customers, including several that have been with RPM for 20+ years.
Capabilities include five molding machines ranging in size from 50 to 120 tons with shot sizes up to 18 oz. The tool room features a Sharnoa 3-axis machining center with Centroid controller, two sinker EDMs, several surface grinders, vertical mills, a lathe, saws and cutter grinders.
Since the company has its own product line, it has a packaging operation so customers that have needs requiring complete, ready to ship product can be easily met.
For more information contact:
Atticus Overbay
Head of Research and Development
Rohart Precision Molds, Inc. (RPM R/C Products)
14978 Sierra Bonita Lane
Chino, CA 91710
909-393-0366
rohartmolds@rpmrcproducts.com
www.rpmrcproducts.com
Centroid
159 Gates Road
Howard, PA 16841
814-353-9256
sales@centroidcnc.com
www.centroidcnc.com
Machines in Motion, Inc.
993 Carbon Canyon Rd.
Chino Hills, CA 91709
714-528-7061
centroid.controls@gmail.com
www.cnc-machine-controls.com