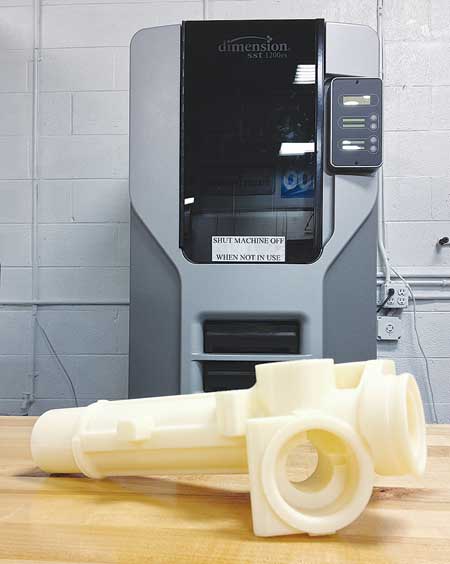
With the purchase of a Stratasys Dimension 1200ES, James Tool has incorporated 3D printing technology into the engineer and build phases of workholding devices and other products. The process involves the incremental build-up of ABS plastic material to produce a representative part used for production evaluation, sales presentations and possible engineering modifications.
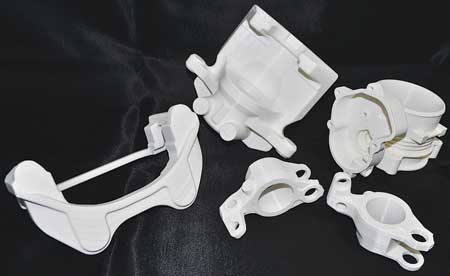
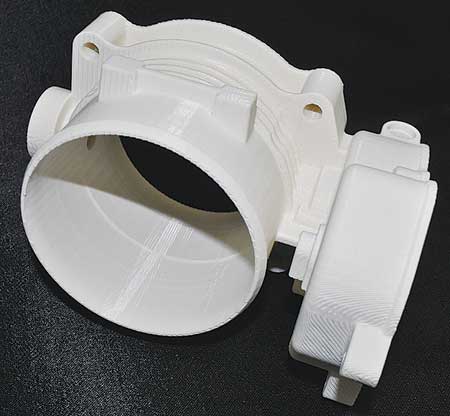
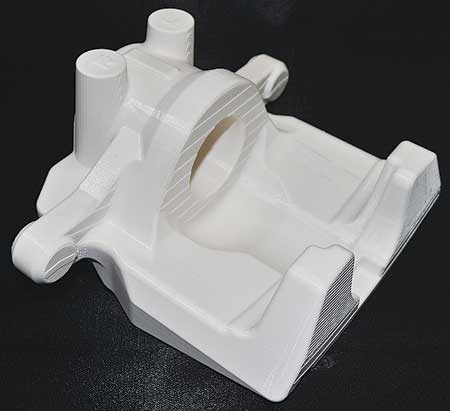
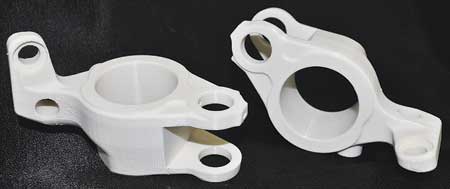
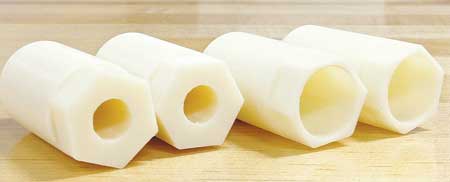
Examples of 3D printed prototypes created on the Stratasys machine directly from the CAD files.
James Tool engineers and manufactures a wide variety of hydraulic workholding devices used in aerospace, automotive and other high-precision industries. Because of the continuous custom work, the company keeps abreast of technological developments in the engineering and production of its products. To that end, James Tool recently installed a 3D printer in its Engineer & Build Hydraulic Workholding Division.
"We started seeing 3D printing make an impact some years ago," said Jeff Toner, President of James Tool. "We waited until the technology had evolved and become more affordable before making our initial investment." The first machine was purchased early 2013 and is currently used to support the company's workholding division, as well as help in the estimating of other CNC machining opportunities. The printer, a Stratasys Dimension 1200ES, has the capability of running parts with a 10" x 10" x 12" envelope in an ABS plastic substrate.
3D printing is a form of additive manufacturing, in which material is built up, one layer at a time, to create a 3D solid working model from a CAD file. It is referenced as additive manufacturing to distinguish it from the subtractive process of traditional machining, in which material is removed from the surface of a blank workpiece. James Tool engineers believe this technology is substantially changing the way the company can serve its customers.
"We were up and running parts within two hours after the installation and set-up," said Toner. "This included the initial calibration on the machine and training from the local technician. Since we utilized 3D imaging in our CAD designs for over 15 years, the transition to 3D printing was practically seamless. The 3D printing image gives our engineers a cleaner concept and enables a much more robust design process, as we can see clamping tabs, locating pins and the entire work envelope more clearly. This results in an easy-to-use, cost effective tool, plus we have significantly shorter times for quote and order-to-first part sequencing. 3D printing has already reduced engineering and quoting time substantially for workholding fixtures and CNC production jobs." James Tool runs roughly an equivalent amount of work in production and one-off or short run jobs.
"While the interaction between James Tool and its customers has not changed substantially, it is quite helpful to have an actual part generated through the 3D printing process before engineering and quoting begin," said Tim King, James Tool Vice President and General Manager. "When you can go into a meeting with an actual part in hand, it can help in many ways. We or the customer can often see desirable changes that might make the component function more effectively, be easier to machine or both. We have already secured our first customer orders by using this system, and the results have exceeded expectations."
"We do not always get a part to study when quoting custom hydraulic workholding. We do almost always get a 3D digital model," said Toner. "Having a part in hand while brainstorming a fixture concept is invaluable. We quote many production CNC opportunities. Having a representative part in hand has allowed us to see features that require special tools or additional processes. It is a time saver.
"I anticipate that, in the future, actual production parts will be printed rather than machined using conventional methods on a large number of the jobs we handle. The future of 3D manufacturing is really limitless. Anyone can now order a desktop 3D printer for his or her business or home office and, once they master the system, have a 3D prototype part in less than a few hours. I anticipate this technology will revolutionize manufacturing and create a new breed of entrepreneurs in our industry. As additive manufacturing grows and becomes more cost effective to manufacture production parts, we want to be very familiar and poised to enter the production additive manufacturing arena."
In its ongoing effort to maintain a quality workforce, the company maintains a full training facility on its Morganton, NC, campus, which has recently expanded to house more machining, finishing, quality lab and large workpiece handling equipment. James Tool actively trains many of its employees in cross-functional machining operations in order to make the company more flexible and capable for its customers.
James Tool provides quality precision machining services in three primary areas:
- CNC production machining
- CNC non-production machining
- Engineering and building of hydraulic workholding devices.
"The ultimate goal of all our efforts and teamwork is to meet customer requirements through our commitment to continual improvement," said Toner.
James Tool was founded in 1987 by James "Bud" Toner. Jeff Toner has been in the manufacturing business for over 30 years. James Tool customers include major OEMs and suppliers to aerospace, automotive, off-highway, energy, nuclear and transportation industries.
For more information contact:
Kevin Moses or Jeff Toner
James Tool Machine & Engineering, Inc.
130 Reep Drive
Morganton, NC 28655
828-584-8722
sales@jamestool.com
www.jamestool.com
Stratasys, Inc.
7665 Commerce Way
Eden Prairie, MN 55344
800-937-3010 / 952-937-3000
info@stratasys.com
www.stratasys.com