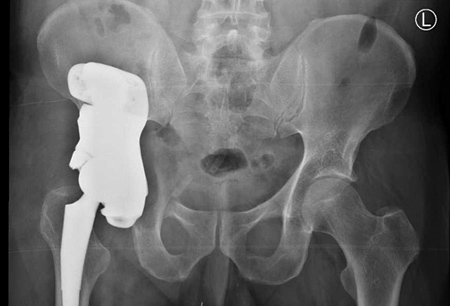
A time-sensitive pelvis reconstruction was achievable with 3-D printing technology.
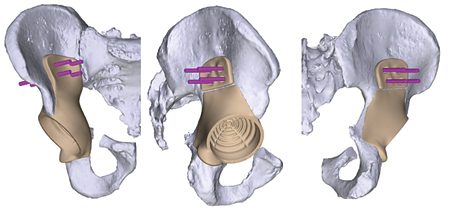
The pelvis reconstruction involved the socket portion that holds the hip joint.
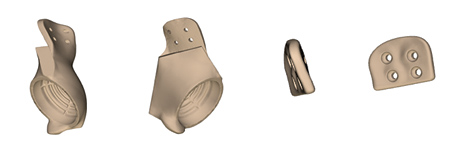
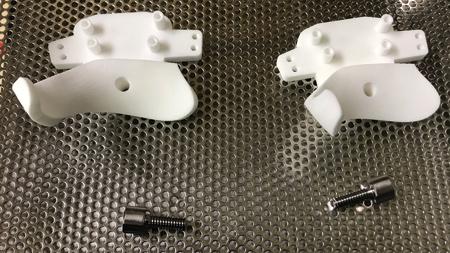
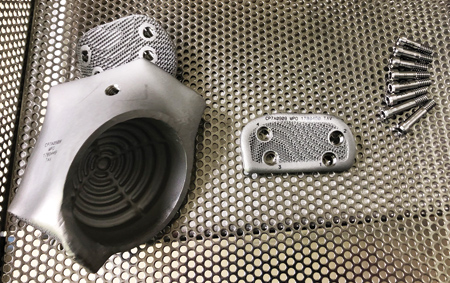
The finished implant was 3-D printed from titanium. The surface material qualities allow soft tissues and bone to grow into it.
With the latest technological advancements in 3-D printing, highly complex bone reconstruction is now a reality.
Orthopedic specialists for years have been developing the technology to model and then create reconstructions of bone defects (often due to tumors or trauma). However, lead times, even up to a decade ago, were too long. It is only in the last few years that lead times have been reduced-allowing reconstruction to become feasible not just for complex cases, but for time-sensitive cases as well. With the latest 3-D printing technology, turnaround time can be as fast as six weeks-a significant leap from the previous six-plus-month lead time. This means new surgery options, more precise bone reconstructions, along with the real possibility of a higher quality of life for patients post-op.
Take, for example, one recent case involving chondrosarcoma of the pelvis, a type of bone cancer that is resistant to chemotherapy and radiation therapy. The portion of the bone with the cancerous tumor had to be removed, along with a margin of normal tissue.
Long bone reconstruction is fairly straightforward because the arm and leg bones are essentially a cylinder shape. However, in this particular case, the cancerous tumor was in the pelvis, and involved the socket portion that holds the hip joint. Reconstructing this area is already a tricky procedure, but in this situation, due to lack of treatment options, a fast turnaround was also essential.
Dr. Ron Hugate, an orthopedic oncologist at Panorama Orthopedics and Spine Center, has had experience with complex cases such as this one. He recognized that this patient would be an ideal candidate for the latest 3-D printing technology. The plan was to first remove the cancer, and then reconstruct the pelvis and restore the patient's functions.
Moving Beyond Traditional Solutions
"The cancerous tumor was in a difficult location-a lot of important structures are in the pelvis," said Dr. Hugate. "Due to the complex shape of the pelvis, an implant could not be easily manufactured using traditional techniques with CNC."
Other issues with traditional techniques included limitations in shapes, sizes and surface treatments. "A newer trend in orthopedics involves using a solid implant with a porous structure-almost like a honeycomb-on the surface," said Dr. Hugate. "This allows the bone and the soft tissues to actually grow into the implant. If you use traditional means, you have to create a solid base, and then either adhere or sinter porous metal wafers onto the material. It is a less-than-ideal manufacturing technique, and causes difficulties when certain shapes are required."
3-D printing allows the creation of almost any shape required, and does not need special machining to achieve this. A porous surface can easily be added during the printing process.
Six-Week Lead Time
Dr. Hugate partnered with a team of engineers to create a personalized implant design. This was accomplished using patient imaging data: A CT scan was used to assess the bony topography, and an MRI to determine the extent of the tumor. Each imaging study was then merged together and converted into a 3-D model.
Using the model, Dr. Hugate met with the engineers and specified design parameters for the implant (hip socket size and position, location of porous material, etc.). They then developed a surgical plan with the use of patient-specific models, guides and templates.
"You have to have a margin of normal tissues that you take out with the tumor," said Dr. Hugate. "I typically add about 1 cm to the dimensions of the tumor, just to make sure that when we make the bone cut, we will remove all of the cancer cells. We then create 3-D printed cutting jigs that actually lay onto the bone in specific areas. These direct me where to make my bone cuts, and they give me a very precise section. The implant is an exact replica of the removed bone, like a perfect jigsaw puzzle piece."
The finished implant was printed from titanium, a very strong, lightweight and metabolically inert metal, so there are no issues with corrosion or fatigue. The surface material qualities allow soft tissues and bone to grow into it, making it ideal for this scenario.
Along with the hip replacement, the surgery took under three hours. "We were able to preserve all of the major muscles that control walking," said Dr. Hugate.
Dr. Hugate has also performed a reconstruction of an entire hemipelvis (half of a pelvis) using 3-D printing technology. Both cases have gone well so far, which bodes well for future cases.
"We are to the point now where we can see a patient, and six weeks later have an implant designed, manufactured, sterilized and ready to go," said Dr. Hugate. "This has made it a more viable option now, especially for cancer patients. We will be using it more and more in tumor surgery."
Customized Surgery
According to Dr. Hugate, 3-D printing is starting to be used more in routine joint replacements. "Standard knee replacements are not customized to the individual," he said. "Typically, a surgeon will have an assortment of sizes available. During surgery, the surgeon will measure the dimension of the joint surface to be replaced, and then select one of maybe 10-15 off-the-shelf sizes. With 3-D printing, a CT scan is taken of a knee, along with the size and shape of the patient's femur. The implant is designed to match the patient's anatomy. It is then printed and available at the time of surgery. A small percentage of knee replacement implants are created using this technique. It will probably expand into hips and shoulders at some point. The customization process in orthopedics right now is largely dependent on 3-D printing."
The 3-D Printing Solution
The 3-D printed implant was created using 3D Systems technology. 3D Systems has a fleet of DMP Flex 350 metal 3-D printers that are used for implant manufacturing. With a build volume of 275 mm x 275 mm x 380 mm (10.82" x 10.82" x 14.96"), the DMP Flex 350 enables short set-up times and greater production speeds of final parts with excellent mechanical properties and reduced material waste.
In addition to 3D Systems' direct metal printing capabilities, it employs a variety of other 3-D technologies for some of its other services. For example, VSP (Virtual Surgical Planning) is a 510(k) FDA cleared service that allows surgeons to pre-plan their upcoming surgeries in a 3-D environment prior to entering the operating room. This offering begins with a patient CT scan which is processed using D2P software by a team of engineers. Next, the surgeon and a 3D Systems biomedical engineer participate in a web meeting during which the surgeon views a 3-D digital model of the patient's anatomy. The surgeon and engineer collaborate to develop a surgical plan which includes patient-specific models, guides and templates. 3D Systems' team of expert designers create the CAD files for these tools which are 3-D printed using 3D Systems' Stereolithography (SLA) technology, and can be sterilized and used in the operating room.
3D Systems' Littleton, CO, site is the global headquarters for its healthcare offerings. A sister facility in Leuven, Belgium, offers similar services to the U.S. site, and a facility in Tel Aviv, Israel, is primarily focused on surgical simulation. All three facilities are ISO-13485 certified and FDA registered. 3D Systems is a pioneer in the integration of healthcare procedures and 3-D technology to enable improved surgical outcomes and enhance surgical training. Its global teams work with surgeons, medical device companies, surgical training institutions and others in the healthcare industry to help navigate technologies and provide support for surgical planning, training, device design, personalized medical technologies and 3-D printing. From converting patient-specific CT data into digital anatomical models for surgical simulation and planning to 3-D printing more effective implants and devices, 3D technology provides a new way of looking at and solving problems in healthcare.
For more information contact:
3D Systems
888-598-1438
www.3dsystems.com