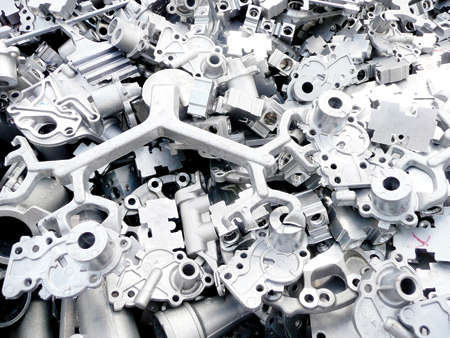
The handling of bulky sprue and runners, punch burrs and defective workpieces is a problem not only in zinc die casting, but also across the board in many light and non-ferrous metal foundries, which impairs the optimum process flow and thus the efficiency of production.
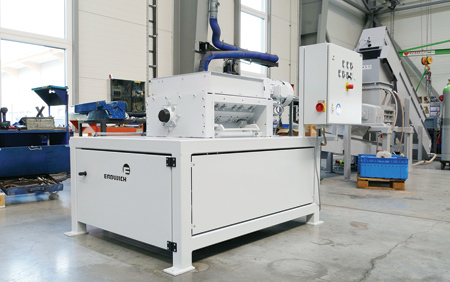
The M600/1 single-shaft shredder has been designed for die-cast parts weighing up to 2 kg and is available in two cutting gear sizes - 400 x 500 mm or 600 x 500 mm length and width - depending on requirements, as well as with a drive power of between 5.5 and 9.2 kW.
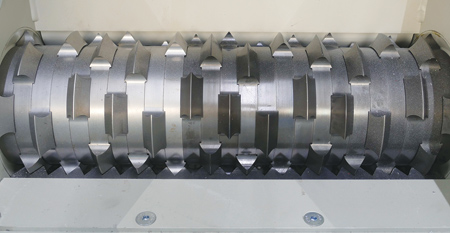
The M600/1 works according to the rotor-stator cutting principle: The material is seized by the cutting rotor and cut at the stator knife until it has reached the specified size.
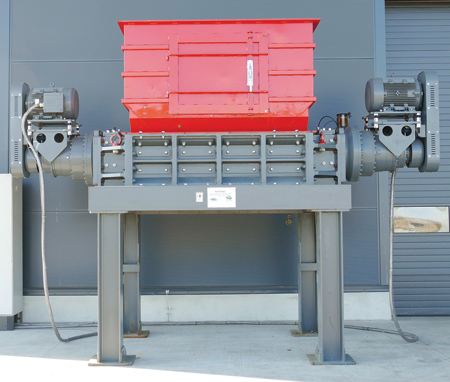
The RM1350/2 ripper is designed for large parts up to complete body structure components in automotive manufacturing.
Products manufactured using the zinc die-casting process can be found in vehicles as well as in toys or medical technology products and can take on a wide variety of forms. Not only is the process particularly versatile, but there is also no loss of material to worry about, as the zinc residues can be remelted and re-processed without any loss of quality, which benefits the environment.
Disposal, however, is a problem: The often bulky production residues require a lot of space and usually have to be removed manually at short intervals, which impedes production processes. The sharp-edged surfaces also increase the risk of injury for the personnel responsible. The M600 single-shaft shredder from ERDWICH Zerkleinerungs-Systeme GmbH, which can be installed directly on the die-casting machine, offers a remedy. It minimizes the space, logistics and time required and makes manual handling obsolete. For components of different sizes, ERDWICH also offers the RM1350 ripper and the M465 and M(H)480 twin-shaft shredders with electro-mechanical and hydraulic drives.
The zinc die-casting process has been established in mass production for a long time: Depending on the size of the product to be manufactured, it is possible to produce several parts in the three- to four-digit range with just one die casting mold per hour. Particularly in the production of parts for the automotive industry or in mechanical engineering, sprue and runners, punch burrs or defective workpieces can lead to full scrap containers within a very short time. If these are not replaced quickly enough by empty containers, this results in a considerable impediment to the operating processes - in the worst case, the production speed must be throttled. "In many companies, the removal for remelting is often still done manually," explained Harald Erdwich, Managing Director of ERDWICH Zerkleinerungs-Systeme GmbH. "The personnel are then not only exposed to noise and heat, but there is also an increased risk of accidents and injuries due to the sometimes very sharp-edged die-cast parts."
On-Site Shredding of Production Residues
How can these difficulties be avoided even during the production of the die-cast parts? ERDWICH has developed shredders for different sizes for this purpose, which can be installed directly at the die casting plant. In this way, the scrap parts are shredded to a more manageable size even before they are stored in the containers provided for this purpose. Among others, the single-shaft shredder M600, which is available with different cutting gear lengths, is suitable for this application. It was designed for shredding small die-cast parts weighing up to 2 kg and can significantly reduce the volume of the parts by up to 60 per cent. "With our plants, we always make sure that they fit the specific requirements of our customers," Erdwich reports. "That is why we offer the M600, as with most of our shredders, with different sizes of cutting gear and drive powers."
The compact machine dimensions are another advantage, because depending on the version, the plant takes up a floor space of just 1.5m2. This means that operation is possible even in confined spaces. "In addition, the company attaches great importance to the longest possible service life and ease of maintenance: The fully hardened knives, which can be reground several times, ensure the longest possible, uninterrupted operation of the shredder," said a spokesperson.
Automated Solutions for Integration into Production Lines
"In addition to the M600, we also offer shredders that are suitable for shredding larger scrap parts," explained Erdwich. "These include the M465 and M(H)480 twin-shaft shredders and the RM1350 ripper, which can efficiently shred and break down parts weighing up to 10 kg or even complete body structure components. Each shredder meets our high safety standards and is designed for long operating times." All equipment can be connected directly to the casting station or die-casting machine and, as fully automated solutions, can also be retrofitted into existing production lines.
After shredding by the ERDWICH shredders, the manageable metal parts can be collected in containers via conveyor belts or transported directly back to the furnace systems. This ensures that the shredded material is returned to the production process as quickly as possible. The volume of waste cast parts is reduced by 50 to 60 percent. Thus, the entire internal logistics process can be optimized, resulting in the eradication of space consuming and cost intensive temporary storage of the reject materials, and further removes the need for manual removal of the dangerous material. Furthermore, the size reduction can lead to energy savings in the melting furnaces, since the smaller components are more efficiently and more easily remelted.
For more information contact:
Harald Erdwich, Managing Director
Erdwich Zerkleinerungs-Systeme GmbH
Gewerbestraße 6, D - 86859
Igling (Germany)
+49 8191 9652-0
infoline@erdwich.de
www.erdwich.com/en