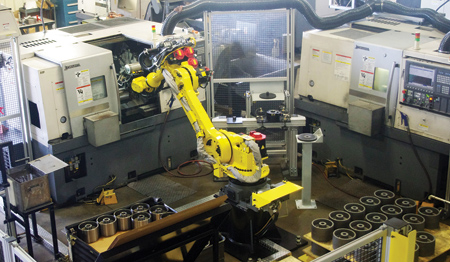
Two Okuma Genos machines are tended by a FANUC robot capable of handling two 37 lb. parts at the same time to optimize throughput.
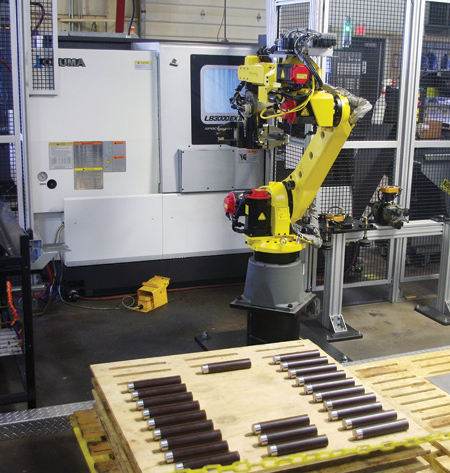
This cell features an Okuma Spaceturn LB-3000 EX Series 2-axis horizontal lathe and a FANUC M20iA/35 6-axis industrial robot.
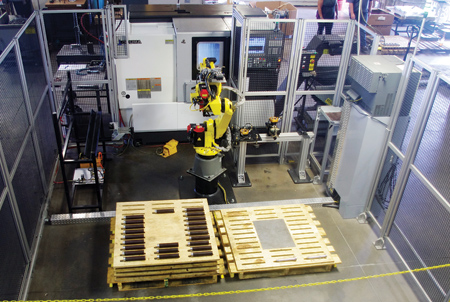
A tool rack located within this cell holds SCHUNK end-of-arm-tools bearing unique identification codes that enable the robot to select the proper gripper.
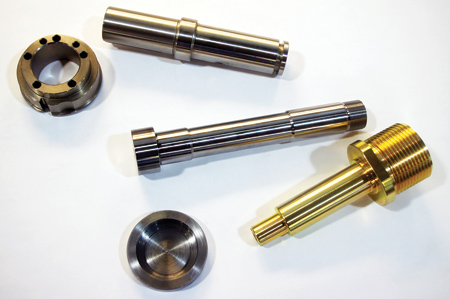
Automating production of these and other parts enables Miller Precision to improve workflow, reduce costs and meet demanding delivery schedules.
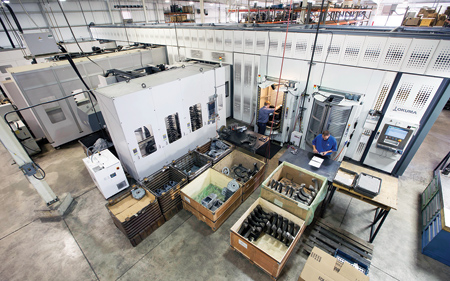
Miller Precision's first venture into manufacturing automation was this FMS designed by Gosiger, Inc. incorporating an Okuma machining center, a FANUC robot and a Fastems pallet container system.
With a population of just over 900, Ottoville, OH, is a quintessential American small town, self-proclaimed as "A strong community with deep roots in tradition." While local CNC shop Miller Precision Mfg. Industries Inc. also has its roots in traditional manufacturing, the company is far from an ordinary job shop. It is, in fact, a full-fledged production facility.
Although comfortably nestled in farm country, the company's two plants are loaded with advanced technology that many big city manufacturers would envy. Along with a sea of CNC machines and machining centers are bar-fed Swiss turning operations, robotic welding stations, laser and water cutting, powder coating and a comprehensive fabrication department.
However impressive the sheer volume of equipment may be, what immediately catches the eye are the various robotically automated work cells. According to company President Jim Miller, "What first prompted us to move into robotic automation was the difficulty we had in finding enough skilled machine operators as our business grew. We knew we needed more than just a worker who could push a few buttons - we needed people who could learn and use the latest machining technologies. We also dealt with some workpieces that were heavy enough to put a strain on our workers and slowed production."
Attending trade shows and seminars allowed Miller and his employees to gain a better understanding of robotic automation. One thing that impressed them was the fact that robotic automation is not just for high volume production, but could also make smaller runs more productive and cost-effective, due in part to quick changeover technology.
The company operates an impressive number of Okuma machines acquired from Dayton, OH, based distributor Gosiger, Inc. "They are a family business, just as we are," said Miller. "We have worked closely together since the early 1990s and have come to know the principals well. So when we first considered automating some of our processes, it made perfect sense to work with their systems integration division, Gosiger Automation."
Many of the parts the company makes are for manufacturers of food processing equipment and lift trucks. Typically, these parts are shafts and pistons, or made from disc-shaped blanks of 300 series stainless steel or 4140 alloy steel. Before Miller automated its processes, the parts were made on a series of individual machines that required a great deal of operator handling along with multiple fixtures and set-ups. Now, one operator manages two automated cells, manual part handling is a thing of the past and set-ups are quicker and easier. As a result, Miller estimates that overall efficiency has improved by 30% or more.
Miller's first foray into automation was in 2009 when he purchased a flexible manufacturing system (FMS) designed by Gosiger Cleveland that incorporated an Okuma machining center with a FANUC robot and a Fastems pallet container system. The FMS exceeded expectations, so in 2012 Miller invested in a second Okuma/Fastems/Gosiger system consisting of four Okuma 500 mm HMCs integrated with a Fastems 56-pallet FMS. Miller uses these systems to machine castings into lift truck transmission housings and industrial pump housings.
More recently, Miller focused on the turning machine side of his operation and added two more automated work cells. "For the first work cell we looked at the various families of parts we produce and decided which ones we wanted to put through the cell," he said. "We chose those parts that have annual volumes of about 1,000 pieces and are run in batches of 250 at a time. We picked two of these part families that could be handled by the same workholding devices."
This cell features an Okuma Spaceturn LB-3000 EX Series 2-axis horizontal lathe and a FANUC M20iA/35 6-axis industrial robot positioned in front of the machine. The robot is equipped with FANUC's 2D iRvision system that enables it to find and identify the correct parts. Workpieces are positioned for the robot on 42" x 42" wooden pallets placed in a steel locating frame with a sheet of plywood between each layer. Another pallet is placed alongside the robot arm to receive finished parts.
A tool rack located within the cell holds the end-of-arm-tools (EOAT) to be used by the robot. Each tool has a unique identification marking so the robot can identify the correct tool and, using a quick-change unit, automatically exchange tools as required. To accommodate the various parts, the cell uses two SCHUNK EOAT: a dual three-jaw gripper and a dual two-jaw gripper. There is also a vacuum tool to remove the plywood separation layers. The dual gripper design enables the robot to hold a raw part in one gripper, unload the finished part from the machine with the empty gripper, rotate and load the raw part into the lathe.
The second cell was designed to deal with a 37 lb. part that the machine operators would rather avoid. The part was being made on two Okuma Genos L-400 single-spindle lathes. To automate the process, Gosiger Automation selected a FANUC R-1000iA/100F 6-axis industrial robot with a reach of 2.23 meters and a payload capacity of 100 kgs. These specs mean that the robot arm is capable of handling two parts at a time to optimize throughput.
Before automating the process, it was a challenge to meet customer delivery dates. Now, in addition to reducing operator touches, improving throughput and eliminating heavy part lifting, Miller can stay ahead of delivery schedules and exceed customer expectations.
According to Miller, "These automated systems not only pay for themselves many times over in improved work flow, they also impress customers who visit our plants. Work cells with robotic automation, multi-axis machine tools, in-process probing for automatic offsets, tool life management and consistent part quality convinces visitors that we are not a small town job shop, but a full service manufacturing company.
"We sent 20 of our 85 people to IMTS this year to see new technologies first-hand. Attending these shows and seminars, finding competent people who can be trained to be automation cell operators and working with dependable equipment providers is what shops like ours need to do to stay competitive."
For more information contact:
Jim Miller, President
Miller Precision Mfg. Industries, Inc.
131 Progressive Drive
Ottoville, OH 45876
419-453-3251
jmiller@millerprecision.com
www.millerprecision.com
Mark Eddy, President
Gosiger Automation
108 McDonough Street
Dayton, OH 45402
877-288-1538
mark.eddy@gosiger.com
www.gosiger.com