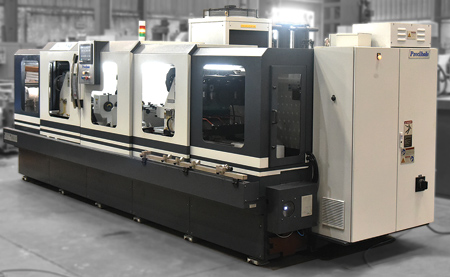
Precihole Machine Tools offers high-precision deep hole drilling and finishing technology.
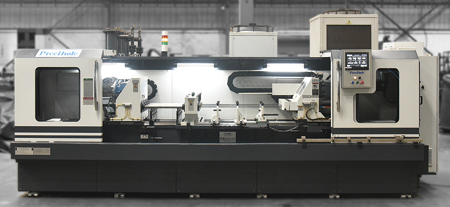
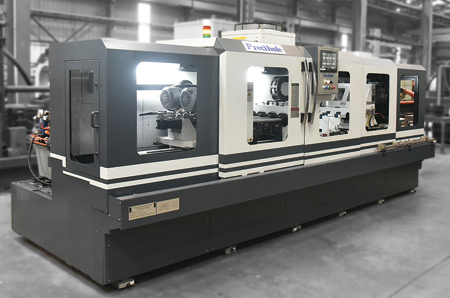
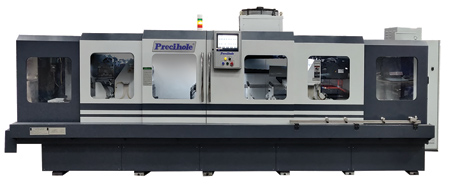
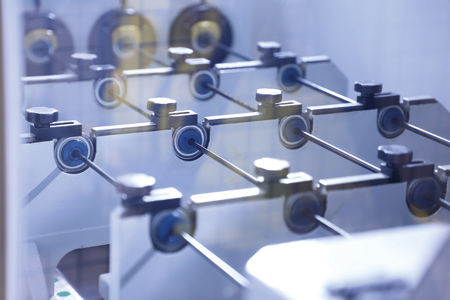
Precihole machine loaded with four gun barrels, shown are the multiple tool steadies to provide tool support.
Deep hole drilling is a machining process that generates holes that can be up to 200x longer than the diameter of the hole. It was invented before World War 1 for making gun barrels. Today, this technology finds applications in over 15 different industries with 200+ different applications, including defense, oil and gas, aerospace, energy, die and mold, medical implants, automotive and hydraulic cylinders.
Conventional drilling can handle length/diameter (L/D) ratios of about 10 effectively. When holes get deeper, several limitations present themselves, such as tool life, surface finish, hole straightness, roundness and chip removal. Once the L/D ratio goes beyond 10 for drilling, deep hole drilling is required. Major types of deep hole drilling processes are gun drilling and BTA drilling.
Gun Drilling is a deep hole drilling process that is used for drilling long holes in diameters from 1 mm to 35 mm. Coolant at high pressure is pumped through the tube, and chips are evacuated from a V shaped flute along the length of the tube from the outside.
BTA Drilling (also called STS-Single Tube System) is a deep hole drilling process that is used for drilling long holes in diameters from 12 mm to 250 mm. Coolant at high pressure is pumped from the outside of the tube and chips are evacuated from inside of the tube
Applications in today's industry require drilling in exotic materials or hard super-alloys while maintaining accuracy and productivity. Maintaining straightness of holes with good tolerance and surface finish requires in-depth knowledge, expertise and experience in the process. Machine features, calculation and selection of process parameters, material input condition, tooling, coolant, filtration etc., have a profound impact on output parameters.
There are three different configurations for deep hole drilling: tool rotating, part rotating and tool rotating/part counter rotating. Selection of the appropriate configuration depends on the application requirements and the accuracies required for the same.
Output parameters for deep hole drilling technology are hole straightness, hole tolerance and surface finish.
"With over three decades of experience, Precihole Machine Tools has been a manufacturer of high-precision deep hole drilling and finishing technology," said a spokesperson. "Together with Absolute Machine Tools, Precihole's commitment to this niche field has earned them a global reputation for delivering innovative solutions and complete customer satisfaction. Furthermore, our combined strength lies in our ability to customize engineering solutions that perfectly align with customer requirements, ensuring them success in every project."
Absolute Machine Tools and Precihole offer a comprehensive range of state-of-the-art deep hole drilling and finishing CNC machine tools. "Together, we are committed to advancing the deep hole drilling industry by investing in research and development and collaborating with tooling partners worldwide. Our continuous innovation ensures that our products remain at the forefront of cutting-edge technology," said the spokesperson.
For more information contact:
Absolute Machine Tools, Inc.
7420 Industrial Parkway
Lorain, OH 44053
800-852-7825 / 440-960-6911
sales@absolutemachine.com
www.absolutemachine.com