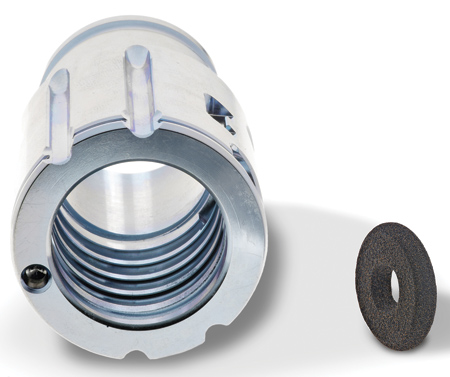
Meister's HPL Wheels are suitable for heavy stock removal grinding applications such as Electronic Power Steering (EPS) ball-nut tracks.
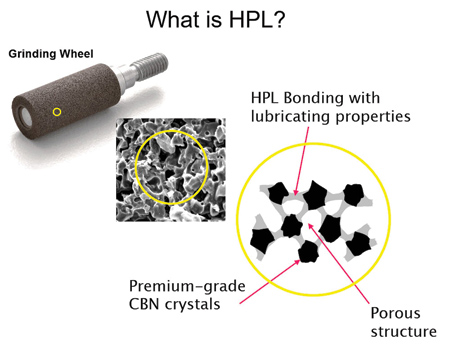
New HPL technology combines high end CBN crystals in a very open pore structure and HPL vitrified bonding, which has lubricating properties.
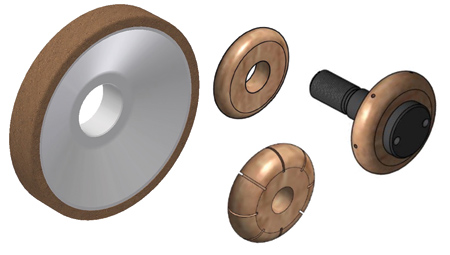
Meister's HPL CBN wheels are available for internal or external applications in mesh sizes 60-1,200.
Meister Abrasives High Performance Lubrication (HPL) Grinding Wheels rely on premium grade CBN crystals fixed with durable, porous, intrinsically lubricated bonding matrix to allow substantially faster grinding of difficult materials without sacrificing quality because of wheel loading and/or part burning.
According to Dr. Peter Beyer, PhD, CEO and Chief Technologist for Meister Abrasives, the HPL superabrasive wheels are an extension of the company's proprietary High Performance Bonding (HPB) technology.
Meister HPL wheels contain a lubricant that is intrinsic to the bonding matrix chemistry and is released uniformly as the wheel breaks down. Wheels manufactured with this technology minimize friction from bond/workpiece interactions, minimize heat generation and deter the onset of metal loading into the bond structure.
HPL technology also makes it possible to implement wheel characteristics that are not economically feasible with standard vitrified bondings. The grit retention and lubricating properties of the bond make it possible to utilize high concentrations of premium grade CBN crystals that in a standard bonding matrix would generate too much pressure and heat.
The unique properties of these intrinsically lubricated wheels address a wide range of problems including: burning of parts; wheel loading; excessive wheel wear because of heat related issues; and quality issues because of temperature sensitive materials.
Beyer said that R&D for this technology has been going on for about 18 months.
"Early adapters in Europe and the United States have tested dozens of application-specific HPL recipes with excellent results," Beyer said. "Although the extent of performance improvements varies from application to application, I can say that our customers rarely switch to a new technology for existing production grinding applications if they are not realizing a 25% or better improvement in productivity."
According to Bruce Northrup, Vice President and General Manager of Meister Abrasives USA, applications for the new HPL abrasive technology include:
- Deep bore grinding with limited coolant access, such as fuel injection nozzle components
- Blind-end bore grinding, such as lash adjusters and tappets
- Heavy-stock form grinding applications, such as electronic power steering (EPS) ball-nut tracks
- Creep-feed grinding of tool steels and superalloys
- High stock removal out-of-round grinding for punches
- Any application where the concentration of oil and lubricant are less than ideal or the flow of the coolant is impeded, as is the case with deep bores.
HPL CBN grinding wheels are available for internal and external grinding with mesh sizes ranging from 60 to 1,200.
For more information contact:
Meister Abrasives USA, Inc.
201 Circuit Drive
North Kingstown, RI 02852
401-294-2530
sales@meister-sbrasives-usa.com
www.meister-abrasives-usa.com