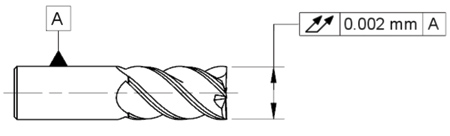
TIR is defined as the difference between the maximum and minimum values measured across an entire rotating surface about a reference axis. Manufacturing high quality, high performance tools requires the TIR to be perfect or minimal for overall tool life and surface finish.
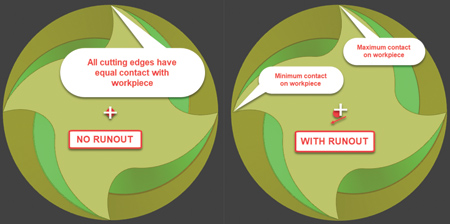
Runout creates uneven chip loads due to uneven contact on the workpiece. The result is that some flutes get too much load and wear fast while others get too little.
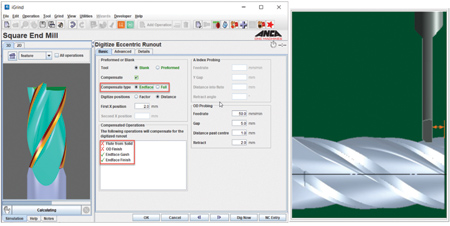
Axial runout compensation
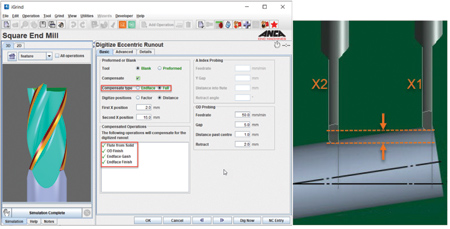
Total runout compensation
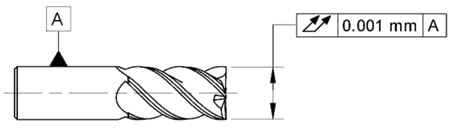
All length values in above chart are in mm.
Total indicator runout (TIR) is a term often used in manufacturing, especially when dealing with rotating parts such as cutting tools, particularly endmills and drills. TIR is defined as the difference between the maximum and minimum values measured across an entire rotating surface about a reference axis.
Manufacturing high quality, high performance tools requires the TIR to be perfect or minimal for overall tool life and surface finish. Runout on blanks before grinding can be achieved by either spending a certain amount of time for workholding set-up or alternatively, compensating the runout in software. The latest software update of ToolRoom has an option to apply complete tool runout compensation when needed.
Runout creates uneven chip loads due to uneven contact on the workpiece. The result is that some flutes get too much load and wear fast while others get too little. This is not an optimal situation for endmills during machining. Not only do tools with runout have shorter tool life, but they tend to be unbalanced and more prone to breaking. Additionally, they vibrate and cause chatter, increase spindle load and result in a bad surface finish on the workpiece.
On the contrary, even cutting flutes result in longer tool life, better surface finish and accurate finished parts.
Circular runout controls only a particular circular cross section of an endmill, while total runout controls the entire surface of the endmill, which includes the outer diameter and endface. There are two kinds of runout: radial and axial. Radial runout is when the axis of rotation is off-center from the main axis, but still parallel. Axial runout is when the axis of rotation is tilted to some degree from the main axis, meaning the axis of rotation is no longer parallel to the main axis.
On an ANCA tool and cutter grinder, runout is measured by rotating the blank around the A-axis (headstock) and using the Renishaw touch probe. The latest update in the ToolRoom RN34.1 release contains the total tool runout measurement and compensation operation in iGrind as an option. This is an addition to the existing axial runout compensation.
The runout measurement and compensation can be performed on a blank or a pre-formed blank. A preformed blank is a tool that has flutes ground, for example tools requiring resharpening. Endface compensation is used for axial runout by digitizing a single point close to the end of the tool. Only the endface operations are supported for this type of compensation.
Total runout or full compensation will measure and compensate radial and axial runout. This is mainly used while manufacturing and two points are digitized. One is near the end of the tool and the other is at the shank end. With the digitizing results, users are able to convert the grinding to the centerline of the blank rather than the centerline of the A-axis.
When an endmill is in rotation it is important that each tooth cuts at the exact same spot along the workpiece for longer tool life and efficient cutting. Every tool in the batch can be measured and compensated for runout to ensure the entire batch is within tolerances.
Runout in drills and reamers will result in oversized holes. This can be avoided by using runout compensation.
It is important to note that accuracy starts with the quality of the blank. Contrary to popular belief, carbide blanks can be out of round, bent or tapered. Ensure that the blanks are checked for size and accuracy, cleaned and chamfered at insertion end.
Manufacturing challenges due to runout is a persistent pain point for many precision tool manufacturers. This new feature addresses this problem and is intended to give users the assurance they need to manufacture high quality tools-ensuring that the hundredth endmill produced will be equally as good as the first.
The complete tool runout measurement and compensation operation is now available as an option in the latest ToolRoom update for RN34.1 release. Customers will benefit from increase in productivity due to the reduced collet and collet adaptor set-up time, and reduced scrap from zero rejections due to runout.
Authored by ANCA Inc.
For more information contact:
ANCA Inc.
31129 Century Drive
Wixom, MI 48393
248-926-4466
usainfo@anca.com
www.anca.com