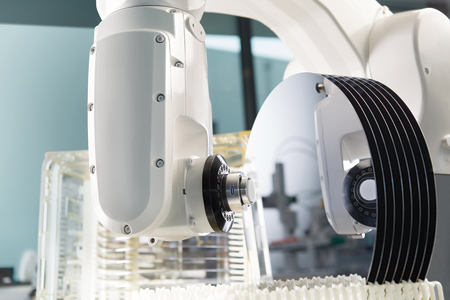
Adhesive SCHUNK gripper with ADHESO gripper technology is customized to the individual application. This way wafers and the smallest electronic components can be handled, as well as foils or workpieces from the field of metalworking and automotive assembly.
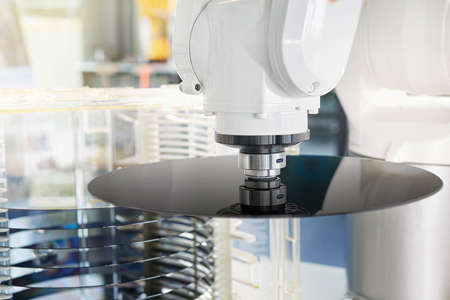
"With the help of adhesive forces, geckos have been moving easily over smooth surfaces for millions of years. Now, SCHUNK is using this principle for developing various fields of handling applications with its new gripping technology, ADHESO," said a company spokesperson.
Components can be gripped in a sensitive way, without leaving any residues or requiring additional energy. "The solutions are always individually developed and are as diverse as the applications themselves," said the spokesperson. "Glass fibers as light as feathers, smallest SMD components or micro-mechanical parts can be handled, as well as sensitive battery components, plastic films, paper and glass, as well as automotive or mechanical engineering components of a weight of 15 kg and more. Automated separation of breathable components is also feasible."
The bionic inspired gripper technology ADHESO is based on the principle of adhesion, using the intermolecularly acting Van der Waals forces for handling. The patented surface architecture is made of special polymers and is optimized by numerical simulation. The result is a structure of extremely finely structured legs, which adheres to different materials and objects. The structure is gently pressed onto the workpiece during the gripping process, thus increasing the contact surface, and the Van der Waals forces can start acting on the workpiece. This effect can be reversed by applying a slight pressure/rotary movement so that the gripper can be loosened residue-free from the handling object. The alternative use of a wiper ensures that the object is gently put down.
The respective adhesive forces and removal of ADHESO depend on the variation of material, topography and miniaturization, and is customized to the different requirements of the relevant environment. Therefore, the adhesive structures can be adapted application-specific to the required size and the loading condition (horizontal/vertical), and can be designed transparent, translucent or opaque. "This is the big advantage: the high degree of individualization ensures that components with dimensions of a few hundred micrometers can be handled as reliably as those measuring several meters," said the spokesperson. SCHUNK specialists are available to support users during the design and planning phase.
"Effort and costs for installation and commissioning are minimal, since the adhesive technology is gentle on components, low-noise and does not require compressed air, vacuum or current," said the spokesperson. An external energy supply is not necessary for gripping or for maintaining the gripping force. In case of a power failure in the handling system, the holding forces of the gripper are reliably maintained. SCHUNK ADHESO allows gripping times of < 100 ms. It can be used in conventional industrial environments as well as cleanrooms and vacuum environments. In the field of micro handling, repetitive positioning accuracies of < 0.01 mm can be achieved with this technology, and it can be also used in collaborative applications. The ADHESO gripper has a bayonet lock and therefore the grippers can be exchanged in just a few simple steps.
For more information contact:
SCHUNK Inc.
211 Kitty Hawk Drive
Morrisville, NC 27560
919-572-2705
info@us.schunk.com
www.us.schunk.com