
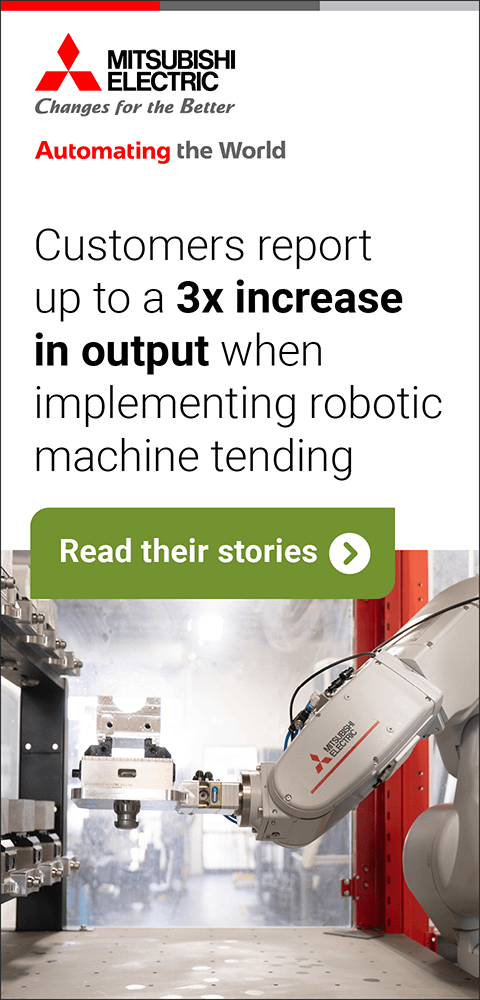
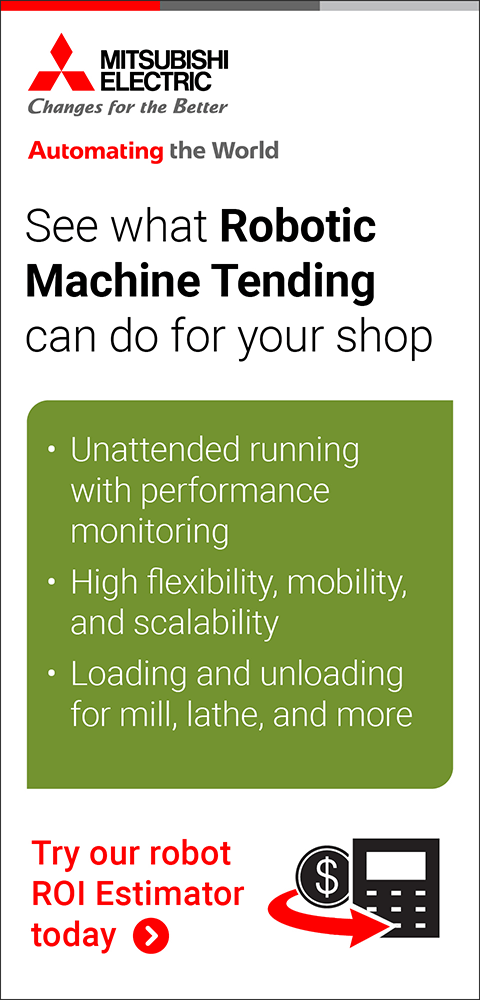
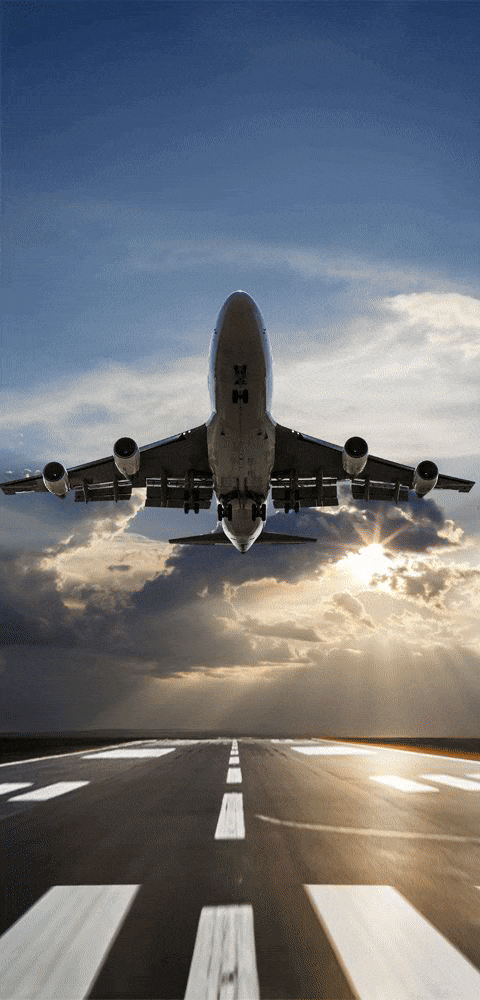
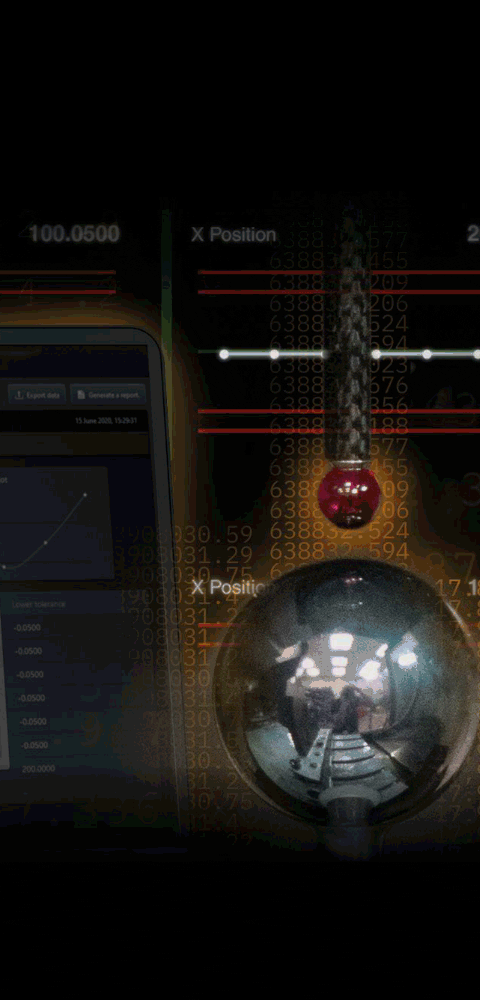
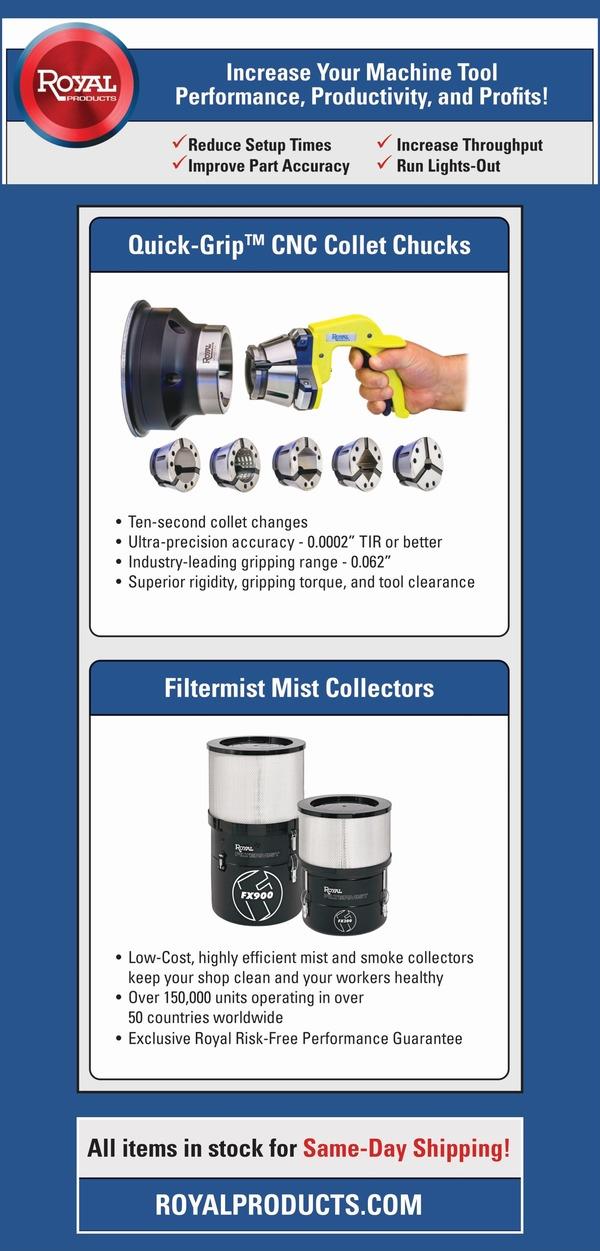
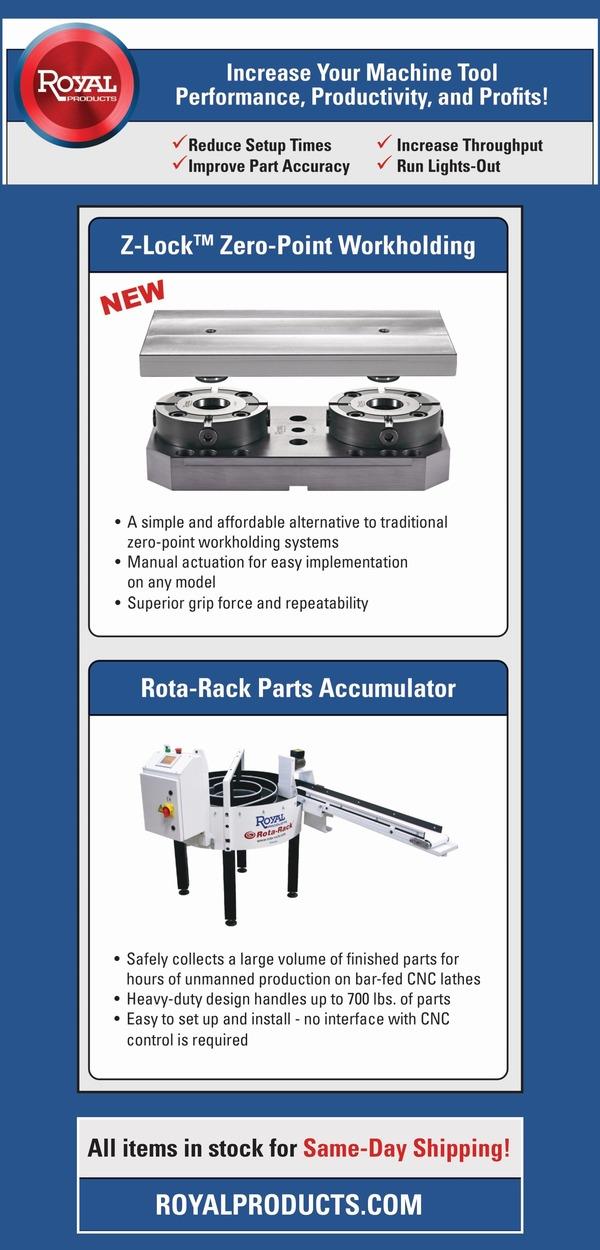

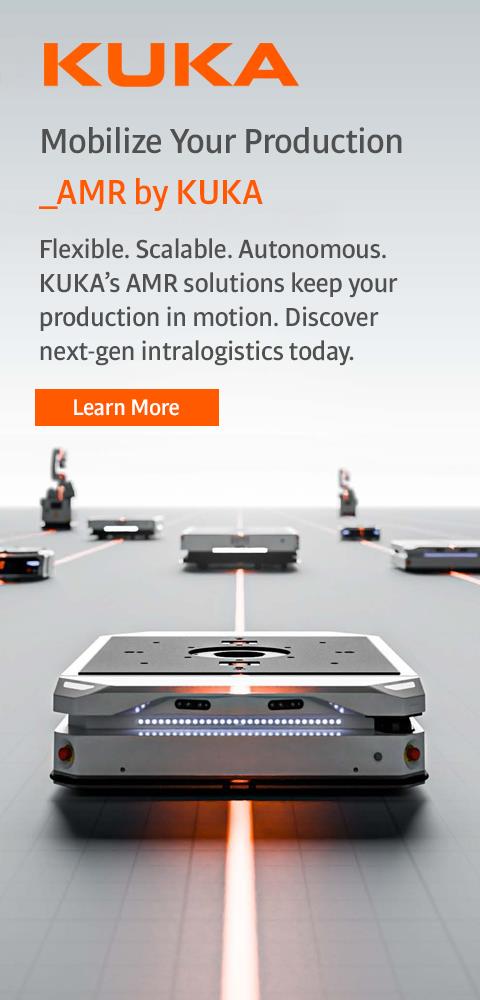
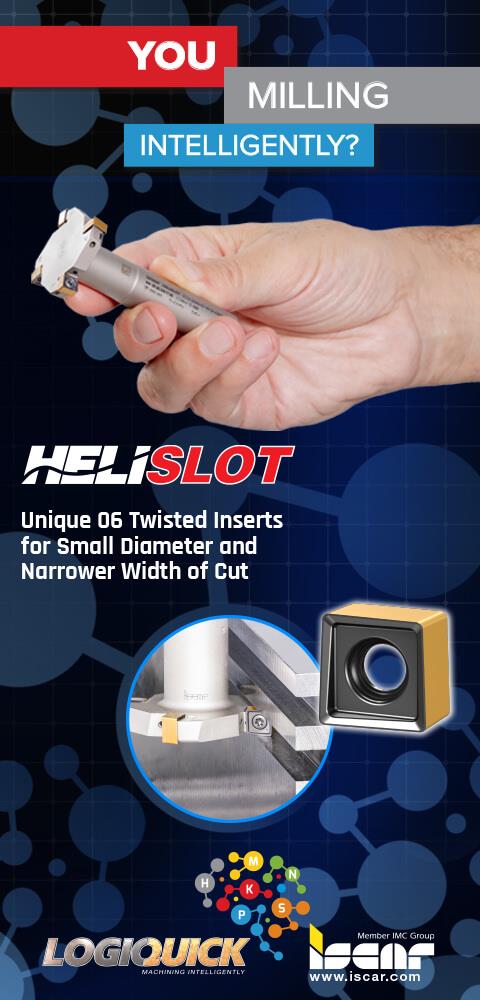
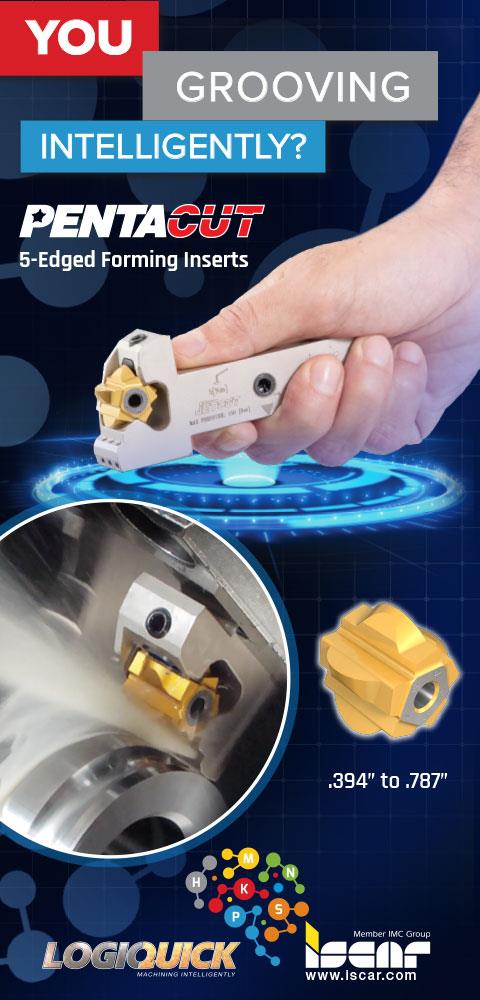
ROHM Service Center Provides Cost-Saving Chuck Repairs and Rebuilds
March 1, 2018

RÖHM's factory-trained technicians provide onsite maintenance and repairs to maximize holding power.
"To better serve its customers, RÖHM Products of America has made significant investments in its ability to offer truly comprehensive chuck repair and rebuild services at its Suwanee, Georgia-based headquarters as well as onsite at its customers' manufacturing facilities across the country," said a RÖHM spokesperson. "In doing so, the company creates a one-stop shop for all chuck service needs."
"When we moved to our new headquarters in 2015," said Adis Malkoc, Manager of RÖHM's Service Center, "we dedicated a lot of space for our service team, along with new 2-ton and 10-ton cranes for the biggest repair/rebuild jobs. With this investment, we have created a turn-key approach that has been very popular with our customers. We offer the quickest way for shops to install, maintain and repair their workholding devices."
RÖHM's engineering staff possesses nearly 50 years of combined experience with the fixturing, equipment and processes necessary for the precision repair and rebuilding of even the largest sized chucks. These same service engineers also provide new customers with installation assistance along with guidance in proper product use and in the development of an optimal preventative maintenance schedule. They also conduct training sessions for products currently in use to keep operator skills and knowledge current. "It is hard for shops to maintain the level of expertise our specialized team has," noted Service Engineer Doug Thompson, "but after our training, we can ensure that manufacturers have the know-how to keep fixtures in working order until they need to be sent back for periodic rebuilding."
The RÖHM Service Center provides rebuild quotes and services that extend the life of valuable products. Most parts needed for these rebuild processes are in stock at the company's Georgia facility, though large, complex or custom fixtures may require parts from the company's German factory. These scheduled rebuilds can also identify worn parts before they fail completely, which results in significant savings for those manufacturers that take preventative maintenance seriously.
For more information contact:
RÖHM Products of America
2500 Northlake Drive
Suwanee, GA 30024
800-445-7646
rohmusa@roehm.biz
www.rohm-products.com
< back