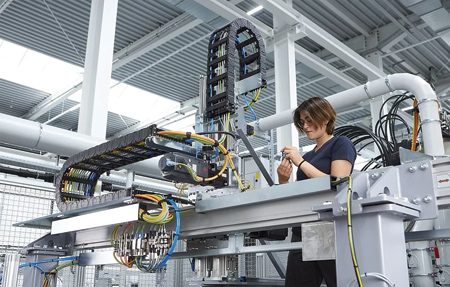
The goal is that all EMAG production solutions work their best and deliver optimum results.
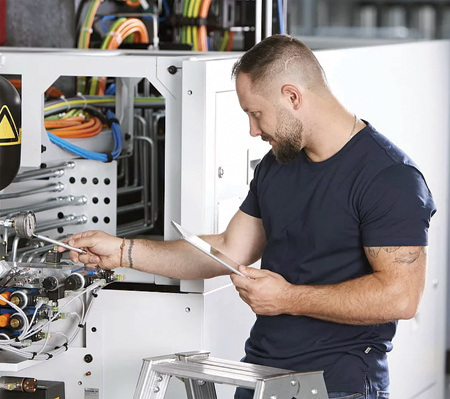
Maintenance is an important element in the life cycle of machines.
The greatest benefit of regular maintenance in industrial production is obvious-unscheduled machine downtimes are systematically avoided, which has a huge economic benefit for users. Take, for example, a turret. Investing a little money in having the key component in the machine tool regularly checked prevents what could end up being serious damage in the five-figure range. Moreover, maintenance generally ensures more efficient production processes with consistent production quality.
The service experts from EMAG estimate that more than half of users do not adhere to regular inspection and maintenance intervals for their machines. Essentially, checks are only carried out when there is no other choice-when a problem with the machine means it stops working. In extreme cases, this means having to purchase an expensive component. Needless to say, a lack of advance planning means this takes longer. In the worst case, this can hold up production for several weeks.
"Time and again, we see cases where major damage could have been avoided, for example by simply replacing a small seal at the right time. But when that is not done, bigger problems occur," said Patrick Theiss, head of the After Sales/Service business unit at EMAG. "We are, therefore, increasingly trying to make our customers aware of the importance of regular maintenance in the life cycle of a machine. There are major economic benefits. Essentially, it is the same as with cars, which also need to be serviced regularly. An ounce of prevention is worth a pound of cure."
The Difference Between Inspection and Maintenance
EMAG makes a distinction between inspection and maintenance. The former is simply a comprehensive check to identify any defects and damage at an early stage. It involves experts for the particular EMAG technology working through a predefined checklist rigorously and quickly. Production is interrupted only briefly. The result is an analysis report that includes a quotation for eliminating any defects. To put it another way, nothing is repaired or replaced during the inspection itself.
In contrast, comprehensive maintenance includes the replacement of wearing parts and is the pinnacle of work in the service department. The entire workflow is planned in great detail as appropriate to the customer's production task.
Theiss noted: "This ultimately affects every detail, such as the scope of the tests and the replacement of maintenance parts. The customer is aware of all the costs and can also change them according to how the maintenance is structured. Users then benefit from EMAG's expertise: the service technicians know 'their' machines-from the travel accuracy and repeatability of the NC axes to the swiveling accuracy of the tool carrier to the ease of movement of the clamping chucks, and the geometry of the entire machine. It is crucial that the service technicians tailor the checklist to the particular machining task, since of course there are different levels of machining forces and vibrations, for example, and the machines are in use for different lengths of time per year. We, therefore, define very precisely which small parts will be replaced after a defined period and offer the option of a maintenance contract."
Analyzing the Machine's State of Health Using AI
The widespread use of data in mechanical engineering is playing an increasingly important role in the context of inspection and maintenance. EMAG has an integrated IoT system called EDNA. The basis of this solution is the EDNA IoT Core, an industrial PC that is connected to the machine's control unit and receives and records production and sensor data using the EDNA Cortex software program. This makes it possible, for example, to measure the machine's state of health using artificial intelligence (AI), producing a result that can be assessed by EMAG experts. In practice, the system delivers substantial cost benefits, as current application examples reveal: many unscheduled downtimes can be identified and waiting times in the service department can be dramatically reduced through the early availability of spare parts and early scheduling of service calls, for example.
Growing Importance of Servicing
"We see our entire service offering as a collaborative process and work together closely with our customers," said Theiss. "Our main priority is that all EMAG production solutions work to their best ability and deliver optimum results. The way to ensure this is by largely avoiding unscheduled downtimes and increasing machine availability-and this is precisely what we ensure with relatively little effort and in close consultation. The latter then also affects, for example, the working times of the EMAG service technicians, who do their work during the customer's scheduled production shutdowns. In addition, bigger teams with different experts working in parallel on various machines can be deployed for large production lines. We are confident that servicing will continue to grow in importance in mechanical engineering in the coming years. Higher requirements on component quality and just-in-time production processes dictate the way ahead. In this context, we could not be better positioned with the services we offer."
Authored by EMAG
For more information contact:
EMAG L.L.C.
38800 Grand River Ave.
Farmington Hills, MI 48335
248-447-7440
info@usa.emag.com
www.emag.com