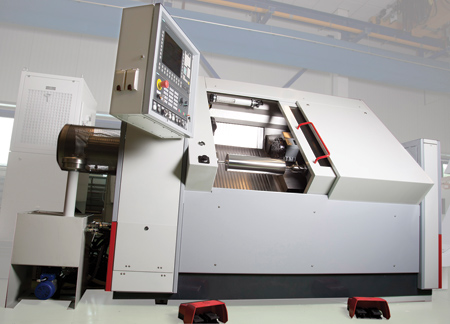
The Mikroturn 200 high-precision hard turning machine from Hembrug
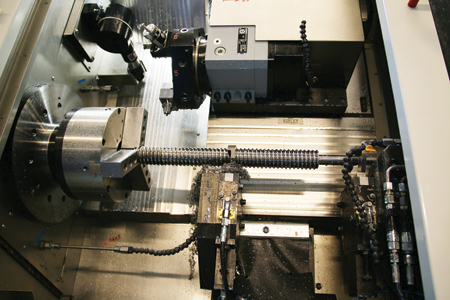
The Mikroturn 200 L can handle threaded spindles and ball bearing nut systems as well as hard finishing between centers.
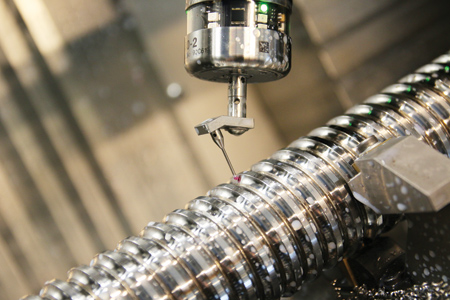
Checking diameter dimensions with an integrated switching probe system
"Higher productivity, shorter cycle times, smaller production runs, cost savings and quick deliveries are playing an increasing role in the industry," said a Hembrug spokesperson. "Increasingly, production plants are required to absorb the development capacity of their suppliers. Hembrug, a specialist in high-precision hard fine machining, is confronting the challenges that arise from this."
Machining Hardened Components
In an effort to reduce its total cost of ownership (TCO), a German manufacturer expressed a wish to replace one, or even two, of its cylindrical grinding machines with a single universal hard turning machine, which could produce ball bearing circulation nut systems and rework threaded spindles. Hembrug reported that its Mikroturn 200 L is the first micro-turning machine, which, as well as being able to hard-turn threaded spindles (Tolerance Class C0), is also suitable for ball bearing nut circulation systems and longer components between the centers.
"Because they offer a range of advantages, these machines are being seen more and more as alternatives to cylindrical grinding machines for high-precision machining of hardened components," said the spokesperson. "These include shorter set-up and cycle times, higher machining volumes with often dry machining processes allowing for better recycling of residual material, lower tooling costs, etc."
High Quality in Series Production
"The main advantage of this machine is the manufacturing quality of the product," said the spokesperson. "The spindles have a very high turning accuracy of a quality that is normally achieved through re-grinding. The diameter tolerances are under 2 um; the surface finish quality Ra is 0.2 um. The values are achieved due to the high accuracy of the turning machine." The main spindle and slide are oil hydrostatically mounted.
The machine base is made of natural granite, which offers good damping qualities and has high thermal stability. The slides are driven by a linear motor. The Mikroturn 200 L can produce threaded spindles with a total resolution error of less than 4 um and a contact angle variation of less than 3° in production.
Features of the Mikroturn 200L:
- Maximum diameter: 380 mm
- Maximum parts diameter between centers: 250 mm x 900 mm
- Maximum spindle speed: 4,000 RPM
- Run-out main spindle: 0.1 um
- Z-axis travel: 750 mm
- X-axis travel: 210 mm
- Rapid traverse: 30 m/min
- Repeat accuracy: +/-0.1 um
- CNC resolution: 0.01 um.
Fewer Process Steps
The Mikroturn 200L offers a range of new features. The machine can, for example, be fitted with two bezels to support the component so that threaded spindles 900 mm long can be machined. Due to its color masks, software from Hembrug is also user friendly. Engineer Martin Huijbers, tasked with developing this software, explained: "The basic software package derives from 15 years experience of hard machining of spindles and therefore offers high reliability, in addition to further refinements."
The software with full color user screens and dialogue structures describes the profile in a clear manner. The open structure enables the user to describe a wide range of profiles. "This makes it easy for the user to program several different products on one machine," said Huijbers. Discrepancies can be easily corrected. Following a brief period of training, the operator can work independently with the software.
Meeting Future Demand
"With this new machine, Hembrug is reacting to discernible trends in the industry," said the spokesperson. "Universal applicability as well as the quick set-up and cycle times can lead to cost savings. Users can offer smaller production runs and with little time wasted in setting up, they can supply their customers faster. The Hembrug Mikroturn 200 L is another step forward in helping users to increase their competitiveness."
For more information contact:
Bill Alexander
North American Sales Manager
Hembrug Machine Tools
802-236-4571
alexander@hembrug.com
www.hembrug.com