
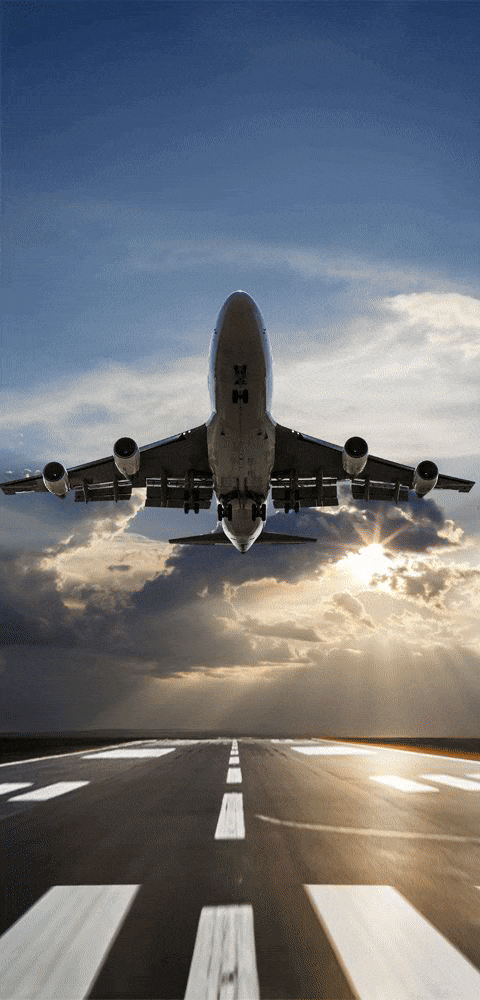
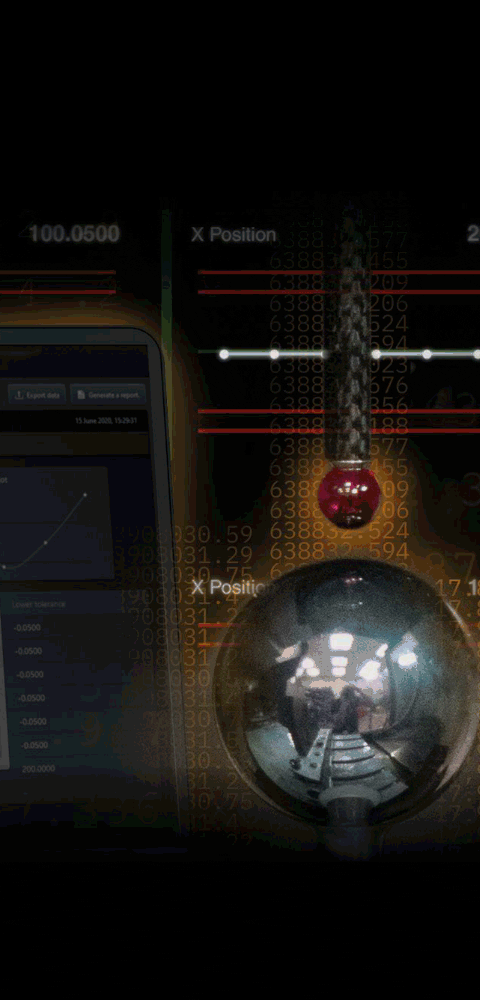
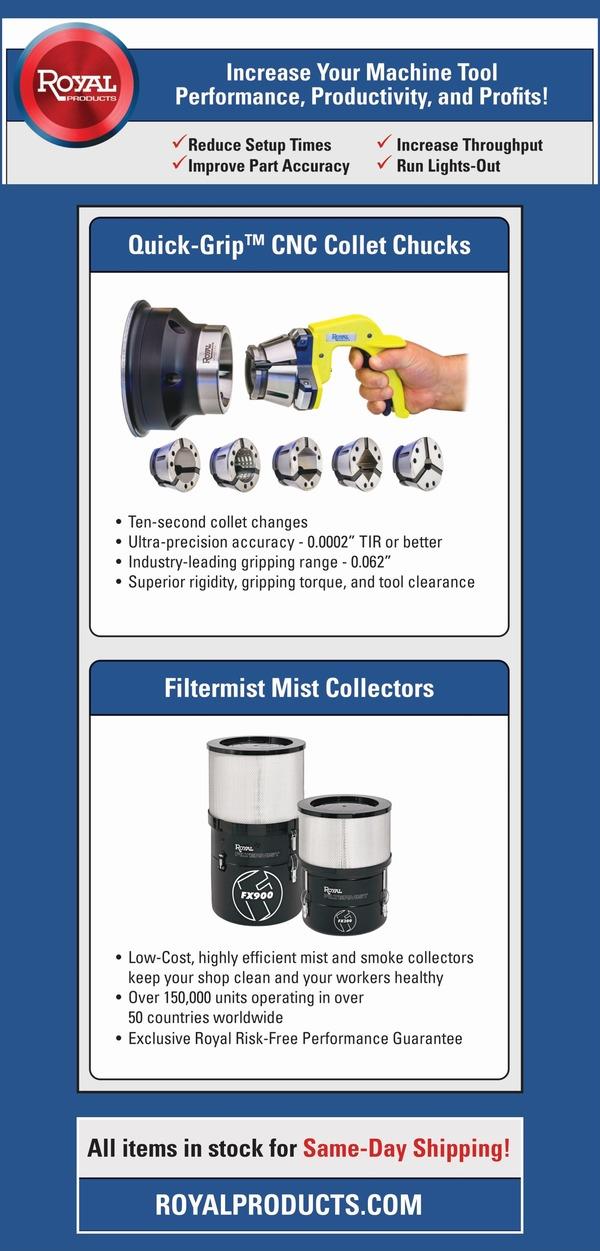
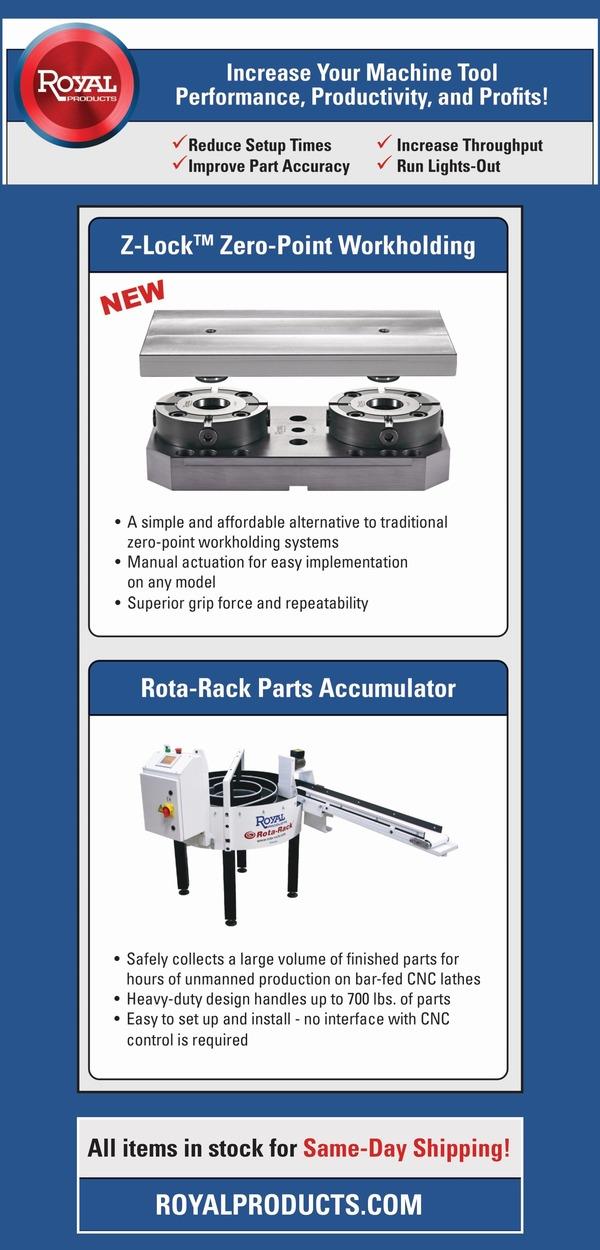

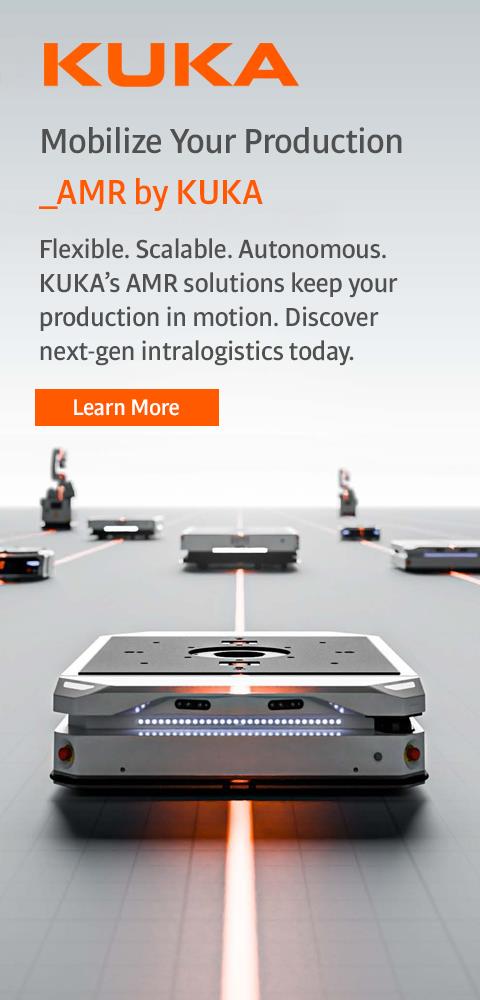
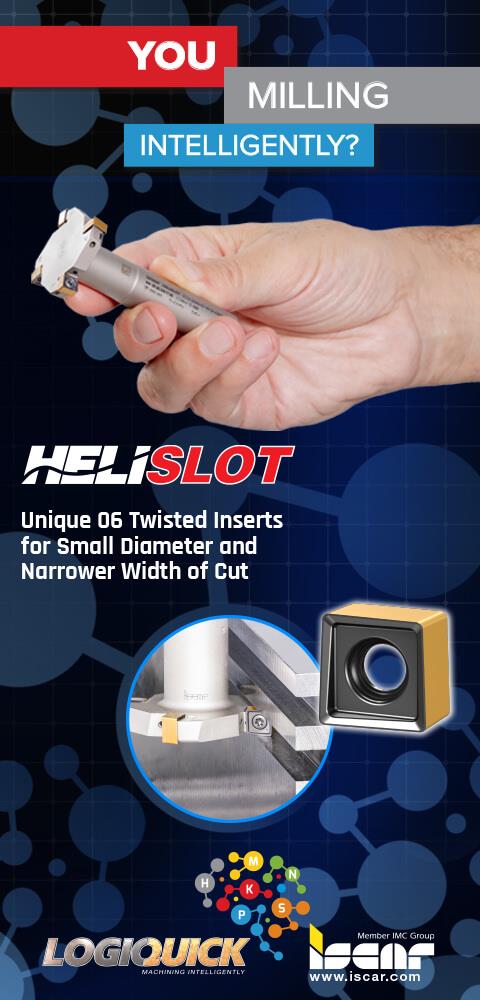
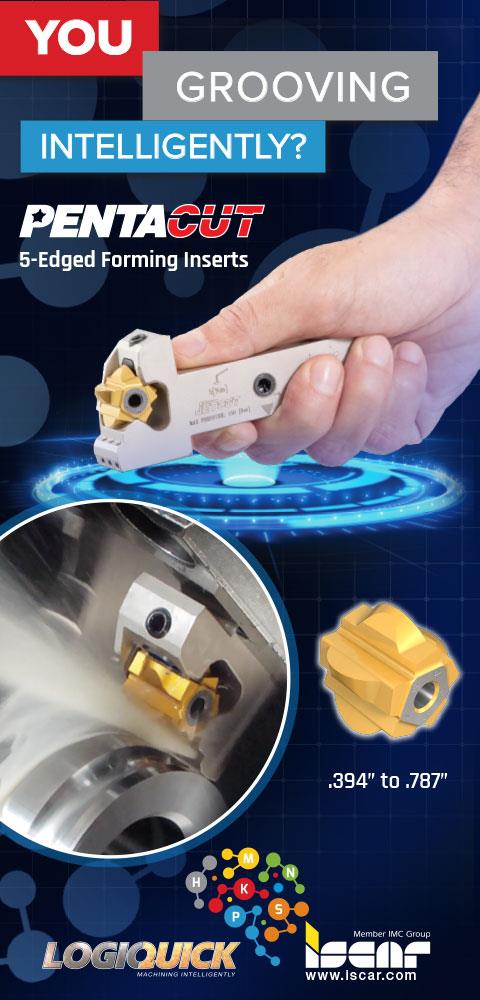
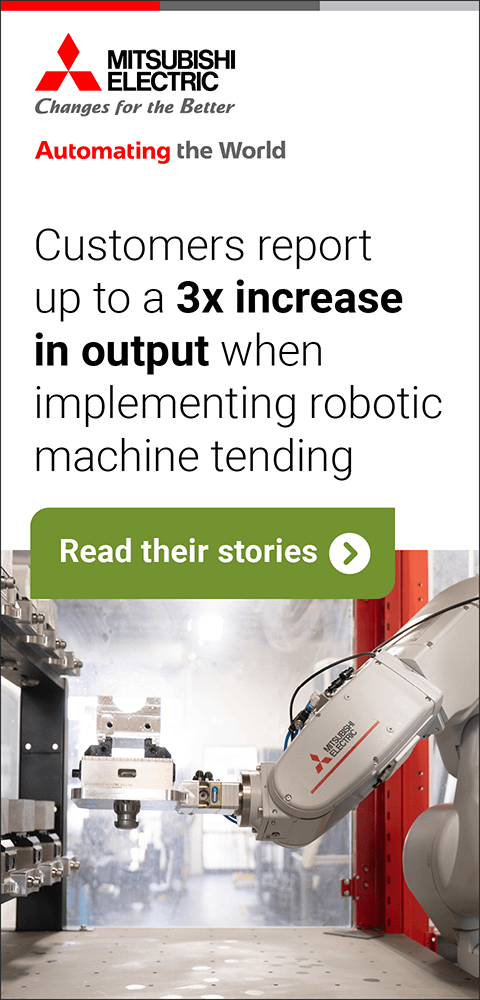
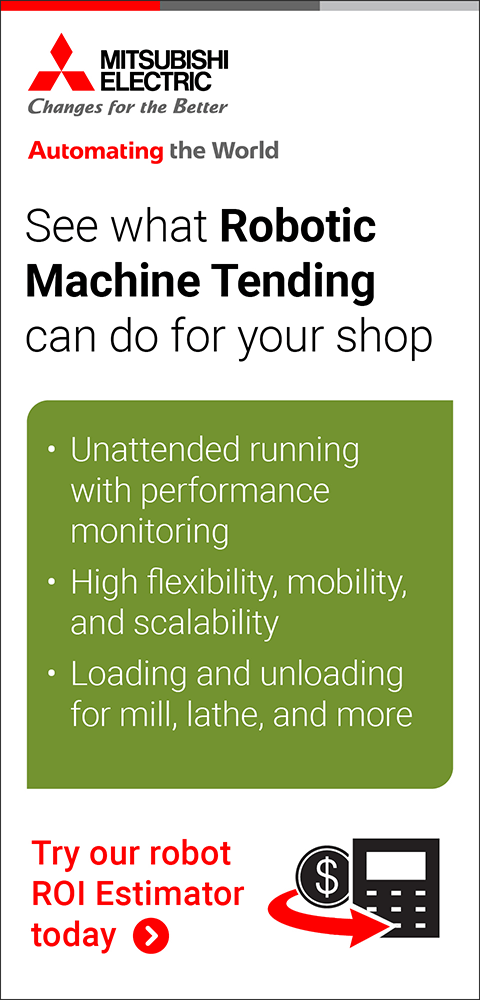
Edgecam, SURFCAM and Radan at SolidWorks 2014
January 23, 2014During SolidWorks 2014, attendees will be able to witness all of the recent enhancements to Edgecam, SURFCAM and sheet metal specialists Radan Software in booth #407. Visitors will also see how all three software solutions provide a seamless integration with SolidWorks 3D mechanical design software.
Edgecam
Edgecam Workflow is designed to reduce costs and improve quality while achieving shorter lead times. Workflow understands the component topology and the required manufacturing environment, therefore accelerating toolpath generation.
Edgecam Workflow has an intuitive method for creating NC code, which focuses on ease-of-use while using a familiar ribbon interface. The Guided Automation accomplishes the tasks of Part Setup, Analysis, Feature Creation, Manufacture and Deployment.
Edgecam Workflow is designed to shorten programming time, and since it is simple to operate, the learning curve for new users is reduced.
SURFCAM
SURFCAM's associativity with SolidWorks enables NC programmers to open native SolidWorks 2014 files directly into SURFCAM, eliminating the translation process. When changes are made to the SolidWorks design models, SURFCAM automatically recognizes the design revisions and offers to regenerate the affected toolpaths within SURFCAM's Operations Manager. With this interoperability between the two systems, SURFCAM programmers can quickly adapt to SolidWorks design changes and efficiently update their programming environment.
SURFCAM 2014 R1, the newest release, includes Adaptive Roughing Technology as well as multiple enhancements designed to deliver additional ease of use and control in Masking, Chaining, Operations Manager and Layering functionality. In addition, end users will receive updated and additional CAD translators, postprocessors and editNC at no additional cost. SURFCAM 2014 R1 supports SolidWorks 2014 parts, assemblies, sketches and configurations.
Radan
Radan 2014 adopts the same common cutting strategy for punch presses as that used for profiling machines. It allows for common cut nests to be created automatically, meaning the user can choose, for example, how many parts form a common cut cluster of parts, reducing the sheet's instability. Tagging for common cut parts has also been improved.
3d Workflow and Nest Projects have also been improved, allowing the user to get from a 3D assembly to a nest projects within a couple of clicks, providing graphical and interactive help when necessary. The user is informed when a part is not closed, when tooling is out of date, or what improvements are needed.
For more information contact:
Vero USA Inc.
2000 Town Center
Suite 1730
Southfield, MI 48075
248-869-4040
info@verosoftware.com
www.verosoftware.com
SolidWorks 2014 Booth #407
< back