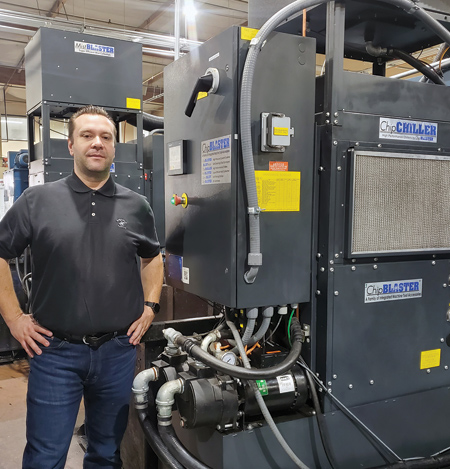
Delta Machine Company, LLC President Janos Garaczi credits
continuous improvement of his manufacturing processes for Delta
Machine’s 100% growth since he acquired the company in 2016.
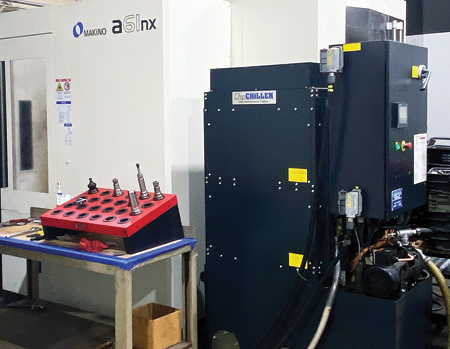
Chillers are used in conjunction with variable high-pressure systems to maintain cutting zone temperatures of 68 °F to 70 °F.
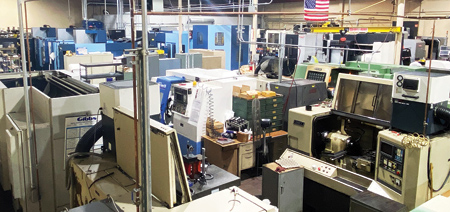
Adding LNS Chipblaster variable high-pressure systems throughout the factory enables Delta Machine to improve tool life by 40% and reduce cutting and drilling times.
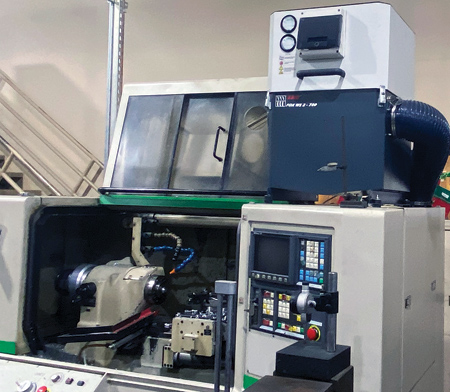
Delta Machine uses LNS Fox WS2 Oil/Mist Collectors to remove up to 99.97% of cutting mist and keep the workplace safe and healthy.
Delta Machine Company, LLC President Janos Garaczi loves what he does. As owner of the 25,000 sq. ft. precision CNC machine shop in Huntington Beach, CA, he is passionate about manufacturing and continually making his processes more productive and cost-effective.
Established in 1980, Delta Machine was a well-respected CNC shop when Garaczi joined the company in 2011. Having practiced computer programming from age eight, he quickly found his niche programming CNC machines to refine part production for greater efficiencies. In 2016, he bought the company and replaced the aging machine tools with a high-performance 12-pallet automated HMC cell with 240 tools, as well as automated 5-axis VMCs. As the business rapidly grew, he added more HMCs and 5-axis machines with robotic unloaders to support 24/7, lights-out manufacturing.
"In the kind of work we do, things that do not seem important to some people can make a huge difference in performance and profits," said Garaczi. "When I started in the business, I recognized that faster spindle speeds and smart programs were not enough when the goal is to make precision parts better, faster and more profitable. This is especially true in our case since we are cutting titanium and other exotic materials for aerospace and military applications. That is why I ordered high-pressure coolant systems with coolant chillers for all our new machines. Unfortunately, the HP units we originally received were not capable of maintaining the cutting zone temperatures in the 68 °F to 70 °F range we required. We run our machines fast and hard, and the temperatures very quickly spiked to 100 °F. As a result, we had excessive tool wear that led to higher tooling costs."
To remedy the situation, Garaczi did his research and upgraded to LNS Chipblaster JV-40 variable high-pressure systems. "The Chipblaster high-pressure coolant delivery units and chillers maintain consistent temperatures very reliably throughout the machining processes," he said. "This is true even in the summer when ambient temperatures here are in the 90s. We run our CNC machines hard, often 24/7. When you run lights-out, you need every piece of equipment to work trouble-free. The Chipblaster does that for us."
At one time, much of Delta's business included making parts for the 737 Max. When Boeing's software and training problems halted production, Delta concentrated on making parts for military applications, such as F-35 fighter jet and drone components. The company also produces over 500,000 automotive parts per year. All work is high-precision, holding tolerances of ±.0001" in diameters, .0002" concentricity and .0005 total indicated run-out (TIR). In addition to machining titanium, Inconel and other challenging materials, Delta makes complex aluminum parts on its 5-axis machine tool.
A typical application for high-pressure coolant delivery at Delta is through-hole drilling. The company also employs custom designed collets and toolholders with built-in nozzles to precisely apply high-pressure coolant for all titanium and 13-8 steel cutting operations.
"We are all about productivity," said Garaczi. "With the high-pressure systems, we do not have issues with recutting chips, because the coolant stream blasts them out of the way. Along with controlling temperature and flow, the Chipblasters give us 40% or greater tool life, which saves us tens of thousands of dollars each year. We can also cut titanium 30% to 40% faster and drill 10x faster. It all adds up to bottom-line profit."
Because Garaczi pushes his CNC machines to the limit, leading tool manufacturers often ask him to help test their new tools, thus providing real-world performance data. With his proprietary techniques and the benefit of Chipblaster high-pressure systems, the tool makers typically find that, on titanium and other difficult to machine metals, Delta machines run faster with better tool life than the manufacturers can achieve in their own testing labs.
"We look at every aspect of production and run tests to learn what works best," said Garaczi. "For example, we evaluated various brands of coolant, and found that changing coolant sources, alone, improved tool life by another 40%."
Garaczi continued, "When you run continuously and lights-out, you cannot afford to have any weak links in your process. That is why we are just as thorough when investing in the peripherals we use as we are in selecting CNC machines. When our original high-pressure systems failed to maintain proper temperatures, the maker gave us no support. The Chipblaster people worked closely with us to meet our needs in the beginning, and continue to support us today."
Delta also has LNS oil/mist collectors that keep the workplace safe and healthy for its machine operators, and MH Series filtering chip conveyors to ensure trouble-free, lights-out production by eliminating chip backups and continuously cleaning coolant.
"We find that filtering chip conveyors keep the coolant cleaner, so it lasts longer," said Garaczi. "Another thing we like about these units is that we can change the filtering boxes to adjust to our process. When we first got the MH chip conveyors, we learned that we needed a different level of filtration. Fortunately, we can change the filter boxes right on the factory floor."
By constantly refining their processes and optimizing the performance of their CNC machines with Chipblaster high-pressure systems and other LNS peripherals, Delta Machine has experienced 100% growth since Garaczi acquired the company in 2016. “We run our machines hard and fast, and we try to be smart in everything we do,” Garaczi concluded.
For more information contact:
Janos Garaczi, President
Delta Machine Co. LLC
5341 Argosy Ave.
Huntington Beach CA 92649
310-323-8207
janos@deltamachineco.com
www.deltamachineco.com
LNS North America, Inc.
4621 East Tech Drive
Cincinnati, OH 45245
513-528-5674
www.lns-northamerica.com