
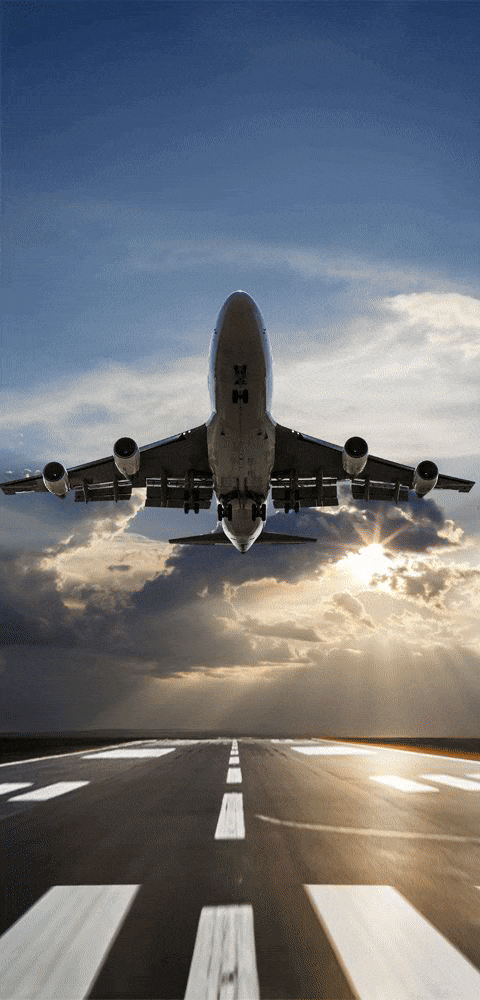
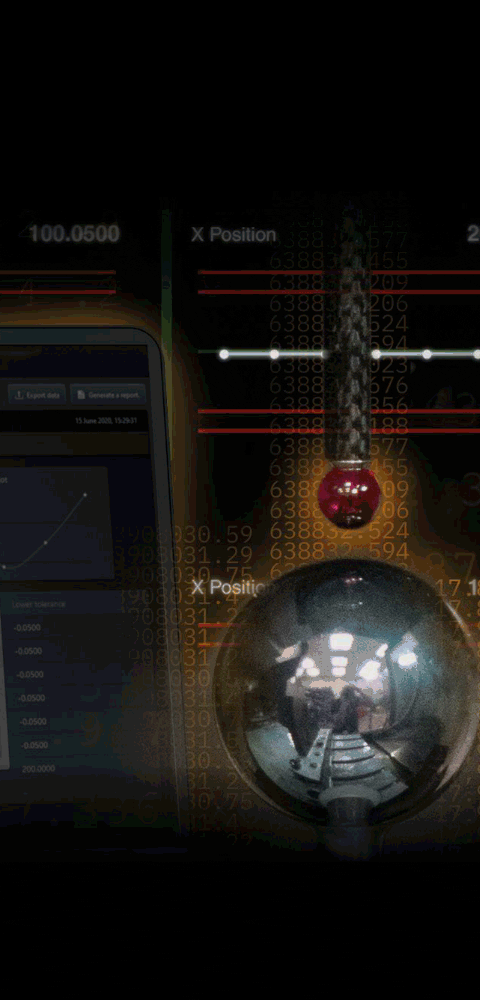
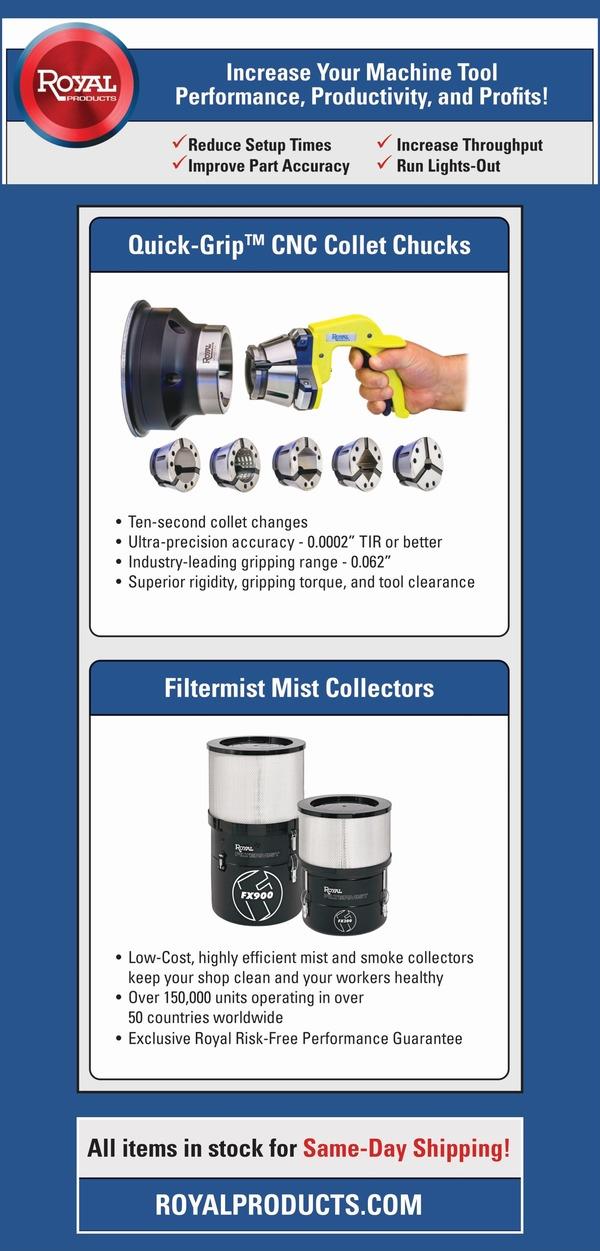
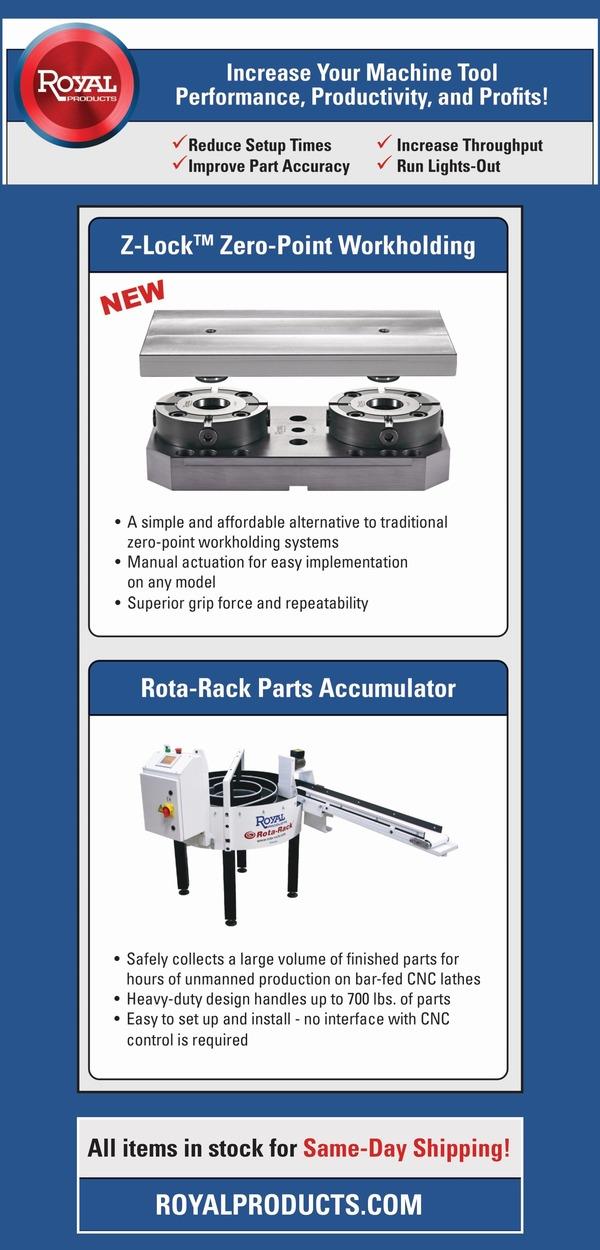

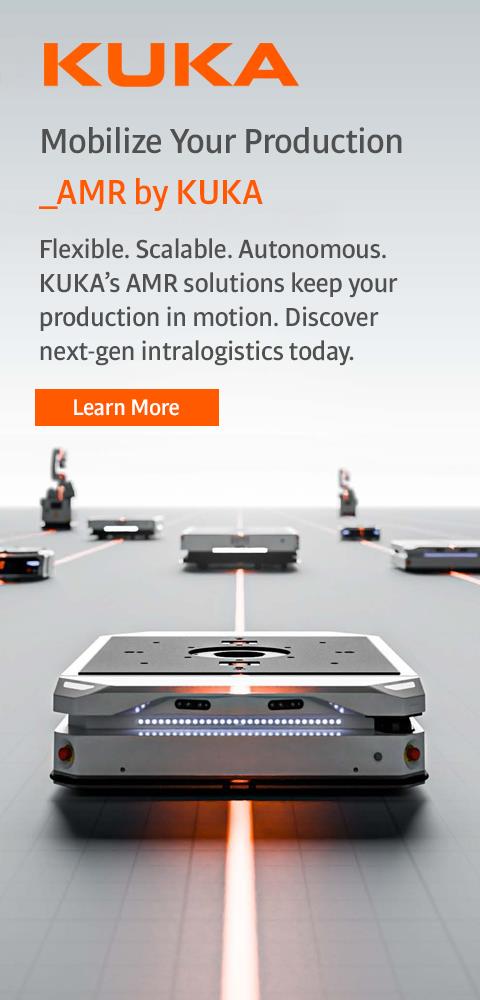
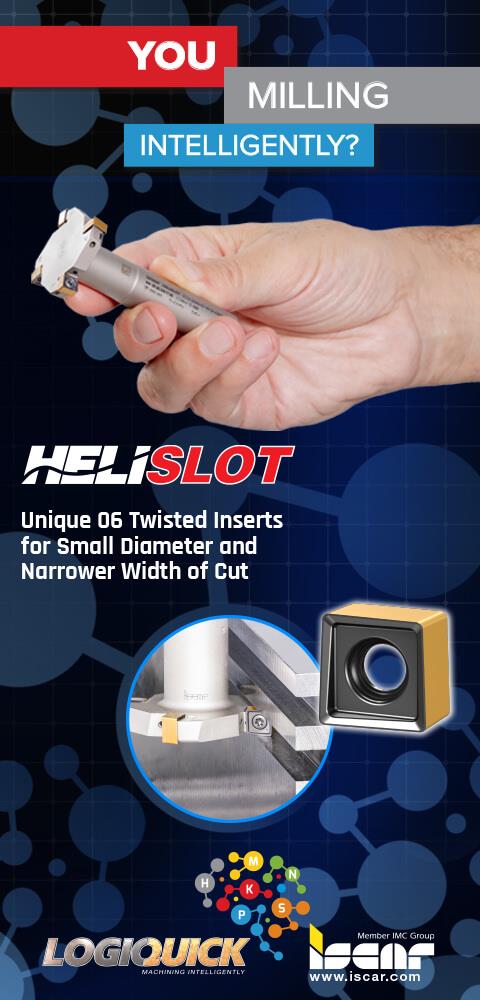
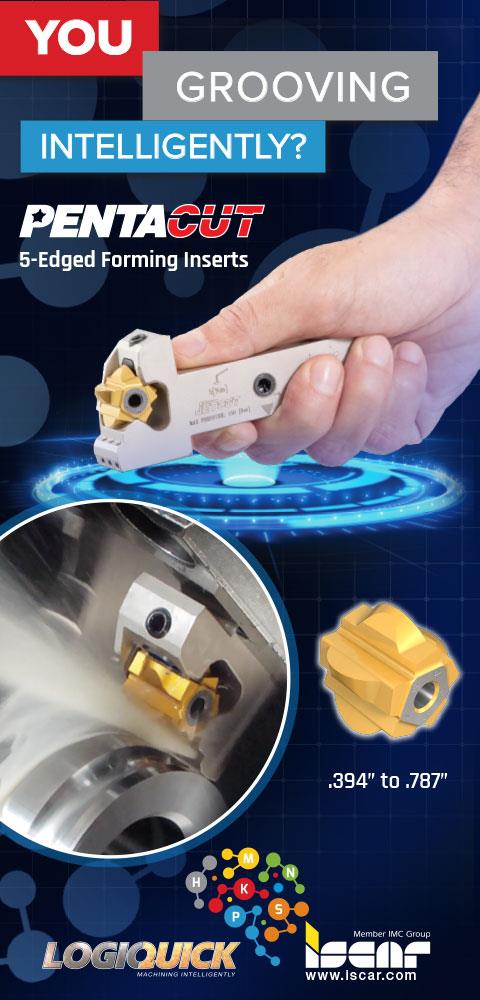
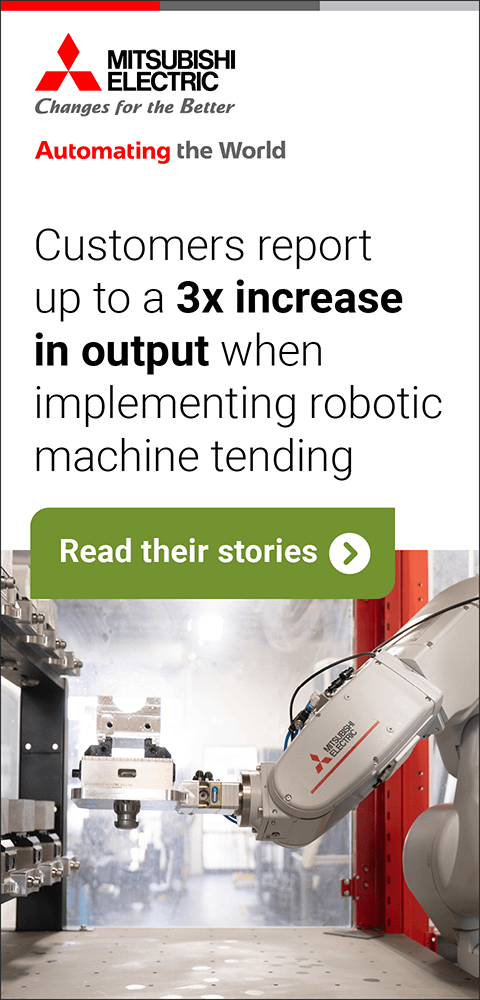
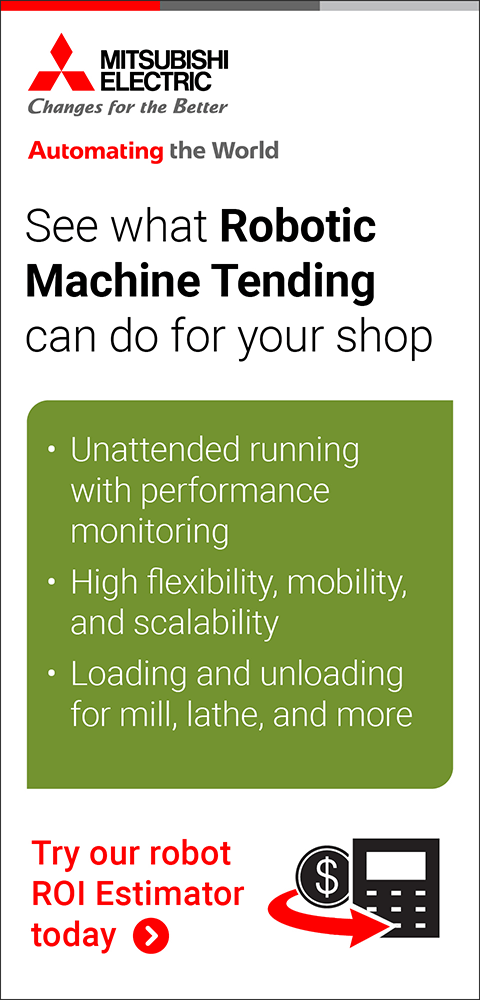
Next Generation Face Mill
November 1, 2017
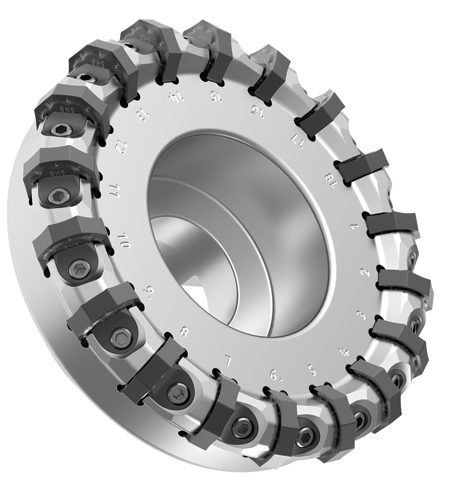
Kennametal's Mill 16 has a wedge-style clamping system, numbered pockets and inserts, and an open pocket design to increase chip flow in heavy roughing
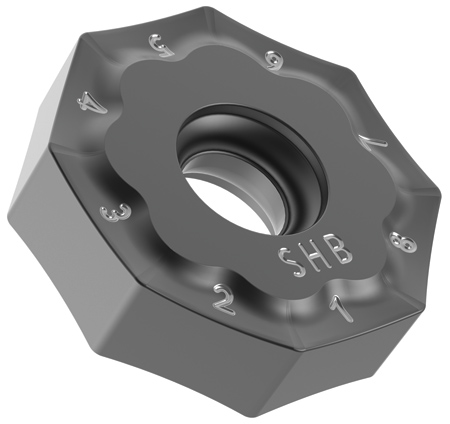
The octagonal, double-sided insert has 16 effective cutting edges
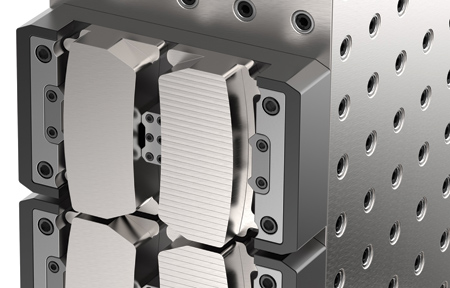
"The finish machining operation on these ductile iron plates saw double the tool life and double the feedrate with Mill 16," said a company spokesperson.
Kennametal's Mill 16 is engineered to meet the challenges associated with machining compacted graphite iron (CGI).
"Compared to cast iron, CGI has lower weight and greater strength, and is suitable for components that are exposed to both thermal and mechanical stresses like engine blocks and heads for cars and trucks, exhaust manifolds and brake parts," said Senior Global Product Manager for Indexable Milling Marcelo Campos. "As with other cast irons, however, it is quite abrasive, and somewhat gummy to machine. We developed Mill 16 not only for CGI, but for all types of cast iron, which remains a popular choice for gear boxes, housings, pump bodies and other components used in the automotive, agricultural and heavy equipment sectors."
Campos outlines Mill 16's strengths as follows:
- The Mill 16 has a fine- and medium-pitch cutter body equipped with an innovative single-screw, wedge-style clamping system. This reduces time spent in the tool crib setting the tool and assures rigid, no-fail tool placement. Each pocket on the cutter body is numbered, as are each of the insert's cutting edges, assuring maximum accuracy and ease of use when indexing to a new cutting edge.
- The heart of the Mill 16 is an octagonal, double-sided insert with 16 effective cutting edges, providing low tooling cost per part. The face of each cutting edge contains an aggressive chip-breaker for positive cutting action and increased chip flow. The wedge clamp on either side of the insert's top face is likewise chamfered to improve chip evacuation.
- Mill 16 is available in cutter diameters ranging from 2" to 10" (50 mm to 250 mm). Kennametal has rated the maximum axial depth of cut (Ap1) at 5.5 mm (0.216"), although depths to 9 mm (0.35" or greater are achievable, an important consideration where casting variation is a concern. Due to the cutter's low cutting forces, up to 100% radial cutter engagement is possible. All cutters have internal coolant supply capability.
- The carbide is new as well. "Kennametal's grade KCK20 is a PVD AlTiN/AlTiCrN multilayer coating bonded to a wear resistant substrate that provides an average tool life of 30% greater than comparable TiAlN-coated grades," said the spokesperson.
- A wide assortment of insert edge preps, geometries, corner radii, as well as a number of complementary grades allow the Mill 16 to perform in a variety of machining conditions, from heavy roughing to semi-finishing. Because of the insert's integrated wiper facet, fine finishing to Ra 3.2 µm or better is possible.
"Customer field tests have shown consistent and positive results. During a dry machining operation on a ductile cast iron plate using Mill 16, feedrates were increased by 41% and tool life doubled tool. A gray iron transmission case was machined at a feedrate of 0.39 mm per tooth (0.015 inch) and cutting speed of 208 m/min (682 ft/min), leading to reduced spindle loads compared to the legacy tool and slightly improved tool life. Metal removal rate and tool life on a water pump housing was more than doubled by switching to Mill 16," said the spokesperson.
For more information contact:
Kennametal Inc.
1600 Technology Way
P.O. Box 231
Latrobe, PA 15650
724-539-5000
www.kennametal.com
< back