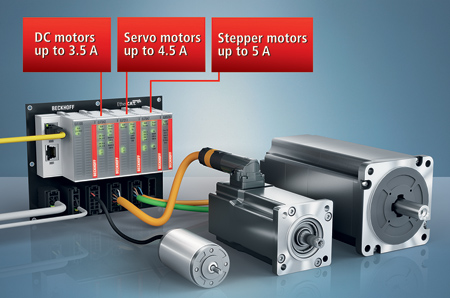
The new EtherCAT plug-in modules for motion applications expand the application spectrum of Beckhoff EJ series I/O in mass-produced machinery.
Beckhoff has introduced new EtherCAT plug-in I/O modules with compact drive technology, which are designed to provide an efficient wiring solution for machines built in large and medium-sized production runs. With new EJ7xxx motion modules, space-saving compact drive technology from Beckhoff is integrated into a plug-in module concept, enabling compact I/O and motion solutions that match customer requirements. These include modules for servo, stepper and DC motor types.
"EJ-series plug-in modules make it easy to implement a platform concept for large-volume production runs without sacrificing customization capabilities," said a company spokesperson. The modules, with electronics based on the EtherCAT I/O system, are directly inserted into an application-specific signal distribution board that transmits signals and power to the individual connectors. Connections via pre-configured cable harnesses replace the expensive installation of individual wires, reducing per-unit costs and minimizing the risk of faulty wiring because the EJ components are clearly coded.
Already available in a bus terminal I/O form factor for years, compact drive technology is now also available from Beckhoff as a plug-in I/O module concept. In combination with a broad portfolio of Beckhoff motors and planetary gear units, three new EJ7xxx EtherCAT plug-in modules now enable especially compact and cost-effective drive solutions.
The EJ7047 stepper motor module was designed for applications in the medium performance range. The device features two inputs for limit switches; the second input can alternatively be configured by the user as an output. This makes it possible to install a holding brake, for example. In conjunction with stepper motors from the Beckhoff AS10xx series, the user can optionally implement vector control, delivering enhanced motion dynamics and reduced power consumption.
The EJ7211-0010 servomotor module features high performance in a compact design. This is, in large part, enabled by the integrated one cable technology (OCT), which combines the motor cable and an absolute feedback system into a single cable. The EtherCAT plug-in module seamlessly integrates with motors from the Beckhoff AM8100 series, offering output current up to 4.5 ARMS. Since the system reads the identification plate of the AM81xx motors electronically, wiring and commissioning efforts are minimized. The fast control technology, based on a field-oriented current and PI speed control system, is suitable for demanding, highly dynamic positioning tasks.
The EJ7342 2-channel DC motor output stage is designed for direct operation of two DC motors, and offers galvanic isolation from the E-bus. Speed and position are set by the automation device via a 16-bit value, so a simple servo axis can be implemented by connecting an incremental encoder.
Integration of the EJ9576 brake chopper module is suitable for dynamic applications and when feeding multiple axes via a single power supply. This protects the system against damage from overvoltage by absorbing part of the energy. If the voltage exceeds the terminal's capacity, it discharges excess energy via a separate external resistor.
For more information contact:
Beckhoff Automation LLC
13130 Dakota Avenue
Savage, MN 55378
877-TwinCAT / 952-890-0000
beckhoff.usa@beckhoff.com
www.beckhoffautomation.com