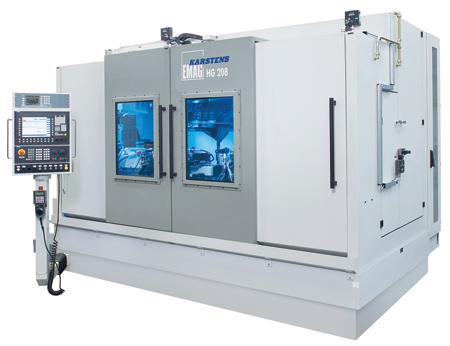
HG 208 by EMAG: A wide range of technology modules are available for the development of individual grinding solutions.
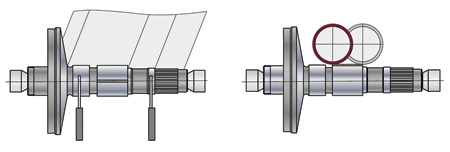
This example illustrates how the HG machine can be specifically adapted to the conditions imposed by the various components. (l-r) a large corundum grinding wheel for external machining and a small CBN grinding wheel for groove machining, arranged on two separate slides with separate dressing systems.
Technological advances in automotive engineering are rapidly changing the demands for production technology-this is not just for new processes, but also applies to established processes such as the cylindrical grinding of transmission shafts. To meet the changing demands, the components have increasingly complex geometric details and also need to be finished with the highest precision. As a result, manufacturing companies depend on mechanical engineering to develop individualized grinding solutions for the shafts-ideally, integrated into complete production lines. The grinding specialists from the EMAG Group have developed solutions for this environment: the HG 208 horizontal cylindrical grinder, for example, is suitable for the precision machining of shafts in series production. With its modular design principle, these machines can be adapted to a wide variety of machining tasks and integrated into EMAG production lines.
Off the shelf grinding solutions are virtually impossible for many applications: drive shafts for electric motors, complex camshafts or crankshafts, as well as transmission shafts all require very different processes. For example, different solutions are required depending on if only a single grinding operation, several parallel grinding operations or combined internal and external grinding operations are necessary. Additionally, the component and grinding technology used may add additional technology requirements such as in-process measuring devices, dressing units for CBN and corundum grinding wheels, automatic balancing units and more.
"It is these very different demands that characterize the development of the HG 208 horizontal cylindrical grinder," said Peter Loetzner, President and CEO of EMAG L.L.C. "We offer our customers a wide range of different technology modules that can be easily integrated into a standardized machine. For instance, the HG 208 can be equipped with one or two compound slides, on each of which different external and internal grinding spindles can be fitted. By using a B-axis or a center drive, for example, we can provide the perfect solution for each customer-specific application."
Customized for CVT Transmissions
CVT transmissions are an example of how developments in the automotive industry can influence and drive forward such a flexible concept. This technology is being used in modern hybrid drives, effectively combining the power of combustion engines and electric motors. The central or primary CVT transmission shaft represents a real grinding challenge in the production process: On the one hand, the control wheel surface is precisely machined by an angle plunge. On the other hand, axial ball track grooves have to be machined. With EMAG, both processes are performed in a single clamping operation in order to avoid reclamping errors and to achieve increased precision. For machining the grooves, the grinder is equipped with a dressable ceramic CBN grinding wheel, allowing the quality of the ball track to stay high.
For machining the taper face on the primary shaft (and similar surfaces on other shafts), EMAG recently expanded its HG modular system: a corundum grinding wheel with a maximum diameter of 29.5" (750 mm) is used for this task. "This example illustrates how we continually adapt the machine and the available modules to the conditions imposed by the various components," Loetzner said. "This allows us to create the perfect technology configuration for the customer: a large corundum grinding wheel for external machining and a small CBN grinding wheel for machining the grooves, arranged on two separate slides with their separate dressing systems. This ensures that the requirements for quality and cycle times are met."
Complete Production Lines from EMAG
"Another important factor for production planners in the automotive industry is the holistic approach from EMAG," said a company spokesperson. "The mechanical engineering company masters all processes for soft and hard machining and has extensive experience in the establishment of complete production solutions. For example, a transmission shaft is pre-processed on EMAG VTC vertical turning centers and finished on HG series grinders. With the associated line automation, EMAG completely adapts itself to customer requirements."
"The HG 208 has been on the market for around 15 years already-this means customers benefit from a technology that is well established, but which continues to advance," Loetzner said. "With these updates, the HG 208 can now successfully perform cylindrical grinding operations on crankshafts and camshafts. Parallel external and internal machining of hollow shafts is also made possible with this concept. For this purpose, there is a variant of the HG 208 with a direct-driven center drive. EMAG grinding experts see a great opportunity in the growing electric vehicle market for the HG 208 and its associated product lines, due to its efficient grinding operation of the central drive shaft for electric vehicles."
For more information contact:
Kirk Stewart
Sales Director
EMAG L.L.C.
38800 Grand River Ave.
Farmington Hills, MI 48335
248-996-4703
kstewart@emag.com
www.emag.com
SOUTHWEST
TX, OK, AR, LA
Eric Klenner
Regional Sales Manager
EMAG L.L.C.
248-595-1530
eklenner@emag.com
NM
Shane Cross
Regional Sales Manager
EMAG L.L.C.
248-207-5365
scross@emag.com
SOUTHEAST
MS
Eric Klenner
Regional Sales Manager
EMAG L.L.C.
248-595-1530
eklenner@emag.com
AL, GA, FL, NC, SC, E. TN, VA
Dave Fitzgerald
Regional Sales Manager
EMAG L.L.C.
248-595-1117
dfitzgerald@emag.com
W. TN
Mark Comeaux
Regional Sales Manager
EMAG L.L.C.
248-938-2097
mcomeaux@emag.com
NORTHEAST
W. NY, W. PA, WV
Mark Comeaux
Regional Sales Manager
EMAG L.L.C.
248-938-2097
mcomeaux@emag.com
E. NY, E. PA, DE, MD, NJ, CT, RI, MA, VT, NH, ME
Kevin Gadde
EMAG L.L.C.
248-938-2430
kgadde@emag.com
MIDWEST
OH, KY, N. IN
Mark Comeaux
Regional Sales Manager
EMAG L.L.C.
248-938-2097
mcomeaux@emag.com
W. MI
Peter Vandersluis
Regional Sales Manager
EMAG L.L.C.
616-307-7401
pvandersluis@emag.com
E. MI
Mark Ashworth
AAM, MPG
EMAG L.L.C.
248-826-4242
mashworth@emag.com
ND, SD, NE, KS, MN, IA, MO
Bill Konetski + Cat/John Deere
Regional Sales Manager
EMAG L.L.C.
612-804-0857
bkonetski@emag.com
IL, S. IN
Tod Petrik
Regional Sales Manager
EMAG L.L.C.
248-470-2646
tpetrik@emag.com
WI
Joe Thompson
Regional Sales Manager
EMAG L.L.C.
248-880-0233
jthompson@emag.com
WEST
WA, OR, CA, NV, ID, MT, WY, UT, CO, AZ
Shane Cross, CMTSE
EMAG L.L.C.
248-207-5365
scross@emag.com