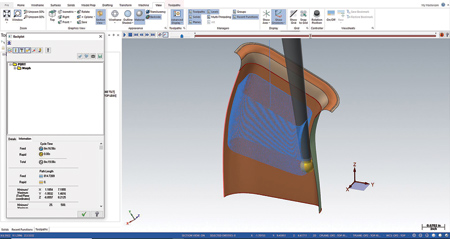
Mastercam's Accelerated Finishing on the port surfaces of an LS engine intake runner.
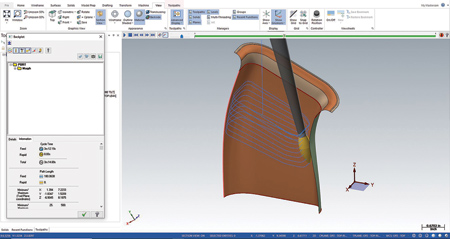
Mastercam's Accelerated Finishing on the port surfaces of an LS engine intake runner.
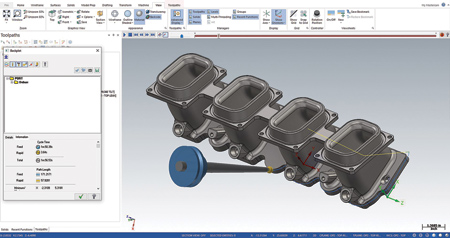
Mastercam screenshot of an LS engine intake runner. Material is 6061-T6 aluminum.
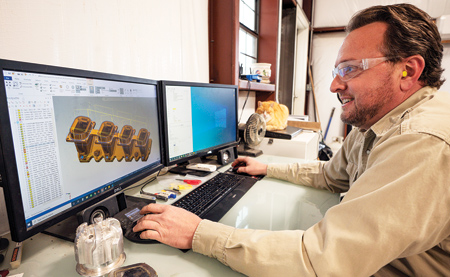
Ryan Green of RockQuality Consulting uses Mastercam to program machining of an LS engine intake runner.
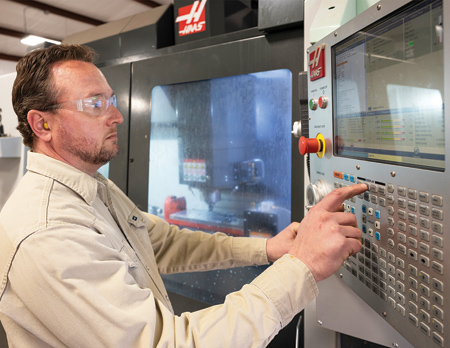
Ryan Green programs a Haas VF-4SS VMC.
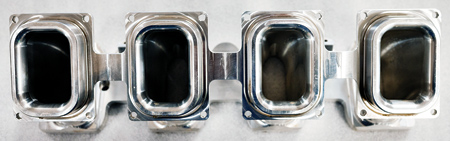
LS engine intake runner, machined by RockQuality Consulting.
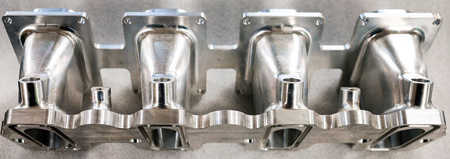
Cross section of an LS engine intake runner, machined by RockQuality Consulting.
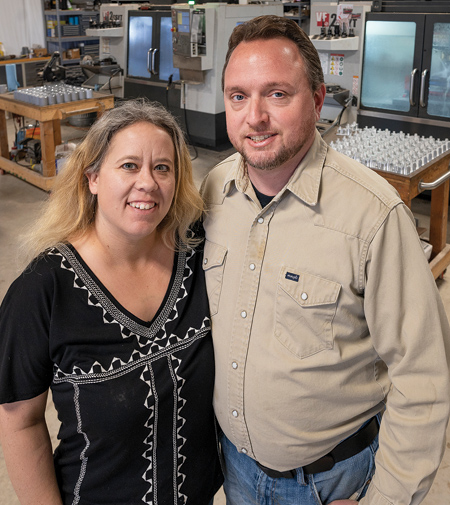
Julie and Ryan Green, owners of RockQuality Consulting, Liberty Hill, TX.
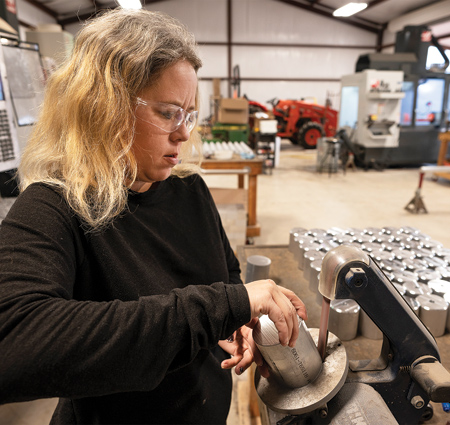
Julie Green, co-owner of RockQuality Consulting, prepping materials to be loaded into a Haas VMC.
When Ryan Green was a college student living in Austin, TX, he studied mechanical engineering and worked part time as an office temp. Recognizing that clerical work was not his calling, he yearned for something in the mechanical field. One day during his commute home, Green spotted a sign in front of a machine shop that read, "Now Hiring Machinists." That sign, and the immediate U-turn that followed, changed the course of Green's career path. He applied for the job and was hired as a machine operator, learning to write code, run machines and eventually, use CAD/CAM software.
"I was just fascinated with how the machines worked," said Green. "The company I worked for went on to hire someone who knew Mastercam CAD/CAM software (CNC Software Inc., Tolland, CT). He just ran circles around us. I remember thinking, `I need to learn how to do that if I want to keep my job.'"
Due to this job and those that followed, Green delved into Mastercam and, eventually, SolidWorks. His CAD/CAM capabilities grew rapidly, and he was hired as an applications engineer at MLC CAD Systems, the Austin-based Mastercam Reseller. Green used the software to train customers and troubleshoot programming issues. Eventually, he moved into MLC's sales department.
Green's next venture was to build his own machine shop business at home. RockQuality Consulting began in his garage, and steadily grew into a busy job shop. When COVID-19 hit, the pandemic affected much of Austin's semi-conductor manufacturing as the supply chain from China was severely disrupted. "That really gave a big shot in the arm to manufacturing here in Texas," said Green.
Green took the plunge in July 2020 and committed full time to RockQuality Consulting. A provider of precision CNC-machined parts and assemblies, the job shop serves several industries, mainly semi-conductor and aerospace.
"We have four machines," said Green. "We still have the one we began with-an old 1990 vertical 3-axis machining center. It is slow, but it is strong. Over time, we have added three Haas high speed machining centers, all equipped with 4-axis capabilities."
As he has throughout his career, Green appreciates Mastercam's capabilities and relies on them to take on a variety of complex machining jobs. One application in which RockQuality uses the CAD/CAM software is the production of high-end musical instruments.
"Our client has a unique product that we helped him design in CAD, and then we machine the metal parts," said Green. "I rely heavily on the Mastercam for SolidWorks product. I do all of my design with it for this particular customer."
Mastercam for SolidWorks is an integrated software solution that combines CAD with CAM. It lets users standardize a database of CAD files without compromising the quality of NC programming. It includes the CAD/CAM software's toolpath technology and post-processors in the CAD environment. The software delivers the ease of SolidWorks modeling, assemblies and drawings with fully associative toolpaths. Users can program an entire family of parts with one click.
RockQuality Consulting used the software solution for production of a critical part for musical instruments and accompanying custom hardware pieces. Placement of features must be tightly controlled since it is crucial to maintaining instrument tone.
"If we have to make a design change that will affect multiple associated parts, it is not even a question of poking around or not," said Green. "With Mastercam for SolidWorks, everything remains associative. Before using it, we would have to export out of SOLIDWORKS and then open up Mastercam, breaking the link between the Mastercam and SOLIDWORKS files."
Beforehand, if a change was made in SOLIDWORKS while there was a separate Mastercam file, it would not propagate back into that Mastercam file. It would take hours to program parts. Now, with the integrated software solution, a RockQuality machinist can easily make a change to a part file, saving valuable programming time.
Another Mastercam feature that helps RockQuality Consulting take on tough machining jobs is Dynamic Motion technology. Because the technology utilizes the entire flute length of a cutting tool, air cutting is reduced or eliminated, tool life is extended and cycle times are reduced. The technology makes cutting tough materials easier, and it helps new and old machines perform better.
"Dynamic toolpaths revolutionized the approach to machining parts," said Green. "It did away with the mindset that you have to have a really massive, expensive machine to handle heavy cutting."
For example, RockQuality cuts some parts from heat-treated stainless steel, which is harder and can be more brittle than untreated stainless. Using proper cutting tools and machine features, in tandem with Dynamic Motion technology, makes the tricky task of machining heat-treated steel possible.
"There is no way I could make some of these parts without Dynamic Motion technology-not on the equipment I have," said Green. "I would have to invest in heavier machines and, to be honest, they would be out of my reach. Dynamic motion makes so much possible."
Mastercam helps RockQuality Consulting push the capabilities of all its machines. A comprehensive selection of toolpaths provides the precision and flexibility needed to take on a variety of machining jobs. When choosing toolpath utilities, Green leans on Mastercam Multiaxis, which improves productivity with simultaneous 4- and 5-axis machining capability. It offers a range of basic and advanced multiaxis machining strategies. In addition, these toolpaths are useful for advanced control of 3-axis machines.
"That is something that throws people-that multiaxis is really helpful for 3-axis applications," said Green. "The introduction of the Multiaxis Deburr toolpath was just huge."
Multiaxis Deburr can use ball end mills or lollipop undercut tools to break edges for 3- to 5-axis and to remove burrs. Fast, automated part deburring is possible through climb or conventional cutting, with more controls for selecting which area of the part to deburr. The toolpath eliminates the need to manually deburr, reducing machining time.
Machined parts cannot have sharp edges; for Green, 3D parts were especially challenging. "They required a manual means of deburring, which was definitely not fun and not consistent," he said.
In the past, the shop team often relied on 2D Chamfer or Model Chamfer toolpaths to deburr all planar edges. For parts with 3D edges, RockQuality would sometimes use a tumbler to finish them. However, some customer requirements do not permit use of a tumbler, since it may lead to excessive edge rounding.
"When Multiaxis Deburr came along, that changed everything for us," said Green. "We simply use it in 3-axis mode and with a .25 in. ball end mill. This has led to consistent edge breaks in all dimensions, for all parts in a run, greatly speeding the manufacturing process."
RockQuality maximizes its surface finish process through Accelerated Finishing, which works in conjunction with advanced cutting tool shapes, including oval form cutters, barrel mills, taper cutters, lens-shaped cutters and lens barrel form tools. Toolpath strategies enable a large cutting radius for small diameter tools, yielding reduced cycle times and improved surface finishes. Accelerated Finishing engineered to deliver higher quality surfaces in less time than traditional finishing methods.
For one of its automotive customers, RockQuality produced a set of billet intake manifold runners by using a lollipop cutter to perform port surfaces in a simultaneous 4th axis set-up. By switching to Accelerated Finishing and using a barrel shaped cutter, the job shop increased stepover by six times and slowed down the feedrate to yield a smoother finish. The result was a 60% reduction in port surfacing time and a higher quality surface finish.
"With Mastercam, I am not at all concerned with what I can and cannot run here," said Green. "The sky is the limit. We take the part, fit it in the machine-and even if we cannot fit it, there are tools in Mastercam to help us around that."
As RockQuality continues to grow, Green is secure in knowing that his colleagues at MLC CAD Systems will lend support if issues arise and keep his shop current on the latest CAD/CAM developments.
"MLC is really good at making sure customers are taken care of," he said. "They put on a regular event called CAM Skills that provides new perspectives on things. It really helped me stay on top of trends."
For more information contact:
RockQuality Consulting LLC
1208 County Road 204
Liberty Hill, TX 78642
512-826-8341
CNC Software, Inc.
671 Old Post Road
Tolland, CT 06084
800-228-2877
info@mastercam.com
www.mastercam.com
SOUTHWEST
MLC CAD Systems
4625 W William Cannon Dr., Bldg. 5
Austin, TX 78749
800-364-1652
www.mlc-cad.com