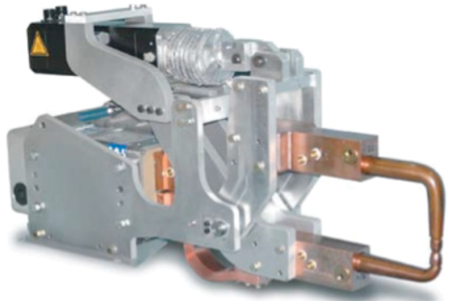
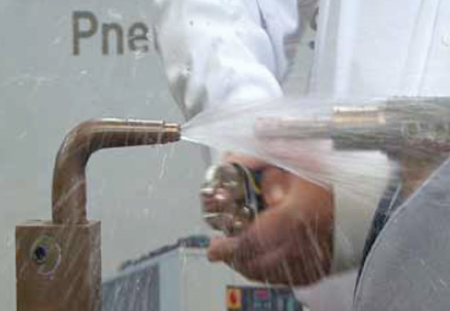
(left) A Parker electromechanical weld gun is shown. (right) Water remaining in the weld gun is expelled during tip changing.
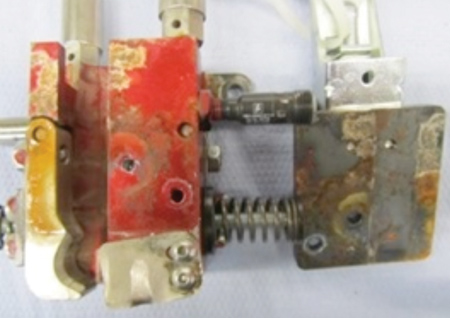
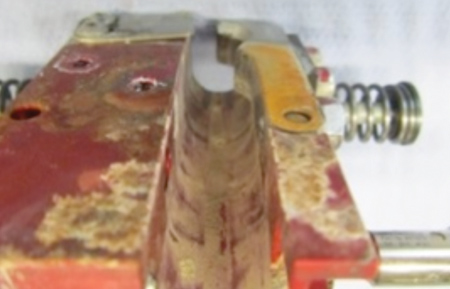
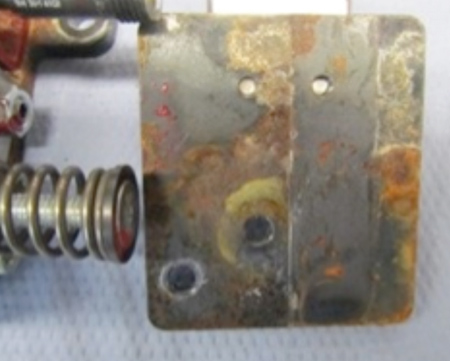
The ingress of weld water irreparably damages automatic tip change equipment.
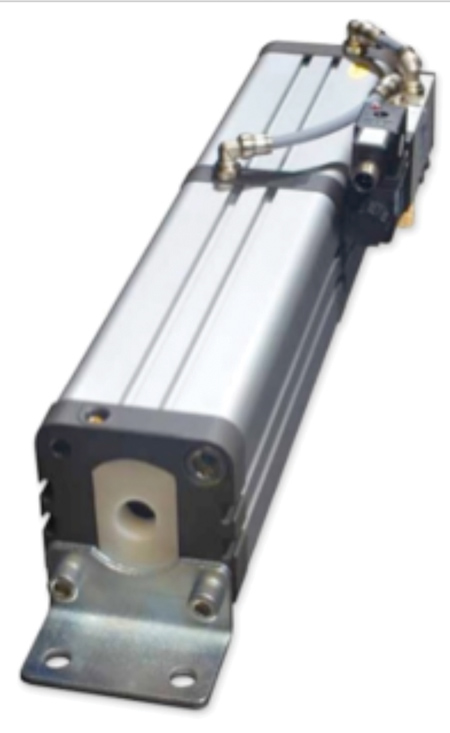
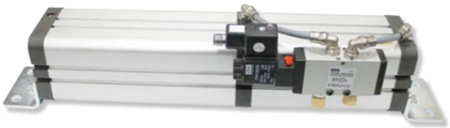
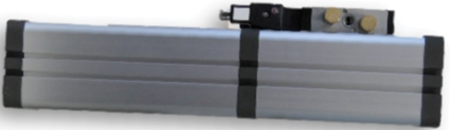
The Parker Water Retract Actuator is backed by Parker cylinder and actuation technology.
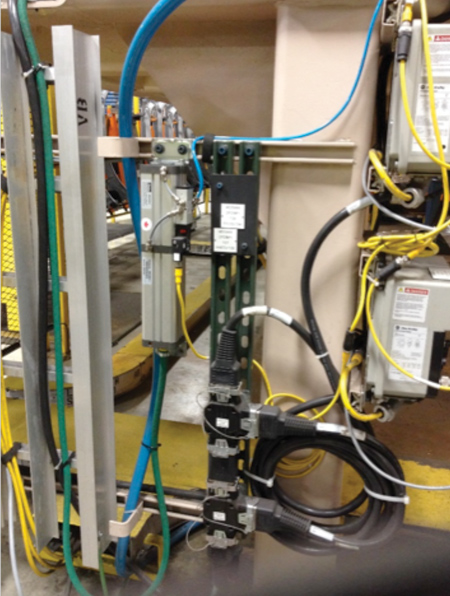
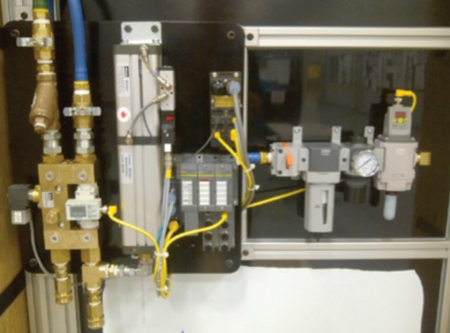
The Parker Water Retract Actuator is installed in two automotive plants' welding lines.
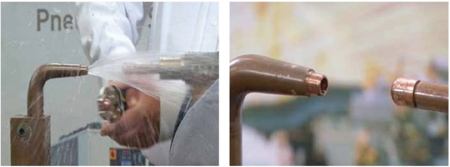
(left) A weld tip change is shown without a Parker Water Retract Actuator. (right) A weld tip change is shown with an actuator on.
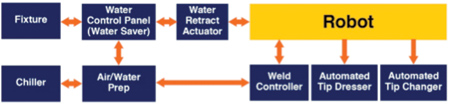
"Parker's Water Retract Actuator is among the many main components of a clean and efficient weld cell that are also manufactured by Parker," said Tim Ritter, Automation Product Manager.
To ensure consistent and repeatable high-quality welding automation, plant engineers need to select proper maintenance equipment (such as tip dressers) and make certain weld consumables and holders are serviced at regular intervals, sometimes as often as three times per day.
Water is circulated through the robotic weld gun to cool it. When the tips are removed to be replaced, even though the equipment is turned off, there is always some water left inside the gun under pressure. This water sprays out as the tips are removed, landing all over the welding cell - on equipment and on the operator. Preventing this water expulsion creates a safer environment, minimizes maintenance problems and reduces downtime.
The Weld Water Expulsion and Ingress Problem
Weld water is treated with antibacterial and rust-inhibiting chemicals. This treatment is typically seen as acceptable because it is intended to remain within a closed circulation system. The problem with that theory is that in practice this hazardous water is actually expelled during routine operation and maintenance tasks within an automated weld cell.
For operators, this obviously poses a risk of skin/eye irritation and injury. It is also a safety concern, because spilled water pools on the floor and causes slipping and falling.
For machinery within the cell, including weld robots and automatic tip changers and redressers, water spray lands on and flows across surfaces along grooves, seams and curves to either ingress or drip to the floor, damaging equipment and causing electrical hazards to power cords and connectors that lead to downtime as well.
Some machinery is designed with channels on its exterior - to channel expelled water away - or with water-resistant seals. Even for those exceptions to the rule where channels or seals are found, it is typically an incomplete solution for preventing all water from escaping or being diverted to a catch basin. Inevitably, water pools on the floor and onto equipment and operators.
In cases where water is diverted down channels, the water's contaminants create corrosive deposits along the way. These deposits build up over time and can impair the machine's performance, leading once again to costly downtime or more frequent repairs/equipment replacement.
Automated weld cells are found in a variety of industries, of course. However, this safety and operational hazard is a particular focus of automotive manufacturers that are at the forefront in using automation and advanced production techniques to achieve every advantage in efficiency and quality they can uncover. To them, this water weld problem is clearly an opportunity for improvement.
Manufacturing philosophies such as those that drive Chrysler's World Class Manufacturing (WCM) and the Toyota Production System all work to ensure uniformity of quality, cleanliness, safety, efficiency and productivity in all plants. Water expulsion is directly at odds with the tenets of these quality systems and will cause plants to receive lower rankings or ratings as a result.
For example, a component of some production systems calls for painting a plant's floors in lighter color tones. There is an extra cost for doing this, of course, but it is justified by providing better overall plant illumination through light reflection and because it makes it easier for plant workers to see dropped parts and tools on floors. Standing weld water makes these painted surfaces slippery for nearby plant employees, and its corrosive characteristics destroy the paint, necessitating costly and unneeded re-painting.
The Weld Retract Actuator Solution
Recognizing that weld water expulsion is a universal problem, Parker Hannifin developed new Weld Retract Actuator (WRA) technology. Backed by Parker cylinder and actuation technologies, the actuator is an aluminum-based construction that includes stainless steel and composite materials compatible with treated cooling water. The Parker Viking Lite Series valve provides reliable and precise operation of the actuator's pneumatic controls.
When activated, the actuator holds the water that remains in the system even after the water flow monitor has shut off the water supply line. Weld tips can then be changed either by hand or by an automated tip changer without any water expulsion. Nearby machines and operators remain dry, water and chemical waste removal costs decrease, and there is no wasteful downtime during changeover needed to wipe down wet surfaces.
Multiplying the amount of time saved by the number of tip changes every day, and then by the number of welding robots, and then by the number of operational days every year, the savings the Parker Water Retract Actuator provides add up quickly and can be substantial for an entire plant.
In addition to the greater employee safety provided, over the course of a year new WRA technology could potentially mean one or more additional vehicles produced, just with this essential maintenance/operations improvement. To quantify just what it means to a plant's performance and associated cost savings, Parker has developed tools that include an ROI calculator that illustrates the volume of water and chemicals wasted and the production time to be gained.
With Parker's new WRA technology, there is no longer any need for automotive manufacturers to place their employees and weld equipment in harm's way during weld tip changeovers. Parker's pneumatic technology, used in thousands of applications, provides a reliable, cost-effective and safe solution for an operational problem that is incompatible with the best practices of advanced automotive manufacturing facilities today.
Authored by Tim Ritter, Automation Product Manager, Parker Hannifin Corporation
For more information contact:
Tim Ritter
Automation Product Manager
Parker Hannifin Corporation
Automation Division
989-714-4878
tritter@parker.com