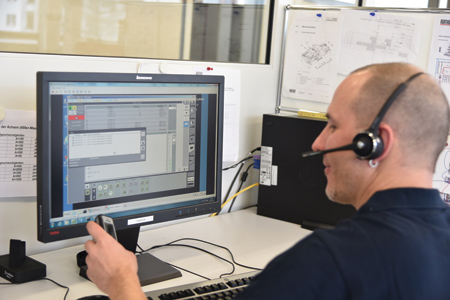
Teleservice allows the customer to have a service technician access through the user interface and check for problems. Problems are diagnosed immediately. Machine operators can take the required actions under the guidance of the technician.
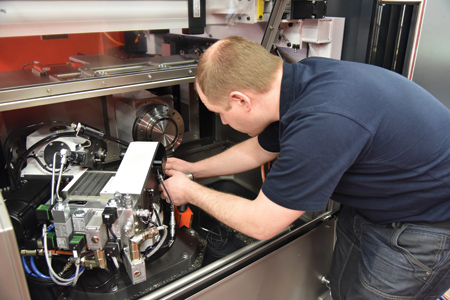
Smart Connectivity allows for scheduled service appointments.
Agathon offers a comprehensive Industry 4.0 package, called Smart Connectivity, that is designed to maximize productivity on three levels: maximize the productivity of the individual machine; raise the productivity of the entire factory floor with plant management; and maintain optimum machine performance with Teleservice diagnostics and preventative service appointments.
Open Interface Technology
The latest models of Agathon grinding machines-Leo, Dom or Evo-are offered with two optional interfaces: one basic and one advanced. The advanced interface allows for accessing up to 300 data elements. With the available data, customers always knows the current status of their machines, including subsystems.
The information made available comes from various areas of the control architecture. It could be as simple as alerting the user to an open door or confirming all components are functioning properly. The interface also provides productivity evaluations over a defined period of time. Real-time data is readily available: Which job is in the queue? Which programs and tools have been set up?
The data is transmitted via an OPC UA interface. OPC UA is a safe and open M2M communications protocol. Safety is provided by encryption and a certificate management. "Open" means that the interface runs on a cross-platform service oriented architecture (SOA) for all types of hardware and operating systems. This is central for comprehensive plant management.
Customer Requirements Determine the Solutions
"What we have now is a machine that can tell the user all about its productivity," said a company spokesperson. "Plus, the user can communicate directly with the machine through the interface. How can this information be used? It depends on the specific customer needs as well as their plant configuration. We thought it necessary to also offer them the instruments required for effectively analyzing the data.
"Together with our partner bfa solutions, ltd., we offer a manufacturing execution system (MES). Another option, an MES solution called PiSolutions, is compatible with all common ERP systems. This means that we are able to select our OPC UA interface depending on the customer's requirements (Basic or Advanced). This evaluation tool can be perfectly tailored to the customer's configuration.
"Depending on the number and types of machines on the floor, our solution only reads and evaluates the data that is essential for the customer. They may invest in a basic server solution offering a broad spectrum of options in regards to data evaluation and reporting. They can determine the overall equipment effectiveness (OEE) and, based on these findings, put in place a plan of action for continuous process improvement. The effects of these corrective actions may also be monitored and traced. This is an excellent starter kit for companies that wish to gain solid insight into their production."
There are also companies with large and heterogeneous machine layouts. If they raise their production, even in the parts per thousand ranges, it will result in a significant increase in productivity of the entire floor. In such cases, Agathon's interface provides in-depth information so that the customer is able to carry out comprehensive statistical analyses.
Plant Management-When Machines Talk
"The more processes that can be integrated within plant management, the greater the overall benefit," said the spokesperson. "For example, in the manufacturing of an indexable insert, grinding is the central process. If the productivity of a single Agathon machine can be maximized using data acquisition and evaluation, imagine the result of linking that to the productivity of all the grinding machines. It can be applied to machines upstream and downstream such as sintering, coating, cleaning. Production then becomes significantly greater throughout the plant.
"This is the core value for Agathon's open interface. A customer who invests in an Agathon machine for the first time, and is already using an existing MES, can easily integrate the new machine into the current plant management. However, the interface offered by us plus the MES solution, PiSolutions, will allow the integration of all machines, even those of other providers."
Teleservice
Smart Connectivity allows for preventive maintenance and Teleservice. A scheduled service appointment for a machine is usually faster and less expensive than an unplanned one.
Teleservice allows the customer to have a service technician access through the user interface and check for problems. Problems are diagnosed immediately. Machine operators can take the required actions under the guidance of the technician. In other cases, the problem can be quickly analyzed and rectified with a field service appointment. In either case, overall productivity is maintained at a greater rate.
For more information contact:
Agathon Machine Tools, Inc.
9 Parklawn Drive
Bethel, CT 06801
203-730-8741
mailamt@agathonusa.com
www.agathon.com