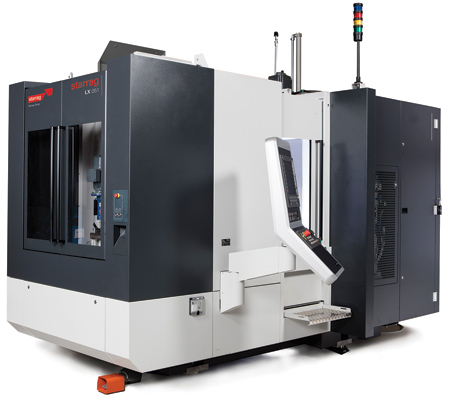
The LX051 5-axis blade machining center is specifically designed for high-precision, efficient machining of turbine blades. Using an innovative flexible fixture concept, machining all types of turbine blades is possible.
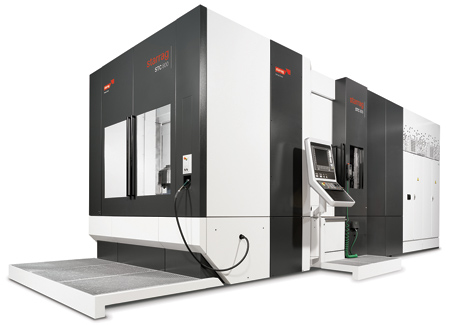
Process capabilities of Starrag's STC 800 include milling, turning, internal machining with an angle head and probe measuring. This 60 kW machine, with a spindle speed of 15,000 RPM and a torque rating of 174 Nm, establishes a benchmark for heavy chip removal of titanium parts.
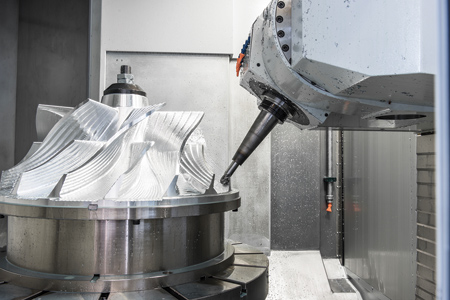
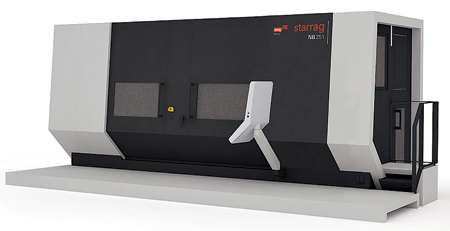
Specifically designed for complete machining of blisks and integrated bladed rotors, the NB 251 machining center provides highly dynamic finishing of flow surfaces in point contact. The NB 251 is capable of handling blisks up to a maximum diameter of 30.7".
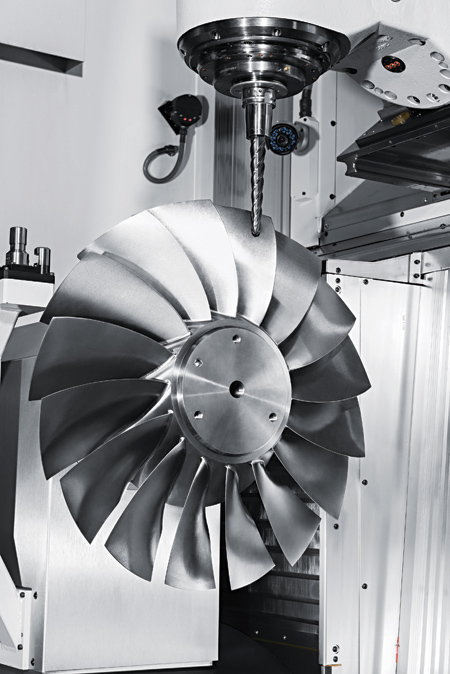
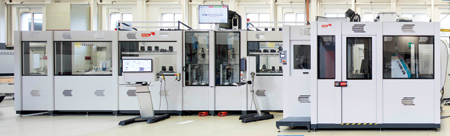
Two cells being integrated into Starrag's latest FMS system modules. The range of turn-key technology covers every aspect of the customer's requirements, from the engineering design and responsibility for delivering and assembly of all system modules, to operator training and production assistance and service.
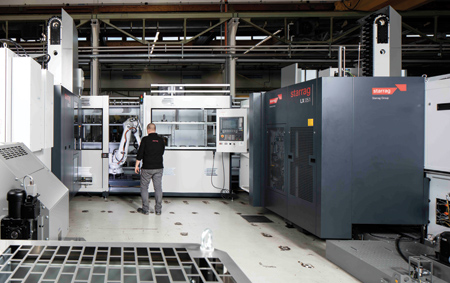
Starrag AG has developed an advanced product portfolio to meet the challenges of the aerospace industry. At Starrag AG's Turbine Technology Days in Rorschacherberg, Switzerland, aerospace manufacturers and suppliers had the opportunity to witness firsthand the company's latest manufacturing technology advancements.
"Starrag starts by understanding the customer process requirements, and then develops the optimal solution to fit the customer's needs," said a company spokesperson. "As such, Starrag strives to be a true technological partner with its customers."
"Strategies, tools, cutting conditions and fixtures are constantly evaluated and improved under Starrag's supervision," continued the spokesperson. Every detail is taken into account." For example, special workpiece geometries create specific demands on the clamping fixture. To meet the specific requirements of these workpieces, Starrag provides in-house specialists to develop individual clamping concepts to meet these requirements.
Additionally, Starrag designs and builds part-specific tooling engineered to significantly increase productivity and lower cost per part. Working directly with the customer, application engineers will design and produce tools based on customer requirements. Furthermore, tools can be reconditioned and coated through Oerlikon Balzers throughout the world.
Attendees also witnessed firsthand that when coupled with machine tools, Starrag Adaptive Machining software provides the capability to machine and blend 3-D components and features automatically, where geometrical differences exist between components. This application is useful when machining castings and forgings that have inherent variation, parts subject to deformation from heat cycling, or wear and tear caused during the actual operation.
Starrag designs and builds machine tools for the aerospace industry under the premise that the machining of titanium and other hard materials requires a systematic approach in order to lower production costs and improve quality. "While Starrag understands the trends toward producing larger and more complex parts, the machine tool builder also sees higher metal removal rates, longer tool life and lower production costs as key factors in developing machine tools to meet the challenges facing today's aerospace industry," said the spokesperson.
"Building on its core competence, Starrag has placed its in-depth knowledge and decades of experience at the forefront of developing process stability, leading to a balanced machine design," continued the spokesperson. "For example, efficient titanium cutting requires the best available operation strategy employing machine tools, cutting tools and coolant systems. Starrag continuously works on all these levels to locate and improve limiting factors. Machine tools are then built to benefit the full potential of these operation strategies."
LX051 5-Axis Blade Machining Center
From the machining of aluminum to the machining of titanium and other advanced materials, such as nickel-based alloys, many machines were on display at Turbine Technology Days. One machine tool gaining the attention of attendees was the Starrag LX051 5-axis blade machining center. Specifically designed for high-precision, efficient 5-axis machining of turbine blades, it maintains a 25.6" stroke in both the X- and Y-axis and a 26.8" stroke in the Z-axis. The rapid traverse speed of 2,441 IPM is extremely quick.
The ultra-modern machining platform is the result of decades of experience in the development of machine tools, CAM systems and special tools combined with in-house expertise in the prototype and series production of turbine blades. A comprehensive integrated solution is centered on the machining system via the specially developed CAM system through to the integration of process monitoring systems. In addition, machining of all types of blades with one jig is possible due to an innovative flexible fixture concept.
The implementation of robot handling on the LX051 HMC provides automated loading and unloading of 40 blades up to 15.75". This extends unmanned operation time up to 10 hours.
STC 800 5-Axis Machining Center
The STC 800 5-axis machining center also generated a great deal of attention. Designed to provide a reduction in cost per unit in the machining of structural parts, multi-blades and casings with long cycle times, this machining center has state-of-the-art static and dynamic properties as well as a rugged and tested rotatable head.
The working area of the STC 800 with a 57.1" linear travel in the X-axis, vertical travel of the main spindle of 47.2" in the Y-axis, 51.2" table travel in the Z-axis and a swing diameter of 55.1" provides ample capacity. In addition, machining wall thicknesses down to 0.196" is characteristic of the STC. "Add to this a maximum workpiece weight of 5,512 lbs. and it becomes obvious that the STC stands as a benchmark for heavy chip removal of titanium and Inconel parts in the aerospace industry," said the spokesperson.
The STC 800 is a 60 kW machine with a spindle speed of 15,000 RPM and a torque rating of 174 Nm. Process capabilities of this machine include milling, turning, internal machining with an angle head and probe measuring. This allows parts such as an aerospace engine casing to be completely machined on one machining center with a reduced number of set-ups, which equates to lead time savings.
NB 251 5-Axis Blisk Machining Center
Starrag's NB 251 machining center is specifically designed for complete machining of blisks and integrated bladed rotors. From efficient roughing of solid material and adaptive machining of friction-welded blisks, the NB251 provides highly dynamic finishing of flow surfaces in point contact.
Capable of handling blisks up to a maximum diameter of 30.7", the machine travel in the X-axis is 27.6" and in the Y- and Z-axis the travel reaches 15.7". In addition, the NB 251 features an angled B-axis on which the tool is practically rotated around the tool center point.
When the rocker swivels, machines with a swivel rotary table automatically brake due to the extremely long compensating movements. These compensating movements are necessary to ensure the tool remains on the same machining point. Starrag points out that with the tip of the tool located very close to the center of rotation, the compensating movements of the axes are five times shorter, which means up to 25% shorter cycle times are achievable.
End users can achieve additional increases in productivity and efficiency by employing the NB 252. This machine is equipped with two spindles. This second spindle equates to two machines on a single tool bed, which allows for two completely different workpieces to be machined independently of each other. The option of two spindles generates a significant increase in productivity while lowering investment costs per work spindle.
Flexible Manufacturing Systems (FMS)
Starrag's expertise at developing flexible manufacturing systems (FMS) is based on 20 years of hands-on experience (know-how). "This experience has brought it to the forefront of designing and building FMS solutions. In turn, the company is now considered to be a prime integrator of FMS throughout the world," said the spokesperson.
Interlinking various machine designs permits complex production processes to reduce unit costs of lot sizes, from one-offs to large quantities. The range of turn-key technology covers every aspect of the project, from the engineering, delivery and assembly of all system modules. Also included are user training systems, production assistance and service.
Highlighted at Turbine Technology Days was the versatility of FMS, with a number of systems being illustrated. For example, machining precision forged compressor blades at a production capacity of 40,000 blades per year with parallel operations for seven different types of precision forged turbine blades held attendees' attention at length. This particular FMS included integrated inspection and marking, two tool grinding machine stations, as well as tool presetting and tool shrinkage stations.
An FMS for the machining of oversized forged guide vanes with a production capacity of 35,000 vanes per year and maintaining the capability of a parallel operation of four different types of oversized forged guide vanes was also illustrated in detail. This particular FMS included two polishing cells, integrated inspection and marking, along with tool presetters and tool shrinking stations.
For machining turbine blades from bar stock, an FMS with a production capacity of 25,000 blades per year and the capability to handle a parallel operation of three different types of turbine blades was also illustrated. This particular FMS also included automated fixture set-up.
Starrag Dengeling
Last but not least, using a machine tool, Starrag demonstrated the micro-forging process, which eliminates post-machining of turbine blades in any form. This micro-forging method of finishing replaces conventional polishing, friction grinding and shot peening with a single process.
During machining, a tungsten carbide ball oscillating axially at high frequencies (up to 600 Hz) smooths the surface. The resulting kinetic energy causes deformation on impact, which leads to residual compressive stress in the surface layers up to a depth of 0.3937".
Initial tests show that the process is significantly more precise and more controlled than the use of the shot-blasting method.
The Starrag Group manufacturers high-precision machine tools for milling, turning, boring and grinding workpieces made from metallic, composite and ceramic materials. Principle customers are internationally active companies in the aerospace and energy, transportation and industrial components, and precision engineering sectors. In addition, the Starrag Group provides integrated technology and maintenance services designed to significantly improve customer productivity.
Specialists from the Group work with customers to jointly develop the ideal solution for the relevant machine task. Whether an individual machine or a system solution, every machine can be adapted in line with customer requirements.
For more information contact:
Starrag USA Inc.
North American Headquarters
Skyport Business Park
2379 Progress Drive
Hebron, KY 41048
859-534-5201
ussales@starrag.com
www.starrag.com