
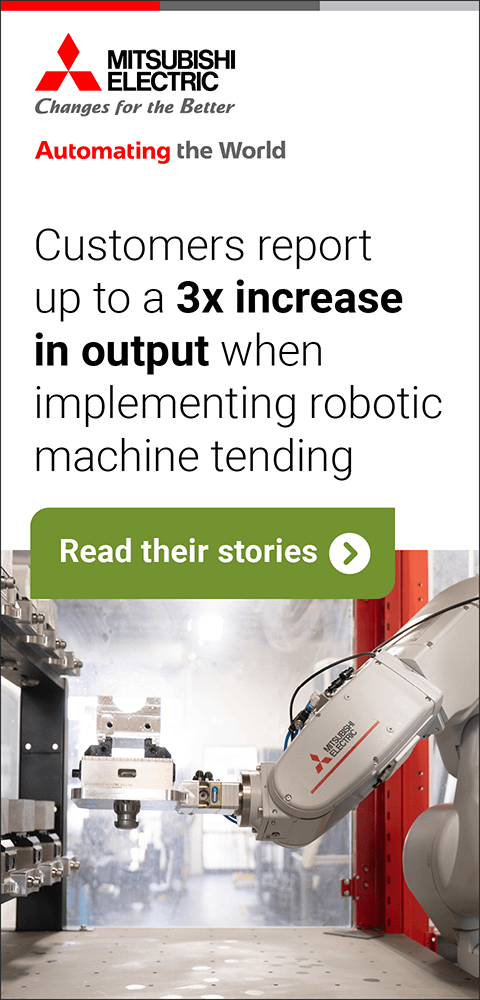
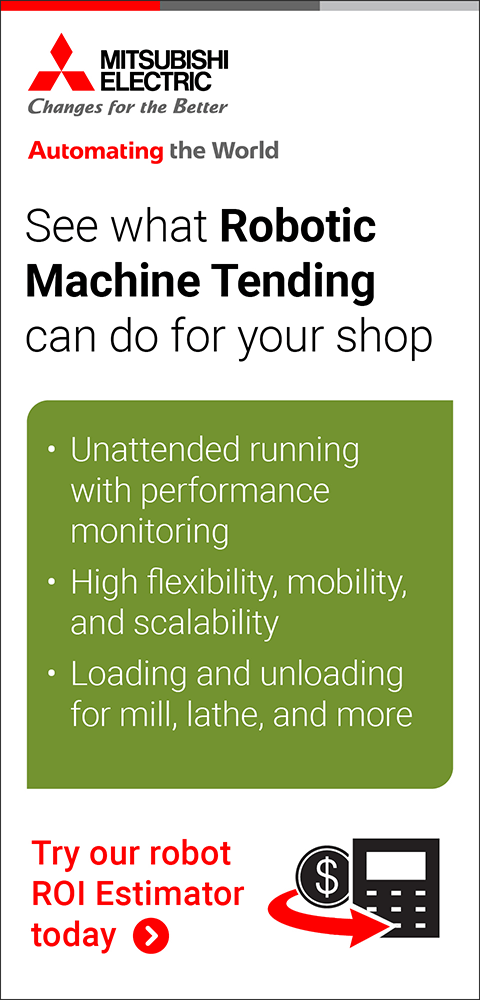
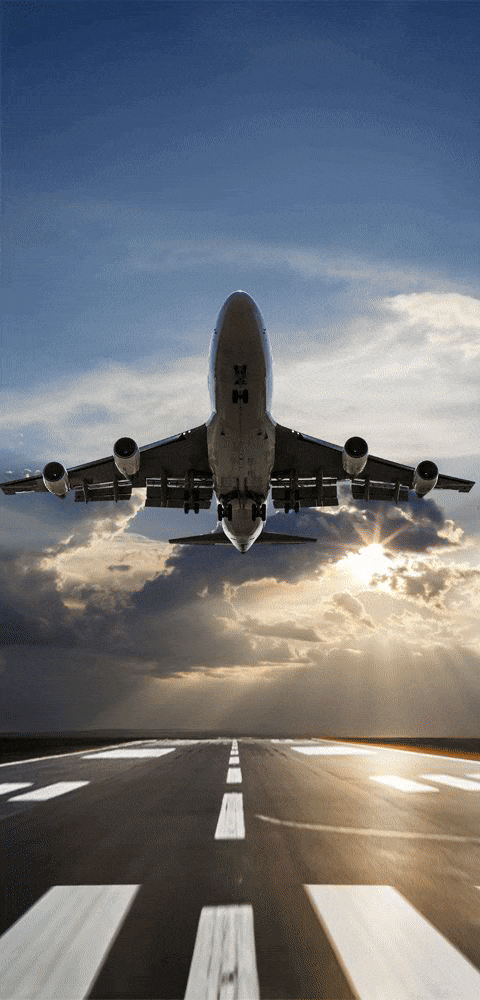
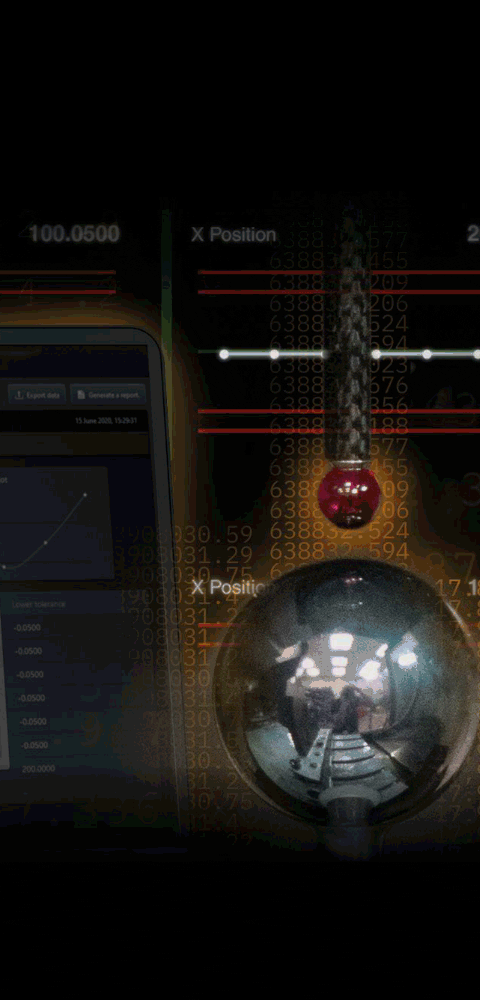
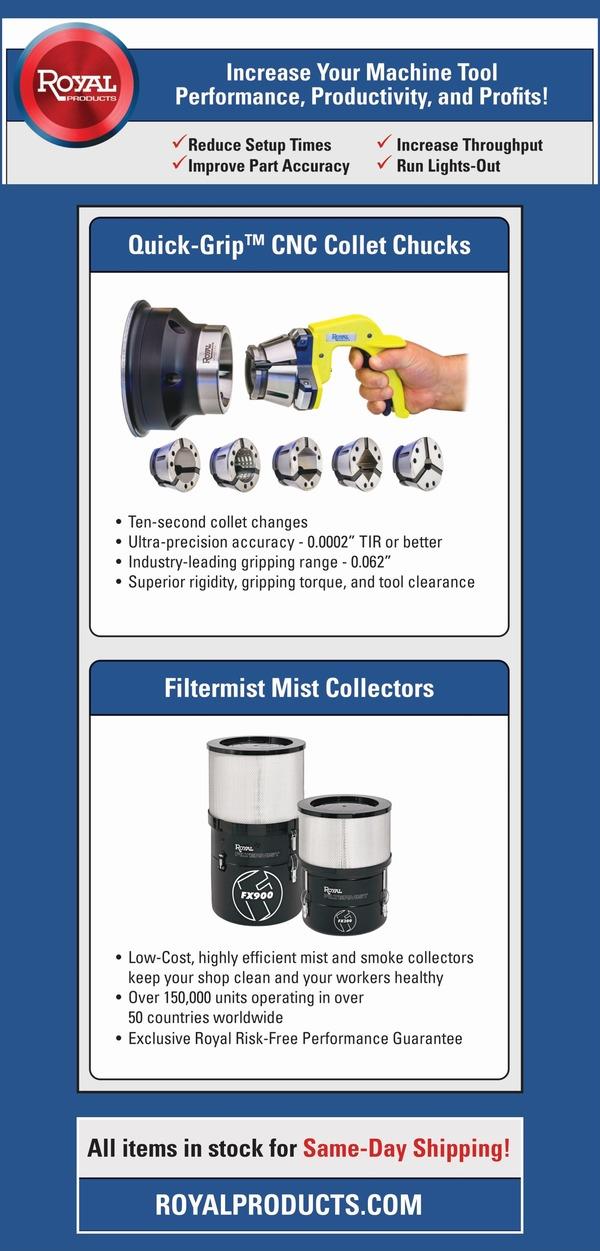
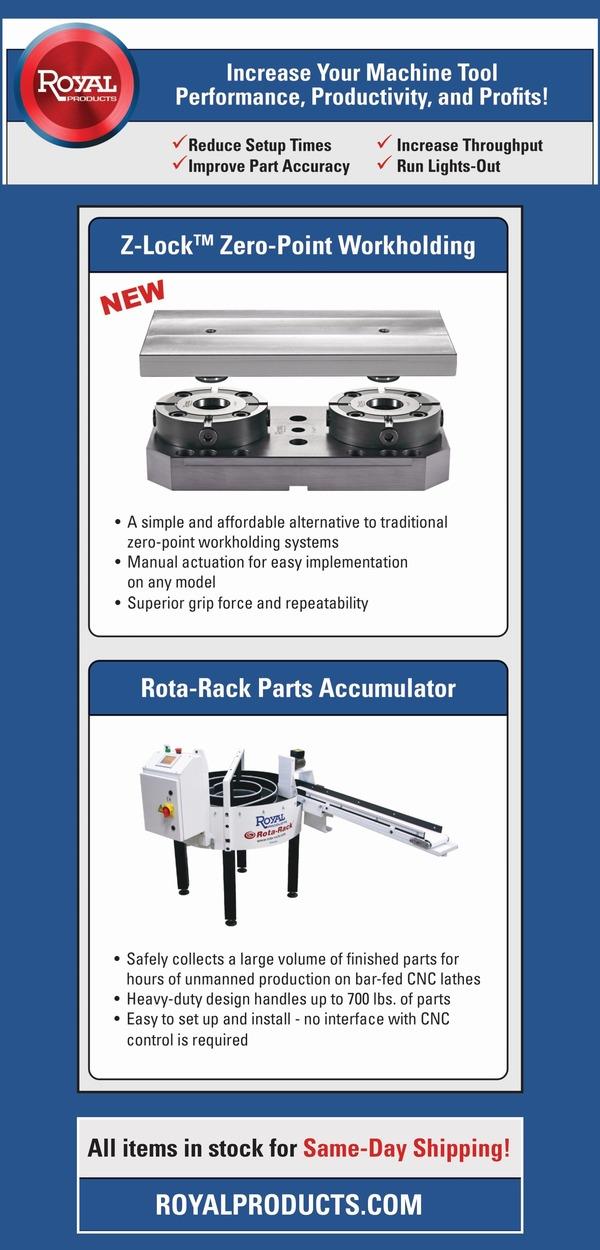

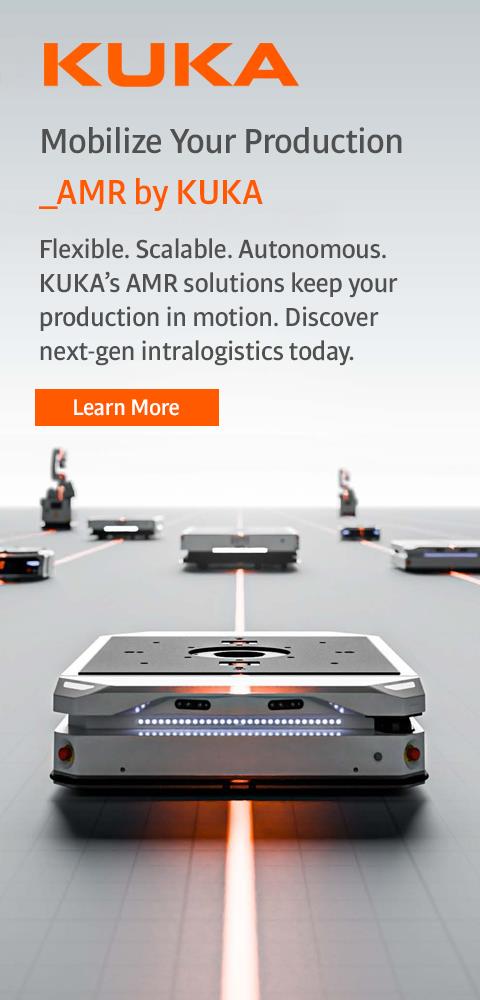
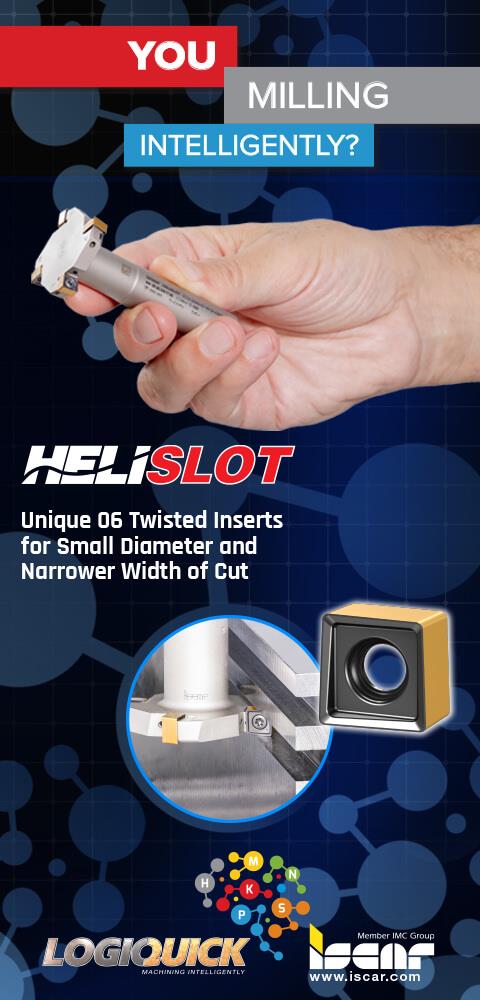
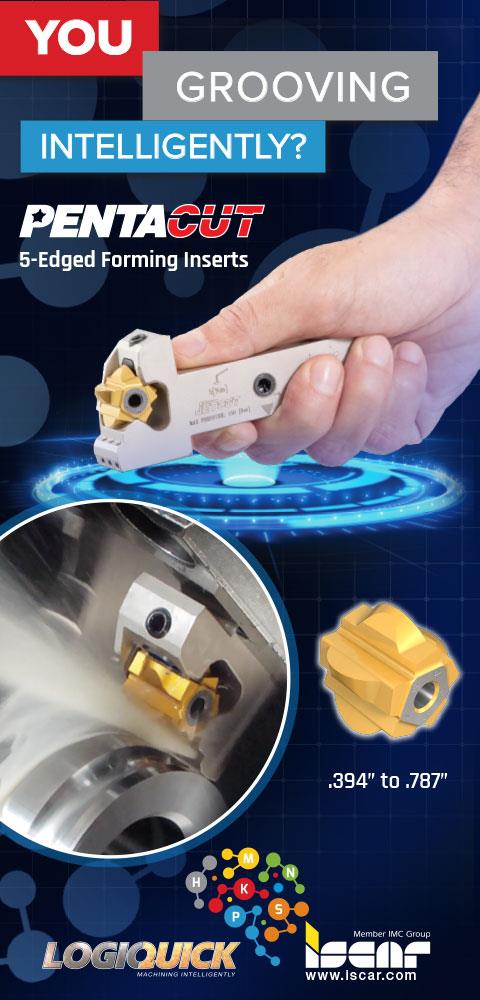
3-D Printing System for Industrial-Scale Additive Manufacturing
March 1, 2018
TRUMPF, a global technology provider of fabricating machinery and industrial lasers, has released the TruPrint 3000, a powerful medium-format 3-D printing machine geared towards the large-scale production of complex metal parts. Depending on the mechanics of the desired part, it can be made from a variety of weldable materials including steel, nickel-based alloys, titanium or aluminum.
The TruPrint 3000 utilizes laser metal fusion (LMF) technology, which uses lasers to generate complete metal parts layer by layer in a powder bed measuring up to 300 mm in diameter x 400 mm in height. Additionally, the machine is equipped with an exchangeable cylinder concept, which allows the construction chamber and supply cylinders to be switched out quickly. This saves time because operators can prepare a new set of supply cylinders and also unpack the finished build outside of the machine.
The TruPrint 3000 is equipped with two supply cylinders measuring up to 75 L, which is about 2.5 times the construction volume and contains enough powder to complete the entire manufacturing process without having to stop, regardless of how large the part is. This reduces downtime while also increasing the 3-D printer's productivity.
Once the manufacturing process is complete, the new parts have to be removed from the machine, cleaned and detached from the substrate plate. This process is completed in the unpacking station, which is seamlessly integrated into the process chain. The unpacking procedure is now an offline process running parallel to production and allowing for increased machine utilization.
At the end of the production process, the excess material ends up back in the automated sieve station that refines several hundred kilograms of powder every hour. This refined material can be recycled back into the TruPrint 3000 and utilized for future parts.
For more information contact:
TRUMPF Inc.
Farmington Industrial Park
111 Hyde Road
Farmington, CT 06032
860-255-6000
info@us.trumpf.com
www.us.trumpf.com
< back