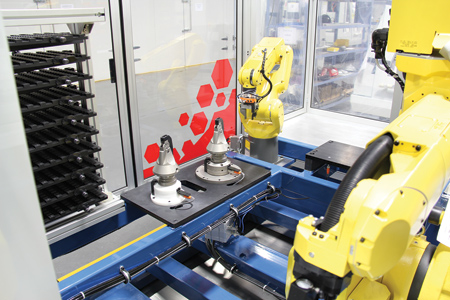
Two part fixtures in the resting station where the fixture gets loaded/unloaded by the small robot, after which the larger robot picks up one fixture and places it into the machine for part grinding.
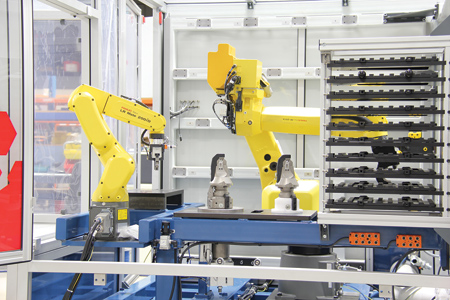
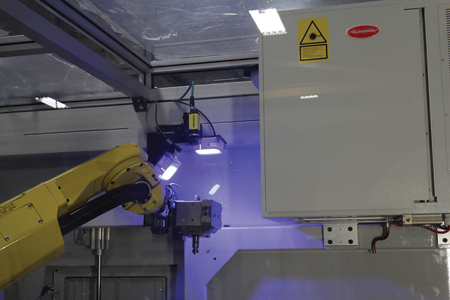
Major aircraft manufacturers predict the global aircraft fleet to double in the next 20 years. At the same time, regulatory requirements, driven by the need for passenger safety and operating economy, present new challenges for those supplying parts to this industry.
Beyond just making the component, manufacturers must be able to trace individual parts through their manufacturing processes, and also provide quality assurance results. Similar trends are seen in other industries such as medical component manufacturing. In meeting these demands, aerospace parts manufacturers are looking for a complete and integrated manufacturing solution.
Recently, ANCA developed a fully automated solution for root form grinding of jet engine turbine blades. ANCA engineers worked closely with customers to deliver a manufacturing cell that would do much more than just root form grinding of turbine blades.
The single-base cell includes automated part loading, high precision grinding and quality assurance, outproducing the previous multi-machine process while achieving part quality requirements.
Using a single robot, ANCA's TXcell automated grinding cell can automatically load grinding wheel packs and the workpiece - a highly successful approach for ANCA customers manufacturing rotary cutting tools. With the addition of a second robot in the TXcell, the machine can complete secondary operations unmanned.
Because of this multi-function processing capability, the ANCA TXcell solution is more productive in terms of throughput compared to ANCA's existing machines, producing more parts complete per hour than the machines it will replace. The previous grinding process only did root form grinding. Supporting part quality and accountability, the cell solution after grinding also detects part numbers, inspects, cleans and laser-marks each part.
The Automated Solution
The first part of the solution was automatic part handling of the turbine blades for unmanned production. With turbine blades being a non-uniform shape, traditional processes require them to be encapsulated in a soft alloy that holds them during grinding. But encapsulating the blades was an added process.
The ANCA solution was to design a two-piece fixture for holding the turbine blade that could be automatically loaded by the large robot. The loading of blades into the fixtures was achieved with the addition of a second (smaller) robot to the TXcell. The original large robot is assigned to change wheel packs and also load the fixture and blade together into the grinding machine.
This opens a whole range of machining possibilities as one CNC grinder essentially becomes a complete flexible manufacturing cell. With two robots in the cell, the customer could use both to do other additional tasks.
In the blade grinding application, an added process is part serial number tracking - achieved with the addition of a Cognex camera and laser etching. Before grinding, the turbine blade serial number is read by the Cognex camera. This data is then passed to the laser etcher for post grinding I.D. marking.
A further capability of the cell is post-process part gauging by a Renishaw Equator automated measuring machine. The larger robot unloads a finish ground blade and presents it to the Renishaw Equator which then automatically gauges the part. Good parts are returned to the pallet by the robot, and fail parts are put in bins based on whether they are oversize or undersize.
In addition to unmanned turbine blade root form grinding, the customer required a certain level of grinding production capacity. Again, using the flexibility of the large robot, an automatic pallet change system was created to extend capacity from one pallet to 10.
These added functions meant the TXcell was not only grinding the parts unmanned over a weekend, but delivering them with individual serial numbers that could be validated against required QC checking systems for later reference. A result that, according to one satisfied user, went "above and beyond the expectations we started with."
Customers who have invested in this technology have found that having two robots in the one manufacturing cell has been successful in managing components that are difficult to hold, such as turbine blades and knee joints. In these instances, the smaller robot loaded the parts into a fixture and the larger robot loaded the fixture into the machine.
Enabling multiple manufacturing operations on a single machine cell has obvious benefits such as reduced capital equipment, better productivity and reduced work in progress (WIP) and inventory.
This new dual robot approach opens the door for great improvement in grinding productivity and quality, no matter how complex the grinding requirements.
Authored by Duncan Thompson, ANCA Product Manager
For more information contact:
ANCA Inc.
31129 Century Drive
Wixom, MI 48393
248-926-4466
usainfo@anca.com
www.anca.com