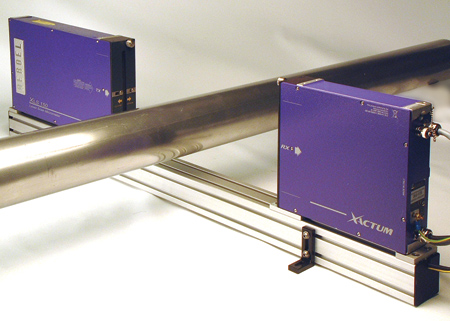
The Aeroel Barline.X from Marposs offers high accuracy measuring of ground bar and tube stock.
Marposs offers the Aeroel Barline.X system for measuring the outside diameter of products manufactured in cut lengths such as steel ground bars, steel drawn tubes, copper tubing, etc. With online gauging and continuous through feed measurement, the system provides real-time grinder regulation, automatically preventing the production of out-of-tolerance products, helping to reduce scrap and risk of rejects later in the process.
The Barline.X systems can measure diameter and ovality of stock from 0.1 mm (0.00394") to 149 mm (5.86") using either a single or dual axis (XY) laser gauge, depending on the diameter range and the type of product. These non-contact systems are impervious to product vibration and movement, enabling continuous inspection. In most cases, the sensor can be installed just after the grinding wheel and before the oiling device so that the use of oil does not interfere with gauging accuracy. In this position the tube/bar can be easily cleaned by blowing away the emulsion.
"The systems feature a patented self-calibration device that guarantees permanent gauge accuracy with no re-mastering required," said a company spokesperson. "Equipped with Barline software, guided menus help ensure maximum ease of usage, even for untrained staff. In addition, due to factory pre-programming, Barline systems are immediately operative in their basic functions."
In addition to three single-axis Barline.X models, there are also two double axis Barline.XY models available. Depending upon the system, repeatability falls within ±1-3 µm. All of the Barline.X laser systems come with pre-loaded software, which is easy to use and simple to program even by nonexperts, according to the company. Also included is a CE-200 Operator's Interface Panel and connecting cables.
By connecting a printer to the CE-200 panel, users can access a print-out listing of max., min. and average values measured on each part. In addition, this data can be recorded and processed as a final statistical report related to each selected bundle of bars. Through an Ethernet or RS232 serial line, a remote computer can be used to download the measured data or to program the system.
How it Works
The Barline systems use an Xactum Laser Gauge, installed at the output of the grinder or drawing bench, which measures the outside diameter of the product passing through the laser beam. The non-contact operating principle enables through-feed inspection without having to stop or slow down the product, since its vibration and movement do not affect the gauging accuracy.
The measured average diameter is continuously compared with the nominal value pre-set by the operator: if the product size moves out of the pre-set limits, the Barline software automatically adjusts the grinder, recovering the wheel wear to keep the product within the desired tolerance limits. After skipping the head and the tail, all the readings taken along the bar are stored in memory and compared to the pre-programmed tolerance limits. If there is a non-conformance issue, signals are activated at the end of the bar to drive sorting and/or rejecting devices.
For more information contact:
Marposs Corporation
3300 Cross Creek Parkway
Auburn Hills, MI 48326
248-370-0404
marposs@us.marposs.com
www.marposs.com