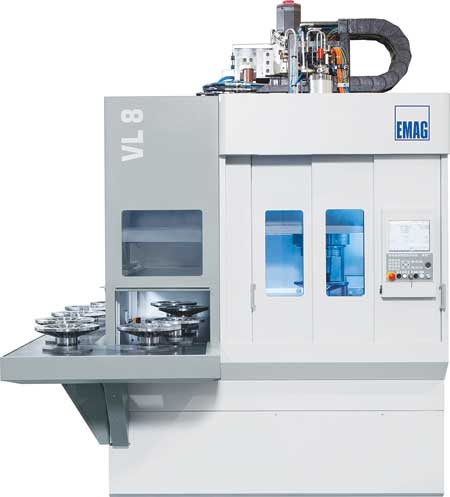
The VL 8 vertical turning center allows for machining of large workpieces, such as components for semi-truck powertrains.
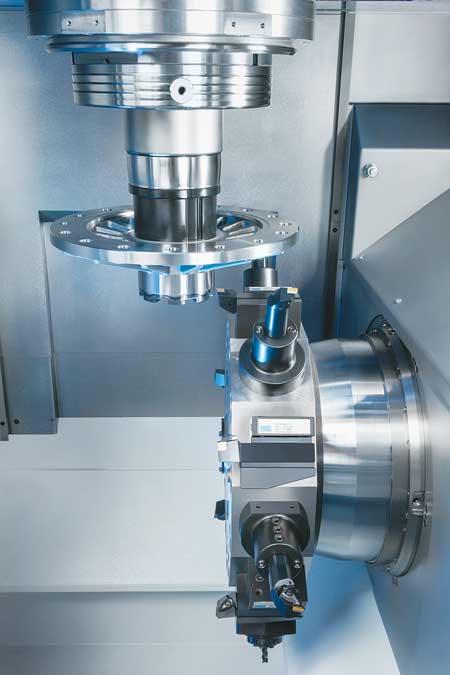
Up to 12 turning or, optionally, 12 driven drilling and milling tools allow for the application of a variety of machining processes in a single set-up.
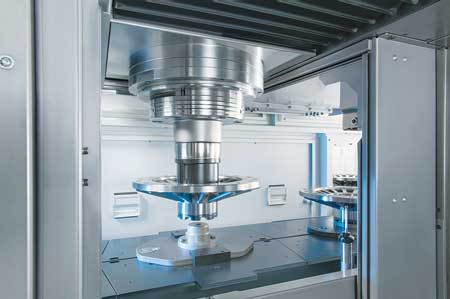
Workpieces are transported to the pick-up station in flexible carrier prisms mounted on the conveyor belt, making resetting efforts to accommodate workpiece diameter changes minimal.
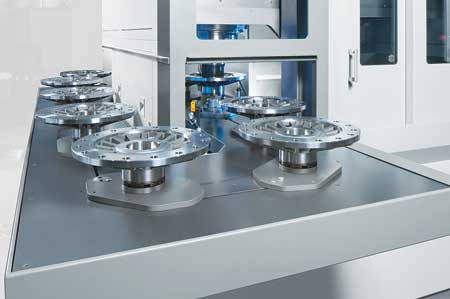
EMAG offers its VL 8 vertical pick-up turning machine for workpieces up to 400 mm diameter. According to the company, it is a highly efficient solution for the production of commercial vehicle components.
"The manufacturing of especially large and heavy components (for instance, for the powertrain of semi-trucks, excavators or buses) poses a unique set of challenges," said a company spokesperson. "How can a large clamped component be machined economically and, at the same time, with high precision? How does the demanding task of handling such components not result in an unmanageably long production process? The VL 8 vertical pick-up turning machine provides the solutions to these challenges. All the advantages of the VL series have been transferred directly to a machine specially designed for the handling of large components, where a number of different turning and milling operations are carried out within the framework of a single closed-loop production process. Integrated automation provides quicker production times, and the vertical layout a high degree of process integrity where chip flow causes no problem. Subcontractors and component suppliers benefit from short idle times and high component quality.
"Sturdy machine construction, dynamic axes and simple operation are the main characteristics of the VL series. They are also based on a completely new machine concept that allows for a variety of production technologies for soft and hard machining to be combined. The following major components ensure a highly efficient production process on the VL:
- A machine base of the polymer concrete MINERALIT to help provide vibration resistant processes for enhanced tool life and machining quality
- The front of the machine base features a compound slide carrying the vertical main spindle that dynamically traverses the Z and X axes
- With a chuck diameter of 500 mm, the pick-up spindle accepts workpieces up to 400 mm diameter
- The machining process uses a main spindle with 60 kW rating, torque of up to 1,220 Nm and speeds of up to 2,850 RPM
- The turret accommodates 12 turning or, optionally, 12 driven drilling and milling tools
- The workpieces are loaded into the carrier prisms of a conveyor belt and positioned via NC axis.
The pick-up spindle collects the workpieces from the lateral conveyor belt and takes them to the machining area. Short travel distance help ensure minimal chip-to-chip times. A flexible machining process allows for the use of a large variety of tools. It is also possible to link up two machines and a component turnover station to create a flexible production cell - to completely machine the first and second sides of a workpiece in one cycle, for example. Additionally, the integration of a Y-axis in the turret allows for the off-center machining of more complex geometries.
"Other features have been developed to ensure precision during the machining process," said the spokesperson. "The spindle, for example, where short distances between the bearings, the use of high-precision separable bearings in a tandem-O-tandem arrangement and support bearings with length compensation at the spindle end provide for a particularly sturdy construction - an important basic condition for micrometer-precision turning processes. Precision is maintained through the integration of an inspection process into the cycle sequence. The required probe is installed outside the machining area and checks the workpiece while it is still clamped. Any corrective data is sent to the CNC control and the process is adjusted accordingly. This guarantees consistently high precision even during automatic operation. All service units are easily accessible and, with an operator to turret distance of just 400 mm, tool changes are quick and easy.
For more information contact:
Peter Loetzner
EMAG LLC
38800 Grand River Avenue
Farmington Hills, MI 48335
248-477-7440
info@usa.emag.com
www.emag.com
Southwest
AR
Ken Pope
EMAG LLC
38800 Grand River Avenue
Farmington Hills, MI 48335
615-308-7170
www.emag.com
TX, OK, LA
David Harris
EMAG LLC
248-755-9167
Southeast
Ken Pope
EMAG LLC
38800 Grand River Avenue
Farmington Hills, MI 48335
615-308-7170
www.emag.com
Northeast
PA, OH, IN
Kirk Stewart
EMAG LLC
38800 Grand River Avenue
Farmington Hills, MI 48335
www.emag.com
NH, VT, MA, RI, CT, NJ, DE, MD, NY, PA
Jonathon Chomicz
EMAG LLC
248-497-8526
www.emag.com
WV
Ken Pope
EMAG LLC
615-308-7170
Midwest
IN, OH
Kirk Stewart
EMAG LLC
248-996-4703
ND, SD, NE, KS, MN, IA, MO, WI, IL
Bill Konetski
EMAG LLC
612-804-0857
KY
Ken Pope
EMAG LLC
615-308-7170
MI
Rob Nash
EMAG LLC
38800 Grand River Avenue
Farmington Hills, MI 48335
248-755-4290
www.emag.com