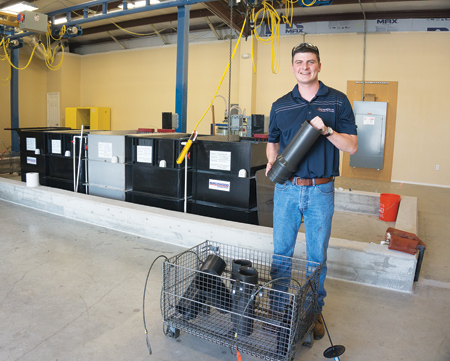
Matthew Dobias, President of A.R. Machining, shows his company's machined parts capabilities with complete metal finishing.
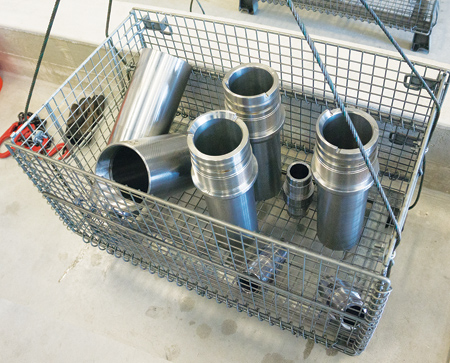
Parts before and after metal finishing.
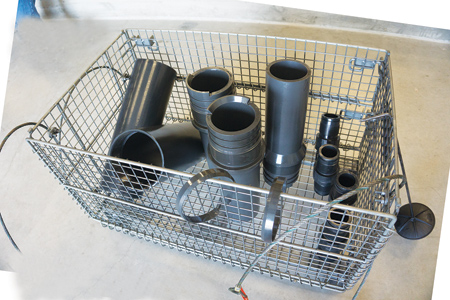
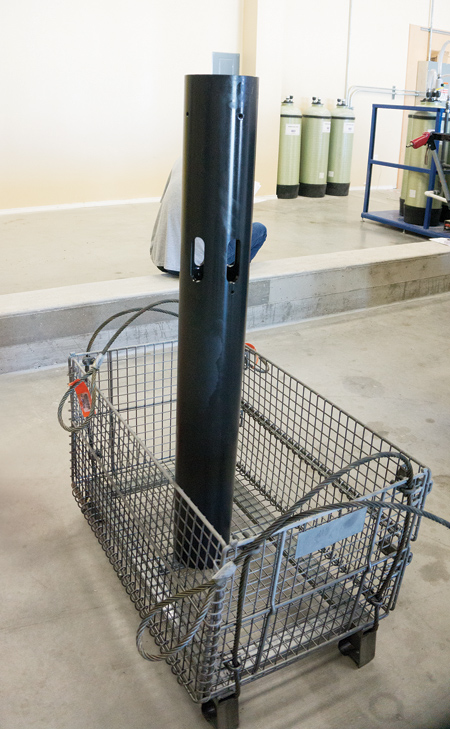
A large down hole finished part.
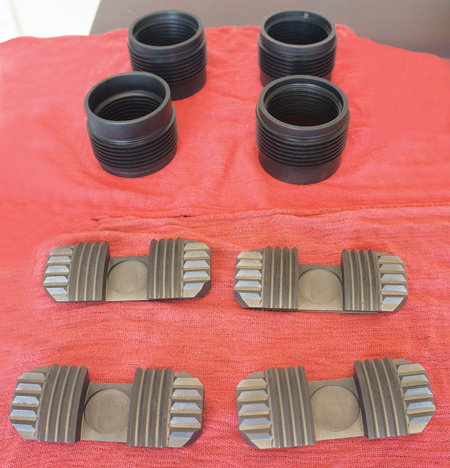
Examples of the Microlok MZN Zinc Phosphating finish on different metals.
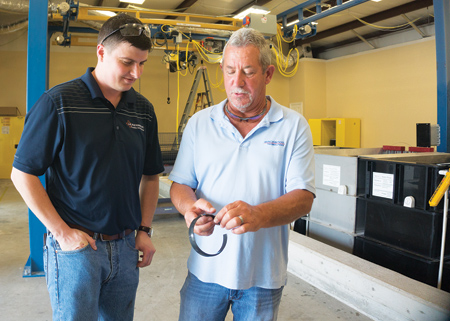
(l-r) Matthew Dobias and Tom Ingersoll discussing the Birchwood Technologies finishing results after the system was initially set up.
OEM manufacturers are demanding faster turnaround times from their suppliers in order to bring their products to market faster. To meet this need, A.R. Machining, Inc. recently installed a new zinc phosphate finishing line from Birchwood Technologies. Improved product quality with capacity to finish parts up to 6' long by 2' in diameter at a fast turnaround time were some of the benefits derived from this new installation.
A.R. Machining is a contract manufacturer specializing in precision machining work for the aerospace, oil, gas and semiconductor industries. "The company has built a solid reputation based on excellence, quality, precision and accuracy serving its customers," said a company spokesperson. "With over 50 highly trained employees and a modern 38,000 sq. ft. manufacturing facility, it provides a full spectrum of services with over 24 CNC mills and lathes with 4-axis capability. The company's capabilities include prototype products, turn-key CNC production, part finishing and mechanical assembly.
"Time and distance to outside finishers was a big factor in our decision to add the in-house zinc phosphate system from Birchwood Technologies," reported Matthew Dobias, President of A.R. Machining. "Using outside finishers took several days and made it difficult to meet customer delivery requirements."
Improving on its processes and delivering its products to customers in a timely manner has been key to A.R. Machining's success for over 37 years. "By being responsive to the changing needs of customers with the latest technology and exceptional service, A.R. Machining has grown into a world-class precision machining part supplier," said the spokesperson. "It is AS9100 Rev. C and API compliant as well as ISO 9001:2008 certified. Its products serve the most advanced and technically demanding industries." As part of its continuous improvement mission, the company decided to investigate in-house finishing options.
Choosing the Right Zinc Phosphate System
"Our oil and gas customers required corrosion protected parts and just-in-time delivery," Dobias stated. "These are large, down-hole steel components that are often stored outdoors before installation, so they are subject to corrosion. In our area, outside finishers are several hours away. Turnaround time was a real problem. Also, their finishing tank sizes were limited for our larger parts. We needed large capacity and ferrous metal corrosion protection. We knew about Birchwood Technologies and asked area Account Manager Tom Ingersoll for metal finishing input. Birchwood Technologies chemists performed several no obligation, no cost test finishes on our sample parts in their lab. Tom recommended their zinc phosphate process and showed us how their MicroLok MZN and Dri-Touch Plus IRP3 process combination would fit our needs, so we went with a new system."
Protective Finish for Iron and Steel with Environmental Benefits
The MicroLok MZN process is a fine-grained zinc phosphating solution for iron and steel components. These materials make up the majority of A.R. Machining's present work. Applied at 120-160 °F, the finish complies with MIL-DTL-16232G, Type Z Classes 1, 2 and 3. This was an important advantage for A.R. Machining because the company is expanding its work in the military industry. When sealed with a rust preventive, the MicroLok MZN finish is designed to provide excellent corrosion resistance, anti-galling protection and break-in lubricity to critical working surfaces - important advantages in certain military applications.
Birchwood Technologies proved to A.R. Machining that the MicroLok and Dri-Touch Plus IRP3 process is ideal for these kinds of work. This includes not only oil field equipment, but also any steel components that require robust corrosion protection, anti-galling properties and break-in lubricity without a significant dimensional change.
For the needed extra corrosion protection, A.R. Machining utilizes Birchwood Technologies' Dri-Touch Plus IRP3. As a heavy-duty protective coating, it produces a robust film that is suitable for use on parts for limited outside storage, in warehouses and for certain battlefield conditions. The product is an effective water displacer with a self-healing, soft, waxy film with noticeably thick consistency and high moisture resistance. "The combination process really improves the appearance of finished goods. The parts coming out a nice, uniform dark gray or black, depending on the material," reported Dobias.
The Birchwood Technologies system consists of seven 220-gallon capacity tanks with a 48" x 30" x 35" footprint. An overhead crane is positioned above the system to handle large individual parts and baskets of smaller parts. The tank line set-up is equipped with an adjacent Ion Exchange system. This Ion Exchange technology purifies and recycles the system's rinse waters, resulting in a closed-loop, zero-discharge installation. Water is conserved and no discharge is made into the sewer system. Making the Ion Exchange process integral to the finishing line was an added important consideration in A.R. Machining's decision to go with the system.
Satisfying Results Bring in New Customers
"System start-up with training from Tom Ingersoll went quickly and smoothly," said Dobias. "No additional workers were required to operate the system, and tank cleaning, changing solutions and preparation for new part finishing takes less than a half day.
"With our new in-house system, we get same day finishing. The cost is less than half compared to outside finishing and is improving as more work is added. Just as important, we eliminated many hidden costs using outside finishing vendors, such as the extra part moves, packing and repacking parts, inventorying and inspecting parts when received, and unexpected delays on different part projects. Having in-house control of quality was a key consideration that led us to going with the new system."
"One pleasant surprise we have had is that prospects for new work know of the Birchwood Technologies process when they see the name on the tank system," continued Dobias. "They know that it is not just a bluing or blackening process but a high quality, patented zinc phosphate process. Birchwood Technologies has a successful history with its zinc phosphate finish with the firearms industry. Another benefit is the fact that the process meets military specifications. Both are helping us acquire new work. Overall, adding the system was good decision, and as new work is added, it is proving to be a good investment."
For more information contact:
A.R. Machining, Inc.
632 West Front Street
Hutto, Texas 78634
512-759-2003
heathera@armachining.com
www.armachining.com
Birchwood Technologies
7900 Fuller Road
Eden Prairie, MN 55344-9702
800-328-6156
info@birchwoodtechnologies.com
www.birchwoodtechnologies.com