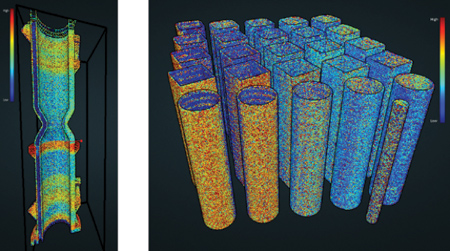
3D thermal mapping and imaging using Thermal Emission Density (TED)
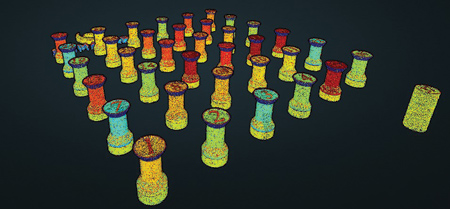
With the increased precision of Sigma Labs' melt pool TED data and part quality characterization methodology, users can more accurately correlate quantitative thermal feature data and in-process quality metric (IPQM) data with post-process quality metric data from NDE, metallography or destructive tests.
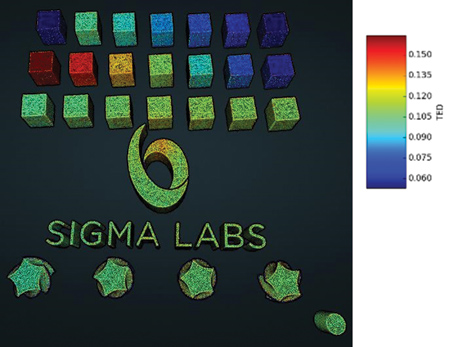
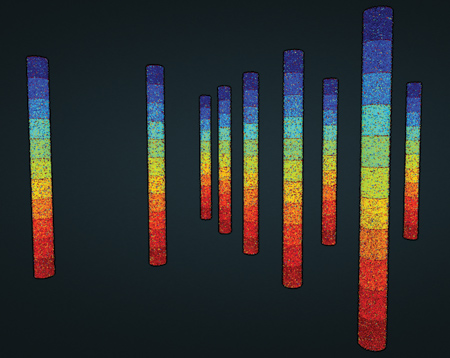
Sigma Labs has developed and released its next generation PrintRite3D INSPECT in-process quality assurance (IPQA) software - Version 3.0. "This release includes software enhancements and hardware upgrades and completes our migration to a distributed web-based application," said a company spokesperson. "Our newest release contains the industries most advanced set of IPQA analytics algorithms that enable future generations of closed loop controllers."
The software is now available for multi-machine single laser systems, providing customers with one portal for monitoring their entire additive manufacturing (AM) lab. Single and multi-machine, multi-laser configurations are in development with the OEM partners and as third party add-ons.
PrintRite3D INSPECT 3.0 software features 3-D thermal mapping and imaging tools as well as the company's exclusive Thermal Emission Density (TED) powered advanced analytic engine designed to meet the needs of users focused on research, development and qualification-level activities. The researcher tools utilize raw sensor feature data without the need for baseline comparisons providing users the data and framework for limitless analysis. Quantitative, in-situ thermal history maps can be used to validate modeling and simulation (M&S) results prior to process characterization studies, process qualification and validation phases, as well as in conjunction with design optimization evaluations.
At the hardware level, existing users of the Version 2.0 platform can update software to Version 3.0. Users of versions older than Version 2.0 require a hardware upgrade to support Version 3.0 software. For new users, the PrintRite3D INSPECT 3.0 hardware package offers a much-reduced footprint at a lower cost. A stand-alone computer console is no longer required at the machine. The onboard sensor suite collects and feeds raw data to an edge intelligent computer. The edge computer performs proprietary data reduction and sends the reduced-order data to a cloud-based server for advanced analysis.
Sigma Labs' distributed, web-based architecture allows data analysis and visualization to be performed by the PrintRite3D INSPECT 3.0 software residing in a cloud-based server. This cloud-based, PrintRite3D INSPECT server can be a company's enterprise wide server, a local server or a remote server. Its user friendly human machine interface (HMI) permits set-up, start, stop, visualization and melt pool analysis results to be reviewed from any web-enabled device connected to user network. An optional tablet is provided at the machine for local HMI functions.
New features - "Research, Development and Qualification" include:
- Part by part, layer by layer real-time melt pool TED data
- High resolution 3-D thermal part map
- No baseline data sets required
- Client-server hardware architecture with a single viewing portal for monitoring multiple machines across an entire manufacturing organization.
Summary of benefits:
- Enables rapid qualification of metal AM
- Confirms modeling and simulation predictions using high resolution thermal history data
- Documents key process input variations on geometry
- Accelerates parameter optimization for optimal thermal conditions
- Allows design optimization to eliminate high stress concentrations.
For more information contact:
Sigma Labs Inc.
3900 Paseo del Sol
Santa Fe, NM 87507
505-438-2576
info@sigmalabsinc.com
www.sigmalabsinc.com