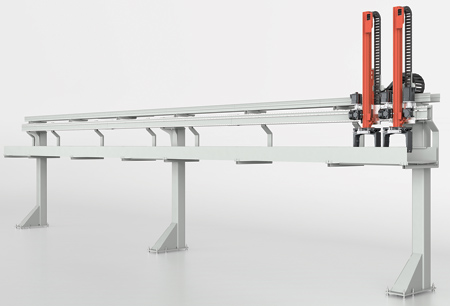
The LP 100 gantry robot can be built with a wider clearance between uprights
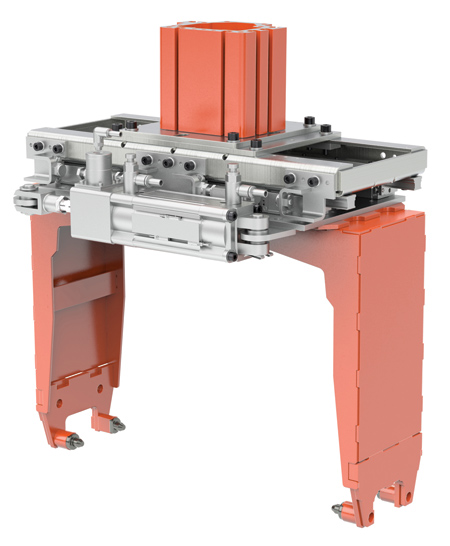
Standard gripper
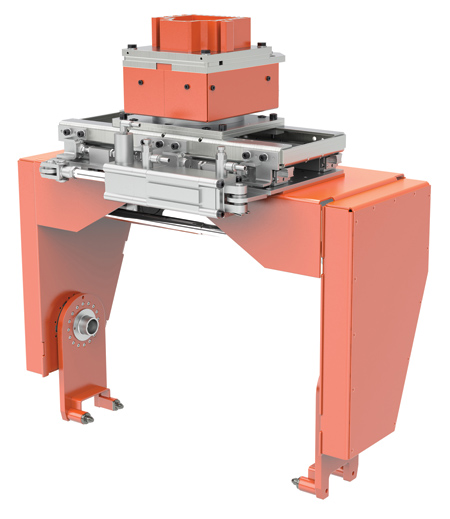
Gripper with additional axes
Liebherr is plugging a gap in the automation system field with the new LP 100 gantry portal, which is particularly suitable for handling smaller and lighter components. Its flexible design makes it dovetail well with inline production concepts, where workpieces have to cover larger distances.
Downsizing is a growing trend in the automotive sector. Engines are becoming more efficient and therefore smaller and lighter. This new size of gantry robot LP 100 gives engine and gearbox manufacturers more options, enabling them to find their own optimum solutions. It is suitable for use in the weight category including cylinder heads and gearbox housings, as well as alternative drivetrain units, like electric or hybrid engines, fuel cells or components of a similar size. The option of configuring the gantry to deliver high-speed or high-load performance is new. This variability further increases the flexible use of the LP 100.
Ideal for Inline Production
The design of the gantry robot has been adapted to meet the range of modern production process requirements. "The new design enables our customers to select a wider clearance between uprights, for example," said Martin Winterstein, Director Global Business Development & Sales Channels Automation Systems in Kempten, Germany. "Planners thus have extra production line design and installation options."
Nowadays, the inline concept, featuring long travel ways, dominates production lines. Loading gantries handle transportation of workpieces, as well as loading and unloading of machines.
Conveyor belt systems for the transportation of workpieces are now only required to a lesser extent. Furthermore, the number of machines covered by a single loading gantry is increasing in order to increase production capacity at minimized use of automation systems.
"Changes in the line design have consequences for the automation system: workpieces must cover greater distances at higher speeds" Winterstein added. "The fact that machinery and machining centers are constantly getting faster is also putting pressure on cycle times. Of course, we take these trends into account in the development of the gantry and offer solutions such as the high-speed versions. This new specialism (high-load and high-speed versions) is due to be applied to existing gantry models during the course of the next two years. Liebherr will therefore be able to provide optimum-sized, cost-effective automation solutions for all industries with no limitations on functionality and performance."
Modularly Controlling the Automation Process
Central tasks of automation software include the acquisition of operating data, production planning, parts tracking and an information system. These modules are available with the new Liebherr Manufacturing System 4.0 (LMS 4.0). They can be added to a basic package forming the foundation of all modules. This means that every customer gets the right software solution for its automation system.
Simple operation is the top priority: a new graphically guided interface concentrates functions in a user-friendly manner on the host computer, and if required allows full control of production. Furthermore, there are interfaces to the most common ERP systems.
For the LMS 4.0 Part Tracking Application module, the workpieces need clear identification codes, such as bar codes or matrix codes. Scanners must be installed at every station to continuously register the processing steps and the status of the parts. The LMS 4.0 Production Scheduler can set up production assignments statically or dynamically according to the final deadline. External assignments - for example from SAP - can also be imported, which gives users flexibility when planning and managing their assignments.
The LMS 4.0 Production Monitoring Application is used for data acquisition. It gathers operating data and statuses of the individual stations and their availability. In addition, it also counts the workpieces and displays error messages. If this module is installed, users can also use the LMS 4.0 Info Board module. This visualizes the production cell: production and operating data can be called up on a large monitor, taking current or historic data (including target specifications) into account. For example, the Info Board means that the user always has an eye on whether the cells are active and whether the target specifications are being fulfilled.
The Benefits of the LP 100
- Optimum matching of costs and speed (Standard, High-Speed, High-Load)
- Parallel assembly operations feasible for short lead and delivery times
- Higher speed for faster cycle times.
For more information contact:
Liebherr Gear Technology, Inc.
1465 Woodland Drive
Saline, MI 48176-1259
734-429-7225
info.lgt@liebherr.com
www.liebherr.com