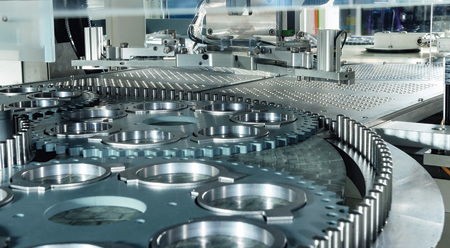
Peter Wolters AC 1250 Fine grinding wheel carrier in twin loader
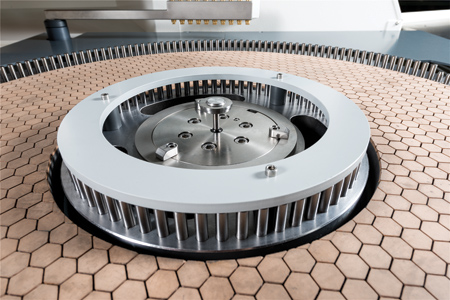
Peter Wolters AC 1250 Inner Pin Ring
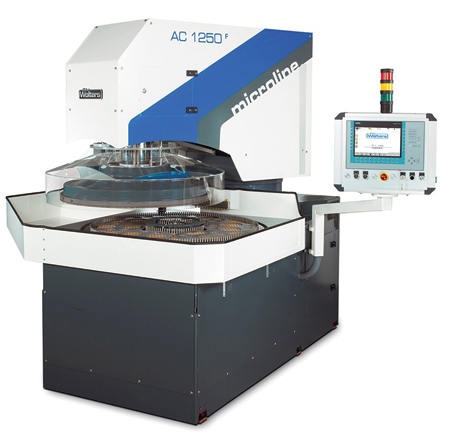
Peter Wolters AC microLine 1250 machine
Lapmaster Wolters, a member of the Precision Surfacing Solutions Group, offers its AC microLine 1250-F/H. It features maximum load pressure in process of 4000 daN and 70 kW servo drives.
The AC 1250 is a further development of the established AC 1200. The working wheel dimensions and epicyclic workholder drive system grew compared to its predecessor. Accordingly, the machine base components have grown as well to ensure its rigidity and precision. Modern Siemens drive technology with up to 70 kW in combination with max. 4000 daN load pressure in process provides high stock removal rates. A revised working wheel cooling labyrinth with increased flow volume also helps to ensure the required and known high precision of Peter Wolters AC microLine series, such as the contactless measurement control unit.
Some features include:
- Automatic carrier loading concept with carrier exchange time ≤ 60 s
- Software functions like for example constant removal rate or automatic working wheel wear compensation
- RangeCare (remote maintenance solution via mobile communications or VPN)
- DataCare (integrated process data recording)
A Twin Loader for Maximum Efficiency
Peter Wolters AC microLine 1250-F in combination with the twin loader represents a powerful production system consisting of grinding machine and automation for automatic workpiece carrier exchange. The core of the twin loader is a rotary index table, which is used as a buffer. This reduces auxiliary process times and the machine capacity is utilized optimally. In parallel to the ongoing grinding process, the operator can unload finished parts and prepare workpiece carrier loading with unmachined parts. "Simultaneously loading and unloading of two workpiece carriers into and from the machine via twin loader significantly reduces the exchange time and increases the overall system productivity drastically," said a company spokesperson. The exchange time of 60 seconds for six workpiece carriers ranks among the best in the market. For even more efficiency, the modular twin loader can be complemented with a robot cell for workpiece carrier loading and unloading.
"The twin loader generation introduced first at EMO 2017 is a further development of the proven and established initial twin loader," said the spokesperson. Relevant optimizations are: solid steel weld construction instead of aluminum profile frames; linear electrical unit for workpiece carrier loading and unloading; improved accessibility through new frame design; flexible selectable position for machine operator and/or robot cell for optimum adaptation to the customer's conditions as well as faster rotary table positioning via servo drive.
Robot Cell
The robot cell is an automation concept for Peter Wolters AC microLine machining tools and is equipped with a Scara robot for pick and place for workpiece loading and unloading. The robot cell also features an infeed conveyor for unmachined part feeding as well as an outfeed conveyor for removing finished parts. This enables optimum integration in existing or new production lines.
The robot cell can load and unload AC microLine machines directly. After process end, the upper machine part swivels out, providing the Scara robot with optimum access to the grinding area and thus allowing workpiece carrier loading and unloading to start. Finished part removal and subsequent loading with an unmachined part is alternated for an efficient loading and unloading time.
Furthermore, the robot cell can be combined with a twin loader for a significant increase in productivity and optimization. For this design variant, workpiece carrier loading and unloading take place in the twin loader during the processing time of the AC microLine machine, which reduces auxiliary processing times to a minimum.
For more information contact:
Lapmaster International LLC
501 W Algonquin Rd.
Mount Prospect, IL 60056
224-659-7101
sales@lapmaster-wolters.com
www.lapmaster-wolters.com