
Cell control panel
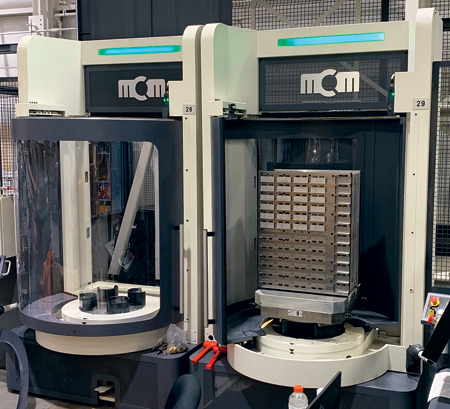
Loading stations
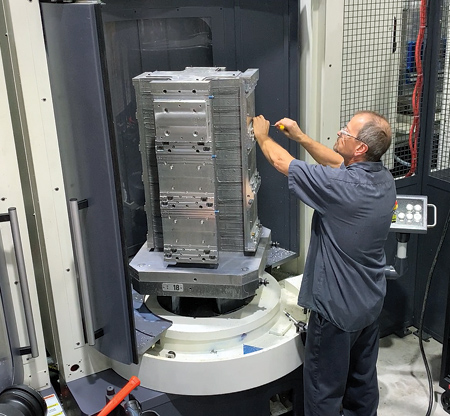
Loading a tombstone
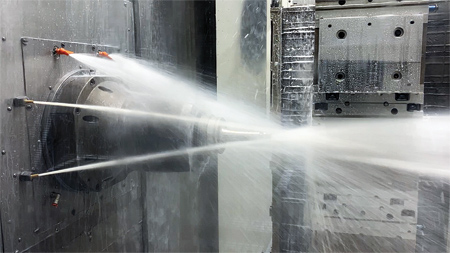
Machining aluminum parts
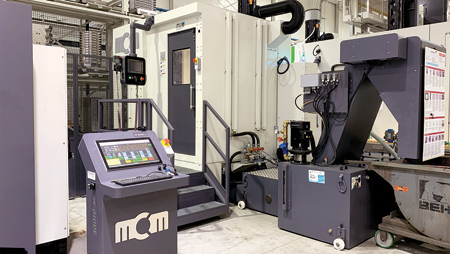
MCM CNC cell
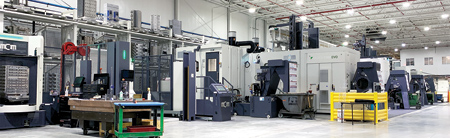
MCM Flexible Manufacturing System (FMS)
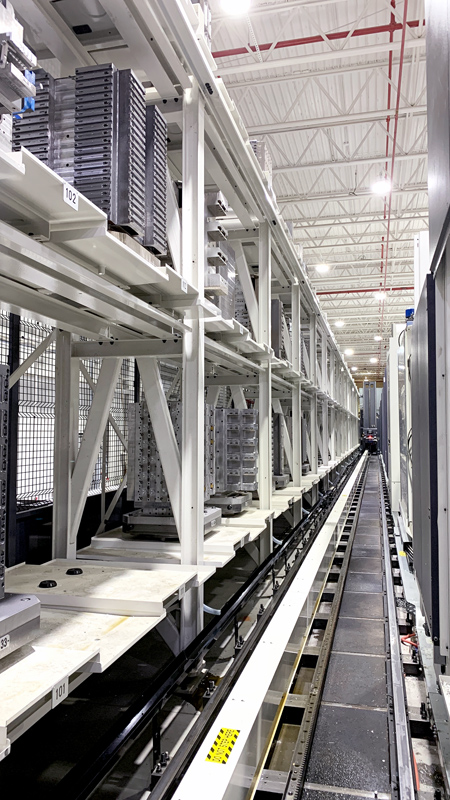
MCM rail line
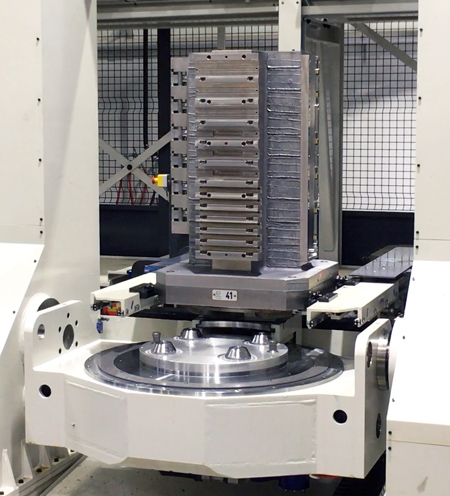
Tilt load station
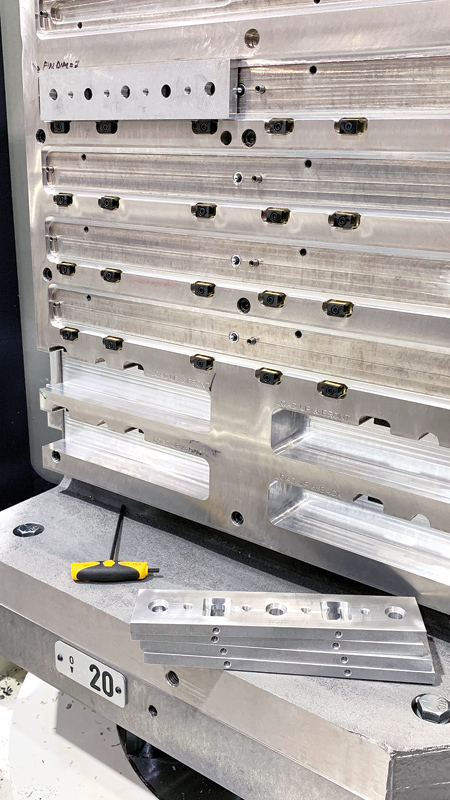
Loading a tombstone
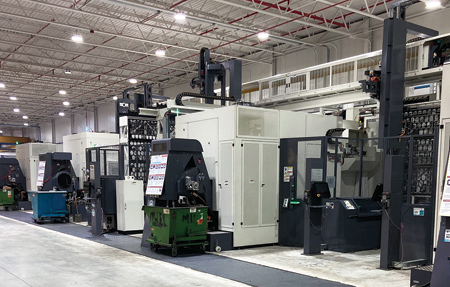
Four MCM Clock 1200s with 630 mm size pallets
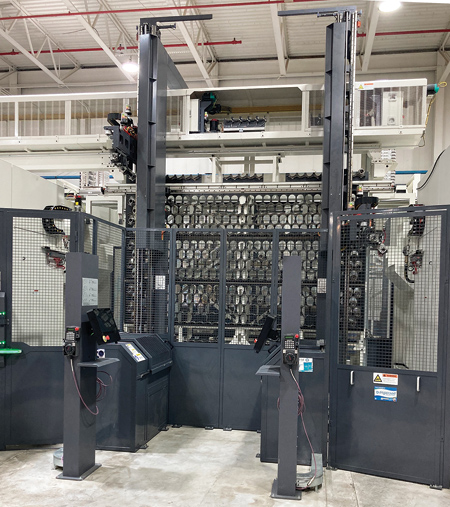
With the 499-tool shared tool changers between two machines, either machine can use any tool.
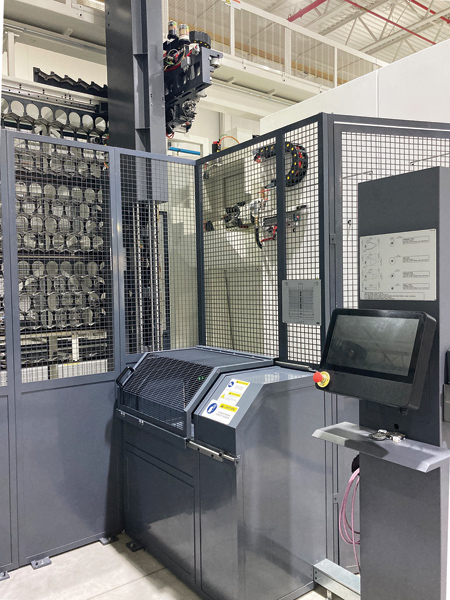
Tool loading at each machine with tool indentation and cleaning.
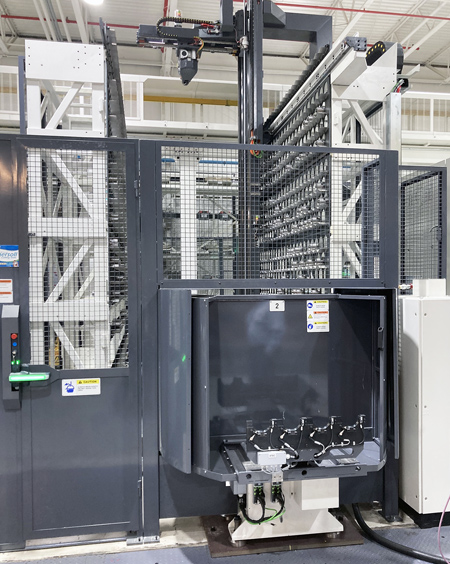
The centralized tool room will feed any machine support tooling. SUPER TOOL features 704-tool capacity.
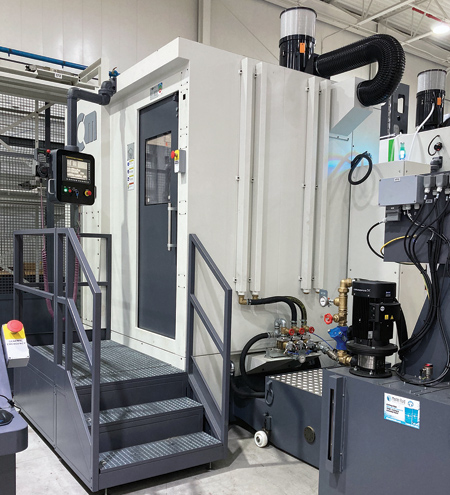
Automatic filtering system from the 98-pallet system.
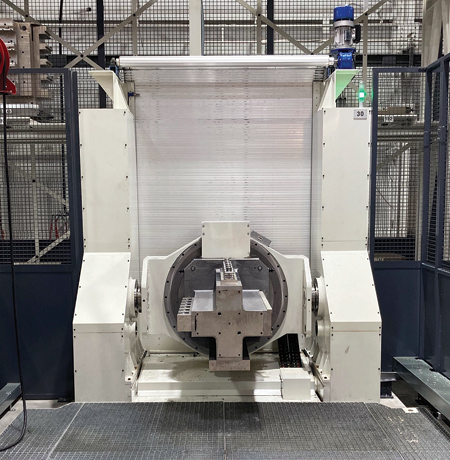
Rotary tilting fixture loading and part loading system.
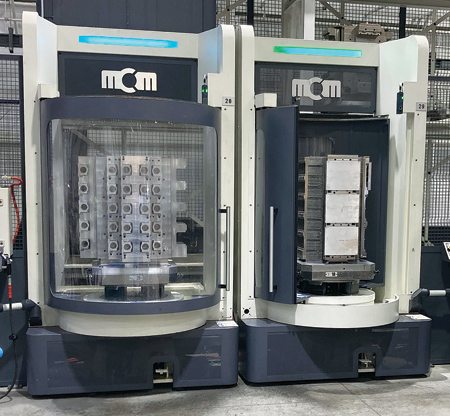
Two-pallet part loading stations.
PBC Linear found itself at a crossroads. Its aging equipment required obsolete replacement parts, its workforce was dwindling and traditional manufacturing processes were becoming unsustainable. PBC Linear needed a solution that would ensure consistent production levels while maintaining product quality.
After extensive research and consultation, the leadership team decided to invest in a new state of the art machining center, the MCM CLOCK 1200 EVO, part of an MCM Flexible Manufacturing System (FMS). According to Tim Lecrone, Director of Manufacturing Engineering, the Flex MCM system offers a myriad of advantages over traditional manufacturing set-ups and several key features influenced PBC Linear's decision.
Increased Efficiency
The MCM CLOCK 1200 EVO eliminates the need for breaks and shift changes, allowing the manufacturing process to run seamlessly 24/7. This significantly increases production efficiency and reduces downtime. This system increased productivity by 40% over the older system and runs unattended 24 hours a day, 7 days a week.
The system consists of four CLOCK 1200 EVO machines with full 4-axis, 3,600,000-position tables, each with 630 mm size pallets, HSK-A-100 spindle taper, 76.4 HP spindle with 14,000 RPM, high pressure coolant of 1,160 PSI, auto compensating of spindle bearing load and vibration spindle sensing. Each spindle is designed to maintain excellent accuracy and performance along its complete life cycle.
Additional features include:
- Chip separation hopper for ferrous and nonferrous chips material via M-code
- Air purged/high precision pressurized optical glass scale feedback system of all linear axis. Accuracy for each linear axis is ±.000008"/axis; rapids for all axes is 2,952 IPM
- Chip conveyors are built into the system
- Mirror image machine right and left with 398 common tools and auto verification sensing via Balluff chip and tool shank washing.
- SUPER TOOL 704 tool storage system feeding any machine in the cell
- 90 pallets on three levels
- Fixture storage system 98 total
- 3,300 weight on each pallet
- Wash station with auto parts and fixture washing
- Tilting/rotary fixture and parts loading station and two separate parts loading stations
- The machine is built according to UL standards.
The systems use the FANUC 31i-B5 numerical control equipped with a variety of options and a 21" full touch display. The system includes tool monitoring, oil separator, full enclosures and Renishaw RMP60 probes.
Precision and Consistency
Automated systems ensure a higher level of precision and consistency in manufacturing processes, reducing the margin of error by allowing multiple parts to be loaded onto a pallet.
The Renishaw RM60 radio frequency probe maps the location of each part on the pallet for accurate positional location. This single feature improved the quality of the part by eliminating the variation of parts being loaded into work vises with positive stops. Each part in the MCM can have its own exact probed location.
Machine accuracy of the four machining centers has been laser aligned and qualified. The addition of spindle cooling and machine base thermal-unit control aids in stable positional accuracy. This allows for linear positional accuracy of 4 µm and repeatability of 3 µm.
The Renishaw probing system is not only for accurate workpiece location, but is also used for post machining part inspection. This added feature also frees up the operator for more critical tasks.
Skill Agnosticism
Unlike a factory machinist who may require specific skills for a particular task, automated systems can be programmed for various functions, making them adaptable to changing production needs. For example, the MCM CLOCK 1200 EVO high speed 14,000 RPM spindles allow for high-speed deburring, which allows for deburring inside the machine before the cycle is finished. The CLOCK EVO also has a separate pallet washing station that cleans coolant and debris from the workpiece so that parts can be sent to the customer or outside process when unloaded from the pallet. PBC Linear was able to redeploy deburring operators and machine-washing operators to more meaningful task to help solve the dwindling workforce issue.
Cost Savings
While the initial investment in automation technology can be substantial, the long-term cost savings are considerable. Switching from 25 HP spindles that rotate at 6,000 RPM to the CLOCK EVO 60 HP spindles that rotate at 14,000 RPM allowed PBC Linear to reduce many of the part cycle times by over 50%. Cycle time reduction coupled with labor reduction of parts loaders, deburring operator and washing operators reduced work in process (WIP) queues by eliminating two operations, so the ROI was obvious to the leadership team.
Occupational Safety
Like many manufacturing companies, PBC Linear has an aging workforce, and operator safety and ergonomics is top of mind. Repetitive single part loading, hand deburring and lifting heavy baskets on to conveyor fed parts washers has significantly been reduced by the MCM CLOCK 1200 EVO. The machinist who works on the CLOCK EVO no longer stands on a platform to load and unload vises and pallets. The CLOCK EVO has a loading station with 90° tilting station that allows the pallet to tilt in a horizontal plane for ease of loading workpieces. The tilting loading station also rotates 360°, so all faces of the pallet can be changed in a comfortable ergonomic position.
New Level of Integrated System Flexibility
Implementing an automated FMS involved a comprehensive strategy for PBC Linear. The transition required retraining of existing staff to operate and maintain the automated system and ensuring a smooth integration with minimal disruptions to ongoing production. MCM provided installation of the FMS, operator training, programmer training and training for the powerful jFMX software package, which is the operating system that allows the monitoring and visualization of the system status. A production planner can determine the priorities of the scheduled workpieces to meet on time delivery to customers while scheduling noncritical queue times to machine parts to replenish part inventories. This allows the CLOCK EVO to operate 24/7/365.
Based on reviews with machinists who have used both systems, the newer CLOCK 1200 EVO FMS system is faster in terms of cycle time and overall user experience. It has a higher initial set-up time for first time runs or prototypes, but any repeat machining of previously completed parts is easier and more consistent. According to Lecrone, "It is definitely solving a lot of the previous system issues and brings a new level of integrated system flexibility that allows for less restrictive planning."
Material used at PBC Linear is primarily 6061 T6 and some structural steel, 70/30% mix with 70% being aluminum. Component types vary from billet to extrusions and cast/metal injection molded pieces. All of them are machinable using a proper tombstone fixture layout that takes each part's limitation/need into account. The scheduling of the jFMX system on the CLOCK 1200 EVO FMS makes for a much better due date and task management experience and allows for maximum productivity for any batching of jobs.
The MCM CLOCK 1200 EVO HMCs have XYZ stroke of 1,200 mm, 1,000 mm and 1,100 mm; spindle max. speed of 14,000 RPM; max. spindle motor 76.4 HP or 57 kW; and an ATC capacity of 199 tools per machine magazine, with cross over from the mirrored magazine arrangement, and counting the central tool room a maximum capacity of ~1,200 tools.
Linear actuator carriages, plain bearing pillow block housings, linear shafting, heavy structural bearing mounting plates and many other components have already been machined on the MCM FMS. Processes are mill type but cover milling, boring, profile cutting and grooving. Each CLOCK 1200 EVO is equipped with a calibrated Renishaw probe that allows for comprehensive locating and qualifying within the machine and allows for more advanced techniques than could be employed on the previous systems due to their probes being unable to hold 0 without calibrating each set-up. Set-up time for the CLOCK EVOs vs. the previous machines is longer initially, but every time after the job is run it is a simple call and recheck to be running at full speed. The old system required a lot more monitoring and set-up on each run. Typical reductions in cycle times are 40%, some jobs more and others less depending on the part and tolerancing required for performance. Final products are smoother, more consistent and overall, require less rework.
"The leadership team at PBC Linear exemplifies the proactive approach that businesses must adopt in the face of a shrinking workforce," said Lecrone. "Embracing automation through the implementation of the MCM CLOCK 1200 EVO has not only safeguarded the company against labor shortages but has also positioned the PBC Linear as an industry leader in efficiency and innovation."
PBC Linear was founded in 1983 by owner Robert Schroeder and has 224 employees.
For more information contact:
Kirk Wescom
Marketing Communications Manager
PBC Linear
6402 E. Rockton Road
Roscoe, IL 61073
815-389-5600
marketing@pbclinear.com
www.pbclinear.com
MCM USA Inc.
215 5th Ave.
Chardon, OH 44024
440-286-2148
service.usa@mcm-group.com
www.mcm-group.com
Richard Ragnini
RBR Machine Tools
8408 Wilmette Ave.
Darien, IL 60561
630-971-8729
www.rbrmachinetools.com