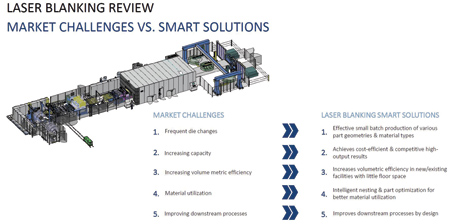
Schuler's Justine Fonteyne explained the various advantages of laser blanking technology in an online seminar.
A blanking line is usually made up of a coil line, an uncoiler, a threading unit, leveler, roll feed, the cutting area and the stacking unit. This holds true with laser blanking lines, but the material is cut by a laser cell instead of a shear or press. Justine Fonteyne, Schuler's Area Sales Manager of the Americas, recently explained the technology's multiple advantages in an online seminar.
"There has been a rising interest for laser blanking lines, given the die-free blanking capabilities. Schuler has sold 15 worldwide, including five in North America. With the frequent changeover of new car models, vehicle manufactures are happy to avoid investing in expensive dies-especially new players within the EV market, for which ramp-up production may be slower. And die change time costs production time," Fonteyne said. "Additionally, no dies equate to no die storage or maintenance, and less initial infrastructure investment as no heavy press foundation or loop pit is required. Apart from that, no noise or vibration is emitted."
Overall Equipment Efficiency of up to 80%
"Because of Schuler's Dynamic Flow Technology (DFT), Schuler's laser blanking lines are also much faster than conventional stop and go laser cutting systems like flatbed lasers," said a spokesperson. "The material runs continuously without the need to stop-and-start before cutting. The output can reach 45 parts per minute, depending on the geometry of the blank. Due to no die changes, the overall equipment efficiency (OEE) is up to 80%."
"Depending on the part mix, laser blanking can be the cheapest way of blanking," Fonteyne stated. "Due to digital nesting solutions, the technology has much greater material utilization." In contrast to conventional lines, the parts can be designed independently from die restrictions. Also, separation strips can be avoided with edge-to-edge nesting. Improvements in material utilization of an outer body part mix of approximately 1% quickly add up to material savings of up to $1 million per year."
No Wear of Dies and Presses
Schuler's laser blanking lines produce homogenous cutting edges with hardly any burr. "This is relevant for aluminum because the flitter in the die is reduced to almost zero," Fonteyne explained. "The rising number of high-strength steel pose further challenges to conventional lines regarding the wear of dies and presses, but the lasers are not affected by this at all. Schuler offers workshops for part simulation and optimization as well as business calculation."
Fonteyne provided insight into Schuler's Track & Trace solution that has already been implemented at the Smart Press Shop in Germany, a joint venture between Schuler and Porsche. "Being the first station for the material in the press shop, we start the tracking of the production data here," said Fonteyne. "The production data is connected to every part and can be tracked easily and continuously. For example, data pertaining to the thickness of a blank or the amount of oil distributed can be transmitted to the press line in order to achieve a perfect forming process."
To view the complete seminar online, go to youtu.be/oC59OzaCW0C.
For more information contact:
Schuler Inc.
7145 Commerce Blvd.
Canton, MI 48187
734-207-7200
info@schulerinc.com
www.schulergroup.com