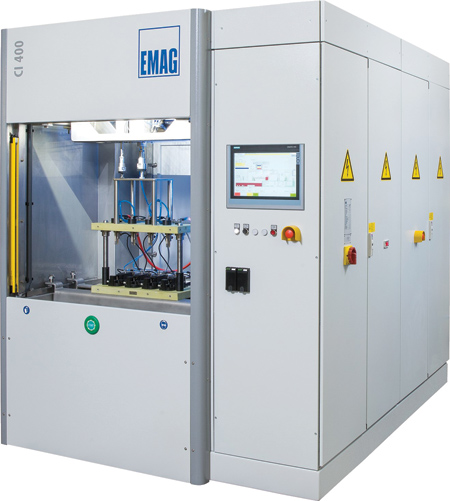
The CI machine from EMAG ECM offers users compact technology with high-quality components.
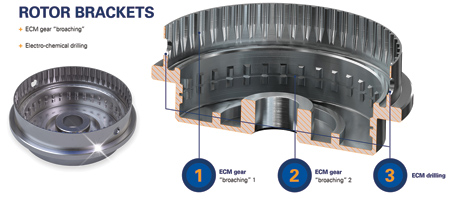
Numerous components in electric and hybrid engines, such as the rotor carrier, benefit from electro-chemical machining. The process is designed to be fast, reliable and energy-efficient.
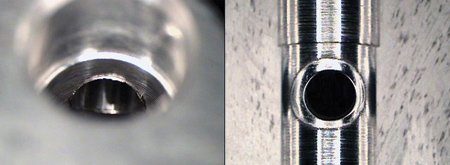
Before and after comparison: the edge of the bore hole is completely burr free after the ECM process (right).
Autonomous steering and brake systems, hydro-pneumatic chassis or radically improved gas mileage-these buzzwords represent a technological change that is triggering a domino effect in the automotive and other industries. An increasing number of components have to satisfy demanding quality requirements. They need to leave the production process in perfect condition and without any defects. If not, the autonomous brake system of a car might fail in crucial moments. Deburring plays a critical role in ensuring this does not happen.
"The required degree of precision is ensured by a process called electro-chemical machining (ECM)," said an EMAG spokesperson. "Currently, many planners are looking for lean production systems to supersede traditional deburring processes. With this in mind, developers at EMAG ECM have extensively updated their CI series of machines: the new ECM CI machine provide extremely fast and precise electro-chemical processes for deburring and machining-or 'ECM cleaning.' It has also minimized installation space. Even complex parts such as pumps or hydraulic housings can be deburred quickly, without error, and in a reproducible manner using EMAG's ECM technology."
To understand the challenge posed by deburring, consider complex components such as pump housings. These components often feature a veritable network of bore holes that hydraulic oil or fuel runs through at high pressure when the part is in use. Removing burrs is not an easy task, particularly when several holes intersect inside the housing. For some large hydraulic components in the aviation and utility vehicle industry, the manual deburring process may take an hour or more, and cost accordingly. "In addition, manual processes carry a risk of error," said Richard Keller, Executive Manager at EMAG ECM. "If a burr is overlooked, it may come loose later during operation and restrict the flow. Considering the high safety standards in airplane or automobile production, this is not acceptable." It is therefore no surprise that electro-chemical deburring has become established for many parts in recent years. Errors are basically eliminated, and the process speed is very high. Throughout the electro-chemical process, an electrolyte solution flows between the workpiece (the positive anode) and the tool (the negative cathode). Metal ions then detach themselves from the workpiece. The shape of the cathode or tool with the active, conductive surfaces is designed so that the removal of material from the workpiece results in the desired component contour. This not only yields a high surface quality without thermal degradation of the workpiece structure, but also ensures completely uniform and reproducible results.
Return on Investment
At the headquarters in Germany, EMAG's ECM specialists continuously develop the process for applications involving new materials, component geometries and quality requirements. The direction of the research is determined by the changing customer requirements all over the world.
With CI series of machines, EMAG ECM is taking the next step: to conserve valuable space in the customer facilities, engineers at EMAG have revised the frame of the CI machine and optimized the size of the cabinet and the electrolyte management system. What is the driving force behind these and other changes? "Against the background of technological development, it is obvious that deburring and ECM cleaning, for example of workpieces that have already been hardened, is becoming more and more important. We wanted to develop a solution that allows enhanced benefits of electro-chemical machining for users while offering reliable processes. This is exactly what the CI series of machines offers. Users reap the benefits of a flexible technology with consistently high-quality components." The cycle time can be adjusted precisely with scalable devices. Depending on the requirements, several components can be machined simultaneously in a single process, and the CI machine can be easily upgraded to a fully automatic system. All parameters of an ECM process are monitored and documented, making them easier to reproduce. The CI machine requires only about 80 sq. ft. of installation space, including the filtration system.
Focus on E-mobility
CI machines are in use at a North American aerospace supplier and an Italian supplier for utility vehicle parts. In both cases, the deburring takes place on highly complex housings. "Despite multiple holes in the component, cycle times are less than 60 seconds-a radical change compared with the previous time-consuming manual process. The examples show that we are on the right track with our approach to development: we have been able to succeed against our national and international competition because our CI machine offers excellent performance at a low cost. The enormous cost pressure for our users necessitates the kind of effective engineering that we offer with our CI machine," Keller explained.
"It appears that the cost-effectiveness argument is gaining more traction with users, as many components in electric and hybrid engines require ECM cleaning, drilling and deburring processes for which EMAG ECM already offers effective solutions," said the spokesperson. "In addition, there is another point that should not be underestimated in the current discussion of carbon dioxide footprints in automobile production. Compared to many alternative processes, electro-chemical machining is significantly faster. This saves a significant amount of carbon dioxide-a fact that convinced the German Federal Ministry for the Environment: an EMAG ECM customer received an environmental innovation award for applying electro-chemical machining on an industrial scale."
For more information contact:
EMAG L.L.C.
38800 Grand River Ave.
Farmington Hills, MI 48335
248-996-4703
info@usa.emag.com
www.emag.com