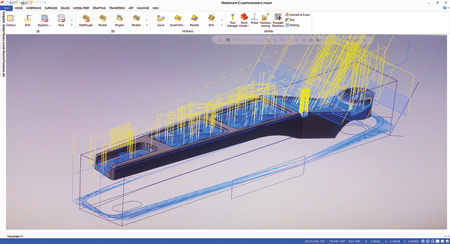
Lowe programs Flowline, Parallel and Equal Scallop toolpaths to machine the swing arm's multiple angles, various pockets and complex geometries.
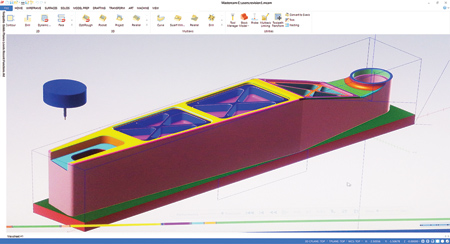
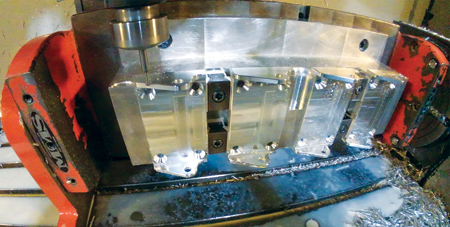
These floor board mounts, made from 6016 aluminum, were run four pieces at a time in one operation on the 4th axis without any operator deburring.
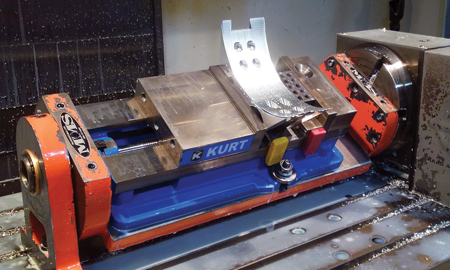
Lowe uses the Dynamic high-speed toolpaths for constant chip loading. Lowe no longer needs to stop and pull the tool out of the material or worry about it getting caught in the chip auger.
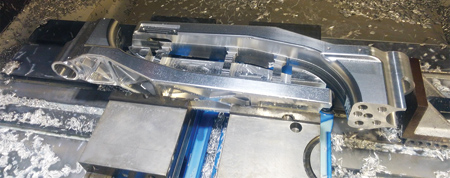
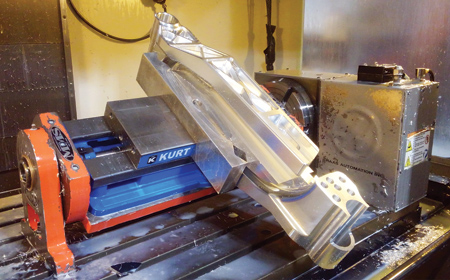
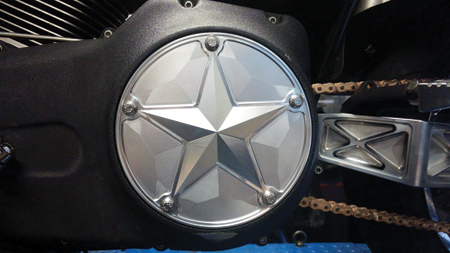
This star logo was machined using 3D surfacing techniques with Equal Scallop toolpaths.
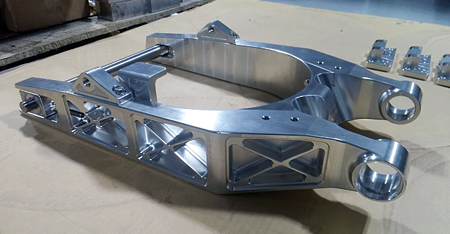
The swing arm is machined out of two or three pieces that are pieced together with pins and bolts like a puzzle. According to Lowe, the machining operation consists of multiple, angles, different pockets, pockets on angles and radiused edges, which must be smooth.
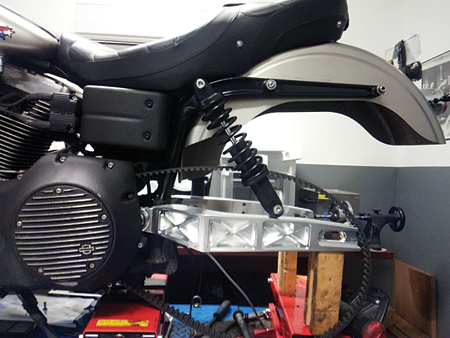
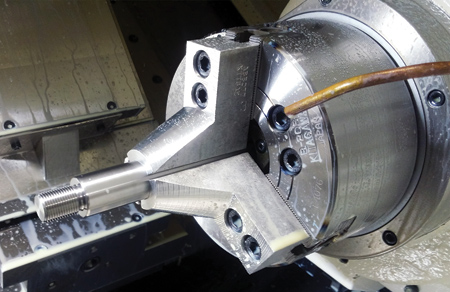
Swing arm axles measuring 25 mm in diameter are machined on the Okuma L300-MYW lathe.
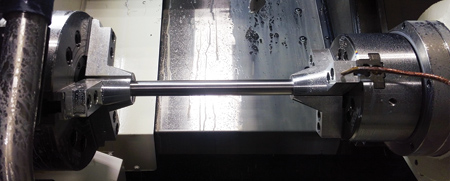
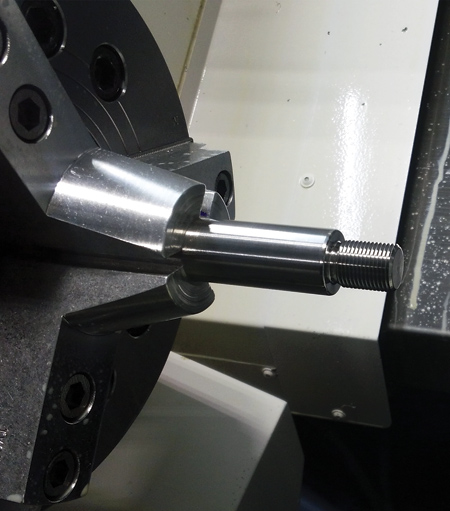
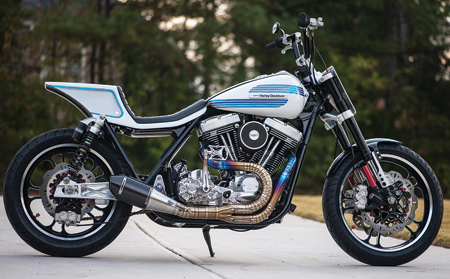
This Harley-Davidson bike features swing arm, foot controls, wheels, brake rotors and rear sprocket machined by Revolution Speed.
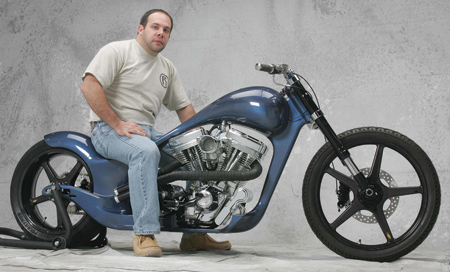
Founder and CEO Michael Kamalian sits astride the CFXr-1 motorcycle featuring lightweight carbon fiber frame and wheels.
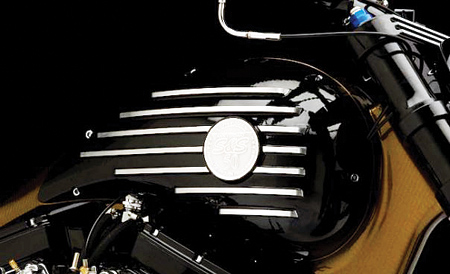
This custom bike was created for S&S Cycle, Inc.'s 50th Anniversary Build-Off Competition. The twin aluminum gas tank halves started as 200-lb. billets each side. It took 16 hours per side to whittle them down to 11 lbs., each side.
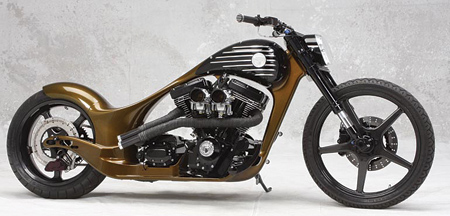
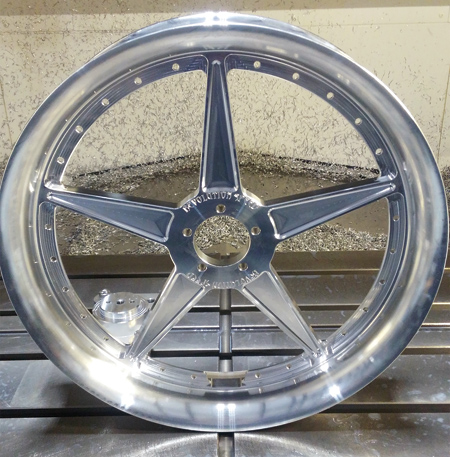
Custom wheels, brake rotors and rear drive sprocket for Harley-Davidson machined using 2D Dynamic Mill and pocket toolpaths.
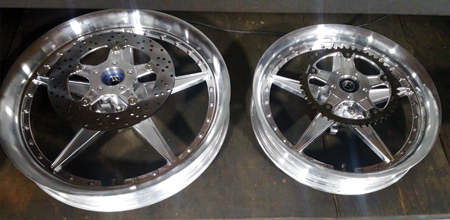
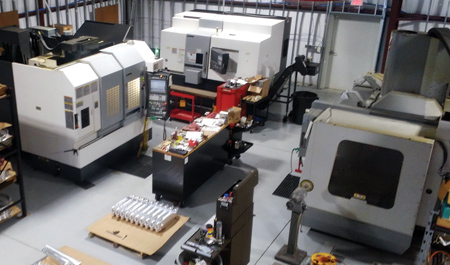
Revolution Speed's 3,500 sq. ft. shop has two vertical mills (one with a 4th axis rotary table) and a twin-spindle bar-fed lathe.
Michael Kamalian started out like any other motorcycle enthusiast, but when his love of bikes turned into a growing business, he started gaining attention from major motorcycle designers, magazines and even television shows. Revolution Speed, located in Marietta, GA, can create anything from a dream bike to a simply customized daily driver. The company likes to state: "If you can think it, we can make it."
Revolution Speed's 3,500 sq. ft. machine shop is prepared to handle any project, from designing and constructing front-running custom motorcycles to creating aftermarket parts from the ground up. Starting out in the mid-1990s primarily as a motorcycle manufacturer, in 2008 Kamalian decided to start making his own motorcycle parts rather than buying them from other companies. That is when he brought in lead machinist Justin Lowe, bought his first CNC machine and began developing a part line for the Harley-Davidson brand.
They machined parts that were designed for themselves, parts other manufacturers designed and even parts they designed for other companies. "We also started making a lot of custom parts for our own bikes around this time, which means we were making everything imaginable on a motorcycle," said Lowe.
More and more manufacturers started approaching the company to make part lines for their brands as well. "So, we started making these parts over the years and became a Tier 1 manufacturer for Polaris making parts for Victory Motorcycles," Lowe said. "These included floorboards, foot pegs, grips and cosmetic covers-all out of machined aluminum."
When Lowe joined the company, he was thrilled to have an opportunity to break into the motorcycle industry. He is currently the only programmer and machinist, but his experience with Mastercam CAD/CAM software (CNC Software, Inc., Tolland, CT) made him an asset since he had been working with the software since Mastercam Version 7. Revolution Manufacturing has one seat of Mastercam Lathe and three CNC machines: two vertical mills, one with a 4th-axis rotary. It also has a twin-spindle Y-axis bar-fed lathe.
While they consider themselves a smaller shop, Lowe keeps things moving quickly by running both mills at the same time so that they can move the parts out faster and get on to the next project. For them, high productivity is critical. "For example, when we are making floorboards, I will be running the attachment bracket in the 4-axis machine so it can create the multiple sides, while the other 3-axis mill is running the boards," said Lowe.
Whether they are running a prototype for a custom bike or a large order for a specific part, Lowe enjoys using the software because it gives him the visualizations he needs. "I like being able to run the visualization through Verify and see the actual part being cut and making sure there are no bad toolpaths," he said. "Being able to verify my toolpaths before I put something in the machine is one of my favorite features."
This was crucial for one project where the customer brought in a CAD file and Lowe was able to use Mastercam to provide them with nice, symmetrical pockets. The customer was able to receive a product better than what they had originally anticipated.
Optimizing time is important to the shop as well. Lowe will run the machines during the day, but he has built up his tool library enough so that he can do his programming at home. Spending time setting up this library accurately so that tools stay in the machine all the time has paid off by giving him maximum productivity. He also takes advantage of the software's compatibility with SOLIDWORKS in terms of being able to easily pull a drawing into the program.
Another benefit of using the software comes from the toolpaths available. "I know that it helps with the tool wear by being able to use more of the flute and distributing that pressure on the tool over a larger area rather than just focusing it down the last quarter inch of the end mill," said Lowe.
For example, if he uses a Surface Rough Pocket toolpath, Lowe can start at the bottom and work his way up so that he maximizes the flute length rather than stepping down. He says that provides a benefit of a shorter run time as well. To continue maximizing time, they are also able to run their machines at 12,000 RPM to 15,000 RPM to achieve 200 IPM to 500 IPM in aluminum with a 20% to 40% stepover.
"On secondary operations, where normally I would be taking just a quarter inch of material held onto the first side, I will turn my stepover up to around 80%, double my feedrate and turn it all into chips rather than just doing a profile around it and having to pick out my material as solid pieces. Sometimes that material will find its way to the tool probe and snap it off and then you have half a day's worth of work getting all that stuff back together."
Lowe never stops looking for ways to maximize time. He even takes old parts and looks for newer ways to speed up their production. For example, he will take the time to find new ways to reprogram their parts and can take a 17-minute tool cycle time down to seven minutes based on how the tools are doing with the material. "It is kind of amazing the time savings that you can get when you start optimizing certain things," he said.
Lowe has also been able to push one of his VMCs to its fullest potential by implementing Dynamic Motion technology. Dynamic Motion, or Dynamic Milling, uses proprietary algorithms programmed into the software to keep the tool constantly engaged with the material, allowing it to cut intricate geometries at higher speeds. "As we started doing the Dynamic toolpaths, the smaller vertical mill started catching up to the bigger machine a bit," recalled Lowe. "In fact, in some things, I feel it works better with the high-speed toolpaths than the others on certain pieces. We have been able to do a lot more jobs on this machine because I can get the cycle times down to where I need them to be." According to Lowe, the machine peels off much more material, eliminating the need to step speeds down incrementally. "It has helped make a machine that had almost become obsolete for us come back into being useful," he said.
While the software helps with productivity, it has also proven useful for specific job applications as well. Over the years, multiple customers have asked for a swing arm, which is the rear suspension piece on a motorcycle. It is machined out of two or three pieces where everything bolts together like a puzzle with pins and bolts. The machining for this part entails multiple angles, different pockets, pockets on angles and radiused edges, which all must be smooth.
"For this 6061 aluminum piece I use the Parallel toolpath to get a nice cosmetic surface," Lowe said. "I have about nine operations where we are doing different angles. I nest the two halves together and machine them out and then cut them apart on the band saw once they are almost finished. I use both Flowline and Parallel toolpaths for these operations. I have also used a lot of the high-speed Dynamic toolpaths for roughing."
They started with a 70 lb. block of aluminum, whittling it down to about 11 lbs. "With these parts, I used to program a ramp toolpath and have a chunk of aluminum to pull it out, leaving a portion of it solid so I was not turning it all into chips," said Lowe. "Now, I have gotten to where I use the high-speed toolpaths to turn it all into chips, so I do not have to stop and pull the tool out or worry about it getting caught in the chip auger."
Even though machining has come a long way, Lowe still remembers the long-hand G-code programming before Mastercam came along. Over the years he has been more self-taught than anything else. "I enjoy working on the programs in my spare time and learning how to use features to make my life easier," he said. "When the machines are running, I am in here trying to program the next operation."
Lowe added that he can put the programming in the machine and never worry about any crashes or problems. He said there has been a marked difference in the reliability of the software over the years. "It is a software that I have been using for a really long time, so I have gotten to see different aspects of it. I am always learning new tips and new tricks," he said.
When he does need any assistance, Lowe reaches out to Brian Kadow, Senior Application Engineer at Mastercam Reseller CAD/CAM Solutions, Inc. (Snellville, GA). As the software becomes more advanced and the parts get more complicated, he knows he can turn to them for help at any time. Lowe has taken advantage of everything from their training classes to their tech support. "I will email Brian and he will get right on it and get me sorted out," said Lowe. "I have known them for a very long time and have a personal relationship as well as professional relationship, which is great. They are always very helpful with whatever we need."
Lowe is confident that using Mastercam has helped the productivity of their business over the years. He said, "I do not know what I would do if I did not have good software to get these parts pushed out in a reasonable time."
Lowe said he can run his machines faster than many other shops, so he is already starting out with an advantage over competitors. By adding the software to the operation, he can optimize the entire project. "As far as the software, it is really the cornerstone of being able to be productive," he said.
For more information contact:
Revolution Manufacturing
1435 Asberry Drive
Marietta, GA 30066
770-420-9191
info@revolutionspeed.com
www.revolutionspeed.com
CNC Software, Inc.
671 Old Post Road
Tolland, CT 06084
800-228-2877
info@mastercam.com
www.mastercam.com