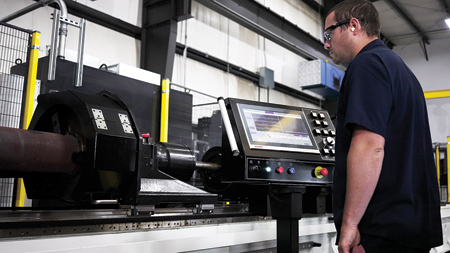
Chris Braby, Senior Team Leader at Midwest, played a large role in design of the new system since he brought the shop floor perspective to the process. "Older drilling systems require a degree of operator expertise, which takes a lot of training," said Braby. "The ease of set-up and programming is important because we are not limited to having just a few qualified operators on staff."
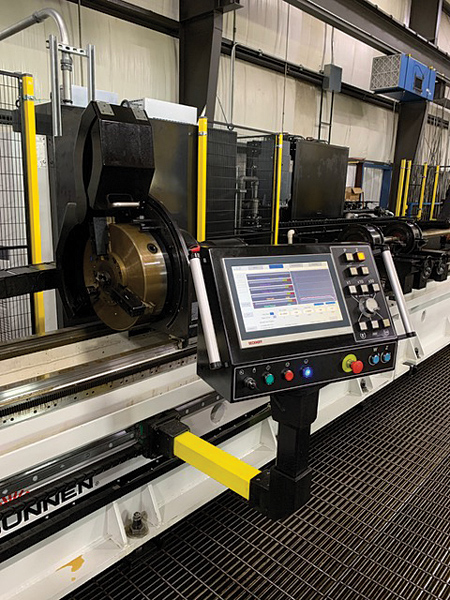
Sunnen consulted with Midwest on all aspects of the new machine design, including servo-driven ball screws for tool feed, heavy-duty linear rails and high capacity coolant system, among others, and also developed an advanced control system to simplify time-consuming machine set-up and training.
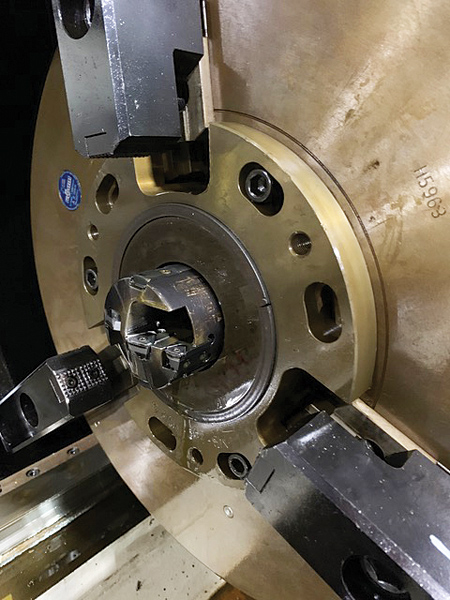
Midwest specializes in tight tolerance drilling services, including deep hole boring, precision gun drilling and precision honing. Typical workpieces have bores with IDs from .062" to 9.5"., some up to 144' in length.
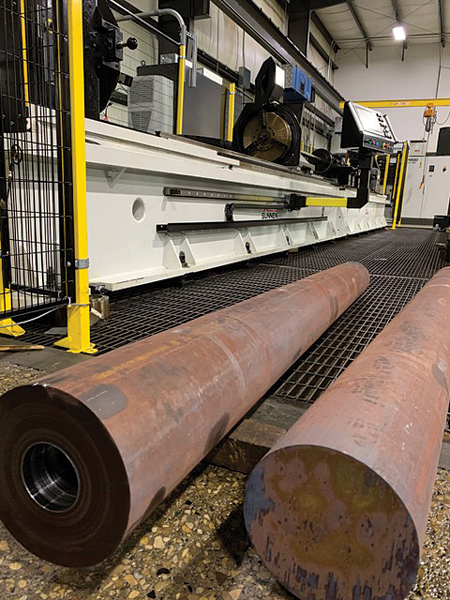
The Sunnen model SHDD-4500 deep hole drill installed at the Midwest facility produces straight, tight-tolerance parts on a variety of materials.
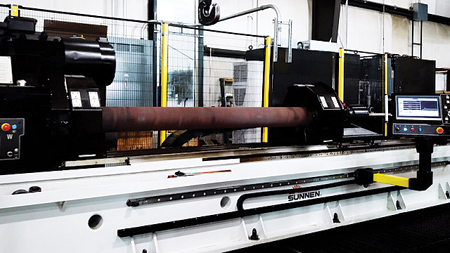
With a reputation for quick delivery times-and the word "precision" in its name-Midwest Precision has a lot to live up to when it comes to deep hole drilling. The Fredonia, WI-based company has specialized in tight-tolerance deep hole bores for almost 30 years, but it was with an eye to the future that Midwest partnered with Sunnen Products Company to develop the next generation of deep hole drilling systems.
The collaboration, with upfront voice-of-the-customer design input from the team at Midwest, led to a deep hole boring solution that is versatile, efficient and reliable, producing parts that are straighter and more accurate than the shop's older drilling machines. The new Sunnen model SHDD-4500 deep hole drill installed at the Midwest facility produces straight, tight-tolerance parts on a variety of materials, allowing Midwest to meet turnaround times and keep a variety of parts moving through the shop. The biggest advantage, however, is the ease of programming and operating the system, so operators are able to turn out precision parts with minimal training.
Midwest was started by Bob Bublitz in what was basically a garage located in Fredonia back in 1993. Beginning with a single gun drill producing parts for regional customers, Midwest has grown to 30,000 sq. ft. of floor space and 24 employees. The company specializes in tight tolerance drilling services, including deep hole boring, precision gun drilling and precision honing. Typical workpieces have bores with IDs from .062" to 9.5", some up to 144' in length. The shop has a number of older deep hole drills that handled the bulk of its long cylinder work, but they wanted a system that was easier to program and operate. With two Sunnen hones already in the shop, the two companies were familiar with each other. And, in a case of good timing, Sunnen was developing a new deep hole drilling system, having acquired deep hole tooling company BTA Heller in 2018.
"We were looking to add a more reliable, consistent drilling machine, and Sunnen approached us with the opportunity to share in the design of an all-new system," said Jason Bublitz, Operations Manager at Midwest Precision. "From a business perspective, our challenge is maintaining a steady workflow. We are a contract shop for a lot of different industries, so machine downtime has a big impact on overall operations and our ability to meet delivery times."
The Sunnen team consulted with Midwest on all aspects of the new machine design, including servo-driven ball screws for tool feed, heavy-duty linear rails and high capacity coolant system, among others, and also developed an advanced control system to simplify time-consuming machine set-up and training. The intuitive control makes part programming easy, and connectivity with Sunnen allows the team at Midwest to keep production moving.
"The advantage of getting real-time assistance remotely, to diagnose an issue or help produce a new part, is a great benefit," said Bublitz. "We were able to sustain business through the COVID-19 months due to our versatility to produce parts for a variety of markets and deliver them on time."
For Tom Huiras, General Manager of Midwest Precision, the reliability of the new drilling system goes deeper than smooth daily operations-it also protects the company's reputation. "We built this business on our ability to turn parts around quickly, sometimes in less than a week, and our customers depend on us to meet their deadlines," said Huiras, a machine drilling veteran who started at Midwest as a machinist and is now a part-owner. "The machine must be running and producing parts to spec or we are not delivering on our reputation. The speeds and feeds of this new drilling system, as well as the accuracy, make it an integral part of our operations. We put mostly Inconel, titanium, 4140 and 8620 alloys through it, and we achieve the precision demanded by our customers in the time they expect. That means we are pushing speeds and feeds, but it is accurate at any hole size. We used to easily tell which end of the part was the entrance and which was the exit, but with the new machine we cannot tell the difference."
Chris Braby, Senior Team Leader at Midwest, played a large role in the design of the new system since he brought the shop floor perspective to the process. "Older drilling systems require a degree of operator expertise, which takes a lot of training," said Braby. "The ease of set-up and programming is important because we are not limited to having just a few qualified operators on staff. We can train a new operator on this system in a matter of hours versus weeks with older systems. The collaboration with Sunnen led to a great design and it continues every time we get a new part challenge."
The Sunnen team welcomed the input from the field. "To paraphrase an old saying, we `walked a mile in their work boots' to create a drilling system that handles high-capacity production and reduces machine set-up and changeover time," said Phil Hanna, Machine Product Manager, Sunnen. "The versatility of a deep hole drilling system that can handle solid drilling up to 5 in., and counterboring or trepanning up to 7 in. diameter, demonstrates our commitment to develop the best deep-hole system on the market."
For more information contact:
Midwest Precision Manufacturing
627 Tower Drive
Fredonia, WI 53021
262-692-9363
office@midwestprecisionmfg.com
www.midwestprecisionmfg.com
Sunnen Products Company
7910 Manchester Road
St. Louis, MO 63143
800-325-3670 / 314-781-2100
sales@sunnen.com
www.sunnen.com