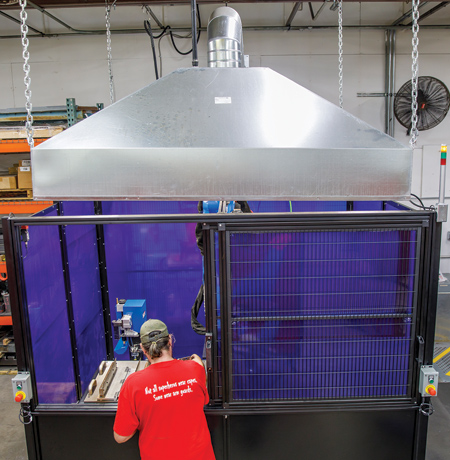
The Yaskawa ArcWorld LC enables quick and easy installation for optimal productivity.
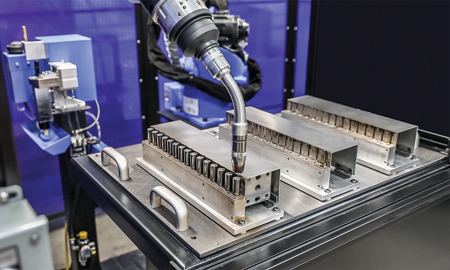
Upgrading welding operations with a robotic workcell positioned Ajax Metal Forming of Minneapolis to fulfill a broader spectrum of welding assignments with greater weld quality and efficient production. Here, a preloaded fixture is ready for the operator to start a welding cycle using the remote teach pendant.
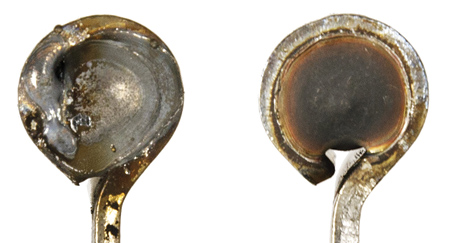
The hinge on the left was welded manually. The hinge on the right was welded in the new Ajax workcell. Note the absence of spatter on the workcell version, due to the pulse capability that delivers just the right amount of power to complete a perfect weld.
When the Ajax process improvement team sought more quality, efficiency and safety for their welding operations, they turned to Yaskawa Motoman and Mechatronic Solutions for a turn-key robotic workcell.
Ajax produces tight-tolerance metal parts for leading OEMs and their suppliers across many industries, including HVAC-R, transportation, auxiliary power, medical, architecture, commercial building products and consumer durable goods. Founded in Minneapolis in 1945 by machinist and inventor Erick Julius Ajax, the company forms parts from carbon and stainless steel, aluminum, brass, bronze, copper and alloys at plants in Minneapolis, MN, and Wilson, NC. Ajax became a member of the Heartland Equity Partners family of companies in 2017.
Succeeding in a demanding, capital-intensive industry like metalforming requires a dedication to continuous improvement. Committed to keeping costs low for Ajax customers, Process Improvement Engineer Antoniy Petkov consistently looks for ways to optimize production. Mindful of a manual process for an OEM customer in their welding operations that would benefit from automation, Petkov examined the process and recommended the implementation of a robotic welding solution for 2-1/2" x 2-3/4" steel lift-off hinges. Among the system requirements would be streamlined set-up and onboarding, OSHA-compliant safeguarding and the flexibility to meet current and future welding needs.
Flexible, Turn-Key Solution
Given the green light to find the ideal solution, Petkov performed a thorough search, engaging with Mechatronic Solutions of Maple Grove, MN. An automation systems integrator and Yaskawa Motoman Strategic Automation Partner, the Mechatronic team listened carefully to Ajax requirements and conducted an on-site assessment at the company's Minneapolis plant. They returned with a recommendation to install Yaskawa's pre-engineered, pre-assembled ArcWorld solution, which met the project requirements perfectly. Yaskawa's OSHA-compliant Functional Safety Unit (FSU) was a strong selling point, as was Yaskawa's long experience as a robotics solution provider to select automobile manufacturers.
Ajax decided on the dual-workstation ArcWorld LC (Lite Cell) workcell with a single high-speed AR1440 arc welding robot coupled to a Miller Auto-Continuum 350 power source. Suited for small-to medium-part welding for low-mix settings, this cost-effective configuration features a fixed tooling table in each workstation divided by a partition. This layout enables Ajax operators to safely prep one side of the workcell while the robot operates in the other, optimizing efficiency.
"With this workcell, both tooling and end effectors can be changed quickly and easily, which is a huge time saver," said Petkov. "The two workstations can be individually tooled to weld different parts or used for sequential operations. That flexibility helps us accommodate more customers and projects."
To begin a welding cycle, a single trained operator manually preloads parts into a custom fixture designed and produced by the Ajax in-house tooling team. Interlocking, sliding access doors with full-coverage safety screens protect the operator from exposure to live welding. Once the parts are placed in the fixture, the workstation access door is secured, and the operator activates the robot via a remote teach pendant. The operator can then preload the other side of the workcell. When a welding cycle completes, the operator carefully offloads welded parts, and the process repeats.
Workcell safety features include an overhead aluminum fume extraction hood, powerful LED lighting and a large emergency stop button within easy reach. Mandatory operator personal protective equipment (PPE) provided by the company includes safety eyewear, ear plugs, cut gloves and full-length arm guards.
As with all machinery and equipment at Ajax, thorough operator training is required to achieve production goals and prevent a work stoppage. Slated to run multiple shifts, six Ajax operators took part in a two-day training course at Mechatronic's teaching facility. Professional-level teaching and testing keep the learning curve as short as possible and prepares operators to be productive from day one. Robot operation was also added to the Ajax skills matrix, the framework that tracks workforce learning and achievement.
Fast, Tangible Results
Since the workcell's implementation in the summer of 2022, Ajax has logged a substantial increase in productivity while generating far less scrap. The dual workstation set-up reduces cycle time and produces consistently clean, precise welds. The pulse capability of the Miller Auto-Continuum enables instant power adjustments that optimize weld tacks and virtually eliminate spatter and subsequent grinding. As a result, operators spend more time on workflow efficiency, quality assurance, count accuracy and all the little things that have compelled customers to stick with Ajax for decades.
The Ajax workcell currently runs two shifts per day, four days a week, operating 10 hours per shift. However, as welding jobs increase, the workcell is anticipated to run a third shift, potentially accelerating the company's initial 23-month payback target.
Offline Programming and Continuous Improvement
As the Ajax Lead Robot Programmer, Petkov relies on Yaskawa's MotoSim offline Windows PC programming to get the most from the new workcell. MotoSim enables high-detail simulation of robot operation and provides an extensive model library and built-in functions that facilitate safe, timely and cost-effective offline robot job creation. This platform will help the company build programming proficiency and establish a knowledge base that can squeeze maximum benefit from this workcell and any future Yaskawa implementations.
The ArcWorld LC robotic welding workcell provides Ajax with a level of welding efficiency, quality and safety far beyond that of even the most proficient manual welder. Combined with professional operator training, the company's in-house fixture production and Yaskawa's offline programming, Ajax now has complete, flexible and customer-centric automated welding capability. As a result, the company can add new welding customers and projects without interrupting service for established customers.
This new welding capability could not come at a better time. As a growing ISO 9001:2015 company, Ajax has faced the challenge of developing a workforce large enough to meet increasing customer demand. This new workcell enabled skilled Ajax welders to be reassigned to other essential functions. Meanwhile, a select pool of newer workforce members completed the workcell training and testing course.
"Investing in people has always been an Ajax priority," said Petkov. "We will continue on that path, but now is the time to adopt more plant automation. The benefits of industrial robotics are just too attractive to pass up."
For more information contact:
Ajax Metal Forming Solutions
7773 Ranchers Road
Minneapolis, MN 55432
763-277-7760
www.ajaxmfs.com
Yaskawa America, Inc.
Motoman Robotics Division
100 Automation Way
Miamisburg, OH 45342
937-847-6200
www.motoman.com