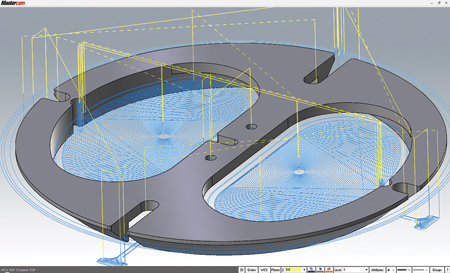
In recent years, 3D-Machine has upped its game to become even more responsive to customers by exploring and exploiting some of the advanced features of its Mastercam CAD/CAM software. Most notable of these features is Mastercam's Dynamic Motion technology, which maintains a constant optimal chipload on the cutting tool, allowing 3D-Machine to take on more challenging parts, while improving material removal rates and reducing cutting tool wear.
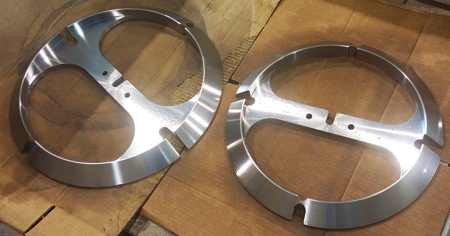
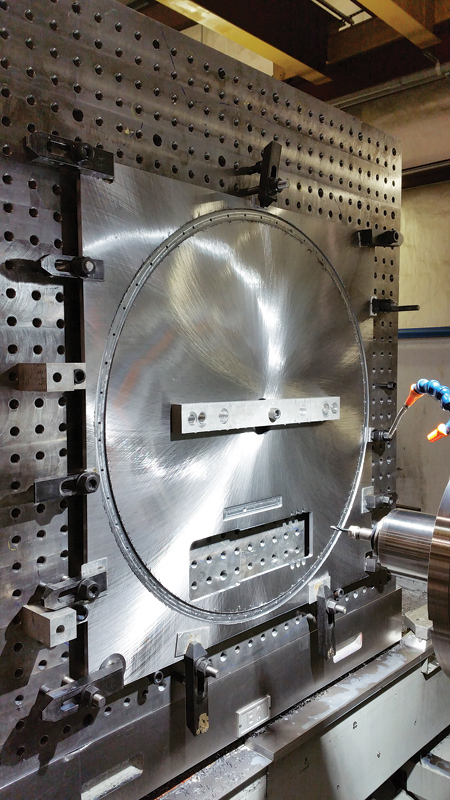
Parts that require a large window to be cut in a thick plate present a problem for horizontal CNCs. The dropping steel could potentially break the tool, hit the spindle, damage the way cover or scrap the part. Roberts handles this problem dynamically instead. He said, "Although we are limited on RPMs, we are able to use Dynamic milling to make chips out of the pocket instead of trying to cut the window out as a drop. Even if the plates are an inch thick or more, Dynamic milling tool paths are a great help in these situations."
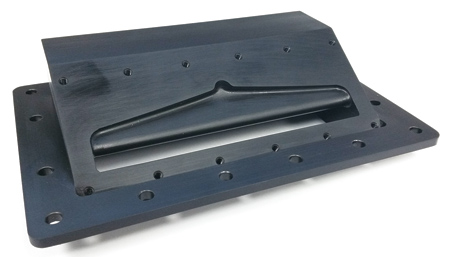
3D-Machine has built a reputation as a go-to shop for critical components such the ones shown here. Tools within this shop's Mastercam CAD/CAM software are helping reduce lead times for demanding customers who need work completed in a hurry.
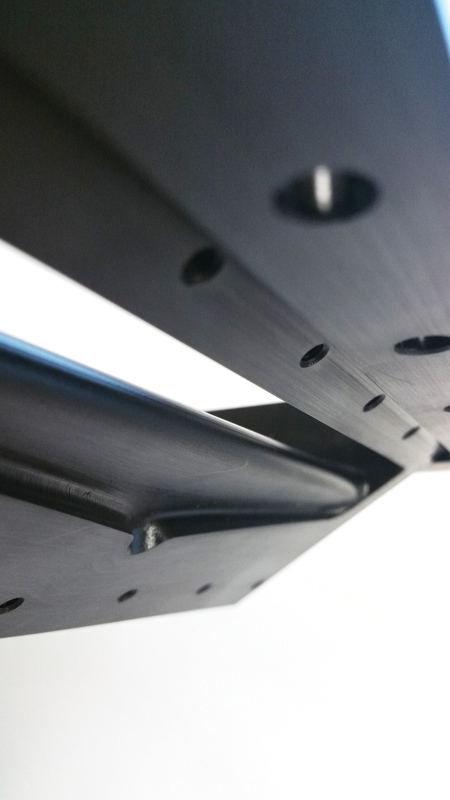
Sam Roberts spent the first 10 years of his machining career working with manual machines. It was shortly after he discovered the benefits of CAM software - and the fact that he could purchase a Haas machine very economically - that Roberts decided to open 3D-Machine, Inc.
That was in April 2001, and since then, Roberts has built a reputation as the go-to guy for machining and quick delivery of large, complex precision parts - jobs that other shops either will not or cannot do. This has proven to be a very attractive proposition in the energy industry where customers frequently need fast, or at least reasonable, delivery times for precision replacement parts, especially steam valves, which take a beating over time due to the high temperatures they must endure.
In recent years, 3D-Machine has upped its game to become even more responsive to these customers by exploring and exploiting some of the advanced features of its software, Mastercam CAD/CAM software from CNC Software, Inc. Most notable of these features is Mastercam's Dynamic Motion technology, which maintains a constant optimal chip load on the cutting tool, allowing 3D-Machine to take on more challenging parts, while improving material removal rates and reducing cutting tool wear.
Overcoming Resistance to Change
When Dynamic Motion technology was first introduced, Roberts was resistant to exploring its potential benefits despite repeated prodding from his reseller, CAD/CAM Solutions. However, once he witnessed this roughing strategy in person, Roberts was hooked. "When you see an end mill going at 150 IPM on 4140 and throwing chips everywhere, whittling the part down to where it is supposed to be, it is just amazing," he said.
When the flute length of a carbide end mill is fully engaged, tool paths incorporating Dynamic Motion technology adapt to material conditions ahead of the tool for the most efficient cuts possible, without burying the cutter. Retracts are minimal, just enough for the cutter to reposition itself when it comes up to a wall, significantly reducing air cutting and allowing for continuous machining. Because programs execute "microlifts" - just 0.005" to 0.010" - when changing position, cutting tools do not "scrub" the floor, causing the friction-generated heat that can cause cracks and premature wear on their surface.
Roberts recalled a job where he was able to cut windows into an 80" diameter A36 plate disc using a Newland NVT 2000 double-column vertical turning center with full C-axis contouring. By creating a new tool path for this application, he was able to achieve a 1.70" length of cut at 1,950 RPM. Chips were flying so fast that the material removal system could not handle them. The operator eventually had to shovel them out of the cutting chamber.
In another instance, Roberts created a tool path featuring a long pocket that, as he noted, would normally take an aggressive shallow cut and "burn up an end mill or two." They switched to Dynamic Motion using a 5/8 end mill, a very shallow step over with a 1.480" depth, and there was very little wear on the tool.
Multiple Economies
By using an end mill's entire flute length as often as possible, 3D-Machine saved tens of thousands of dollars by extending the life of its cutting tools. Shrink fit toolholders grab the cutting tool securely and lower lateral forces allow for very high material removal rates, so Roberts does not need to worry about the part moving in the vise, even during very rapid roughing operations. These factors, in combination with the fact that tools have to be changed far less often, have improved the company's scrap rate.
By improving material removal rates across a broad range of CNC equipment with Dynamic Motion technology, 3D-Machine is able to postpone the need to purchase new equipment. Roberts was also surprised to discover that Dynamic tool paths have made it possible to optimize programs on its existing older milling machines - some of which are more than 10 years old. On some of these machines, code is posted via floppy disks that have very limited memory capacity. This has not been a problem since Roberts can significantly shrink the amount of code in a CNC program by as much as 50% by simply initiating Mastercam's filtering function.
"My thinking about CNC equipment tended to be old school - that you have got to have heavy duty machines to get these jobs done," said Roberts. "However, we have seen these Dynamic tool paths eliminate the absolute need for some of the heavy machines. With faster Dynamic material removal rates, these lighter machines give us higher material removal rates that do not push the machine."
Energy to Grow
While 3D-Machine continues to look for new customers in a variety of industries, energy continues to be its main source of business and the company is looking for ways to be even more responsive to needs. The company maintains a database of programs filled with repeat parts that are machined for these customers. In many cases, the existing programs can help 3D-Machine turn jobs around within days. In other cases, they can serve by creating Mastercam programs for similar parts.
Still, Roberts pointed out, most of the time programs are created from scratch with turnaround times falling within the two-week range with three to four weeks being typical. The company will also not hesitate to take on emergency jobs.
Roberts hopes to further reduce turnaround times by building up his tool library. "It will be nice to have all of the information there so that when you click on a tool it will find the right length of cut and angles, radius and other information," said Roberts. The company is also looking to add more programmers to the roster to improve machine utilization and reduce lead times.
Roberts considers his CAM software "one of the better tools in the shop - like a good end mill." The advanced manufacturing concepts facilitated by its CAD/CAM software have enabled 3D-Machine to grow from a small shop with a single, relatively inexpensive machine and one person, to one with 20 CNC machines and 20 employees in 2015. That is twice the size Roberts ever thought possible in those early years. Considering the fact that the shop sits on four acres, there is plenty of room to expand as business grows.
For more information contact:
Sam Roberts, President / Owner
3D-Machine, Inc.
4073 Fambrough Drive, Bldg. 100
Powder Springs, GA 30127
770-222-4918
s.roberts@3d-machine.com
www.3d-machine.com
CNC Software, Inc.
671 Old Post Road
Tolland, CT 06084
info@mastercam.com
www.mastercam.com
SOUTHEAST ONLY
CAD/CAM Solutions
2336 Wisteria Drive, Suite 520
Snellville, GA 30078
770-982-3400
www.cadcamsolutions.net