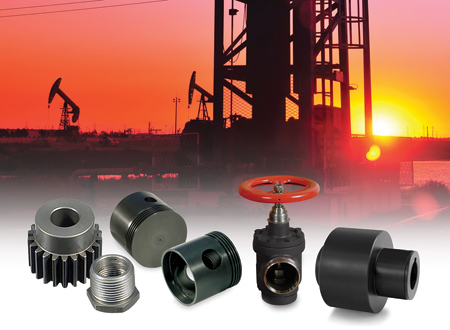
Efficient corrosion protection and break-in lubricity are quickly and easily accomplished on these oil and gas drilling components with one of three Birchwood Technologies' finishing processes. Each one has unique benefits targeting certain finishing needs.
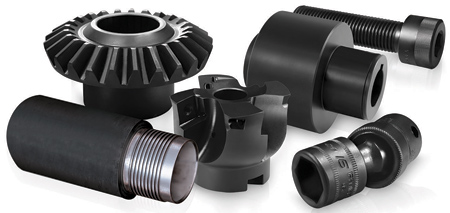
Parts finished with the TRU TEMP process have the highest level of corrosion protection of the three processes discussed in this article. The finish withstands up to 150 hours of neutral salt spray and meets ASTM B 117 specification.
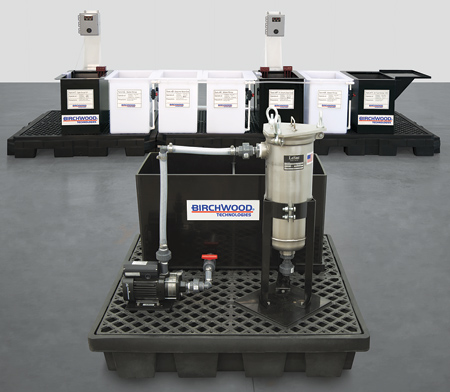
Near-Zero water recycler (foreground) makes the finishing line (background) a closed loop process, reducing water consumption by 99%.
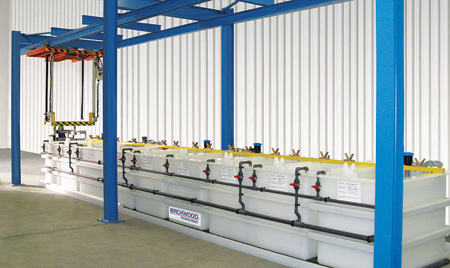
In addition to the Near-Zero water consumption feature, black oxide finishing lines can be designed with complete CNC like the one pictured. It allows for unattended operation by taking advantage of the latest automation.
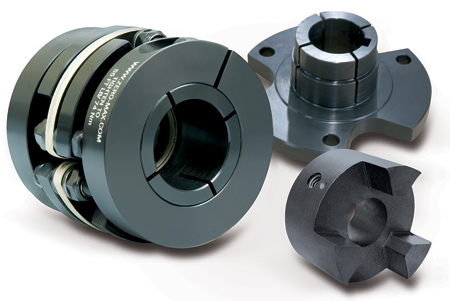
Couplings and connectors are some of the oil and gas drilling components that can be finished effectively using the cold Presto Black process. The 20-minute process provides high corrosion protection meeting SCD 129-2894 specification.
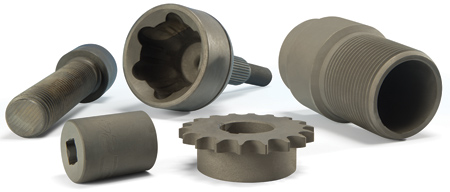
This silver/grey MicroLok AO finish provides robust corrosion protection, plus it has high temperature stability of up to 1,400 °F for high heat applications. The process has the added feature of needing no waste water treatment.
Manufacturers of gas and oil drilling components can face complex issues when dealing with coating and finishing processes for down hole sucker rods, casings, tubing, couplings and related parts. Metal finishing is an important last step in the manufacturing process, and older metal finishing processes may not measure up to today's standards. While corrosion protection is the primary goal, additional factors to take into consideration include component and system functionality, ease of finish application, increasingly stringent governmental and environmental regulations, as well as cost and turnaround time.
Here we will examine factors that should be considered in the selection of a metal finishing process, along with three product choices used by manufacturers of today's gas and oil drilling components. Each of the three product options have significant differences and are designed to meet specific requirements. They include: TRU TEMP Black Oxide (magnetite coating); Presto Black Cold Blackener (copper selenide coating); and MicroLok AO (aluminum oxide coating). These products are designed for use on most iron and steel down-hole drilling components.
TRU TEMP Low Temperature Black Oxide Process
Of the three, the TRU TEMP process provides the most corrosion protection. The TRU TEMP finish withstands up to 100-150 hours of neutral salt spray (ASTM B 117) or several hundred hours of humidity (ASTM D 1748), as verified by independent testing. The satin black TRU TEMP finish is just 0.5 microns thick (20 millionths) with no affect on material hardness or load-bearing properties. This high level of corrosion protection is important for both part storage and shipment in corrosive atmospheres, including ocean shipment. TRU TEMP meets Mil-BTL-13924 and AMS 2485 specifications.
Start-up lubricity of components finished with TRU TEMP is also superior to the other two choices. So where high value oil and gas drilling components are subject to handling, storage and field set-up-with significant time elapsing between these operations-this process provides the most robust protection. The need for extra protection is especially important for valves, couplings, pumps and similar components with value-added operations, such as special features.
An additional benefit of TRU TEMP, besides corrosion protection and break-in lubricity, is the fact that it can be installed in any plant setting without endangering personnel or surrounding equipment. TRU TEMP solutions contain no EPA regulated chemicals, so there is usually no need for waste treatment equipment. In most installations, TRU TEMP rinse waters are sewerable as non-hazardous discharge. This benefit simplifies installation and minimizes the modest capital investment for setting up a TRU TEMP process line.
It is important to note that the TRU TEMP process requires a seven-tank line (Presto Black also requires seven tanks while MicroLok AO is a simpler five-tank line). TRU TEMP also has a longer processing time of 30 minutes, compared to 20 minutes for each of the other two processes.
Because of its magnetite chemistry, TRU TEMP presents a true black oxide finish that is a very consistent, deep satin black finish equivalent in every way to hot black oxide. Because it operates at a low 200 °F temperature, it does not boil or splatter as does traditional hot oxide, making it safer to operate.
Of the three process choices, the TRU TEMP process is the only one that can be set up to operate with minimal water consumption. The optional Near-Zero Water Recycling System provides up to 99.5% in water savings compared to a conventional flowing rinse system.
Adding this option to a seven tank TRU TEMP line allows the user to recycle and reuse the water in the rinse tanks for a month. Then the Near-Zero filter media in the three rinse tanks require replacement. After this easy changeover is complete, the three rinse tanks are refilled with clean water and the monthly cycle starts over. Total water consumption is only 300 gallons.
By comparison, a standard BC100 TRU TEMP black oxide process line utilizes three flowing rinse tanks, each utilizing about two gallons of water per minute. When operated for one shift per day for a month, the total water consumption is about 63,000 gallons, which is disposed of into the municipality's sewer as non-hazardous discharge. Even though the actual cost of this volume of water is usually very small, a flowing rinse system may not be a viable option for many users. This may be the case with metal finishing installations where normal water and city sewer services are not easily accessed. This can occur in small shops on septic systems, where sewer districts restrict water usage, and in plants where the blackening line is located in a warehouse or other location where water and sewer hookups are not easily accessed. In all of these cases, a Near-Zero Water Recycling System can be installed on a new process line or added to an existing line as a retrofit.
The Near-Zero Water Recycling System is designed for TRU TEMP process lines up to 150 gallons in tank size, and is completely pre-engineered for fast set-up. Also, the system can be integrated into most existing TRU TEMP tank lines in only a few minutes.
Once equipped with Near-Zero Water Recycling, a TRU TEMP process line operates with a 30-minute turnaround time for black oxided parts. The finish bath operates at 200 °F and forms a non-dimensional, high quality black magnetite finish that is corrosion resistant and Mil Spec/RoHS compliant. Because this process features a short cycle time, it streamlines part movement, provides better control of finished part inventory and enhances ISO accountability, giving the user same-day turnaround capability to satisfy key customers.
In today's green manufacturing environment, conserving water is highly desirable because it saves valuable natural resources and lowers operating costs. Water restrictions are occurring everywhere, especially in drought-stricken regions. Securing the water necessary to operate a finishing line may become increasingly difficult. A growing number of corporations, backed by government initiatives, are following a mission wherever possible to conserve Earth's natural resources. The Near-Zero Water TRU TEMP black oxide process is designed to achieve these goals.
The TRU TEMP process blackens parts at a cost of 4 to 8 cents a pound.
Presto Black Cold Blackening Process
Cold blackening has received increasing attention and use by manufacturers of oil and gas drilling components. Users choose this cold process because it produces a uniform depth of blackness and also because the corrosion resistance meets their needs without the complexity and hazards of a hot oxide finishing line.
Providing high corrosion resistance tested for up to 1,200 hours humidity exposure, Presto Black meets SCD 1229-2894 specification. It is easy, fast and safe to apply and produces a uniform 0.000030" (1 micron) thick finish that has a porous, crystalline structure. This structure makes it an excellent absorbent base for adding a rust preventative topcoat for extra corrosion protection without a chipping or peeling problem.
Presto Black is recommended not only for blackening oil and gas drilling components, but also for most parts made of cold and hot rolled steels, alloy steels, tool steels, as well as cast iron, forged steels and powdered metal (it will not blacken stainless steel). The process is ideal for both large and small parts held in storage and shipping, and then put into service corrosion-free.
The fast 20-minute Presto Black process makes it ideal for any quantity of parts, from prototypes, short part runs to long runs including just-in-time finishing programs. The process itself is easy to learn. Operators and managers quickly become comfortable with the process due to its simplicity and low maintenance attributes.
One feature of Presto Black is its copper selenide chemistry, which is different than what is used in the TRU TEMP process. The copper selenide formulation contains regulated metals and therefore requires ion exchange treatment of the waste water. This removes the heavy metals so that the process rinse waters can be reused rather than sent to the drain. Adding ion exchange is relatively low cost; it is routinely utilized on process lines of all sizes with excellent success.
The Presto Black process is available for use in existing tank lines or in one of Birchwood Technologies' space-saving, modular tank systems in sizes of 40 gallons, 100 gallons and larger. These systems can be configured to handle virtually any finishing volume and part size, including those with integrated automated part handling. A Presto Black process line requires seven tanks.
Including ion exchange, parts can be blackened at a cost of about 20 cents a pound.
MicroLok AO Process
As a superior functional coating, MicroLok AO is also ideal for finishing oil and gas drilling components. It provides anti-galling protection to aid in component assembly and for oil and gas drilling start-up. It has high temperature stability up to 1,400 °F for high heat applications.
MicroLok is also a patented coating process. Like TRU TEMP and Presto Black, it is an immersion process. It is a non-toxic aluminum oxide conversion coating that is 0.000060" (1.5 microns) thick, silver/gray in color, with tight adherence to the metal surface. (Note the color difference for this process-silver/grey-which many users prefer over a black finish.)
When compared to cold temperature blackening, the MicroLok AO coating exhibits somewhat better corrosion resistance and operates at half the cost, without requiring waste water treatment. It is safe to apply at a temperature of 120-140 °F with no boiling or splattering. There is no scale or sludge buildup in tanks and needs only simple bath maintenance and pH monitoring. The MicroLok AO process avoids the use of EPA regulated chemicals (the cold blackening uses toxic copper and selenium-both of which are tightly regulated). Also important, the MicroLok AO process rinse waters are sewerable as non-hazardous discharge and require no waste treatment.
As a superior functional coating, MicroLok AO is an ideal finish for assemblies with sliding components such as suckerods, couplings and mating down hole drilling components. It applies quickly and easily to small and large components.
Another advantage of this process: finishers with existing lines can easily convert to the process. There are no technical or costly conversion challenges when switching from an existing cold process using existing tank facilities. Also, new, economical tank lines are available from Birchwood Technologies in space-saving, modular tank system sizes of 40 gallons, 100 gallons and larger. These systems can be configured to handle virtually any finishing volume and part size, including those with integrated automated part handling. This process requires only a five-tank line (the other two processes require a seven-tank line), no ion exchange or other add-ons. And parts can be finished at a modest 4 to 8 cents a pound.
Authored by Jesse Vouk, Sales and Marketing Manager, Birchwood Technologies
For more information contact:
Birchwood Technologies
7900 Fuller Road
Eden Prairie, MN 55344-9702
800-328-6156 / 952-937-7931
info@birchwoodtechnologies.com
www.birchwoodtechnologies.com