
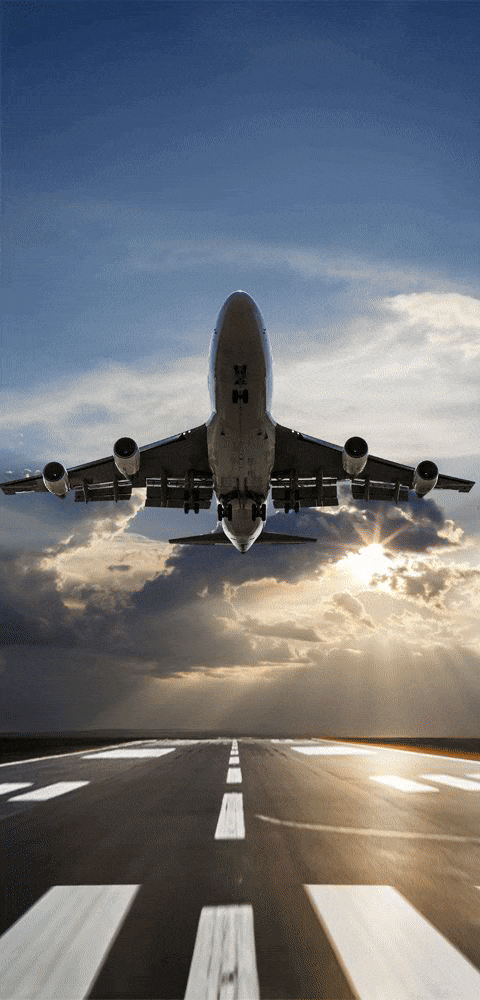
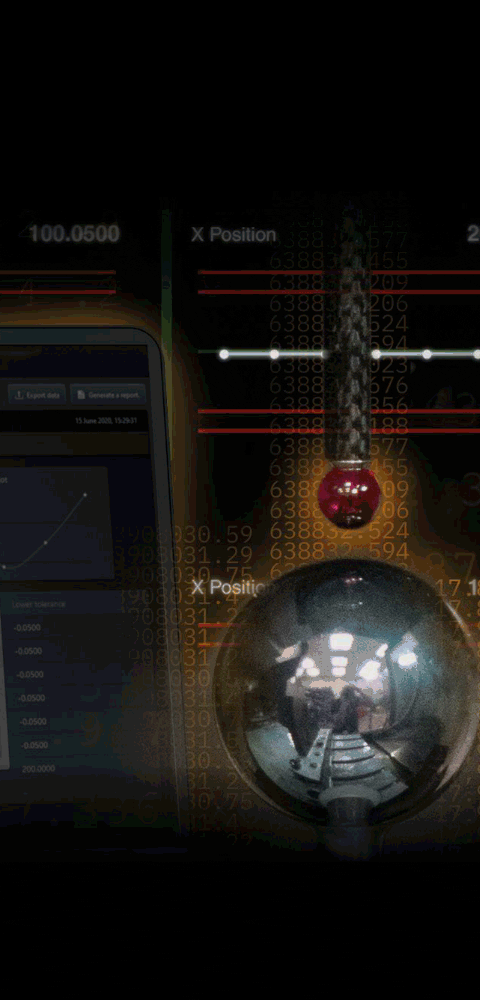
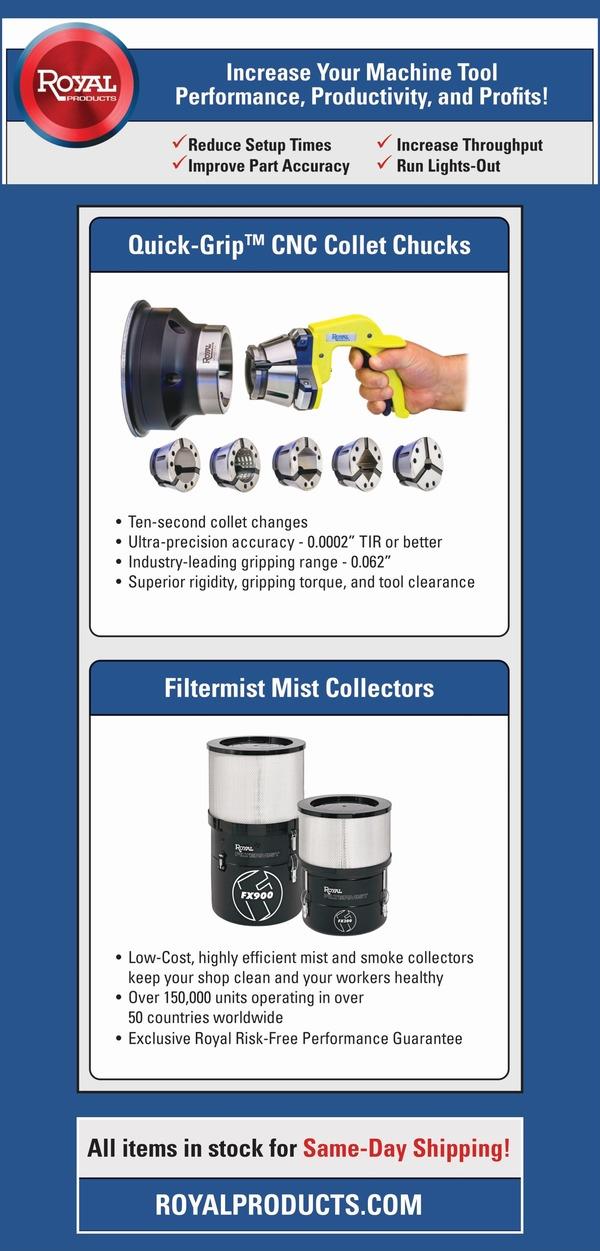
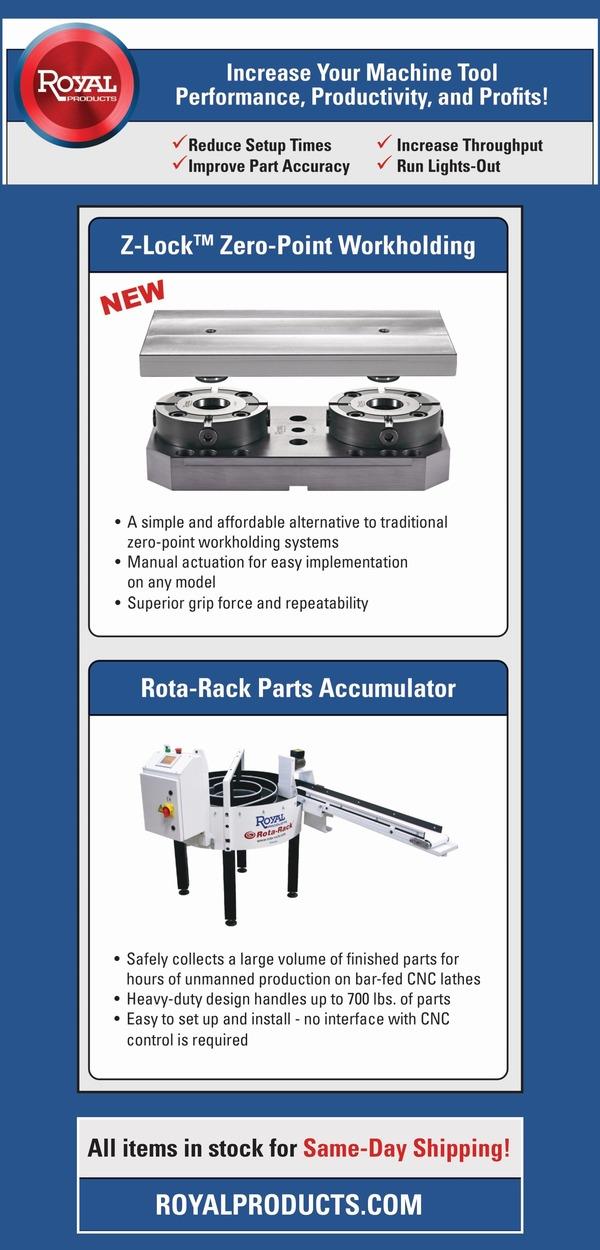

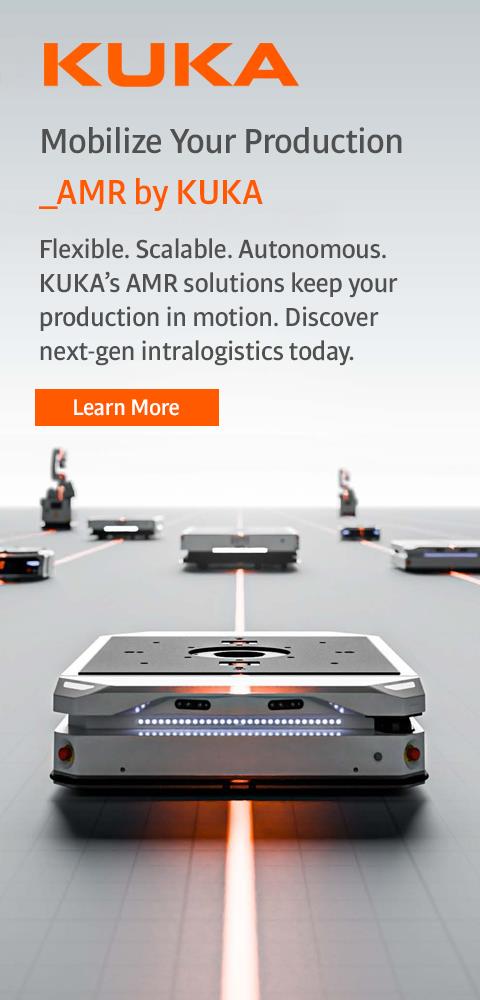
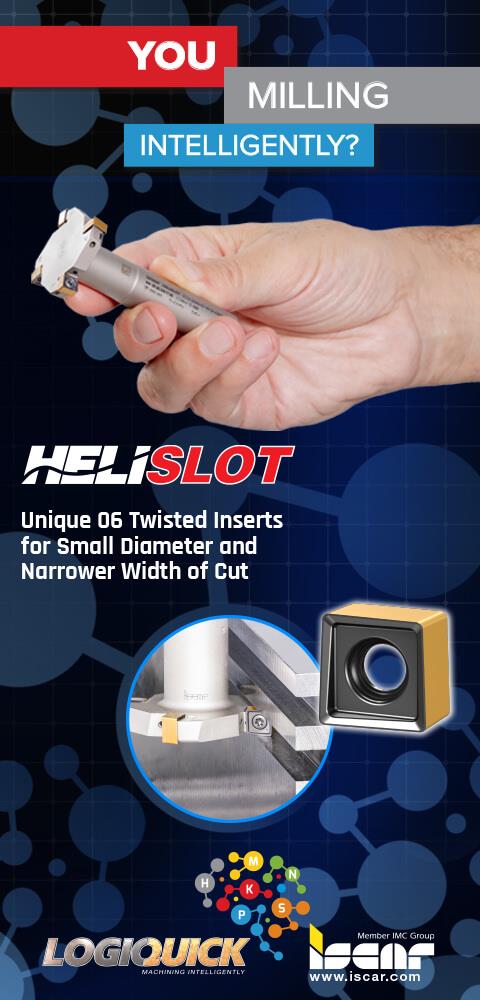
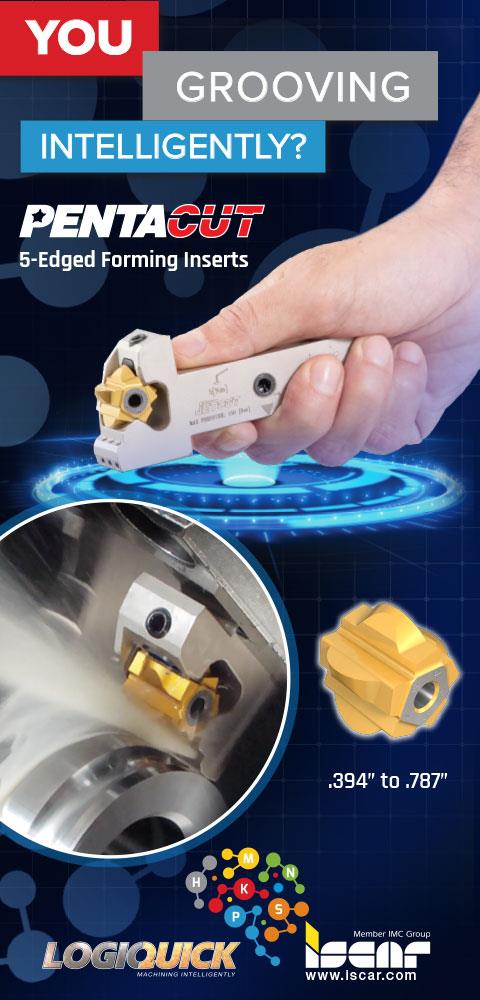
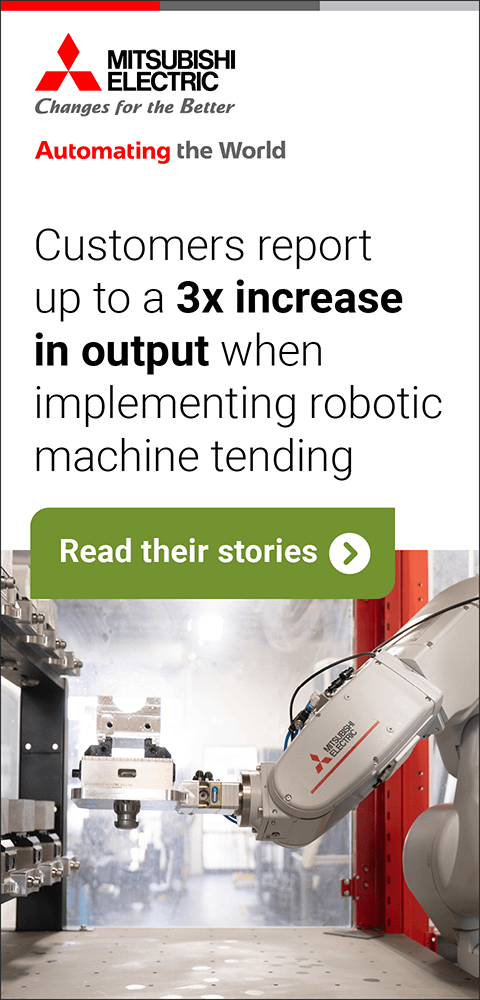
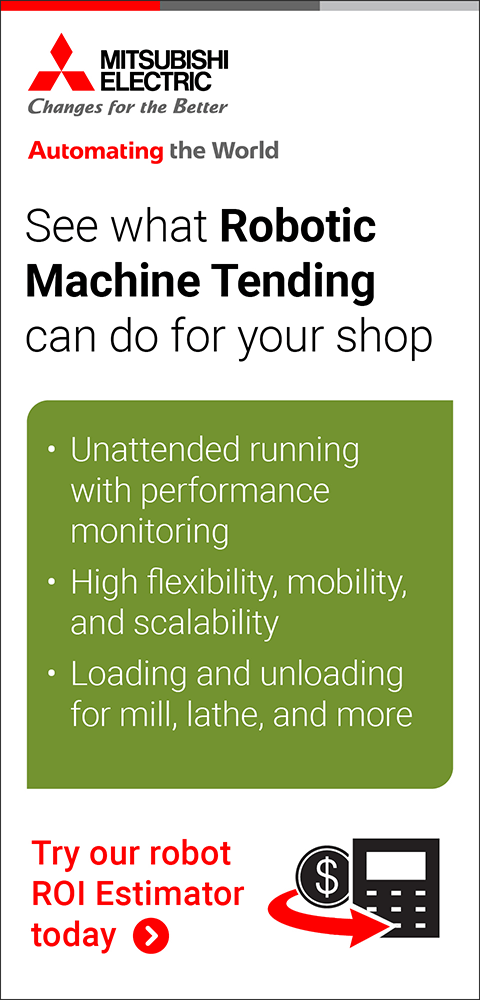
Next Generation Metal Additive Manufacturing
March 1, 2018
OR LASER has unveiled its latest metal additive manufacturing (AM) development - the ORLAS CREATOR hybrid 3-D printing and milling machine. The ORLAS CREATOR hybrid brings together the benefits of AM and subtractive manufacturing within a single platform to offer a comprehensive manufacturing solution. It combines the advantages of 3-D printing complex metal components using the direct AM powder melting process with OR LASER's advanced milling capabilities for precision finishing.
The ORLAS CREATOR hybrid goes beyond the capabilities of classic milling/machining, whereby structures and surfaces that are not normally reachable (such as inside contours, undercuts or hidden cooling channels) can be milled effectively. The ORLAS CREATOR Hybrid offers all of the 3-D printing features of the classic CREATOR, including the full laser power of 250 W at a spot of 40 µm; laser processing speeds of 3,500 mm/s; and a build platform 110 mm (diameter) with a maximum Z-axis of 100 mm.
OR LASER has also launched its cloud manufacturing services. As Industry 4.0 gathers momentum and digital data becomes increasingly fundamental, AM users need to be able to seamlessly join this revolution. OR LASER's cloud manufacturing capabilities offers users a continuous, connected interface with the machines and data. With multiple functions, this cloud manufacturing service can monitor machines in real time, as well as provide preventative maintenance reports that avoid downtime; provide monitoring and analysis of multiple systems from one location; and provide analytical insight for industrial applications based on the machines parameters and the materials being used.
OR LASER has also launched another hardware system - the ORLAS CUBE -a solution for demanding laser material processing tasks. The ORLAS CUBE is a flexible and fully enclosed system designed to fulfill challenging industrial tasks due to its high-quality and precise axis system combined with a stable and durable granite processing table. The CUBE system's flexibility stems from the fact that it can be utilized with all laser sources and processing heads from OR LASER, which means that it can be deployed as a welding system or as a compact cutting system for a variety of possible applications, including powder cladding applications.
The system is controlled by a modern 10.2" touch display, while machining strategies can be generated directly with the system using the built-in ORLAS SUITE CAM software. Due to the closed machining case, the system fulfills all requirements for laser safety and can therefore be used in a wide range of environmental conditions. The processing case is removable or can be moved to the back of the system for crane loading, which can accommodate the processing of large or palletized workpieces.
For more information contact:
O.R. Lasertechnology Inc.
1420 Howard St.
Elk Grove Village, IL 60007
847-593-5711
sales@or-laser.com
www.or-laser.com
< back