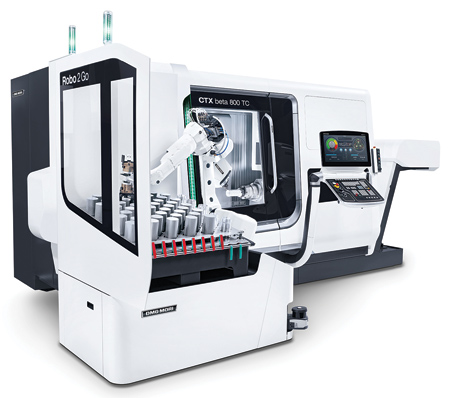
Robo2Go is designed for mobile use with up to four lathes.
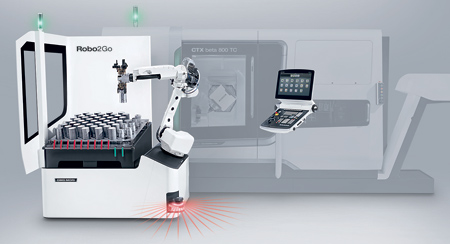
Use of an area scanner means that Robo2Go can do without protective fences -- as the operator enters a defined safety area, the system slows down, and once he is in the danger zone, it shuts down completely for the safety of the worker.
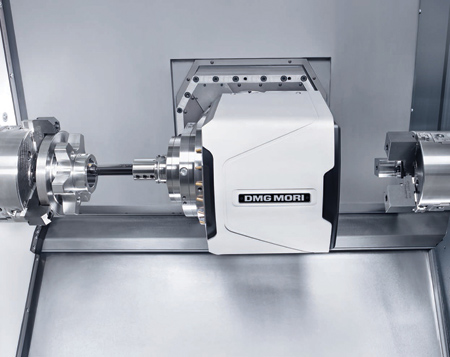
All the operator has to do is enter the dimensions of the workpiece, the chuck and the gripper, then select one of the pre-defined arrangements of the workpiece tray and finally start the automatic process.
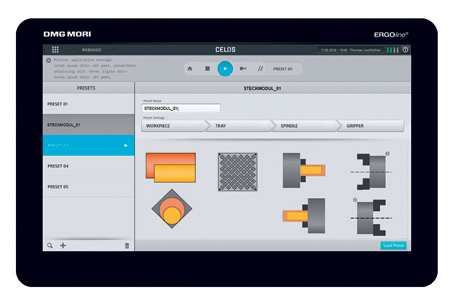
With a Y-stroke of 7.9 in. and the ultra-compact turn & mill spindle compactMASTER with HSK-A63 interface (Capto C6 as an option) the CTX beta 800 TC offers users a wide range of applications from turn & mill complete machining through to 5-axis simultaneous machining.
One of the latest examples in the field of automated Turn & Mill complete machining is the CTX beta 800 TC equipped with Robo2Go. DMG MORI has offered the Robo2Go, a solution that combines performance of the turning center's ultra-compact turn & mill spindle compactMASTER with automation flexibility, adding more productivity. The CTX beta 800 TC closes the gap to the classic universal lathes in the direction of maximum flexibility for components for the machine-engineering, fluid or hydraulics industry.
Robo2Go: Automation Made Simple
The Robo2Go system can be positioned at different lathes as required with a lifting device in a short amount of time, which maximizes investment security. Free access to the work area of the machine tool is possible at all times.
The robot is taught directly with a powerTOOL on CELOS. The operator enters the dimensions of the workpiece, the chuck and the gripper and then selects one of the pre-defined arrangements of the workpiece tray to start the automatic process. This intuitive way of programming a robot enables especially small and medium-sized enterprises entry into flexible automation without the need of any expert knowledge.
Area scanner usage means that Robo2Go can do without protective fences. As soon as the operator enters a defined safety area, the system slows down, and once he is in the danger zone, it shuts down completely for the safety of the worker. A faster working speed is possible for the robot, because this is not a collaborative solution in which the human operator works in the action area at the same time as the robot.
CTX Beta 800 TC: Turn & Mill Technology
With a Y-stroke of 7.9". and the ultra-compact turn & mill spindle compactMASTER with HSK-A63 interface (Capto C6 as an option) the CTX beta 800 TC offers users a wide range of applications from turn & mill complete machining through to 5-axis simultaneous machining and counter spindle. The compact design of this spindle with its integrated release cylinder for tool changing provides a torque of 88.5 lbf. ft. and a length of just 13.8". The B-axis with a swivel range of ±110° enables highly dynamic machining with rapid traverses of 70 RPM. It has a speed rating of 12,000 RPM with an output of 29 HP. An optional 20,000 RPM high-speed version is also available without any decrease of torque.
With a high-tech modular building block system DMG MORI allows customers to equip the machine individually in line with their particular range of components. This includes among other things different tool magazines with capacities of up to 80 pockets instead of the standard 24. In its standard version the CTX beta 800 TC is equipped with an NC-controlled tailstock and a main spindle designed as a fluid-cooled integrated spindle motor (ISM76) with 280 lbf. ft. and 46 HP or optionally as an ISM102 with 568 lbf. ft. and 51 HP. The machine can also be equipped with a counter-spindle instead of the tailstock for 6-side complete machining. The ISM52 PLUS with 6,000 RPM and 125 lbf. ft. is available for such operation. In combination with the ISM102 spindle motor, chucks with diameters of up to o 16" can be used on the machine. Steady rests that are available for workpiece diameters of up to o 6" are recommended for the machining of long workpieces.
The sturdy traveling column concept stems from the larger CTX beta 1250 TC. Maximum stability and accuracy are achieved through the combination of direct measuring systems in all axes of the traveling column.
The machine concept also improved in its ergonomic design: a distance from the machine front to the spindle center of only 13.7" ensures ideal conditions for simple loading and unloading. It has a footprint of just 91.5 ft2 or 115.2 ft2 with chip conveyor.
The possible applications of the new CTX beta 800 TC are manifold. Above all, the machine is aimed at the classic user of a universal lathe, but is far more flexible due to the integrated tool changer, as time-consuming retooling operations are no longer necessary with now up to 80 tools. In addition, the B-axis means that only low-cost standard tools are required for machining at an angle. The machine has a stroke in the Y-axis of ±3.9".
The CTX beta 800 TC comes with the ERGOline control with CELOS on Operate 4.7 with Siemens 840D solutionline, which offers performance on 5-axis free form machining. Possible applications of the CTX beta 800 TC are expanded by 16 exclusive technology cycles that are available as an option.
For more information contact:
DMG MORI - Americas Headquarters
2400 Huntington Blvd.
Hoffman Estates, IL 60192
847-593-5400
Service Hotline: 855-DMG-MORI (364-6674)
info@dmgmori.com
www.us.dmgmori.com