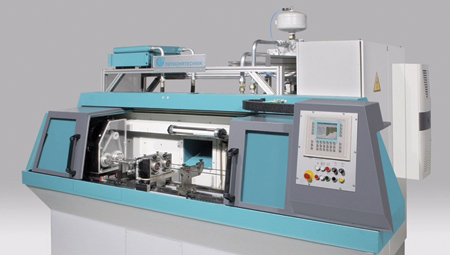
A TBT ML200 manually-loaded, twin-spindle deep hole drilling machine, two of which are being supplied by Kadia Inc to DC Machine in Summerville, Charleston, SC
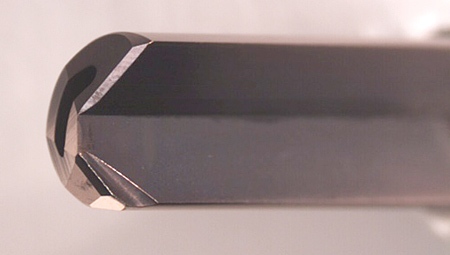
The TiAlN-coated deep hole drill with special cutting edge geometry and chip breaker used for cutting trials on the first TBT ML200 being supplied to DC Machine.
Kadia Inc. has set up a division to provide deep hole drilling solutions to manufacturers in the U.S., Canada and Mexico.
The development follows the company's appointment to sell and service the full range of deep hole drilling machines and tooling from TBT Tiefbohrtechnik, which was founded in southern Germany in 1966. Both Kadia and TBT are members of the multinational Nagel Group.
The agreement includes a license for Kadia Inc. to manufacture, stock, resell and regrind carbide-tipped gun drills locally. The machines themselves will continue to be built at TBT's factory in Germany.
"We develop deep hole drilling processes for any size of manufacturing project, from firearms through automotive and petrochemical to medical drilling solutions," commented Dennis Tanis, Vice President of Kadia's North American operation.
"In most cases these drilling systems are supplied based on standard TBT gun drilling machines with one to six spindles.
"If a machine has more than two spindles, it is often equipped with automated loading and unloading by a gantry-mounted, or pick-and-place robot.
"We make carbide tipped tools here for gun drilling and stock 250 different part numbers for immediate delivery in the size range 0.05 to 1". TBT's range goes higher, however, to 1.65" diameter and also encompasses solid carbide, indexable insert and drills ground with a high speed chip breaker."
The first two TBT deep hole drilling machines sold by Kadia Inc are being used for rifle barrel manufacture.
Process reliability trials of over 100 cycles were carried out on the machine using a 33" long drill with a special TiAlN-coated cutting edge and chip breaker geometry. Bores 450 mm deep and 5.6 mm in diameter were drilled at a feedrate of 240 mm/min, meeting the customer's required cycle time. Surface finish of 0.03 to 0.05 mm Ra runout was also achieved.
The short, four-month lead-time from receipt of order to supply is due to TBT holding partly finished machines in its factory located in Dettingen an der Erms, near Stuttgart, for rapid completion to customer specifications. Both machines are ML200 horizontal, twin-spindle models (www.kadiausa.com/tbt-machinery) from the TBT range, supplied without automation for manual load / unload by DC Machine's operators. The company's owner, Brian Plaisance, already has several deep hole drilling machines on the shop floor including one from TBT. The machine's performance left him in no doubt as to which make to choose when he needed to invest in extra capacity to cope with increasing demand for barrels from rifle manufacturers in the U.S.
TBT gun drills are suited to producing long small diameter holes on conventional machining centers and lathes. When using a gun drill on these types of machines a pilot hole must be first drilled to guide the tool.
For more information contact:
Dennis L. Tanis
Executive Vice President
North American Operations
KADIA Inc.
8020 Kensington Ct.
Brighton, MI 48116
734-277-4060
dtanis@kadiausa.com
www.kadia.com