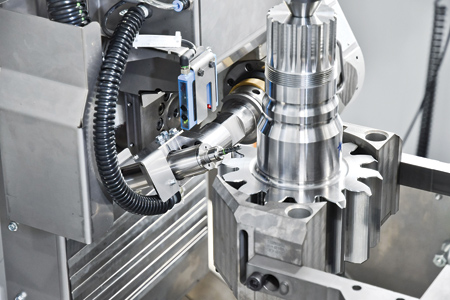
The LC 500 DC offers high performance in an optimal machining chamber
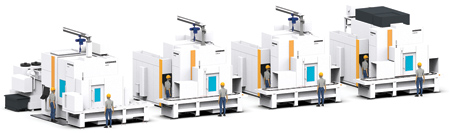
An overview of the machines on the redesigned platform.
Liebherr-Verzahntechnik GmbH has overhauled its gear cutting machine platform for workpieces with a diameter up to 500 mm. The new machine generation now provides more flexibility. The highlight: easy chamfering during the machining process is now possible using either ChamferCut or FlexChamfer.
"What is clear when looking at the modern, monolithic design is that a lot has changed with this new generation," said Thomas Breith, Head of Product Management for Gear Cutting Machines at Liebherr-Verzahntechnik GmbH. "But it is the technical improvements in this comprehensive overhaul that are even more remarkable. In the past few years, we have continued to improve the machine platform for machining workpieces with a diameter up to 500 mm, optimizing the machine bed, the chamfering device and the machining head."
The machine bed was completely overhauled. For dry machining, the machine table, machine column and box guideways have been lined with stainless steel plates, offering improved chip evacuation. This means that, in particular, the temperature behavior remains constant, providing greater gear quality and process stability. The reworked HH240 hob head on the LC 500 gear hobbing machine with its longer travel ranges and improved rigidity in its counter bearing offers high performance. Optional add-ons include a swivel-in measuring probe and a mobile meshing device for centering the tool into the workpiece.
What is unique about the new generation is that an optional chamfering device can be integrated into the machine, providing two possibilities for chamfering during the machining process: the fast and economical ChamferCut process and FlexChamfer, which chamfers using common end mills and is suited for small batch sizes.
"This means that two chamfering technologies have been integrated into one machine," said Breith, "something that is unique on the market."
An automatic ringloader transports the workpiece from the main machining position to the perpendicular chamfering position. Internal gears can now even be chamfered on the gear shaping and gear skiving machines. Longer travel ranges and optimized rigidity also provide more stability and thus greater process reliability.
The user comfort and ergonomics of the machines have also been optimized. A larger machining chamber, fold-out steps and glass maintenance doors make it easier to access the machine and encased hydraulic units make it quieter. The control panel with its LHGearTec user interface has also been improved. The fixed LHStation monitor unit as well as the LHMobile handheld terminal, both equipped with a Multi-Touch interface and context-sensitive user guidance, make it even easier to use and program the intuitive controls. Although the monolithic design of the machines makes them seem larger, their footprint is in fact smaller than that of previous units.
In order to be able to satisfy the requirements of a variety of sectors from heavy industry to automobiles as well as other industrial applications, Liebherr has always relied on a modular machine concept. According to Breith, "Our gear cutting machines are robust, high-quality and can be individually configured. Different table drives, machining heads and automation solutions as well as optional accessories satisfy a wide range of applications. We were determined to continue this tradition in our new machine generation."
For more information contact:
Liebherr Gear Technology, Inc.
1465 Woodland Drive
Saline, MI 48176-1259
734-429-7225
info.lgt@liebherr.com
www.liebherr.com