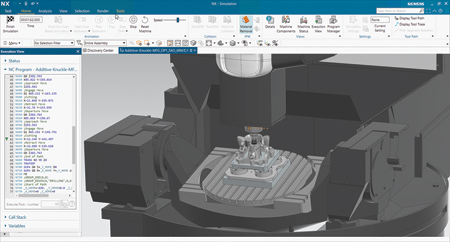
NX CAM G-Code driven simulation of the 3D printed steering knuckles
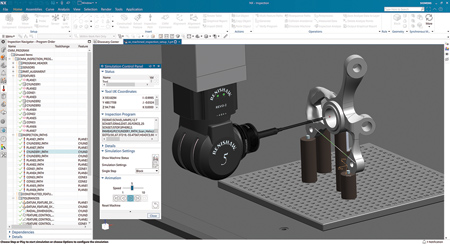
NX CMM inspection programming of the finished steering knuckle
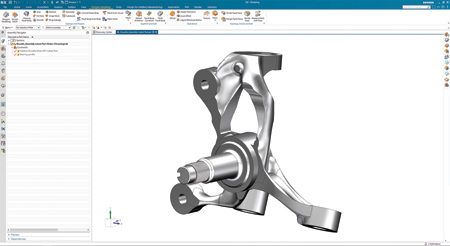
NX Topology optimization of the steering knuckle
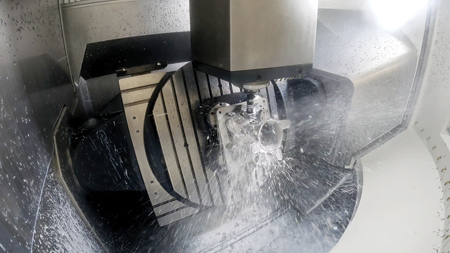
Operation 1 machining the 3D printed steering knuckles on a DMG MORI monoBLOCK 85
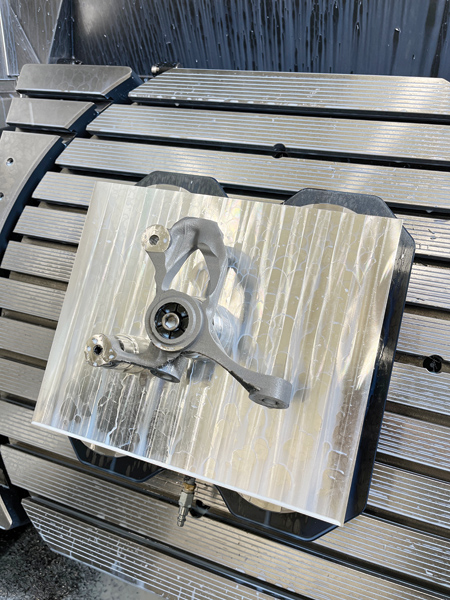
Operation 2 machining of the steering knuckle on a DMG MORI monoBLOCK 85
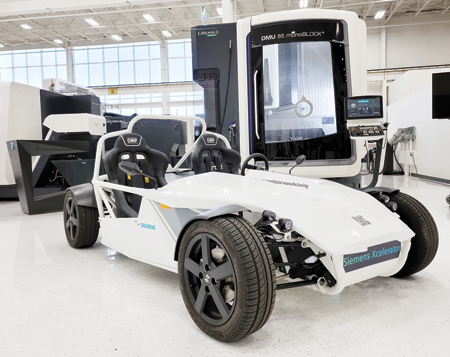
Siemens eRod EV equipped with the lightweighted steering knuckle
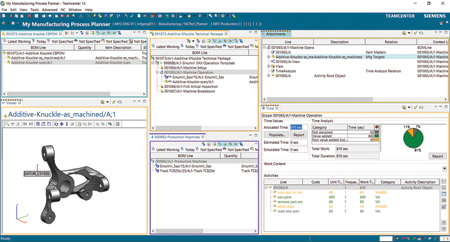
Teamcenter Manufacturing is used to define the complete manufacturing plan
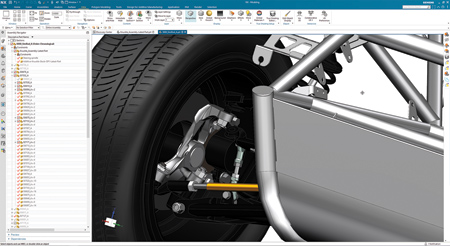
Topology optimized steering knuckle assembly installed on the eRod
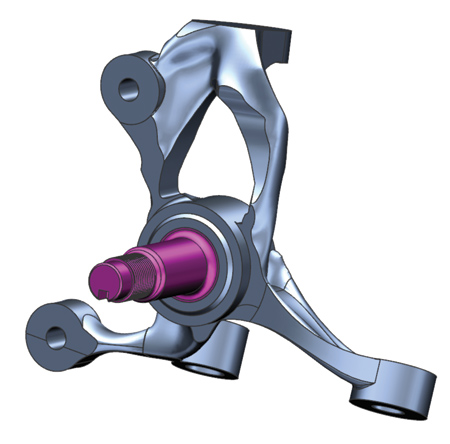
Topology optimized steering knuckle
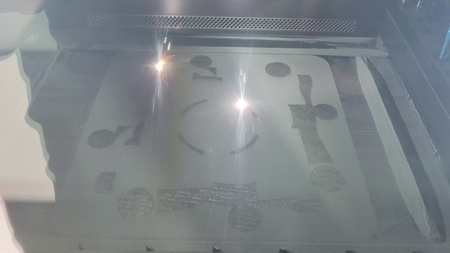
3D printing the steering knuckles on a DMG MORI LASERTEC 30 DUAL SLM
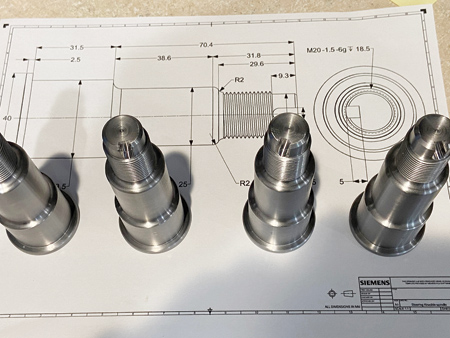
From blueprint to the finished part: Wheel knuckle spindles as machined on the TRAK TC820si equipped with the SINUMERIK ONE control platform from Siemens
Siemens, together with DMG MORI USA, Walter and TRAK Machine Tools, recently unveiled the latest collaboration between four industry leaders in the world of software, machine tool building, tooling hardware and machine tool CNC automation. The project demonstrates the power of the Siemens Xcelerator business platform that includes a partner ecosystem in designing and manufacturing next generation EV components.
"The potential for integrating optimization as a fundamental part of the design and engineering workflow, when considered alongside the power of additive combined with traditional manufacturing, is enormous," said a spokesperson. "We are at a convergence point with these technologies, and it is only through projects like this that we can prove out, validate and embrace that potential-whether from the perspective of reducing waste and maximizing resource utilization during design or as a way to reduce mass and energy consumption during use."
The new digital thread leverages technologies from all four companies, beginning with Siemens NX software to generate the initial design, taking operating parameters of an electric vehicle and using them to drive the development of an optimal part design for a critical suspension component with integrated generative engineering tools like design space exploration. During the Design for Additive Manufacturing phase, the part concept is fully validated using structural simulation technologies and optimization is performed to not only ensure that its performance requirements are met, but also to optimize the manufacturing processes available to produce it. In this project, simulation-driven design ensures that the optimal part is created with a minimal amount of material, resulting in an innovative steering knuckle design that reduces weight by 45% and improves performance so that it can better handle stresses.
The next phase, Process Planning, demonstrates how comprehensive manufacturing plans are developed with Teamcenter software and Opcenter software. This helps manufacturers automate programming by applying their own standard CNC programming, inspection path methods, tools and program templates and ensures that correct revisions of parts are programmed and measured on the shop floor, creating a single source of data for the entire digital manufacturing process.
The manufacturing phases show how the Siemens eRod component is manufactured using a combination of additive and traditional manufacturing methods then finished to achieve the necessary dimensional accuracy and tolerances while reducing the programming time by 60% with automation of routine tasks.
Advanced capabilities in NX CAM, such as 5-axis simultaneous programming, cloud-based post-processing and integrated simulation, help prepare the part for both additive manufacturing (AM) using Ti6Al4V powder on a DMG MORI LASERTEC 30 DUAL SLM Selective Laser Melting machine, and finishing using a DMU 85 monoBLOCK 5-axis machining center by DMG MORI equipped with the SINUMERIK 840D sl CNC system for a two-step machining process. As a provider of additive and subtractive technology, DMG MORI can provide customers with solutions for next-generation, hybrid process chains that improve cycle times, reduce waste and allow customers to completely re-imagine part design.
Walter's tooling hardware will be used for the finishing and cut-off operations to ensure the required tolerances are met. Walter is uniquely prepared to address new machining challenges such as the light-weighted component featured in this digital manufacturing example. Machining of AM titanium presents challenges beyond the usual ones encountered in machining titanium components. The advantages of additive for generating complex components are clear, but the finish machining of those components is often not as straightforward as might be expected. This is where the solutions expertise of Walter combined with advanced precision tools designed for titanium provide the opportunity for unique solutions. Among the challenges addressed in the machining solution developed for the component are 3D printed Ti6Al4V stock material, removing support structures that tend to be more brittle than the bulk material, difficult to access features and minimizing vibration during machining where clamping for the component is weak due to the complex geometry.
By working together with DMG MORI and Siemens, Walter developed an efficient machining process that uses a combination of tools to address all the challenges and provide a finished component that meets all dimensional accuracy and surface finish requirements.
When evaluating the entire assembly, the design team determined that certain components could still be manufactured more efficiently with traditional subtractive processes. Specifically, the spindle, designed in NX, lends itself to a traditional turning process; however, by utilizing Run MyVirtual Machine, the digital twin of the CNC control, it was possible to add a TRAK Machine Tools TC820si turning center in the overall digital manufacturing process. The spindle was virtually programmed in the SINUMERIK ONE control utilizing ShopTurn conversational programming and validated with the TC820si's 3D twin.
To close the loop, Quality Control and Production Preparation is carried out using automated CMM processes driven by dimension and tolerance data captured and stored using Product Manufacturing Information (PMI) and leveraged within NX CMM Inspection Programming software to ensure that the part is within the tolerances expected and ready for assembly. During final assembly, the more traditional spindle component is married to the newly optimized knuckle and installed on the Siemens eRod.
For more information contact:
John Meyer
Marketing Communications Manager
Siemens Industry, Inc.
john.meyer@siemens.com
usa.siemens.com
DMG MORI - Americas Headquarters
2400 Huntington Blvd.
Hoffman Estates, IL 60192
847-593-5400
Service Hotline:
855-DMG-MORI (364-6674)
us.dmgmori.com
Walter USA LLC
1510 S Batesville Rd.
Greer, SC 29650
800-945-5554
www.walter-tools.com/us
TRAK Machine Tools
2615 Homestead Place
Rancho Dominguez, CA 90220
800-421-6875 / 310-608-4422
www.trakmt.com