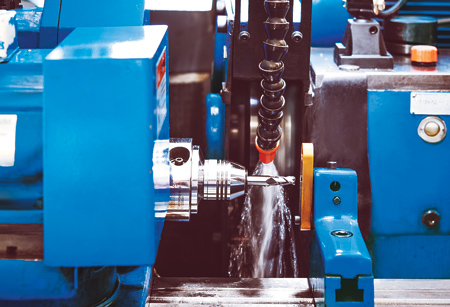
Kopp produces high-precision milling tools and uses KNUTH cylindrical grinding machines for their production.
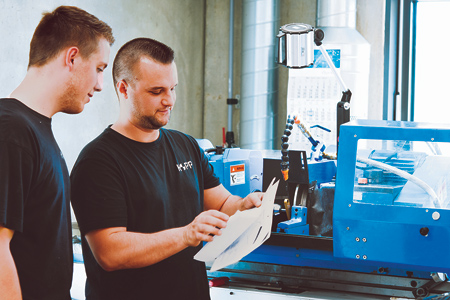
Kopp's first KNUTH cylindrical grinding machine was a used RSM 500 CNC. Kopp recently bought two more RSM 500 CNC machines, which are being fully utilized every day.
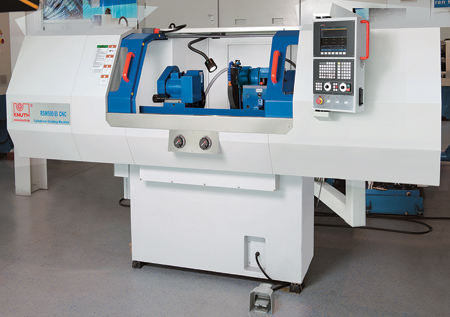
RSM 500 B CNC Cylindrical Grinding Machine
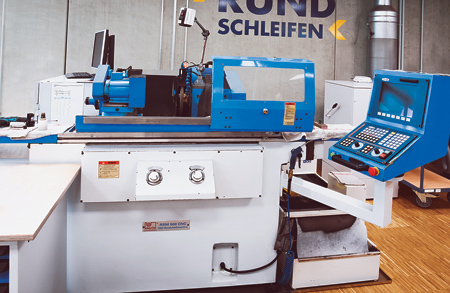
The RSM 500 CNC features a solid machine base with wide V guideways and box ways to help ensure minimum vibration and smooth operation.
Kopp Schleiftechnik (Germany) produces high-precision milling tools and uses KNUTH cylindrical grinding machines for their production.
Kopp's first KNUTH cylindrical grinding machine was a used RSM 500 CNC. More recently, two new machines have been added that are being fully utilized every day.
High-Precision Milling Tool Production
Helmut Kopp Sr. founded Kopp Schleiftechnik GmbH in 1970 with three manual tool grinding machines. Today, the company has 40 employees and serves customers in the automotive, aerospace, medical, energy and engineering industries. In 2016, Kopp expanded and moved into its newly constructed headquarters and 1,500 sq. m production area. At this location, they operate 20 CNC grinding machines for an annual production of approximately 400,000 high-precision carbide milling tools for cutting and drilling metals and plastic materials. Their standard portfolio alone includes approximately 1,000 individual products. All tools can be reground or reshaped multiple times.
Cylindrical Grinding-an Exacting Discipline
Kopp recalled reading about KNUTH in a trade magazine and subsequently purchased a used KNUTH cylindrical grinding machine from a local dealer. KNUTH took the machine to its headquarters in Wasbek, Germany, to test the machine functions and accuracy and to restore any deviations, if needed.
"Cylindrical grinding is an exacting discipline," explained Patrick Jöhnk, Sales Associate at KNUTH Werkzeugmaschinen. "On one hand, we often have to deal with extremely hard metals, and on the other hand, it requires exact calculations that consider heating and expansion of the material during machining, which has to be compensated for by the machine. More intricate workpieces require a more exacting machine and operator processes. The RSM 500 CNC features a solid machine base with wide V guideways and box ways to ensure minimum vibration and smooth operation for optimum work results. The grinding spindle provides superior precision and features hydrodynamic bearings."
Accuracy Within One-Thousandth of a Millimeter
After the machine was set up at the Kopp facility, a KNUTH service technician provided training to familiarize Kopp employees with the machine. "We use the RSM 500 for exact cylindrical grinding of solid carbide metal rods, where an accuracy within one-thousandth of a millimeter is required, before moving the rods on to the next step, where they are refined with a stepped cutter," explained Kopp.
Kopp recently bought two more RSM 500 CNC machines, which are being fully utilized every day. "We rarely have downtimes with our KNUTH machines, and the occasional replacement of a spindle or minor repairs are quick and easy," said Kopp.
RSM 500 B CNC Cylindrical Grinding Machine features and benefits:
- Center height: 5"
- Workpiece length: 22"
- Grinding diameter: 7.9"
- High flexibility for small batch productions
- Solid machine frame with wide V-guides and boxways
- Servo-driven axes run on precision preloaded ball screws
- Electronic hand-wheels for grinding headstock movement
- High-precision hydrodynamic bearings of the grinding spindle help ensure optimum grinding results
- Fagor control optimized for grinding cycles.
"Our customers should be able to focus on their core business," said Jöhnk. "That is why KNUTH offers individualized service packages that are customized for every machine and every workload. This way, we can prevent failures caused by wear and tear, and support interruption-free production."
For more information contact:
KNUTH Machine Tools USA
590 Bond St.
Lincolnshire, IL 60069
847-415-3333
info@knuth-usa.com
www.knuth-usa.com